La sostenibilidad en el ámbito industrial: fabricación de componentes críticos y el movimiento ‘green wave’
A. del Olmo; G. Martínez de Pissón; G. Gómez; I. Holgado; M. González; I. Ayesta; O. Pereira; y L.N. López de Lacalle, del Dpto. de Ingeniería Mecánica, Universidad del País Vasco (UPV/EHU) y el Centro de Fabricación Avanzada Aeronáutica (CFAA, UPV/EHU); y E. Gonzalez, del CFAA (UPV/EHU)
02/05/2024En los últimos años, uno de los temas que más ha preocupado a la industria y al mecanizado, es cómo contribuir a mejorar a la sostenibilidad y reducir el impacto medio ambiental que se genera al planeta: emisiones de gases de efecto invernadero, vertidos de fluidos de corte, ratio de piezas desechadas o el uso abusivo de materiales limitados. La situación económica y energética, además de la promoción por parte de las instituciones, obligan a un cambio en industria del mecanizado, que enfrenta la necesidad de transformar sus métodos de fabricación tradicionales hacia una dirección más sostenible, caracterizada por una reducción de la contaminación y una mayor inclusión ambiental.
Cada vez se deben cumplir más criterios ecológicos, bajo la siempre creciente presión de costes, debido a la inflación que atraviesa el país. Desde la Unión Europea, se buscan implementar principios esenciales, como las 3R (Reducir, Reutilizar y Reciclar), para mejorar la gestión de residuos y fomentar la conservación del medio ambiente. Esto implica promover conceptos como la minimización de desechos, la reutilización de materiales y la reducción de la demanda de recursos naturales. Estas indicaciones están vinculadas a la fabricación, ya que la materia prima es el punto de partida de la industria.
El acceso confiable y sin obstáculos a las materias primas es una preocupación creciente dentro de la UE y en todo el mundo, dado la rareza y escasez de ciertos materiales ampliamente usados. Para abordar este desafío, la Comisión Europea ha creado una lista de materias primas críticas (CRMs) sujeta a una revisión y actualización periódica que combinan materias primas de alta importancia para la economía y de alto riesgo asociado con su suministro.
![Figura 1. Marco conceptual del Ecodiseño dentro de una Economía circular. [1] Figura 1. Marco conceptual del Ecodiseño dentro de una Economía circular. [1]](https://img.interempresas.net/fotos/4661591.jpeg)
En este contexto la atención se centra cada vez más en estrategias que puedan, no solo ayudar a la sostenibilidad, sino incrementar la producción, reducir la cantidad de piezas desechadas por errores evitables o prolongar la vida útil de las herramientas de corte. Todo ello, se traduce en una reducción de costes, de emisiones de CO2 y una minimización de los desechos, reduciendo en el camino la huella medioambiental. Entre las estrategias más destacadas estarían las siguientes:
- Prolongar la vida útil base de la herramienta de corte
- Geometrías adaptadas según el material a mecanizar
- Nuevos diseños de concepto de herramientas (cabezas intercambiables)
- Diferentes tipos de refrigeración
- Recubrimientos
- Reafilado de las herramientas de corte
- Monitorización y aseguración del proceso
- Reciclado herramientas
- Procesos de fabricación aditiva
Para hacer innovaciones así, los centros de investigación son fundamentales en la búsqueda de técnicas de fabricación más sostenibles. Son ellos quienes impulsan el desarrollo de nuevas tecnologías y métodos que permiten reducir el impacto ambiental de la producción industrial.
En esta línea, el Centro de Fabricación Avanzada Aeronáutica (CFAA) se posiciona como un aliado para las empresas vinculadas al ámbito de la fabricación, ofreciendo asistencia para dar los pasos necesarios que marcan la diferencia en el impulso hacia prácticas más sostenibles en la industria.
¿Cómo funciona el CFAA?
El Centro de Fabricación Avanzada Aeronáutica (CFAA) es una iniciativa colaborativa entre la Universidad del País Vasco (UPV/EHU), empresas del sector aeronáutico y entidades gubernamentales como el Gobierno Vasco y la Diputación Foral de Bizkaia. Su objetivo es desarrollar y aplicar tecnologías de fabricación innovadoras en la industria de fabricación, especialmente en la aeroespacial, promoviendo la transferencia rápida de conocimientos la mejora de la competitividad del sector en la región.
El CFAA opera como un espacio de convergencia entre la academia y las empresas, donde se materializan ideas con el objetivo de mejorar los procesos de producción y aumenta su rendimiento para reducir el impacto ambientas. El centro tiene máquinas reales en un entorno similar al industrial, pero con el enfoque y la metodología de trabajo propios de un laboratorio de I+D+i. Esta configuración permite superar la brecha del desarrollo tecnológico, pasando del nivel de TRL 4-6, el denominado valle de la muerte, para implementar nuevas tecnologías de manera efectiva en el entorno industrial.
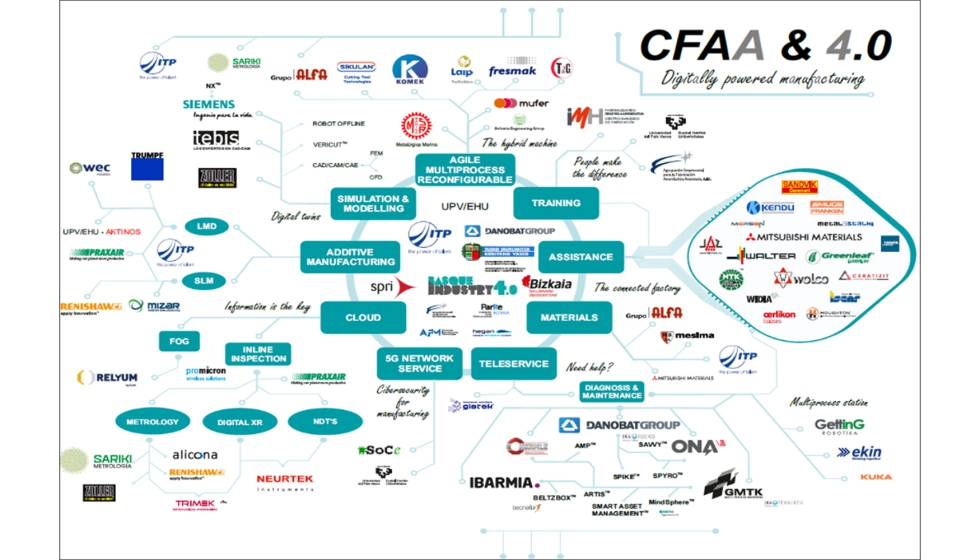
Las máquinas de CFAA
Como se ha señalado anteriormente, uno de los principales desafíos de la industria radica en cómo adaptar sus procesos de fabricación para reducir su impacto medioambiental. El centro de investigación debe abordar las operaciones de mecanizado del sector, así que debe contar con las diferentes tipologías de máquinas utilizadas por el sector. Para satisfacer esta necesidad, en el CFAA hay muchos centros de mecanizado y bancos de ensayo, que cubren las necesidades de operabilidad requeridas por los socios del centro de investigación.
La maquinaría del CFAA, junto con las ayudas de las instituciones públicas, en forma de proyectos o iniciativas, permiten desarrollar y perfeccionar las máquinas y consumibles empleados durante el mecanizado, avanzando hacia la madurez de nuevas tecnologías. Estas mejoras pueden manifestarse tanto en la optimización de la maquinaria existente o como en la innovación de materiales y/o componentes utilizados durante el proceso de fabricación, permitiendo el progreso tecnológico en la industria.
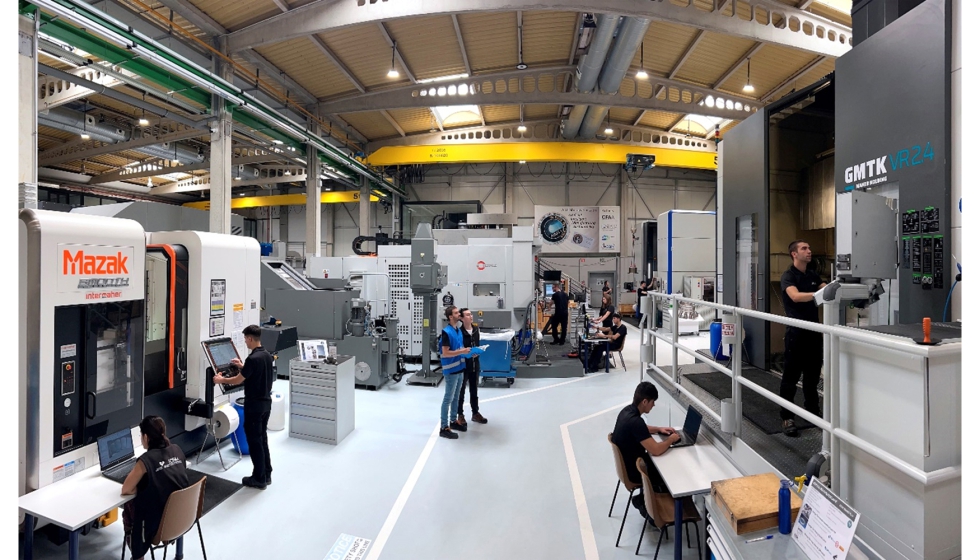
En el inventario tecnológico del CFAA se cuenta con una amplia gama de maquinaria de vanguardia que impulsa la capacidad productiva, entre las que destacan la siguientes, como parte del arsenal tecnológico del centro:
1. Procesos de mecanizado
Ibarmia THR 16 Multiprocess
El centro de mecanizado 5 ejes THR 16 Multiprocess es una máquina altamente versátil y avanzada: combina operaciones de fresado, torneado y ahora operaciones de rectificado. Su husillo principal cuenta con una potencia de 74 kW, mientras que el motor de torsión de la mesa (eje C) alcanza los 70 kW, lo que permite una rotación de alta velocidad para operaciones de torneado en duro. Integra un cambiador de herramientas automatizado, con un robot antropomórfico, permitiendo un intercambio eficiente de herramientas y cabezas angulares para realizar operaciones con ángulos en orientaciones difíciles.
