Nuevas cintas transportadoras y sistemas de separación de MTF Technik en Equiplast 2023
La separación de la colada en la industria del plástico tiene un gran impacto en la productividad y en los costos de producción. Y por este motivo, en la feria Equiplast 2023, MTF Tecknik y su representante en España, Coscollola, presentarán una amplia gama de innovaciones y avances en tecnología de transporte, separación de piezas y automatización, junto con sus superventas habituales.
Los visitantes tendrán la oportunidad de descubrir la versatilidad y flexibilidad de los transportadores MTF Multi-Tech, que cuentan con sistemas especiales. Además, podrán conocer la amplia variedad de cintas, unidades de transporte y variantes en sus estructuras base, así como diversas opciones de equipamiento que ofrece MTF Tecknik y Coscollola.
Para lograr una separación eficiente es importante utilizar la tecnología de separación adecuada y optimizar los procesos de separación existentes.
Algunas técnicas económicas comunes de separación de coladas incluyen el uso de selectores de canales manuales o automáticos, válvulas divergentes, separadores de husillo, separadores de rodillos y tambores de separación.
Es importante evaluar cuidadosamente cada técnica de separación en función de los parámetros específicos de producción, como la geometría de las piezas y la colada, la tasa de producción y el tiempo de ciclo. Con la técnica y la optimización adecuadas del proceso, se pueden lograr tasas de separación asequibles y muy productivas.
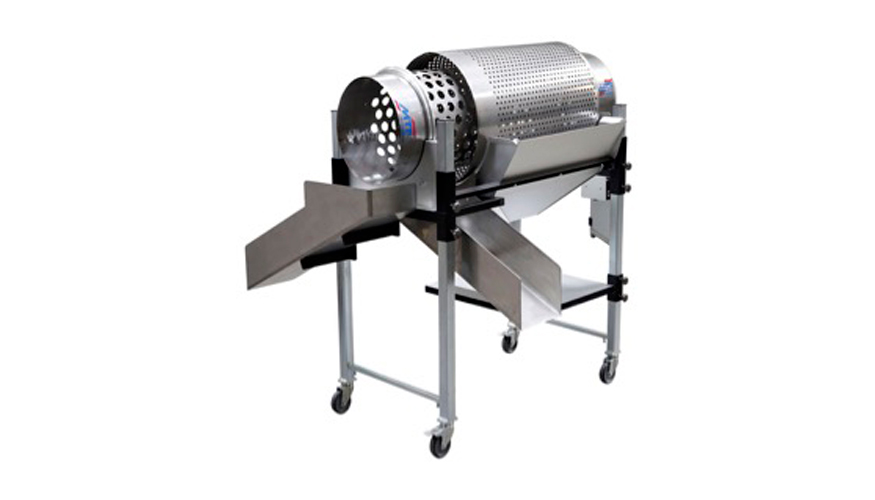
A pesar de los moldes de colada caliente, sigue habiendo innumerables aplicaciones en las que la separación posterior entre la pieza utilizable y el bebedero es inevitable. Además de la separación manual, se utilizan recogedores de colada, válvulas de desvío, accesorios de separación en cintas transportadoras o tambores de separación. Aunque en general se trata de tecnologías consolidadas, en muchas empresas existe un enorme potencial de productividad que a menudo no se aprovecha en la actualidad.
Aquí hay un ejemplo: En la producción de piezas técnicas, se producen dos piezas y una colada por inyectada. El tiempo de ciclo es de 7,5 segundos. De esto, aproximadamente 1,5 segundos se destinan a la eliminación del ramal mediante un picker. Esto significa un potencial de productividad teórico de hasta el 20% si se puede instalar la separación de coladas abajo.
Sin embargo, esto solo es realista si se utiliza eficientemente la tecnología de separación adecuada. Aquí, muchas empresas ya están satisfechas con tasas de separación del 90%, aunque en algunos casos cambios simples en la configuración del equipo existente pueden mejorar aún más la calidad de la separación.
Depende de muchos parámetros, qué tecnología de separación es adecuada. Además del tiempo de ciclo y el número de cavidades, la geometría de la pieza útil y la colada juegan un papel decisivo. Para la separación abajo, siempre es necesaria una cierta diferencia de tamaño. En muchos casos, esto es una diferencia de altura, pero también puede ser una dimensión de superficie diferente.
