Poliamida PA6GF30 en la impresión 3D como sustituto del aluminio (Al)
El proceso de modelado por extrusión de materiales compuestos en 3D muestra un gran potencial en términos de rentabilidad en comparación con otros procesos de impresión en 3D. En colaboración con la Universidad de Rostock, la start-up AIM3D ha realizado una serie de pruebas con el material PA6GF30 (BASF Ultramid B3WG6). Las muestras de ensayo se imprimieron en las máquinas AIM3D ExAM 255 y ExAM 510 y la resistencia a la tracción de las muestras se comparó con procesos alternativos como el moldeo por inyección y la impresión 3D convencional. Las evaluaciones de las pruebas del material fueron sorprendentes: la PA6GF30 impresa es claramente superior a otros procesos de impresión 3D y casi alcanza la resistencia a la tracción del moldeo por inyección clásico.
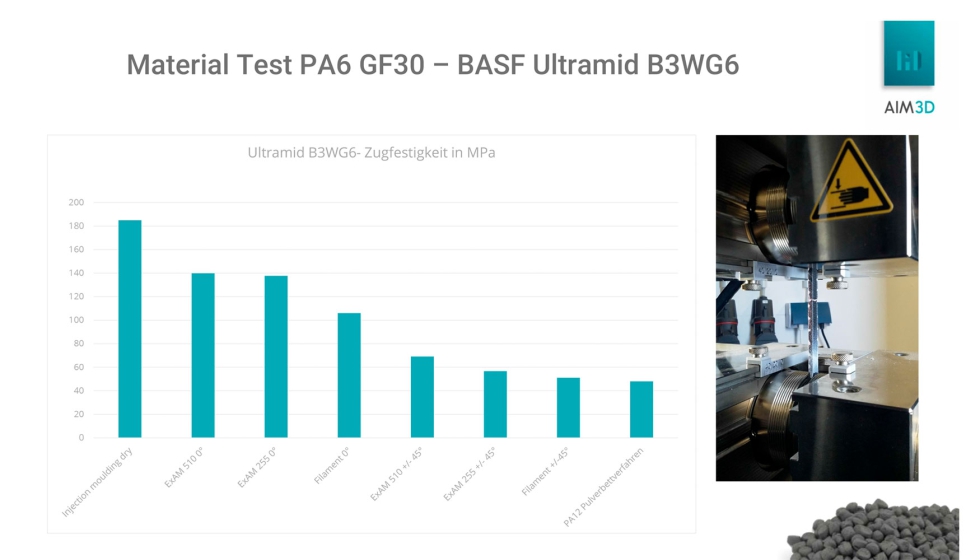
Gráfico 1: Comparación de las resistencias a la tracción de diferentes procesos de adición para el procesamiento de PA6GF30 (BASF Ultramid B3WG6). Foto: AIM3D GmbH, Rostock (Alemania).
La poliamida reforzada con fibra de vidrio impresa en 3D presenta una gran resistencia a la tracción
Hoy en día, la PA6GF30 es un material indispensable en las aplicaciones industriales de producción en serie, que combina de forma casi ideal unas elevadas propiedades mecánicas con la resistencia a la temperatura y a los medios. De este modo, el PA6GF30 es un material plenamente consolidado para aplicaciones en el sector de la automoción, la construcción de máquinas especiales o la tecnología de equipos. Los componentes de PA6GF30 son muy adecuados para aplicaciones de sustitución de piezas metálicas o de aluminio siempre que las temperaturas de funcionamiento lo permitan (PA6GF30: 130°C en uso continuo, 150 °C en periodos cortos). En cuanto a las propiedades mecánicas, como la resistencia a la tracción, se obtuvieron valores muy elevados mediante la impresión 3D en los sistemas AIM3D ExAM 255 y ExAM 510 (véase el gráfico 1). En comparación con los procesos de lecho de polvo o los procesos de impresión 3D que utilizan materiales de filamento, los sistemas de proceso CEM logran resistencias a la tracción que se acercan a los procesos clásicos de moldeo por inyección de termoplásticos.