En esta anualidad se prosigue con un proyecto de máximo interés para el CFAA, el proyecto GENESIS (ZL-2023/00229) financiado por el Gobierno Vasco, que tiene como objetivo por parte de IZAR CUTTING TOOLS y OERLIKON-BALZERS desarrollar nuevas herramientas de corte más eficientes, competitivas y sostenibles para la industria manufacturera del futuro. Los esfuerzos se han centrado en la validación de una nueva geometría recubiertas de alta tasa de arranque de viruta para el mecanizado de aleaciones de aluminio, incluso en seco, que aumente la productividad y la vida útil de la herramienta. La nueva tipología de fresas se basa en herramientas comerciales para aluminio, con cambios en la geometría y un recubrimiento mejorado para evitar adhesiones de material, un problema frecuente con el aluminio.
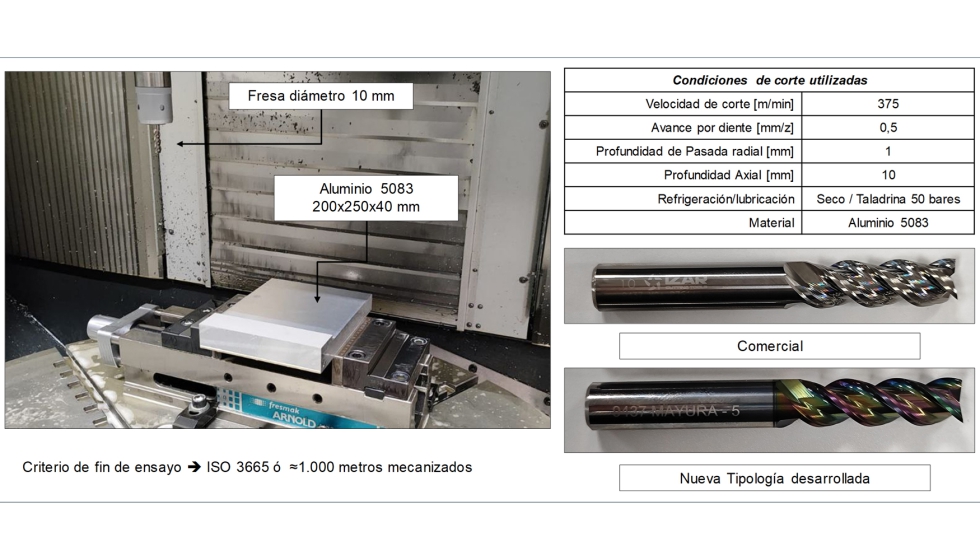
Para la validación, se realizan diversas baterías de ensayos, en aluminio 5083, para establecer las condiciones de corte de partida e ir mejorándolas hasta mejorar las industriales. Se realizaron también pruebas en seco para evaluar la viabilidad de la nueva tipología bajo las condiciones más adversas y compararlas después con el rendimiento obtenido usando taladrina, considerando que la eliminación de fluidos de corte implica ahorro y reducción de la huella ambiental del proceso. Para evaluar el rendimiento de las herramientas, se evalúa el desgaste de los filos de corte con la norma ISO3685 y la integridad superficial de la pieza. Cabe destacar, que ni para la operación en seco, que ni para la operación con taladrina, se observó un aumento en el desgaste en las nuevas herramientas incluso después de haber superado casi 1.000 m de mecanizado.
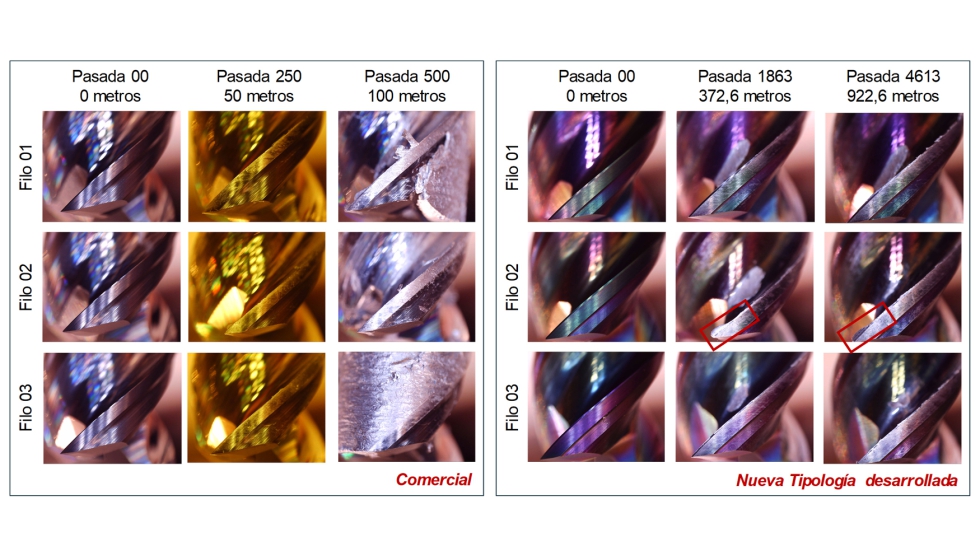
La fresa comercial alcanzó 100 metros de mecanizado en seco antes de embotarse, una vida aceptable en la industria. Sin embargo, la nueva fresa, optimizada, multiplica esta longitud por 10, llegando casi a los 1.000 metros mecanizados. Este avance permite el mecanizado en seco y aumenta significativamente la productividad, rompiendo con el estancamiento en el desarrollo de herramientas para aleaciones maleables
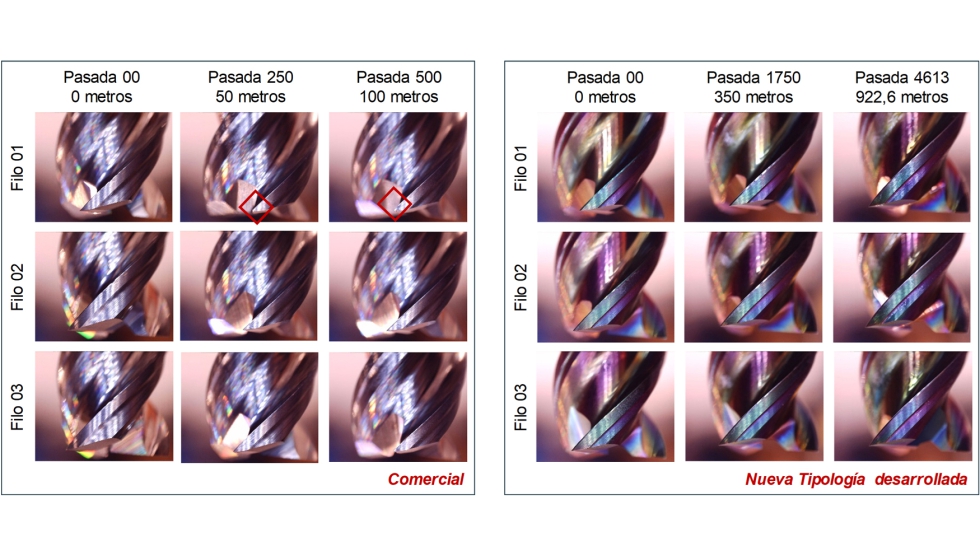
Por otro lado, las pruebas con taladrina inyectada revelaron que, aunque las fresas comerciales no sufrieron embotamiento, los filos presentaron roturas después de alcanzar los 100 metros mecanizados. En contraste, la nueva tipología desarrollada alcanzó de nuevo casi 1.000 metros sin mostrar signos significativos de desgaste.
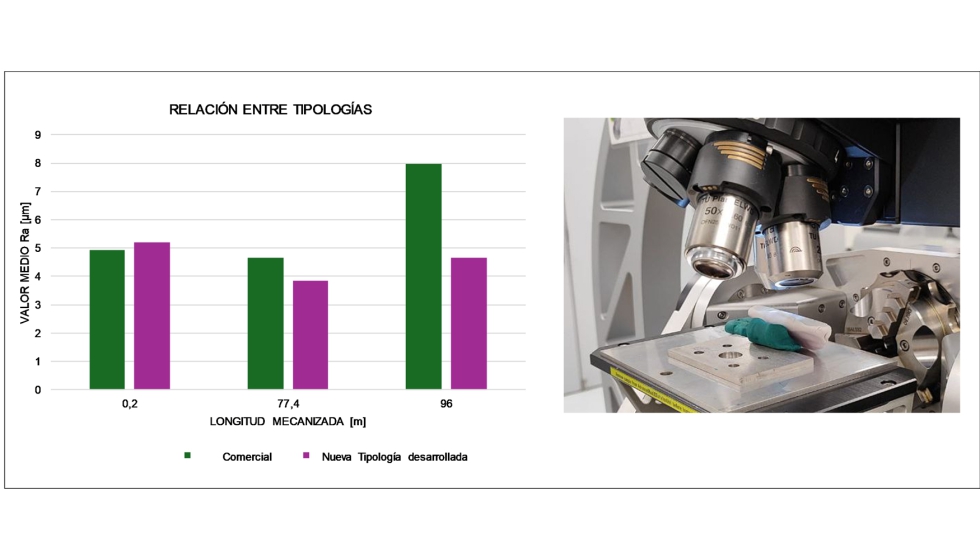
Por último, se lleva a cabo un análisis de la calidad superficial de las piezas mecanizadas para diferentes etapas de la vida útil de las herramientas, comparando las rugosidades obtenidas de la herramienta comercial y la herramienta de nueva. Se emplean resinas para tener un negativo de la pieza y un microscopio Alicona para analizar la superficie generada. Los resultados muestran valores similares en etapas iniciales, pero que a posterior la diferencia entre ambas se amplía, la nueva tipología de fresa mostrando una mejora de hasta un 20% en la etapa intermedia y aproximadamente un 70% después de 100 metros mecanizados. Además, se observa que la rugosidad de la herramienta nueva se mantiene prácticamente estable sin presentar aumentos hasta llegar a los 1.000 metros mecanizados aproximadamente.