La siguiente lista cubre los principales tipos de equipos y destaca las características esenciales de calidad:
Separadores de husillo
Para la mayoría de las aplicaciones en la industria del plástico, se pueden utilizar separadores de husillo con buenos resultados. En este caso, se monta un rodillo giratorio con un perfil de husillo aplicado sobre una placa de chapa fija. La separación se determina por la distancia entre el rodillo y la chapa, donde las piezas pequeñas se deslizan debajo del husillo y las piezas grandes se empujan hacia un lado.
Para lograr una tasa óptima de separación con estas unidades, varias características de diseño son importantes. Es fundamental que el rodillo de husillo sea estable y tenga soporte en ambos lados, de modo que el rodillo tenga la misma distancia a la placa de descarga en todas partes y no “vibre”.
Además, es crucial que la velocidad de rotación del husillo pueda ajustarse a la tarea de separación correspondiente. Algunos componentes requieren un proceso de separación “tranquilo”, mientras que otras piezas se pueden separar mejor si el rodillo de husillo gira lo más rápido posible. En este contexto, lo ideal es una unidad de accionamiento separada del tornillo con protección de sobrecarga integrada para evitar el atasco de piezas y cumplir con los requisitos de seguridad laboral óptima. De esta manera, la velocidad de rotación del husillo se puede controlar de manera independiente de la velocidad de la cinta de alimentación. Esto es particularmente importante si, por ejemplo, las piezas tienen que enfriarse primero en la cinta transportadora. Por lo tanto, es necesario una velocidad de cinta muy lenta o en intervalos, y al mismo tiempo, un rodillo de husillo giratorio rápido para obtener una tasa óptima de separación. Esto solo se puede lograr con unidades de accionamiento independientes.
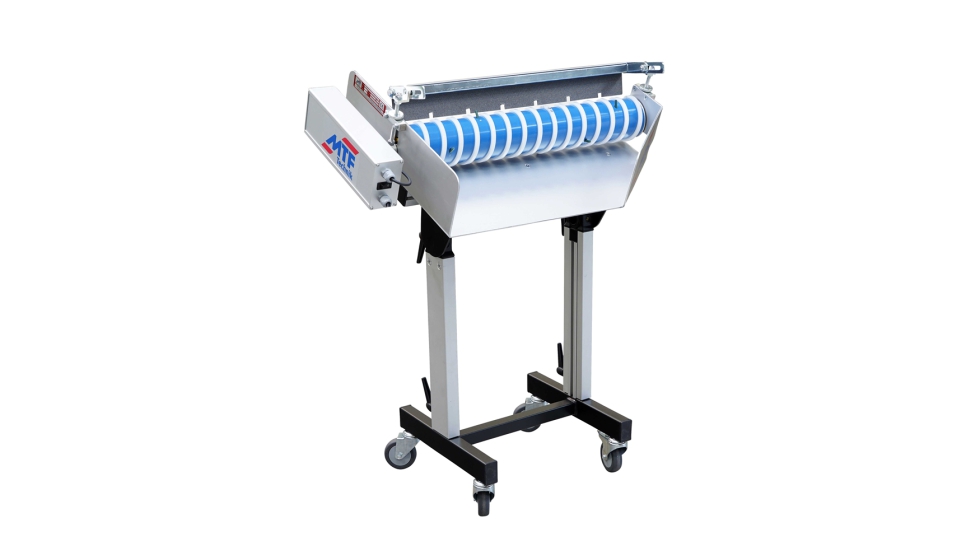
Separadores de husillo.
Otro detalle importante son las púas flexibles que se deben colocar a lo largo de la circunferencia del husillo y que sirven para aflojar el material a separar. Esto asegura que las piezas más grandes que se colocan delante del husillo y han bloqueado el paso para las piezas más pequeñas siempre se muevan, despejando así el paso para las piezas más pequeñas.
Un raspador flexible sobre el rodillo de husillo evita que las piezas salten sobre el husillo durante la alimentación, por ejemplo, por una cinta transportadora. Colisionan con el raspador y se devuelven al proceso de separación.