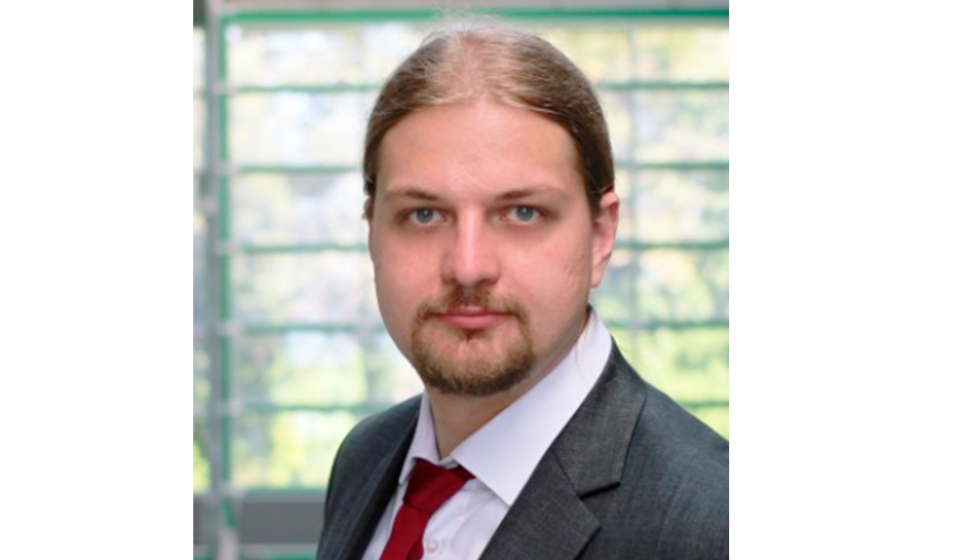
Vincent Morrison, director general de AIM3D: “Un precio comparable al del moldeo por inyección para materias primas que no contienen filamentos es una enorme ventaja para nuestra tecnología de sistemas de impresión 3D CEM. Utilizando la PA6GF30, nuestra máquina ExAM 255 es capaz de producir tanto piezas complejas y delicadas con una fina resolución de impresión, como grandes componentes estructurales con mayores espesores de capa, lo que se traduce en una máxima rentabilidad con la impresión 3D más avanzada". Foto: AIM3D GmbH, Rostock (Alemania).
Pruebas y análisis de materiales en detalle
En primer lugar, se imprimieron barras de tracción en una máquina ExAM 255 con PA6GF30 y en la máquina más grande ExAM 510 (que se presentará en Formnext 2022) (véase el gráfico 1). También se varió la orientación de las bandas impresas en 3D. 0° para una colocación en línea con la dirección de tracción (la orientación de las fibras también estaba en la dirección de tracción) y +/- 45° para un patrón con una dirección alternativa de +/- 45° a la dirección de tracción. La empresa de Rostock comparó esto, por un lado, con los valores de la hoja de datos para el moldeo por inyección con el material original y, por otro lado, con el uso de filamentos de PA6GF30 comparables. Además, se realizó una comparación con un material PA12 utilizado para la impresión 3D en lecho de polvo, ya que este material se utiliza a menudo como referencia en la impresión 3D. El gráfico 1 muestra que la tecnología CEM está muy cerca del moldeo por inyección, pero tiene una ventaja significativa sobre los filamentos.
Este fenómeno se debe, entre otras cosas, a que los gránulos originales utilizados de la tecnología de moldeo por inyección de BASF contienen en realidad fibras de vidrio de hasta 3 mm de longitud, que pueden soportar las fuerzas de tracción durante más tiempo. En comparación, la longitud de las fibras en los filamentos es significativamente menor por razones tecnológicas. En general, se distingue entre reforzado con fibra (GF) y relleno de fibra (si sólo se utilizan fibras cortas). Si también se tienen en cuenta otras características de la ficha técnica del material Ultramid B3WG6 de BASF utilizado en la prueba, queda claro que la combinación de una alta resistencia al imprimir en 3D y la elevada temperatura de funcionamiento continuo de 130°C a 150°C significa que se trata de un material de aplicación universal.