GMTK Multi-Process VR 2.4
El centro de mecanizado GMTK VR2.4 es una solución flexible que satisface los requisitos específicos para producir componentes aeroespaciales de gran tamaño, y con una configuración rígida y alta dinámica. Esta máquina sobresale tanto en operaciones de torneado como de fresado, con dos ejes lineales y un eje C hidrostático rotativo le permite realizar cualquier operación. Tiene un rango de trabajo máximo de 2400 mm de diámetro y una potencia de accionamiento de 56 kW, ideal para la fabricación de componentes de revolución como discos y carcasas aeronáuticas. Además. mediante un sistema robotizado integrado para cambios de herramientas, portaherramientas y cabezales, se ofrece precisión y productividad. El centro de mecanizado GMTK VR 2.4 ofrece una eficiencia y fiabilidad excepcionales para manejar geometrías complejas en la industria aeroespacial.
La fabricación de componentes aeronáuticos, como carcasas es una de las líneas principales de investigación del CFAA, así lo demuestra el proyecto de I+D+i Iteneo: ‘A global approach to improve the manufacturing of casing for new aeroengines (PID2019 -109340RB-100)’, financiado por el Ministerio de Ciencia e Innovación y la Agencia Estatal de Investigación de España ((MCIN/ AEI/10.13039/501100011033/)). En estas piezas, el proceso de mecanizado más empleado es el torneado, abarcando aproximadamente el 50% de los procesos requeridos para su conformación. Esta operación, especialmente en materiales de baja maquinabilidad, conlleva altas cargas térmicas y mecánicas que aumentan el riesgo de un desgaste rápido en la herramienta, comprometiendo la integridad superficial de la pieza.
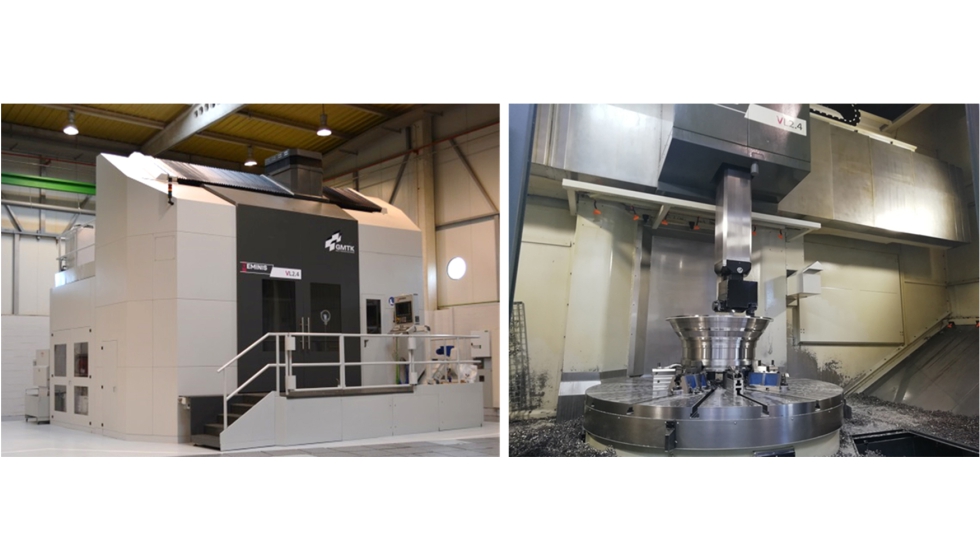
En la actualidad, los insertos cerámicos y de metal duro son los más empleados, para ambos casos empleándose parámetros de corte conservadores limitados al rendimiento y no a la eficiencia. Por ello, se busca equilibrar las limitaciones y beneficios en el mecanizado aeronáutico, aprovechando el aumento de potencia en los centros de mecanizado para explorar el uso operaciones de alto avance como el High Feed Turning (HFT) para el desbaste de carcasas.
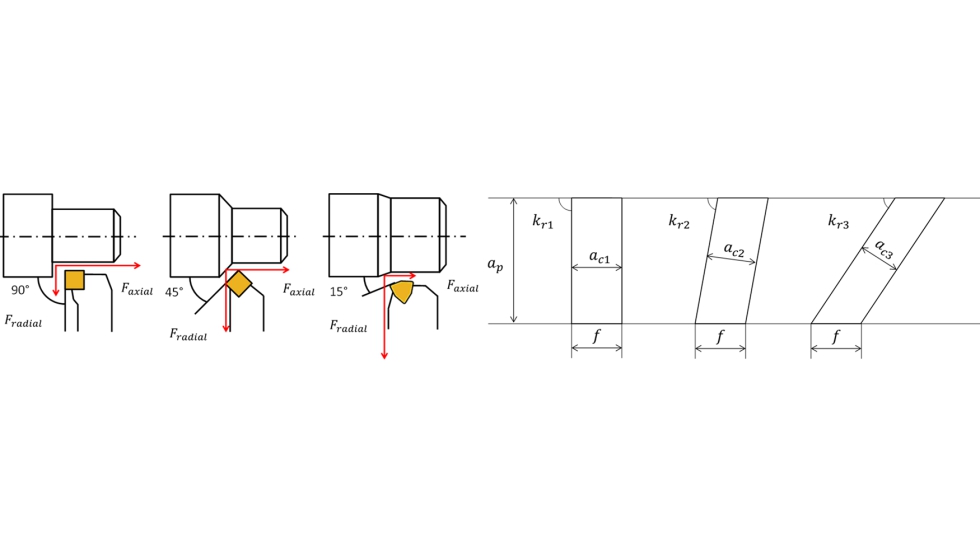
Esta técnica implica cambiar el ángulo de avance para reducir el desgaste y mejorar la distribución de cargas termo-mecánicas a lo largo del filo de la herramienta, mejorando la estabilidad del proceso, permitiendo que la plaquita pueda soportar mayores esfuerzos y así aumentar la velocidad de avance. Además de ofrecer mayores tasas de arranque, también prolonga la vida útil de la herramienta. En este proyecto, se trabaja con la implementación de esta tecnología en el desbaste de una carcasa aeronáutica, probando el incremento de las fuerzas de corte frente a un aumento controlado del avance de la herramienta de corte.
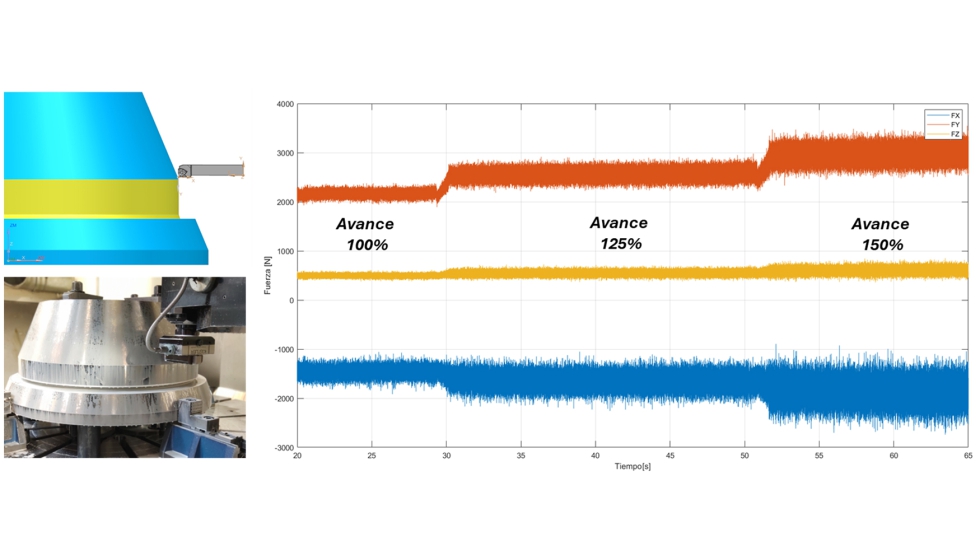
El centro de torneado Mazak Integrex i-200 se destaca como una máquina multitasking y versátil que integra de manera óptima las capacidades de torneado y fresado. Su cabezal giratorio y eje B, posibilita un mecanizado preciso en varios ángulos y orientaciones, lo que amplía las opciones para trabajar con geometrías complejas. Su funcionalidad multieje y la capacidad de acoplar un contrapunto (0,1 - 0,7 kN), ofrece una mayor eficiencia en la producción de piezas precisas, con un control propio CNC (Mazatrol), que hace la programación más fácil e intuitiva. Integra cambiadores automáticos de herramientas y husillos de alta velocidad y garantiza un posicionamiento correcto, sin interrupciones y manteniendo velocidades de mecanizado elevadas.
En el CFAA, también se trabaja con geometrías libres, que suponen a la hora de mecanizar una mayor complejidad para los fabricantes. En esta línea, junto con varios socios del centro de investigación: Intermaher, Trimek, Mesima y Jaz Zubiaurre, se está llevando a cabo un proyecto denominado DESPRO (ZL-2023/00832) financiado por el Gobierno Vasco, que tiene como objetivo desarrollar nuevos productos y estrategias que ayuden en la fabricación ecológica de álabes de titanio para turbinas de aeronaves 100% sostenibles en cuanto a la emisión de CO2.
