Fabricación aditiva de grandes piezas mediante tecnología BAAM
Departamento de Fabricación Avanzada de Fundación Idonial
31/05/2023Esto es posible debido fundamentalmente a dos factores: una elevada tasa de deposición de material, que oscila entre los 10 y los 100 kg/h, y la cinemática de los propios equipos BAAM, que permite una rápida impresión.
Esta tecnología tiene numerosas aplicaciones en la fabricación de piezas para la industria aeroespacial, la automotriz, la construcción, la producción de utillajes y la fabricación de elementos de máquinas. También puede utilizarse para la producción de moldes de fundición y prototipos a gran escala. Además, ofrece beneficios medioambientales, ya que la producción aditiva reduce el desperdicio de materiales y energía en comparación con los métodos de fabricación tradicionales, pudiendo utilizar materiales reciclados o biodegradables para la producción de piezas, lo que reduce aún más su impacto ambiental.
Idonial, pionero en las tecnologías aditivas, desarrolló en el marco del proyecto Cervera Readi (Red de Excelencia en Fabricación Aditiva) un cabezal BAAM, integrable en un sistema robótico industrial. El presente artículo resume el concepto desarrollado, las problemáticas confrontadas, y los resultados obtenidos.
Esquema básico de cabezal de impresión BAAM
La tecnología fundamental de un sistema de impresión BAAM está basada en el principio de la inyección, en el que el material en formato granza/pellet desciende por una tolva donde se encuentra acumulado, para mediante un sistema de husillo desplazar el material hacia la zona de la boquilla o de salida. A medida que el material avanza por el husillo se va calentando, hasta conseguir una temperatura superior a su temperatura de transición vítrea, lo que permite su deposición.
A lo largo del husillo se pueden distinguir tres etapas principales, donde la temperatura en dichas etapas varía hasta conseguir que el material en formato pellet alcance la temperatura de fusión para después ser depositado. La distribución que se ha utilizado para el cabezal diseñado por Idonial es la que se muestra en la Figura 1.
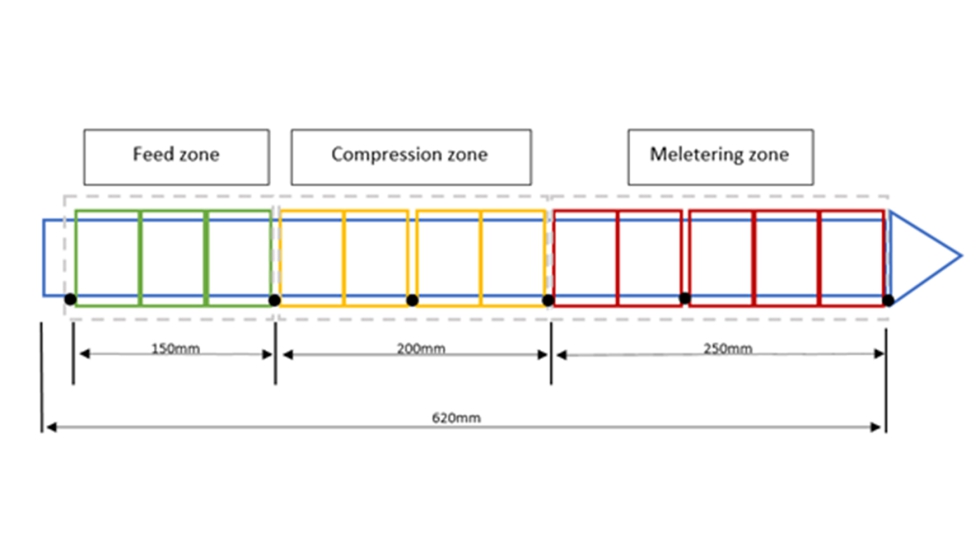
Figura 1. Esquema básico de un husillo de inyección.
En la distribución de la Figura 1 se puede observar el posicionamiento de las resistencias, que se encargan de controlar la temperatura de las distintas zonas del husillo, así como el posicionamiento de los termopares que sirven para controlar la temperatura entre las distintas zonas en bucle cerrado. Como se puede observar, la zona situada más cercana a la boquilla dispone de un mayor número de instrumentos de control y calefacción, ya que dispone de dos zonas calefactadas distribuidas en grupos de dos y tres resistencias.