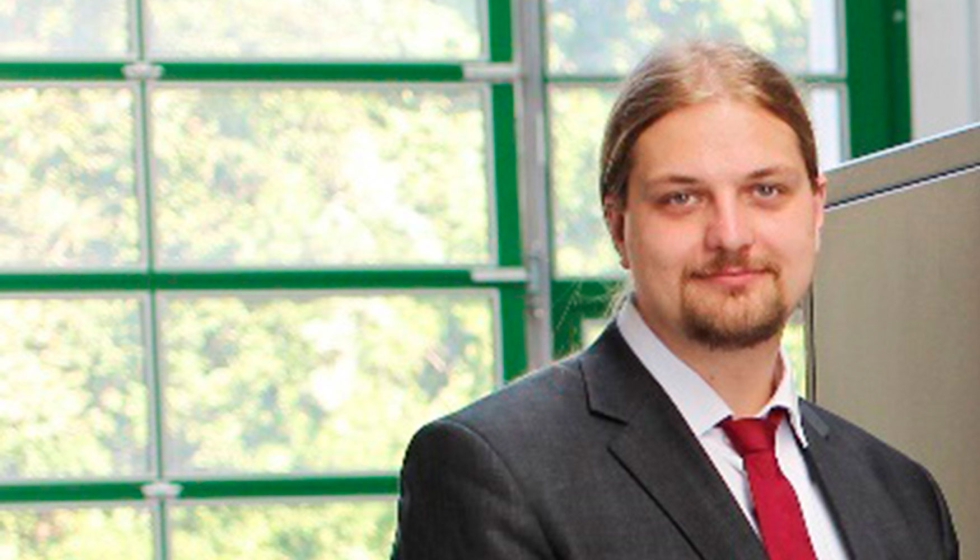
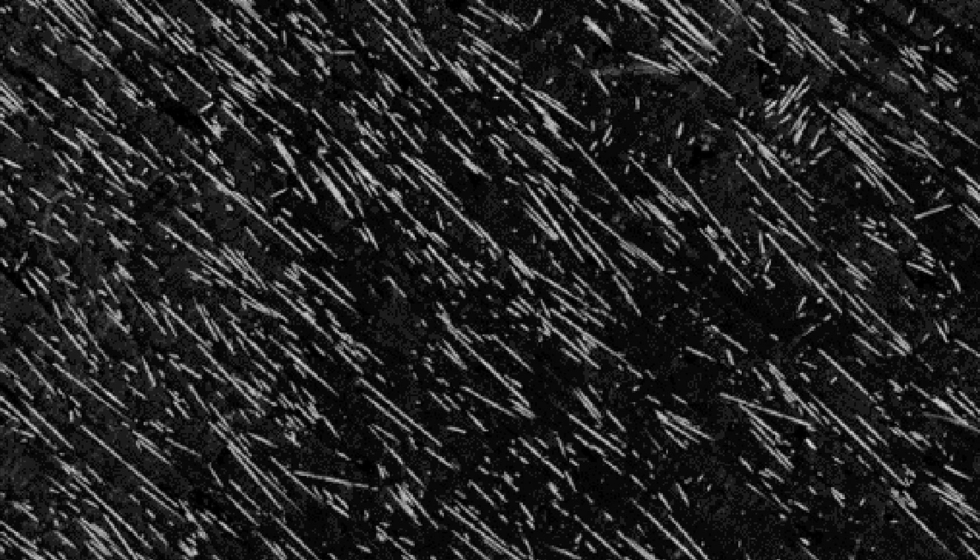
Ventajas de coste obtenidas gracias a la integración funcional en la impresión 3D
En comparación con los componentes fabricados de forma convencional, el atractivo especial de la impresión 3D reside en la denominada integración funcional mediante enfoques de diseño compatibles con la impresión 3D. La integración funcional significa que los conjuntos pueden fabricarse en un solo proceso de impresión, lo que constituye una de las ventajas estratégicas de la impresión 3D. AIM3D fabricó una carcasa de extrusora equipada con un soporte de motor fabricado en PA6GF30 como demostración del proceso. El soporte del motor, dos conductos de aire colocados en las paredes, una salida de ventilación y un soporte para los sensores se integraron en la carcasa como un único componente.