Este proyecto define un proceso global para atender la demanda de componentes tipo álabes rotativos en Ti6Al4V, contemplando todas las etapas del proceso:
- Obtención de la geometría de preforma
- Desarrollo de centro de mecanizado especializado
- Desarrollo de equipo de refrigeración criogénica para estas piezas
- Herramientas de desbaste/acabado
- Herramientas de super acabado
- Servicio de medición del producto
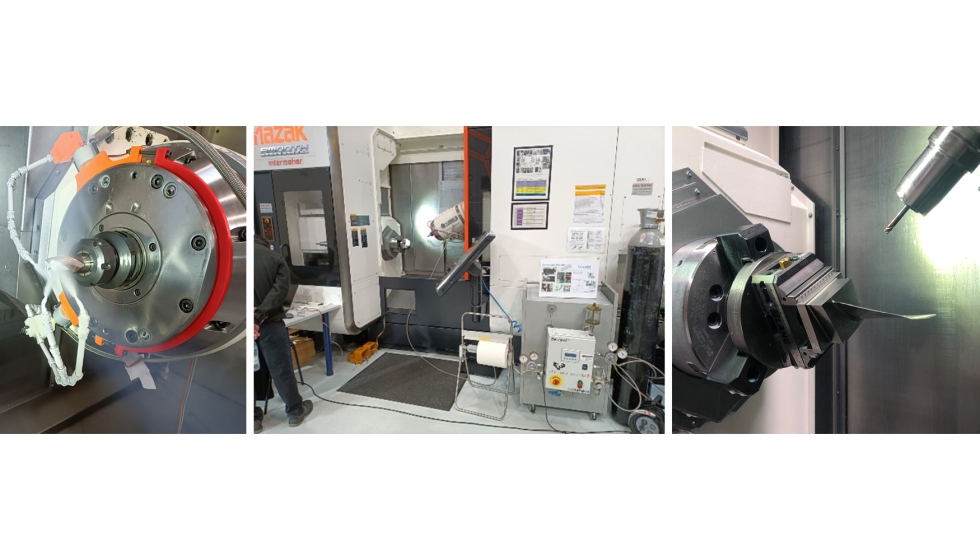
Durante la fase inicial se ha hecho énfasis en la adaptación del sistema de refrigeración criogénica desarrollado en el CFAA, al centro de mecanizado de interés, Mazak Integrex i 200, atendiendo a las limitaciones de espacio de trabajo y la flexibilidad de movimiento del husillo. El sistema se ha probado con una geometría alabeada similar para comprobar las dimensiones de las boquillas y el movimiento necesario por parte de estas para enfocarse en la zona de corte y evitar la colisión con la pieza.
Danobat TV-1500 Vertical lathe
El TV-1500 es una construcción robusta que combina precisión y rigidez para permitir un rendimiento de mecanizado eficiente al tornear piezas grandes, gracias a su configuración de corredera transversal. Cuenta con un husillo potente y un cambiador automático de herramientas, lo que facilita transiciones entre herramientas sin problemas durante operaciones de alta carga. Destaca por incorporar un mecanismo de doble RAM para mejorar la eficiencia de extracción de virutas y la estabilidad durante el proceso de torneado duro.
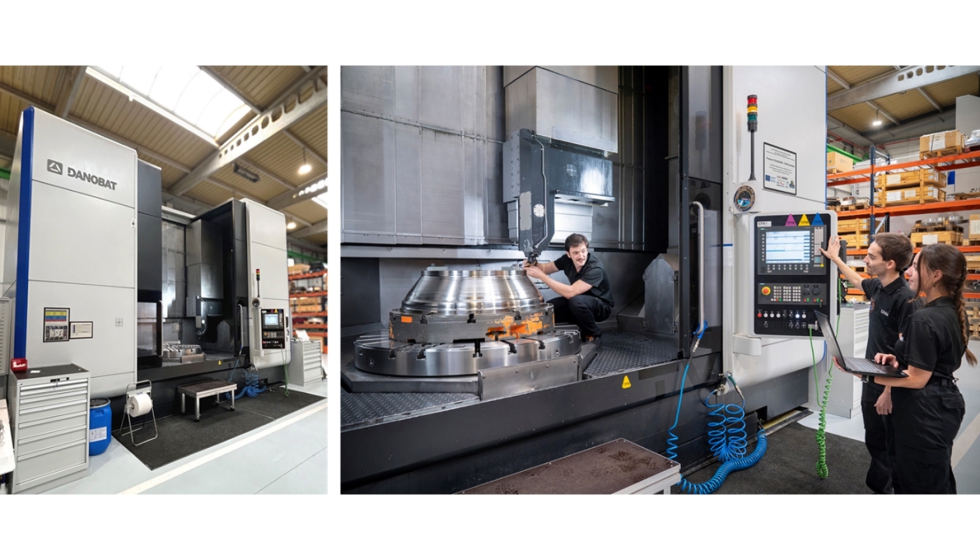
En consonancia con una industria más sostenible, la tendencia en la fabricación de componentes apunta hacia el uso de materias primas que requieran mínima transformación para alcanzar su forma final. Esta visión, conocida como componentes UNNS (Ultra Near Net Shape), se centra en la creación de piezas que están muy cerca de su forma definitiva, lo que resulta en una reducción significativa de material de desecho y en la optimización de los tiempos de proceso. Aunque esta idea es simple en su concepción, plantea diversos desafíos en la implementación y ejecución de los procesos de fabricación, como el control preciso de las tolerancias, la gestión eficaz de las deformaciones residuales y la optimización de los procesos de mecanizado para adaptarse a la geometría cercana a la forma final. Además, se enfrenta al reto de garantizar la calidad y precisión en las operaciones de acabado, así como la gestión adecuada de las tensiones residuales en las piezas.
En esta línea, el CFAA participa en el proyecto Cortex (ZE-2022/0029), financiado por el Gobierno Vasco a través de 'Hazitek 2022' y en el proyecto CPP2021-008932 de acrónimo CRESCENDO, financiado por MCIN/AEI/10.13039/501100011033 y por la Unión Europea ‘NextGenerationEU’/PRTR. Una de las múltiples actividades realizadas recientemente en esta máquina tiene que ver con la monitorización de proceso de mecanizado de un componente UNNS tipo carcasa de turbocompresor aeronáutico. Gran parte del proceso de este componente, proveniente de forja, implica el torneado. Durante el mecanizado, la pieza experimenta deformaciones debido a la liberación de tensiones residuales originadas en el proceso primario. Dado que los márgenes de tolerancia se reducen por la naturaleza de los componentes UNNS, se requiere un mayor control durante el proceso de mecanizado. En este contexto, se llevaron a cabo ensayos utilizando las garras sensorizadas Smartchuck de TdG, las cuales miden la fuerza de sujeción ejercida sobre la pieza, buscando establecer una correlación con las fuerzas del proceso de mecanizado.
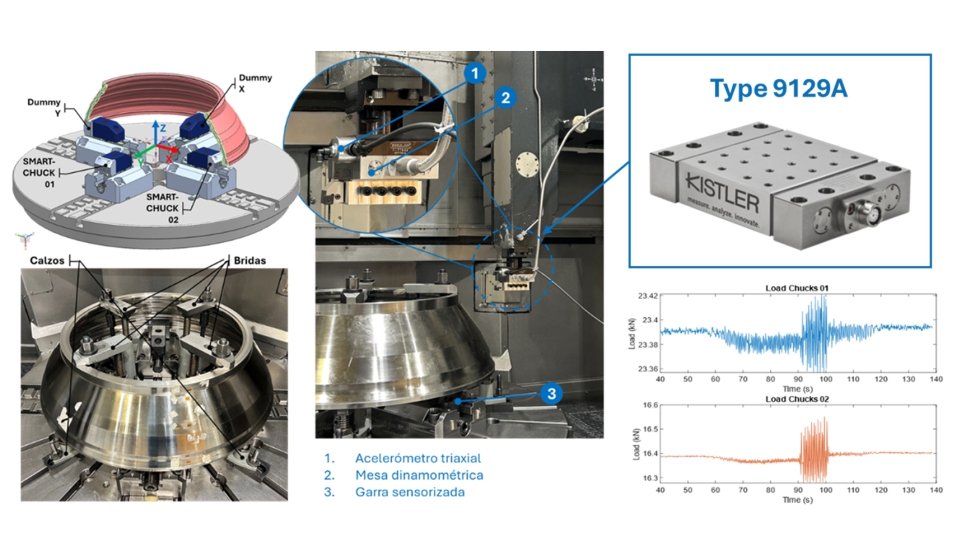
Procesos de acabado
EKIN A218/Rashem
La Ekin A218/Rashem es un banco de brochado diseñado para mecanizar la periferia de discos de turbina. La máquina tiene una capacidad máxima de carga de 70 kN, con una velocidad máxima alcanzable de 40 m/min. La máquina está equipada con un sistema de supervisión que incluyen sensores embebidos y datos máquina de los drivers de los servomotores. El banco de pruebas cuenta con un microscopio USB integrado, ubicado dentro de la máquina, que permite monitorear el desgaste de la herramienta a lo largo del tiempo. Toda la información se recoge, organiza y clasifica antes de enviarla a un sistema basado en la nube con una arquitectura de datos compleja, cuyo elemento principal es el dispositivo de Edge Computing.
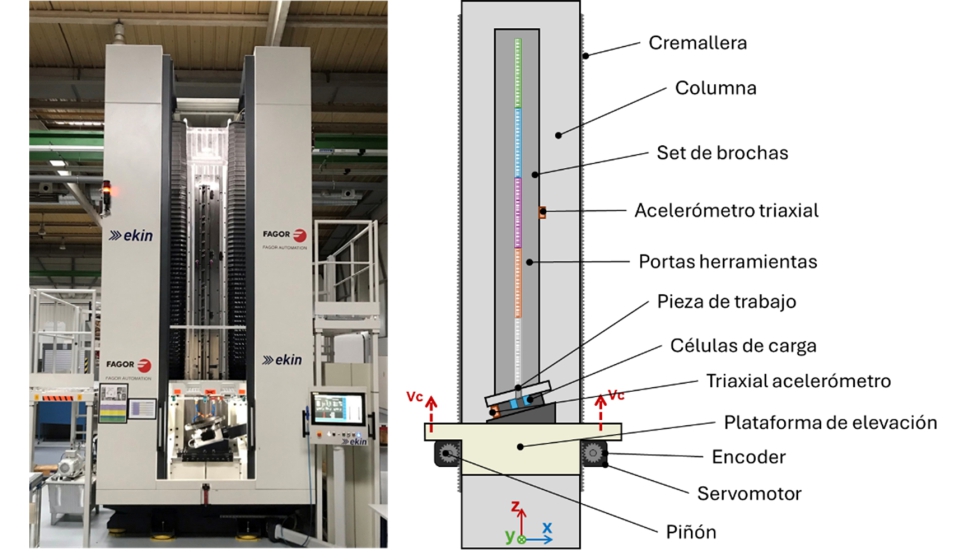
Los discos de turbina del motor aeronautico son componentes esenciales del motor aeronáutico, y su fabricación sostenible y rentable es todo un reto para los fabricantes. En esta línea, Ekin, Wolco, Sariki, Fagor y CFAA unen fuerzas en el proyecto Hatasu (ZL-2023/00594) financiado por el Gobierno Vasco, que tiene como objetivo desarrollar la tecnología de producción de discos de turbinas, así como su calidad final a través de la monitorización de variables importantes y el aprendizaje constante del proceso. Los discos de turbina se dividen en dos tipos: integrales y de ensamble. Este último se puede vivir en dos partes: el disco y las palas (blades). La unión de ambos componentes se realiza con una cola de milano especial llamada fir-tree, por su forma similar a la de un abeto, y que tiene unas tolerancias muy estrictas que no todos los procesos de mecanizado pueden conseguir. Entre ellos, el brochado es uno que reúne velocidad de fabricación y repetibilidad, junto a una precisión de varios micrómetros.