Mediante un PLC se realiza el control tanto del giro del motor como de la distribución de la potencia calorífica entre las distintas resistencias del cabezal, permitiendo un ajuste de estos parámetros a lo largo de todo el proceso de impresión 3D. Es importante significar que estos parámetros y el ajuste necesario son característicos de cada material, dado que cada uno de ellos presentará diferentes temperaturas de operación y diferentes reologías.
En cuanto a los elementos complementarios al propio husillo y el sistema de calefacción y control descritos, el sistema consta de un servomotor que, mediante un acoplamiento, es capaz de transmitir el giro al husillo donde se transporta el material en un estado viscoso hasta la boquilla para, posteriormente, ser depositado en la zona de fabricación generando las sucesivas capas que formarán la pieza.
Por otra parte, un aspecto muy importante a tener en cuenta en este tipo de tecnología es la alimentación del material en formato granza/pellets, ya que debido a la longitud del husillo y la tasa de deposición que ofrece la tecnología, el consumo de material es de un alto volumen en muy poco tiempo. Por ello, para solventar esta problemática, se empleó un alimentador basado en un sistema Venturi, encargado de realizar la carga de material de una forma continua desde el reservorio de material.
El cabezal de BAAM se instaló en un robot Kuka KR500-2, que en base a sus 6 grados de libertad permite una gran versatilidad de movimientos y trayectorias. Ello introduce dificultades adicionales, ya que estando los sistemas robóticos industriales más orientados hacia la manipulación de piezas/replicación sistemática de movimientos puntuales que hacia el trazado de trayectorias complejas, ello aumenta la complejidad a la hora de hallar modos eficaces de transferir estas trayectorias al sistema robótico. Esto se ha resuelto procesando la información mediante un ‘slicer’, un software de ‘rebanado’, que divide la geometría del archivo CAD 3D de la pieza en capas, base para la definición de la trayectoria de impresión de cada capa para el cabezal BAAM, realizado mediante un desarrollo basado en el complemento Grasshopper que ofrece el software Rhinoceros.
Pruebas de impresión del sistema. Problemáticas y soluciones
Se realizaron diversas pruebas para comprender mejor el comportamiento del cabezal, y de manera específica la transformación sufrida por el material a lo largo del husillo. Ello supuso un importante incremento sobre el conocimiento previamente existente en la organización, basado de manera fundamental en la impresión de material en formato pellet/granza a escalas menores, mediante cabezales de considerable menor dimensión, que únicamente contenía dos zonas calefactadas, y por lo tanto no era comparable en términos de la dinámica y el control térmico del sistema.
Posteriormente se llevaron a cabo una sucesión de pruebas de ajuste y deposición con PLA (ácido poliláctico), donde se observó que la fluidez del material era muy difícil de controlar, limitando las geometrías que se podían fabricar, puesto que la concentración de calor durante la fabricación era excesiva. Por tanto, lo que se realizó para solventar esta problemática fue la construcción y puesta en marcha de un sistema de refrigeración para reducir la temperatura del material tras su deposición en cada capa, a medida para este sistema. Este sistema fue efectivo hasta los propios límites del material PLA, en esencia presentando una excesiva fluidez y baja consistencia, si bien se obtuvieron resultados razonablemente satisfactorios, y fue posible fabricar piezas como la mostrada en la Figura 3, que hizo uso de 12 kg de material en formato pellet, y alcanzó una altura y diámetro aproximados de 80 y 60 cm, respectivamente. Se pasó por ello a realizar pruebas adicionales con un material basado nuevamente en PLA, pero combinado al 20% con de fibras de celulosa, observando que, gracias a la presencia de fibras en su composición, no necesitaba de refrigeración adicional para mantener la sustentación de la pieza. Realizando los ajustes pertinentes, fue posible fabricar piezas como las mostradas en las Figuras 2, 4 y 5, piezas con un altura, largo y peso considerables (respectivamente, 67 cm, 84 cm y 5,8 kg de material), en un tiempo de fabricación de unas 6 horas.