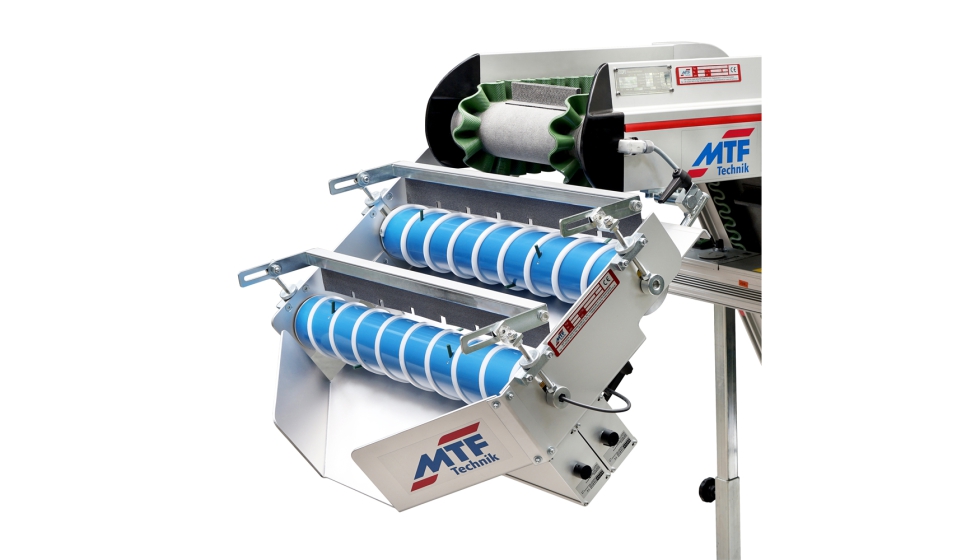
Separadores de rodillos y separadores de discos
Las combinaciones de piezas y canales, donde, por ejemplo, un canal plano y muchas piezas pequeñas deben separarse entre sí, generalmente se pueden separar bien con separadores de rodillos o separadores de discos. Los canales planos más grandes pasan por encima de los rodillos, mientras que las piezas pequeñas caen entre los rodillos.
Estas técnicas de separación se pueden utilizar para separar piezas y canales con diferentes áreas de superficie.
Al igual que con los separadores de husillo, el enfoque principal aquí es el soporte estable y de doble cara de los rodillos individuales y el control individual de velocidad para lograr un resultado de separación óptimo.
Además, debería ser posible utilizar diferentes recubrimientos de rodillos. Dependiendo de la tarea y el comportamiento de las piezas, puede ser necesario que los recubrimientos de los rodillos sean muy adherentes o suaves.
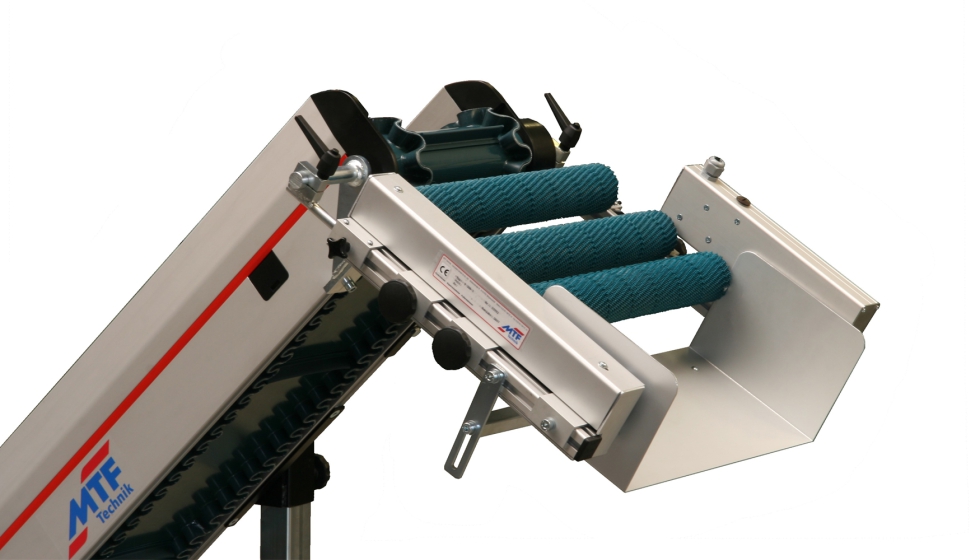
Tambores de separación
Los tambores de separación se utilizan a menudo para mayores cantidades de producción o combinaciones de piezas y canales donde la circulación puede mejorar el resultado de separación. Mediante el proceso de recirculación, se puede lograr que los problemas de piezas huecas (es decir, el canal se encuentra dentro de la pieza) se resuelvan y se separen mucho mejor que con accesorios de separación.