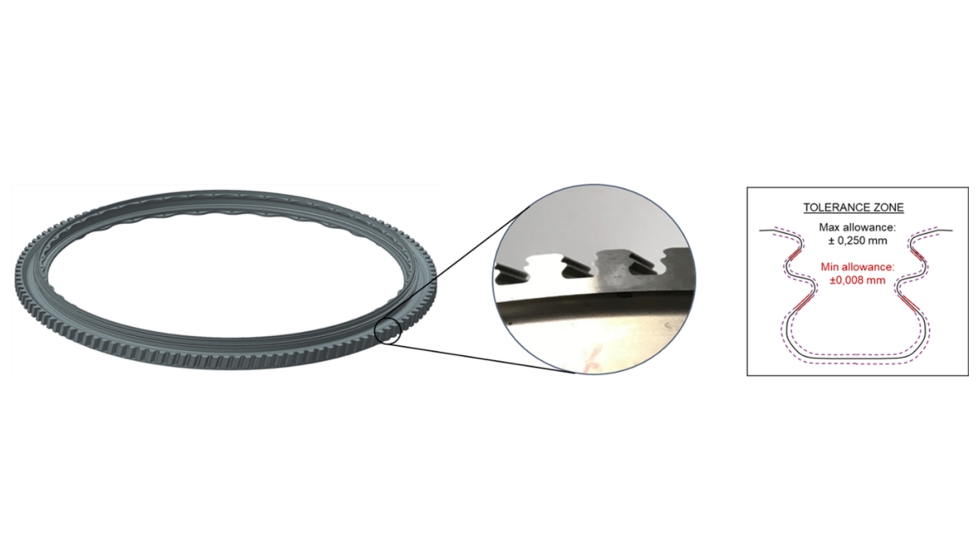
Sin embargo, una de las desventajas de brochado radica en que se debe realizar una inversión inicial considerable en las herramientas de corte, dada su complejidad de forma para fabricar, ya que todas las características del proceso están adscritas en la geometría de la propia herramienta. A ello se le de sumar, el material y las dimensiones de las herramientas de brochado, que en comparación a insertos de torneado o fresas enterizas, por lo que el precio que puede alcanzar un juego puede rondar 20.000-50.000€.
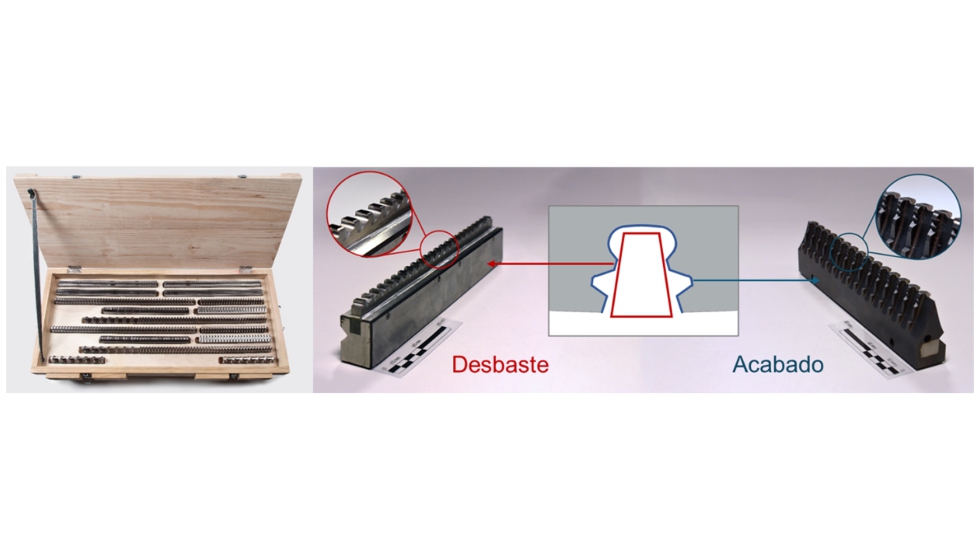
Para reducir el impacto ambiental y además ahorrar en costes, se ha empezado a realizar un mantenimiento a estas herramientas, refilándolas nuevamente para poder extender su vida útil en la fabricación de discos de turbina. No obstante, uno de los mayores stopper del continuo reafilado es la rotura de los filos, lo que imposibilita la recuperación de la herramienta. Tanto el desgaste, como la rotura del filo, son procesos aleatoria y como se usa una herramienta progresiva, esta puede propagarse a lo largo de todos los filos.
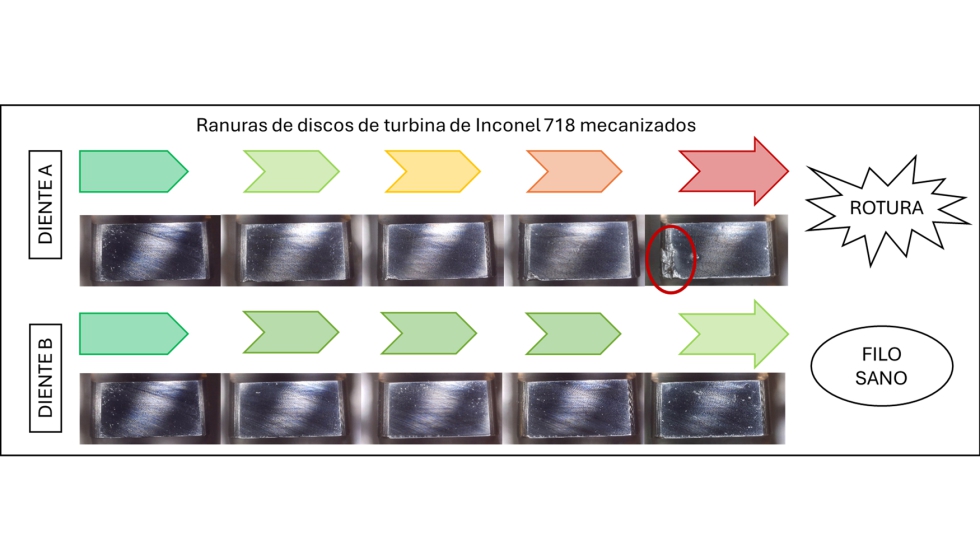
Para hacer frente a estos problemas y además facilitar la recuperación de las herramientas por reafilado, se propone la implementación de un sistema de monitorización como solución. Este equipamiento permite analizar los datos del proceso como fuerzas de corte, vibraciones o consumo de parte para identificar patrones y tendencias, lo que posibilita la detección temprana de desgastes o roturas, pequeñas o catastróficas.
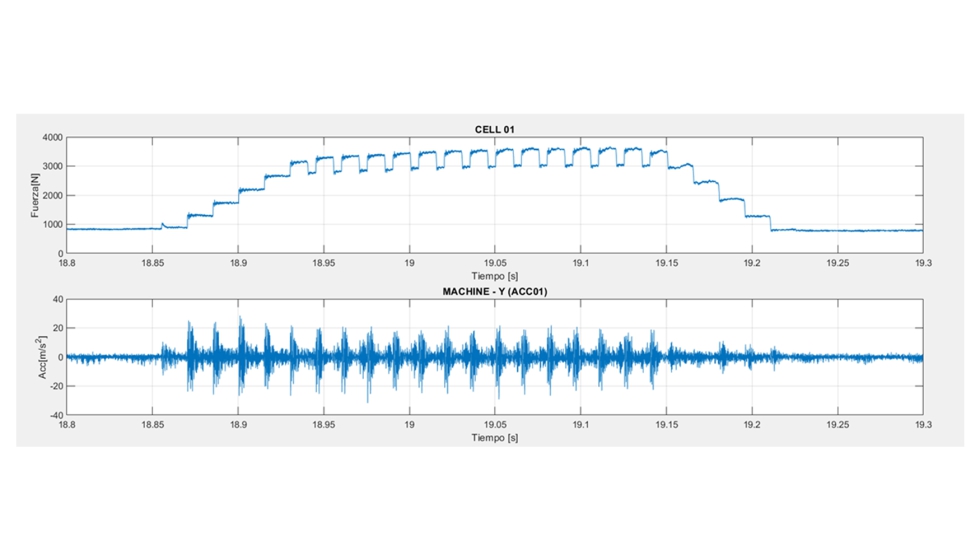
Esta medida no solo optimiza el proceso de brochado, sino que ayuda con el proceso propio proceso de reafilado evitando desgastes excesivos que hagan irrecuperable la herramienta. También puede contribuir a la prevenir la propagación de daños y a la mejorar del mantenimiento de máquina. La recopilación de datos a lo largo del tiempo puede sentar bases para el desarrollo de algoritmos predictivos que anticipen roturas o desgastes de herramienta o componentes máquina, proporcionando una gestión proactiva y preventiva de los recursos materiales.
MEK&BOT finishing cell
El CFAA cuenta con una célula robotizada con múltiples cabezales y estaciones de trabajo para operaciones de superacabado tanto con pieza como con herramienta en mano. Esta tecnología habilita a la célula para realizar operaciones de cepillado y rebabado con gran flexibilidad para adaptarse a toda clase de componentes de alto costo. Además, la cabeza del robot es intercambiable y se han incorporado varias configuraciones a la célula para mejorar la flexibilidad y facilidad de uso. Este equipamiento se complementa con un cabezal dotado de un escáner de luz azul estructurada, habilitado tanto para posicionar piezas de geometrías complejas, como para reconstruir las geometrías escaneadas y medir variaciones en sus características con respecto al sólido digital (CAD) original.