En el caso de una estrategia de producción convencional con piezas de aluminio fresadas, se habrían tenido que fresar de 3 a 4 piezas a partir de un bloque, lo que supondría un desperdicio de materias primas. Además, durante la fase de diseño habría que dedicar tiempo a idear una solución para evitar el uso de herramientas especiales, como taladros de ranura, etc., y a realizar una conexión adecuada de los componentes. También se elimina el tiempo dedicado a escribir programas de fresado CAM, especialmente para la producción de lotes pequeños. El trabajo de montaje manual se reduce significativamente, lo que también tiene un efecto positivo en el cálculo del coste de las piezas.
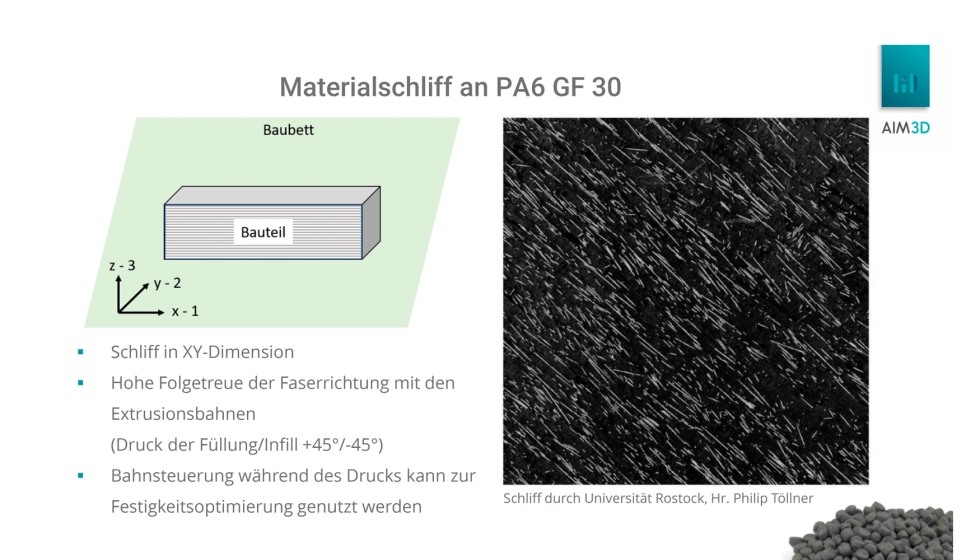
El proceso CEM: eficiencia de costes convincente
En palabras de Vincent Morrison, director general de AIM3D: “Un precio comparable al del moldeo por inyección para materias primas que no contienen filamentos es una enorme ventaja para nuestra tecnología de sistemas de impresión 3D CEM. Utilizando PA6GF30, nuestra máquina ExAM 255 es capaz de producir tanto piezas complejas y delicadas con una resolución de impresión fina, como componentes estructurales de gran tamaño con mayores espesores de capa, lo que se traduce en una máxima rentabilidad con la impresión 3D más avanzada”.