Existen varios tambores de separación, dependiendo de la diferencia en la geometría de las piezas.
Tambores de separación de rodillos
Los tambores de separación de rodillos se utilizan para separar componentes y canaladuras con diferentes dimensiones de altura. Se pueden utilizar para una variedad de tareas de separación. Aquí hay tambores de separación con ajuste individual del espacio de separación o dispositivos con un ajuste central planetario.
Con el ajuste individual, cada rodillo se fija individualmente en la jaula del tambor. La distancia entre dos rodillos define el espacio de separación. Dado que este ajuste es relativamente laborioso, este tipo de tambor de separación solo es adecuado para aplicaciones en las que una máquina está ocupada con un artículo durante mucho tiempo o en las que se pueden separar varias combinaciones de componentes/canaladuras similares con un solo ajuste.
Los tambores de separación con ajuste central del espacio de separación, por otro lado, son adecuados si se desea separar una amplia gama de productos con la ayuda del tambor. El ajuste central ofrece un ajuste rápido: se puede ajustar a una nueva combinación de productos en unos pocos segundos. En este caso, dos rodillos siempre forman un par firmemente conectado, de modo que solo cada segundo espacio entre los rodillos también es un espacio de separación. Esto reduce el número de espacios de separación en comparación con un tambor de separación con ajuste individual. Por lo tanto, el volumen máximo de procesamiento es más bajo.
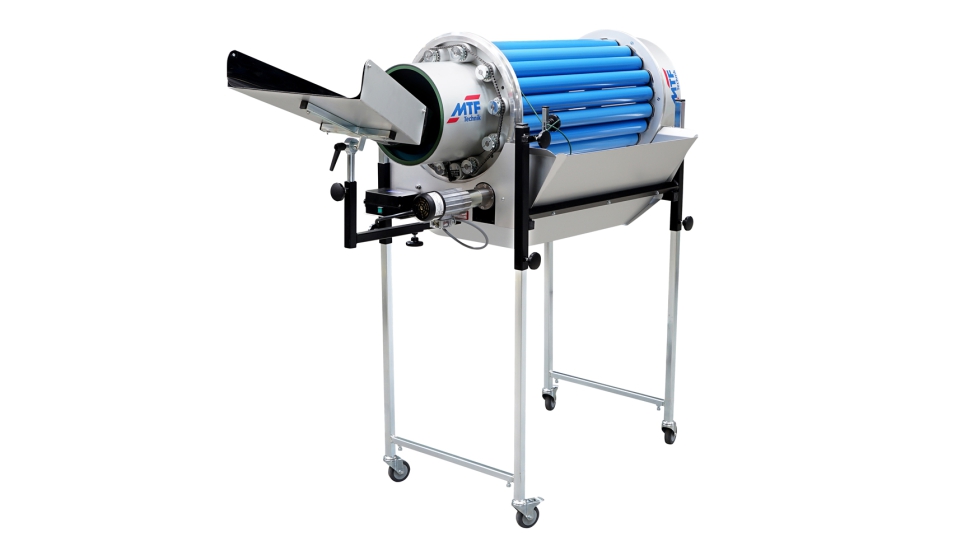
Tambores de separación de rodillos.
Tambores perforados
Los tambores perforados se utilizan cuando las piezas a separar no difieren en altura sino en su superficie (por ejemplo, monedas con diferentes diámetros, pero el mismo grosor de material). La ventaja de los tambores perforados es, por un lado, el bajo precio y, por otro lado, el alto volumen de procesamiento. Dado que se puede elegir un paso de agujero muy pequeño, el tambor perforado consiste casi exclusivamente en espacios de separación, es decir, los componentes más pequeños tienen muchas oportunidades de caerse del tambor por revolución.
La desventaja de los tambores perforados es que hay una geometría de agujero fija y esto significa que el dispositivo solo se adapta a un rango limitado de piezas. Sin embargo, las jaulas de tambor completas se pueden reemplazar fácilmente para cubrir un espectro correspondientemente más amplio de piezas.