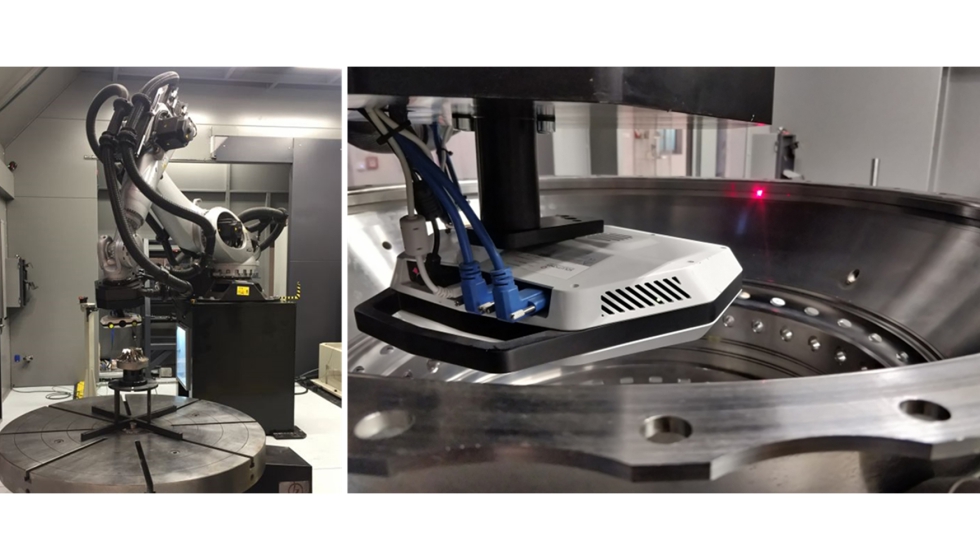
La aplicación de la visión artificial en el mecanizado se está convirtiendo en un foco clave para mejorar la precisión y calidad de las piezas, pudiendo ayudar tanto en el cálculo de las trayectorias de la herramienta a generar, como en la garantía del acabado dejado en la propia pieza. El CFAA es consciente de la necesidad de automatización en el ámbito del mecanizado, por lo que está desarrollando la tecnología necesaria para ello. Como parte de una tesis doctoral, se está trabajando en la construcción de un software utilizando visión artificial para detectar automáticamente las aristas en componentes con geometrías no estándar, para la aplicación posterior de un proceso de rebabado.
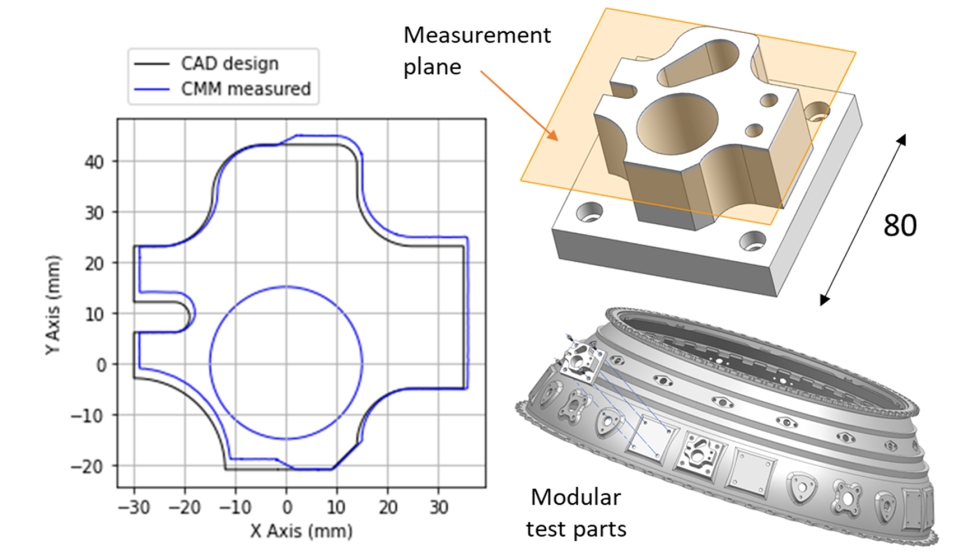
El proyecto está centrado en el desarrollo de un software de detección automática de contornos, diseñado para piezas de geometría plana con rebabas, como las que se encuentran comúnmente después del planeado de geometrías obtenidas de fundición. Este sistema utiliza una cámara convencional para analizar mediante una única fotografía y, a partir de ella, identifica automáticamente las trayectorias de rebabado en el contorno exterior de la pieza, y genera una trayectoria adicional para preparar la arista, actuando solo en las áreas donde se detectan las rebabas principales. Este enfoque innovador busca mejorar la eficiencia y la precisión en el proceso de acabado de piezas, representando un avance significativo en la automatización de tareas industriales clave.
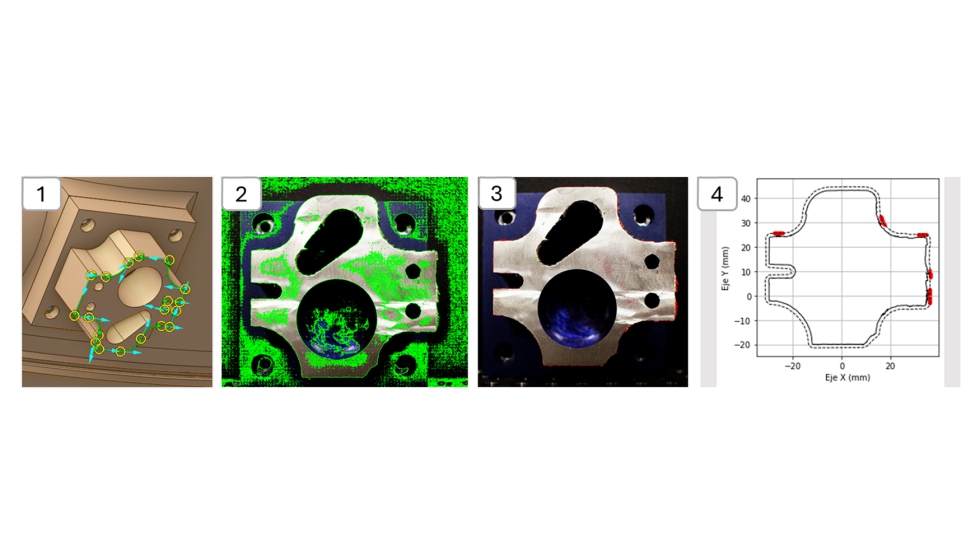
Procesos de mecanizado por descarga eléctrica
ONA AV35 Wire-cut EDM
La máquina ONA AV35 representa la última tecnología en maquinaria diseñada específicamente para el corte por hilo. Su sólida estructura, amplia área de trabajo y eficiente sistema de alimentación del hilo, permite realizar cortes precisos en materiales conductores, incluso en formas y contornos complejos. Integra una interfaz intuitiva con capacidad de personalización de los parámetros de mecanizado y avanzadas funciones de automatización, asegurando resultados de corte de alta calidad con una rugosidad superficial de hasta 0,1 micrómetros (Ra 0,1 μm). Además, el sistema automático de tensión del hilo garantiza una tensión óptima en todo momento, lo que se traduce en cortes uniformes y precisos con una velocidad de hasta 450 mm2/min.
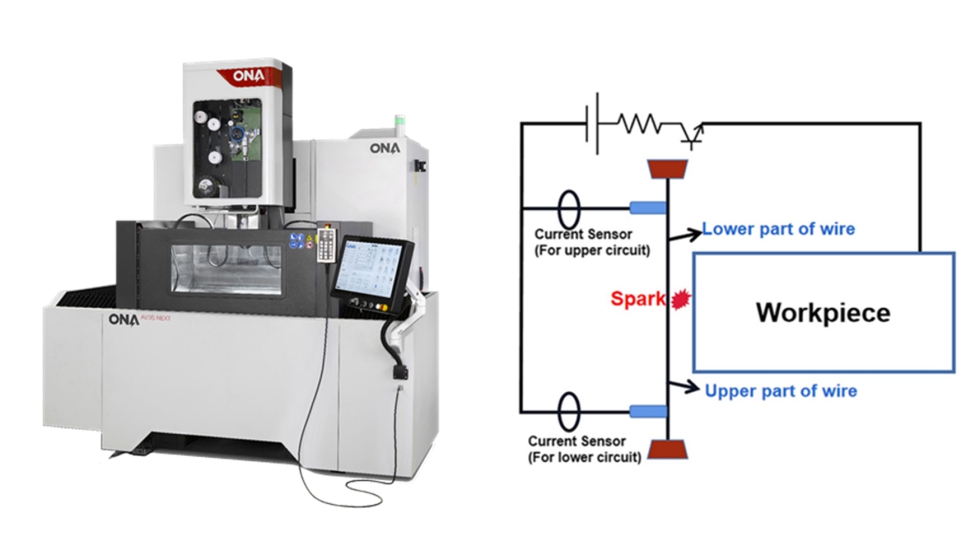
Entre los proyectos del CFAA en el ámbito de estudio de la tecnología WEDM, el proyecto MHAYA (MIG-20221059) de la convocatoria ‘Misiones 2022’ del CDTI es uno de los más interesantes, donde se busca desarrollar máquinas con capacidades inteligentes en la toma de decisiones durante proceso críticos, para salvaguardar la calidad de la pieza. En este proyecto, una de las tareas estrella en la que se está colaborando entre el CFAA y ONA EDM es el proyecto de localización de la descarga del proceso de electroerosión por hilo. Conocer el punto exacto donde cae la descarga en la longitud del hilo, permite mejorar las funcionalidades de maquina: ganar velocidad de corte, precisión, evitar roturas de hilo, etc. La idea es simple, relacionando la intensidad que pasa por el cabezal de arriba y el cabezal de abajo, se puede saber en qué altura del hilo cae la descarga. Sin embargo, si se estudia el problema con mayor profundidad, aparecen múltiples retos a resolver.