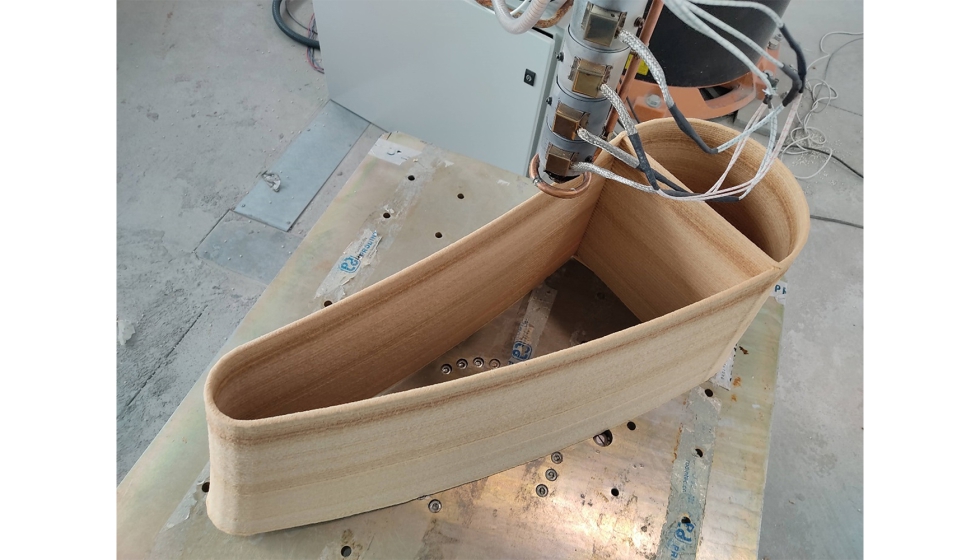
Figura 2. Cabezal BAAM durante la impresión de una pieza con geometría genérica tipo álabe.
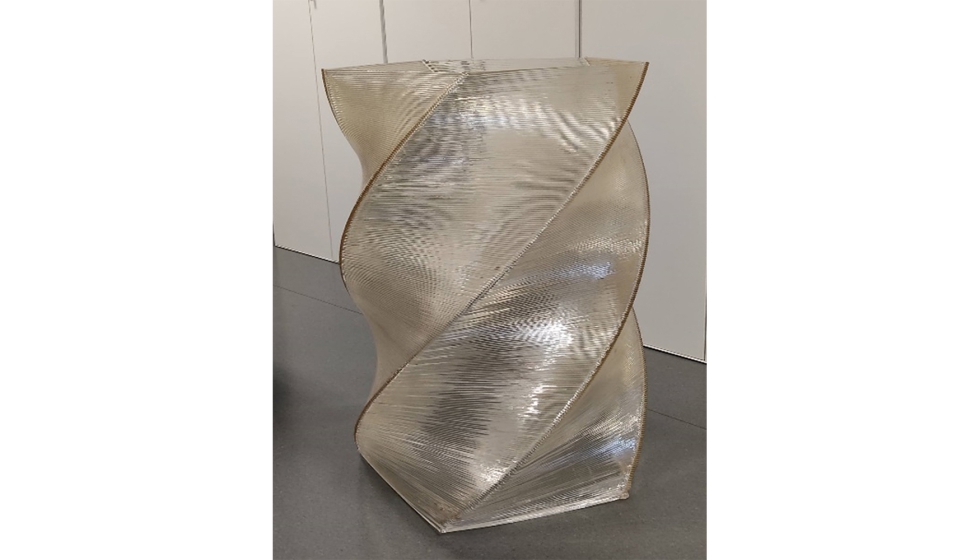
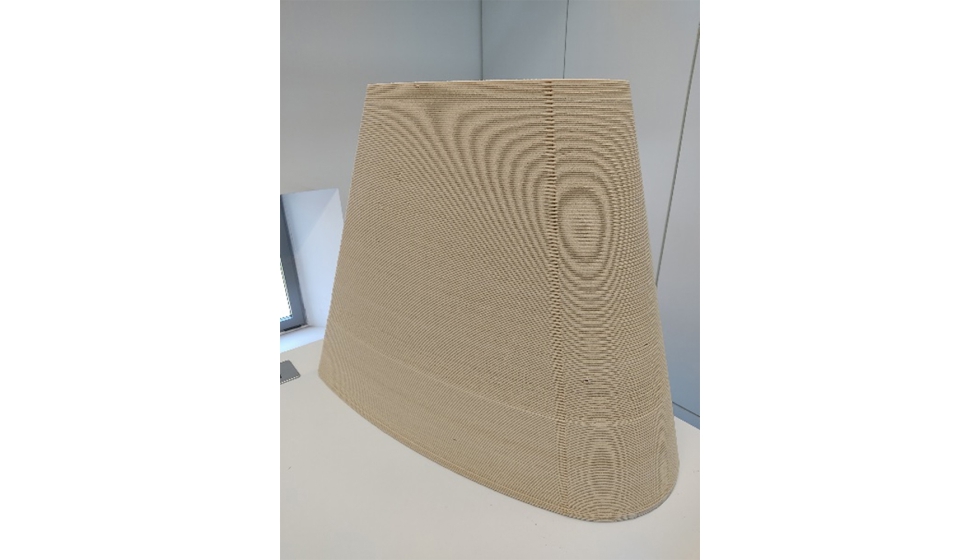
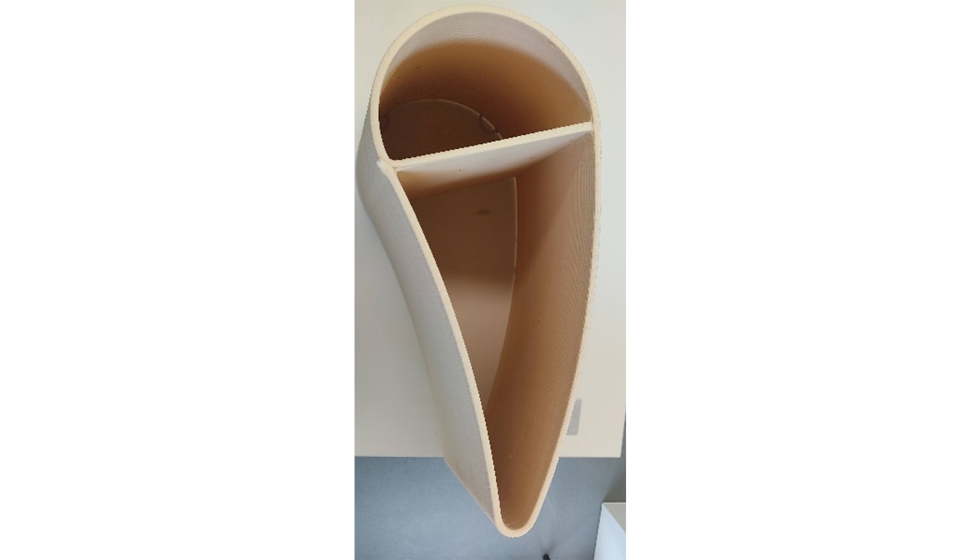
Uno de los principales retos durante los trabajos descritos fue el de lograr un adecuado control del calor suministrado por las resistencias. La dificultad principal radica en lograr una administración de energía específica para cada material en cada punto del husillo, a fin de evitar, por ejemplo, que en la zona de entrada del material al cabezal se alcance una temperatura excesivamente alta que pudiera dar lugar a aglomeraciones de material y atascos.
Otra de las dificultades detectadas fue el estudio y selección del motor adecuado a la longitud del husillo, para conseguir el correcto giro del motor y la correcta deposición del material. El cálculo específico del par adecuado es complejo, al tenerse en cuenta que el material en formato pellet presenta a lo largo de su flujo una transición entre estado sólido, semifluido y fluido en el interior del cabezal, variando además el par necesario entre los diferentes materiales que se pueden procesar mediante esta tecnología. La granulometría del material también supone un reto a la hora de alimentar el husillo principal ya que, debido a la disposición del cabezal y la posición donde se encuentra situada la zona de entrada del