Dependiendo de la aplicación, se pueden utilizar muchos materiales diferentes para las jaulas de tambor. Además de las jaulas de acero y acero inoxidable, se pueden utilizar materiales de goma o silicona para garantizar la mejor protección posible de las piezas.
Tambores de separación con tubos de manga
Los tambores de separación con tubos de manga son una forma especial de tambores perforados. Aquí, se aplican tubos de manga en la circunferencia exterior de la jaula del tambor en extensión a los agujeros, que tienen la geometría y el tamaño de los agujeros. Esto asegura que, por ejemplo, las piezas en forma de S no puedan “moverse” a través de los agujeros. Estas piezas solo pueden sumergirse en el tubo de la manga con su punta, pero luego caen de nuevo en la jaula del tambor.
De la misma manera, los tubos de manga evitan que los sistemas de alimentación propensos a enganches se atasquen en los agujeros.
Tambor rectangular
Los tambores rectangulares representan un tipo completamente independiente de tambor de separación. Estos tambores de separación tienen cuatro espacios de separación, cada uno consistente en dos superficies paralelas de 80 mm de ancho. La jaula del tambor está completamente hecha de acero inoxidable, por lo que estos tambores también se pueden usar en la producción de artículos de tecnología médica o producción en salas limpias, por ejemplo. La limpieza de las superficies lisas es muy fácil.
Al igual que con los tambores de separación de rodillos o los separadores de tornillo, la separación también se lleva a cabo aquí - como con los tambores de separación de rodillos o los separadores de tornillo - mediante la dimensión de altura de los componentes. Sin embargo, el diseño de la separación paralela a la superficie también evita que los componentes se muevan a través de ella.
La separación se ajusta mediante husillos roscados. La altura de la separación se puede ajustar con precisión y leer mediante escalas aplicadas. Esto da como resultado una alta precisión de repetición.
Otra característica importante de este tambor de separación es el proceso patentado por MTF Tecknik en el que la separación se abre con cada revolución. Debido a un mecanismo especial, las separaciones se abren brevemente en la parte superior. Esto permite separar componentes en tambores rectangulares, lo que causaría problemas en otros tambores. Estos incluyen, por ejemplo, componentes muy pequeños o cónicos que pueden atascarse en los tambores de separación de rodillos. Pero también materiales muy blandos (por ejemplo, caucho o silicona) se pueden procesar muy bien en este tipo de tambor.
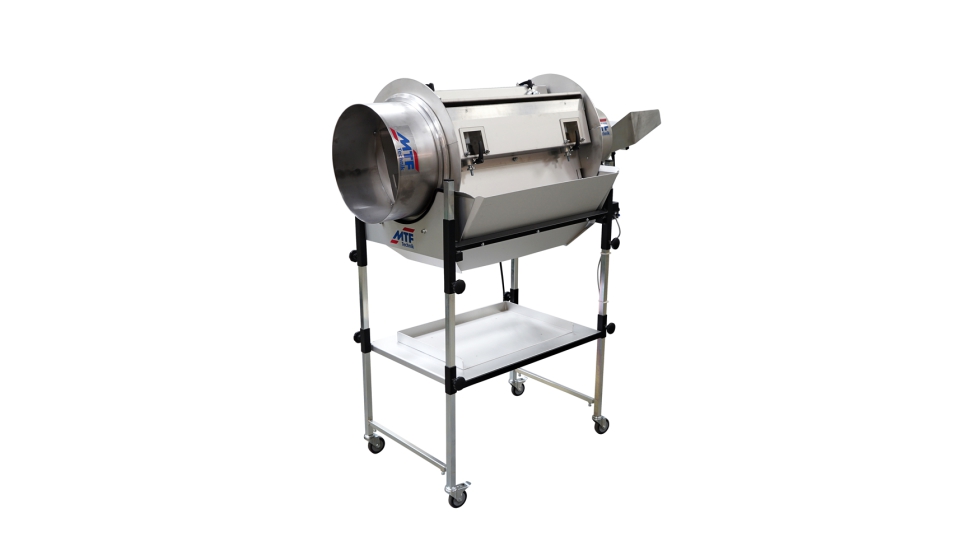
Tambor rectangular.