Uno de los mayores retos con el que se trabaja es la frecuencia de las señales a tratar. Tal como se ha mencionado, es necesario monitorizar la intensidad de cada descarga en dos zonas de la máquina para después relacionar estos dos valores. En un proceso normal de desbaste, se tienen 12.000 descargas por segundo y esto conlleva captar datos más frecuentemente, varias pruebas realizadas muestran la necesidad de usar una frecuencia de muestreo de 200 ms/s. Trabajar a tan alta frecuencia en la adquisición en los procesos de fabricación no es habitual y exige sensores y tarjetas específicas, además de algoritmos de cálculo optimizados.
Una vez resuelta esta problemática, se han obtenido los primeros resultados del proyecto. El primer objetivo ha consistido en aplicar la localización de la descarga a la predicción del espesor de pieza que se está cortando, para así poder adecuar los parámetros óptimos en cada momento. Para ello se ha trabajado en dos partes, una parte de calibración del algoritmo y otra parte la predicción del espesor. En la siguiente figura se muestra el diagrama de los pasos de cada parte.
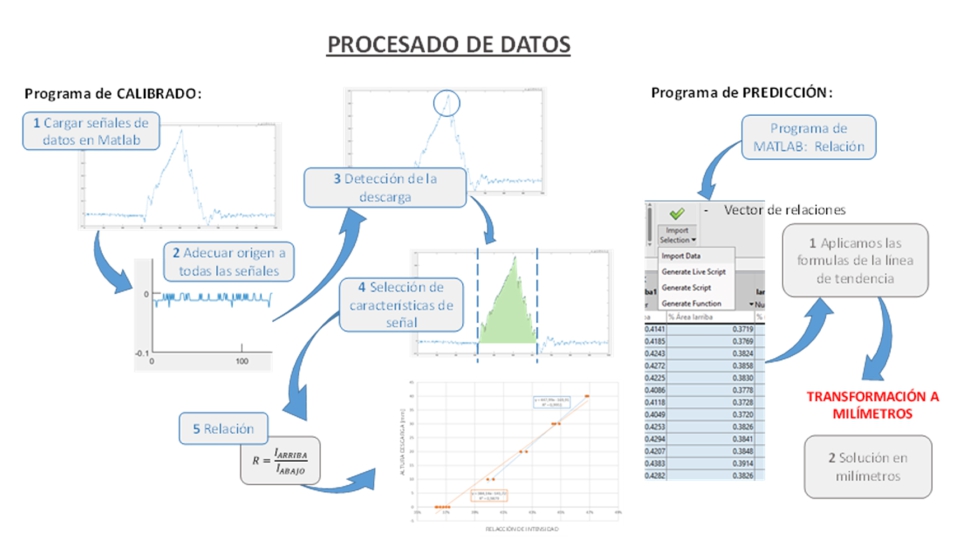
Ajustado esto, se han conseguido los primeros resultados de predicción de espesor. Los resultados son satisfactorios en cuanto a optimización de tecnología respecta. La máquina puede ajustar la tecnología optima dependiendo del espesor de corte que se encuentre, así aumenta la eficiencia y el consumo es menor. Sin embargo, para otras aplicaciones, tales como el control de precisión o la rotura de hilo, se debe trabajar en disminuir el error. En esto consiste el reto actual del proyecto y para ello se trabaja en dos líneas: la mejora del algoritmo y el uso de un sistema de adquisición más avanzado.
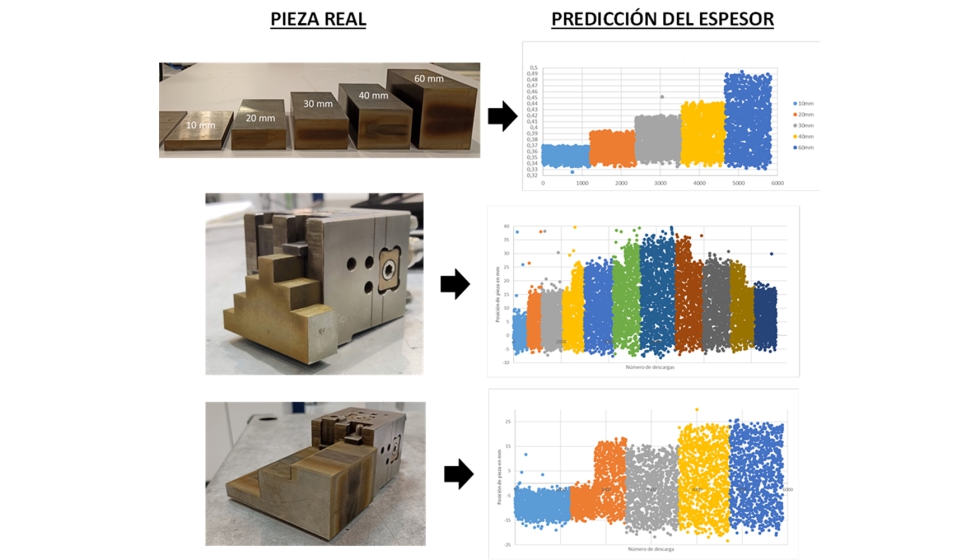
Metrología / inspección
Trimek GE X-Cube Compact 225
Trimek GE X-Cube Compact 225 es una estación de radiografía digital que permite obtener tomografías en 3D de los componentes en los que se han realizado diversas operaciones, como soldaduras, micro-fresado o fabricación aditiva. Este dispositivo facilita la detección de posibles defectos asociados a cada proceso de fabricación siendo una herramienta clave en la detección y control de porosidades de las piezas de fabricación aditiva. La estación de inspección tiene un volumen de trabajo de 600 x 900 mm y puede soportar un peso máximo de 100 kg, con una potencia de 195 KV.
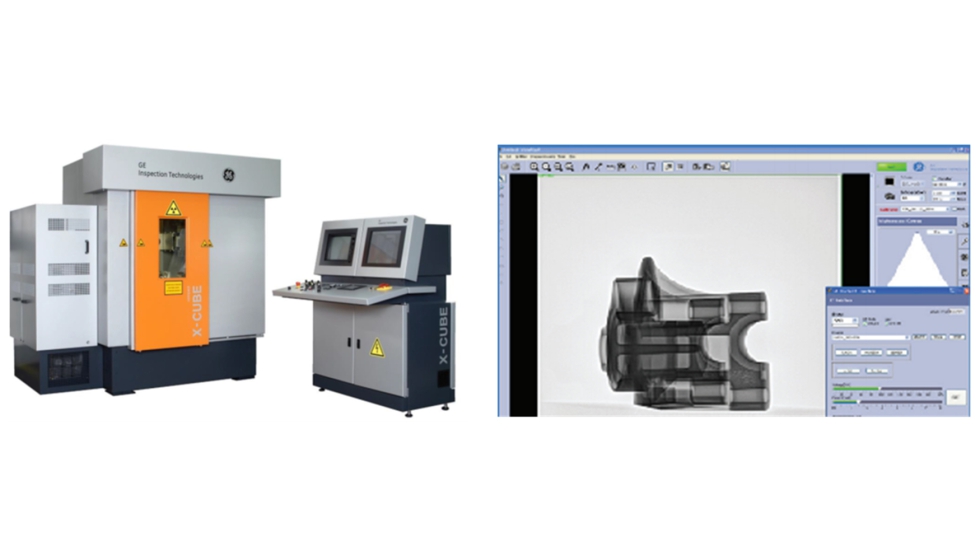
Esta tecnología aún está en proceso de maduración, pero será una herramienta interesante que ganará relevancia en los años venideros, a medida que la fabricación aditiva adquiera una mayor presencia. En esta línea, el CFAA junto con otros centros de investigación: Ideko, Ikerlan, Lortek, Tecnalia y Mondragón Unibertsitatea, trabajan en un proyecto llamado ANDREA (KK-2022/00030), financiado por el Gobierno Vasco a través de 'Elkartek 2022', que trabaja la transformación digital y el uso eficiente de recursos materiales mediante inspecciones no destructivas. Este proyecto impulsa tecnologías como la digitalización por TC, en contraposición a métodos contaminantes e imposibles de digitalizar y automatizar, como los ensayos por ácidos o partículas magnéticas. En colaboración con Innovalia, se lleva a cabo un análisis para evaluar cómo el método de digitalización de pieza ya sea mediante tomografía o escaneo láser, afecta la calidad del resultado obtenido. Este análisis se realiza en piezas de alto valor añadido.
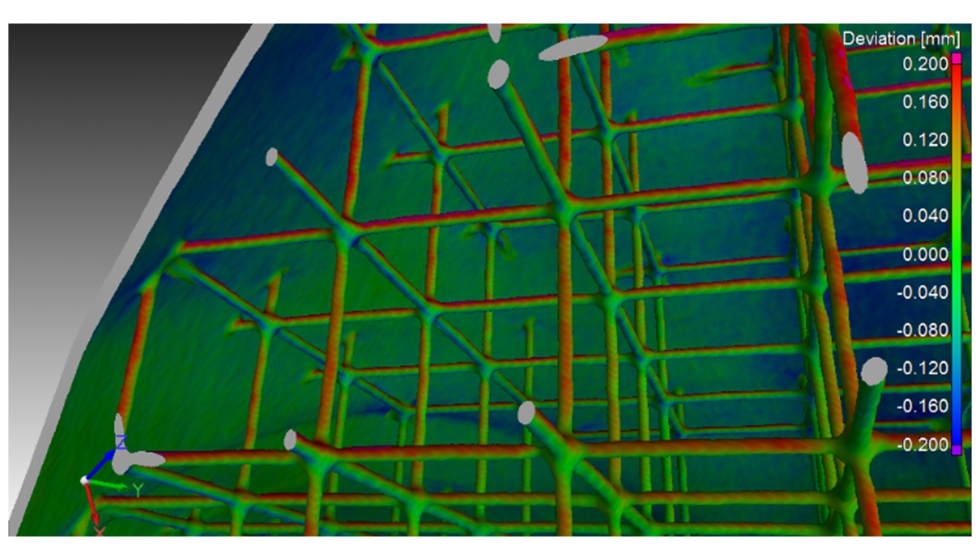
Para este caso, se realiza el análisis de desviaciones nominal/actual de un prototipo de intercambiador de calor mediante el digitalizado por TC. Ello implica la alineación del modelo volumétrico digital de la pieza real con la de su modelo nominal (por ejemplo, el modelo CAD). Esta comparación permite determinar con precisión las desviaciones, lo que resulta crucial para identificar si las discrepancias provienen del proceso de inspección o de errores en el proceso de fabricación en sí.