material, así como la disposición del cabezal durante la fabricación, dificulta la entrada del material a no ser que este tenga una geometría completamente esférica, y sea un material con una morfología uniforme que no se adhiera a la canalización de la zona de alimentación del husillo principal.
Cabe destacar además la próxima implementación de una nueva entrada de material, que facilite la introducción idónea del material en formato pellet en el husillo, y evitar así los problemas de alimentación de material.
Estado actual. Trabajos futuros
El conocimiento adquirido a lo largo del proceso descrito es altamente relevante para Idonial, ya que ha conllevado el desarrollo de una primera capacidad para la fabricación aditiva de piezas de gran formato, para diversos campos y aplicaciones. Las necesidades de mejora detectadas durante el proceso están siendo desarrolladas e implementadas, y se prevé en el futuro próximo incorporar materiales con un mayor carácter técnico, como puedan ser los materiales cargados con fibras de carbono, que permitirán obtener un flujo mucho más uniforme y en paralelo conseguir una mejora de las propiedades mecánicas de las piezas generadas y un mejor acabado estético de las mismas.
En base a las capacidades ya obtenidas y las mejoras en marcha, Idonial está en condiciones de explorar y abordar con clientes y colaboradores las posibles aplicaciones en el campo de la fabricación aditiva de gran formato.