Fabricación aditiva
RenAM 500
RenAM 500 es un sistema mejorado de impresión 3D de metal que emplea tecnología de fusión de lecho de polvo. Con un volumen de construcción mejorado en relación con su predecesora RenAM 400, láseres de alta potencia y un sistema de gestión de polvo integrado, permite la fabricación de componentes metálicos complejos con excelentes propiedades mecánicas. El sistema utiliza un sistema de gas en cascada para asegurar condiciones de procesamiento uniformes y una eliminación eficiente de las emisiones del proceso. Su sistema óptico de enfoque dinámico minimiza los tiempos de fabricación al optimizar la distribución de la energía láser. Además, incorpora sistemas integrados de gestión del polvo, supervisión avanzada y control basados en sensores fotodiodos, junto con software de fácil manejo, para garantizar un funcionamiento eficiente y una calidad óptima en las piezas fabricadas.
El CFAA está activamente involucrado con esta tecnología y con las posibilidades que puede ofrecer, así lo demuestra con su participación en el proyecto europeo ADAM^2, financiado por el programa Horizonte 2020 (subvención n. 862025). El proyecto busca mejorar la fabricación de componentes críticos, como las palas de turbinas de un motor aeronáutico mediante la inclusión de microestructuras para obtener una pieza con propiedades mejoradas. Para ello, se han diseñado diferentes estructuras de tipo lattice o celulares, las cuales han sido desarrolladas en colaboración con Technion e INRIA, permitiendo reducir el peso de los componentes a la vez que se ha mejorado su rigidez estática tanto antes como después de ser mecanizados, reduciendo el amortiguamiento de este, como se puede ver en las siguientes imágenes.
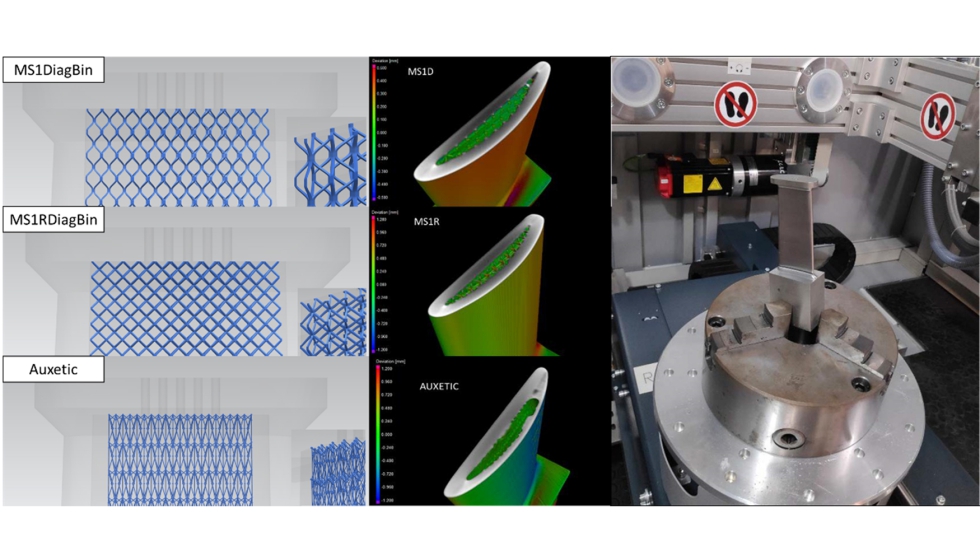
El estudio comparativo entre álabes con microestructura y álabes sólidos revela diferencias significativas dependiendo de las variaciones internas, que impactan en la resistencia estática de la pieza.
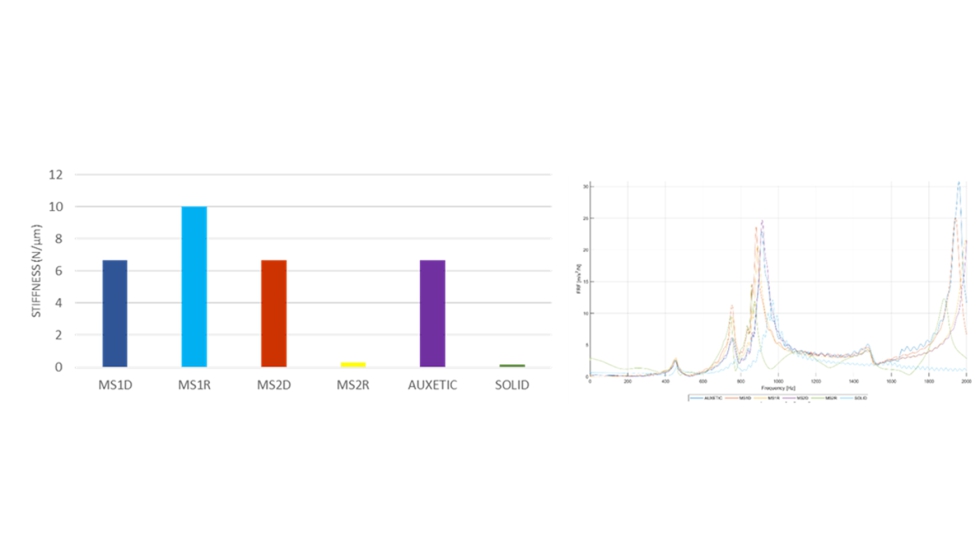
Conclusiones
En resumen, la reducción de la huella ambiental se ha convertido en una preocupación de máxima prioridad para gobiernos e instituciones en todo el mundo, como se demuestra mediante las ayudas que ofrecen estas. Es alentador ver cómo el sector empresarial está cada vez más comprometido en la búsqueda de soluciones innovadoras para minimizar la generación de residuos y optimizar el uso de materiales en los procesos de fabricación.
El sector de la fabricación, especialmente el de la producción de metal, siempre ha sido percibido como un proceso contaminante, debido a las emisiones generadas y al uso de aceites como lubricantes o refrigerantes en el proceso de corte. Además, se debe añadir el constante goteo de desechos de herramientas usadas que quedan inservibles. No obstante, la industria avanza de manera consciente y en recientes innovaciones ya está logrando reducir su impacto; implementando nuevos refrigerantes, herramientas de corte más eficientes y procesos de reutilización y reciclaje de las mismas, o evitando la pérdida de productos mediante la monitorización. Estos enfoques no solo benefician al medio ambiente y a la explotación de recursos naturales, sino también al ahorro económico y a la mejora de las empresas.
Sin embargo, queda claro que aún hay mucho trabajo por hacer. Se necesitan políticas más sólidas, incentivos adecuados y una colaboración continua entre los sectores industriales y de investigación para abordar eficazmente estos desafíos globales de manera eficaz. Con un compromiso renovado y acciones concretas, podemos construir un futuro más sostenible y equitativo para las generaciones venideras.
Referencias
[1] Basque Ecodesign Center – Ecodiseño y economía circular: Estrategias de diseño de producto que favorezcan la aplicación de la Economía Circular. (s. f.). https://www.basqueecodesigncenter.net/Paginas/Ficha.aspx?IdMenu=de39febf-1d3a-461c-aa61-dd091ea99e96&Idioma=es-ES
[IBARMIA] Davoodi, B., & Tazehkandi, A. H. (2014). Experimental investigation and optimization of cutting parameters in dry and wet machining of aluminum alloy 5083 in order to remove cutting fluid. Journal of Cleaner Production, 68, pp 234-242.
[GMTK] Amigo, F.J., Urbikain, G., de Lacalle, L.N.L. et al. On the effects of cutting-edge angle on high-feed turning of Inconel 718© superalloy. Int J Adv Manuf Technol 125, 2023, pp 4237–4252.
[MAZAK] Jun Zha, Nagore Villarrazo, Gonzalo Martínez de Pisson, Yipeng Li, Huijie Zhang & Luis Norberto López de Lacalle. An accuracy evolution method applied to five-axis machining of curved surfaces. The International Journal of Advanced Manufacturing Technology, 125, 2023, pp 3475–3487.
[DANOBAT] C.H. Lauro, L.C. Brandão, D. Baldo, R.A. Reis, J.P. Davim. Monitoring and processing signal applied in machining processes – A review. Measurement, 58, 2014, pp 73-86.
[EKIN] I. Aldekoa, A. del Olmo, L. Sastoque, S. Sedino-Mouliet, U. Lopez- Novoa, L.N. López de Lacalle. Early detection of tool wear in electromechanical broaching machines by monitoring main stroke servomotors. Mechanical Systems and Signal Processing, Volume 204, 2023, 110773.
[MEK&BOT] Mikel González, Adrián Rodríguez, Unai López-Saratxaga, Octavio Pereira, Luis Norberto López de Lacalle. Adaptive edge finishing process on distorted features through robot-assisted computer visión. Journal of Manufacturing Systems, Volume 74, 2024, pp 41-54.
[ONA] U. Küpper, E. Tchoupe, A. Klink, T. Bergs. Prediction of Geometrical Accuracy In Wire EDM By Analyzing Process Data. Procedia CIRP, 113, 2022, pp 23-28.
[XRAY] Ziólkowski, G., Chlebus, E., Szymczyk, P. et al. Application of X-ray CT method for discontinuity and porosity detection in 316L stainless steel parts produced with SLM technology. Archiv.Civ.Mech.Eng 14, 2014, pp 608–614.
[AM] Lesyk, D., Martinez, S., Dzhemelinkyi, V., & Lamikiz, A. Additive manufacturing of the superalloy turbine blades by selective laser melting: surface quality, microstructure and porosity. In International Conference ‘New Technologies, Development and Applications’, 2020, pp. 267-275.