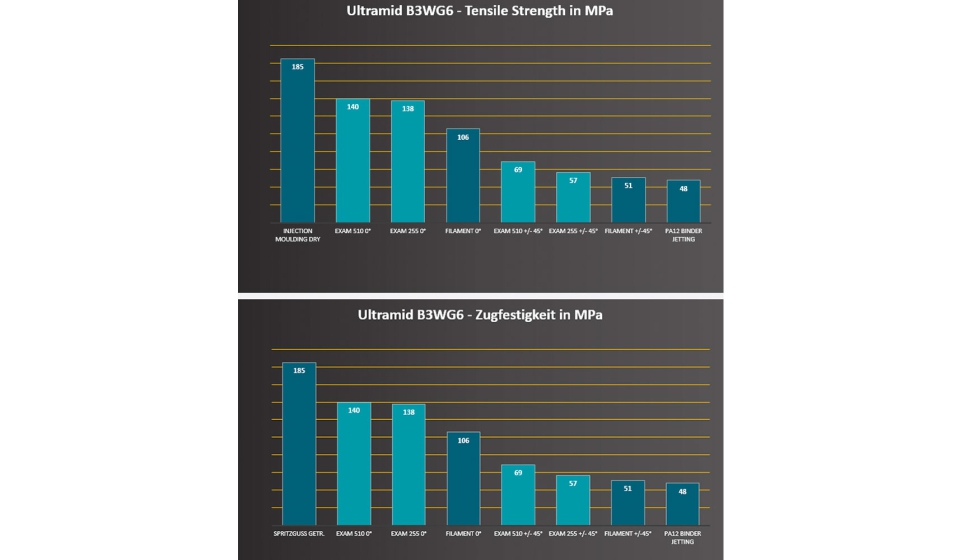
Comparación de las resistencias a la tracción con PA6GF30 en función de diferentes estrategias de fabricación. Foto: AIM3D GmbH, Rostock (Alemania).
Sustitución del Al en la impresión 3D
Sobre todo, la sustitución del proceso de CEM por soluciones de producción de aluminio fresado tiene un gran potencial, como explica Vincent Morrison: “El aluminio como material es comparativamente caro debido a que su producción requiere mucha energía. ”Las piezas de aluminio se suelen fresar a partir de un bloque sólido. Esto ejerce una gran presión sobre los precios. A ello se suma la actual escasez de materias primas. El material PA6GF30 impreso con nuestra tecnología CEM como solución de producción alternativa crea dimensiones completamente nuevas en términos de eficiencia de costes. Esto se aplica aún más cuando entran en juego los enfoques de diseño biónico para aumentar el rendimiento de los componentes".
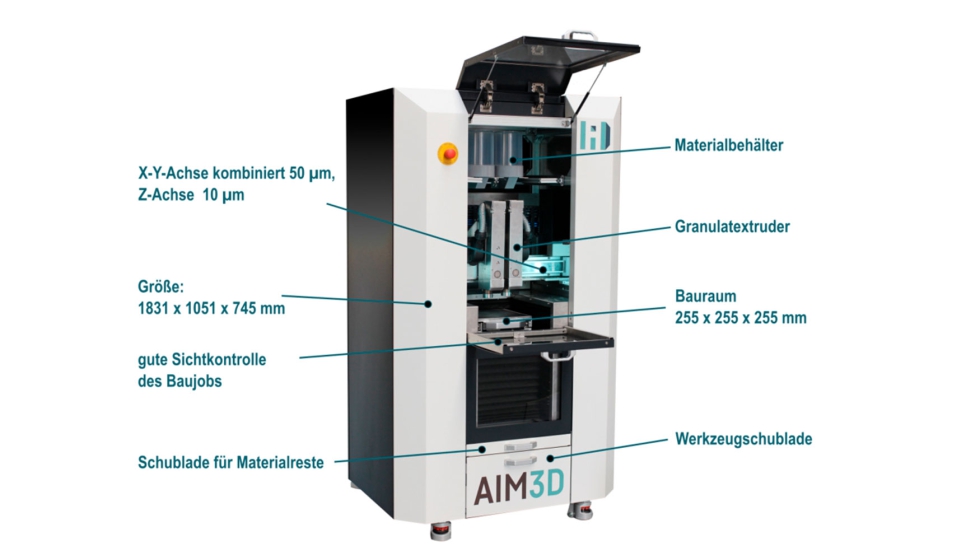
XAM 255 (impresora 3D CEM) de AIM3D con detalles técnicos. Foto: AIM3D GmbH, Rostock (Alemania).
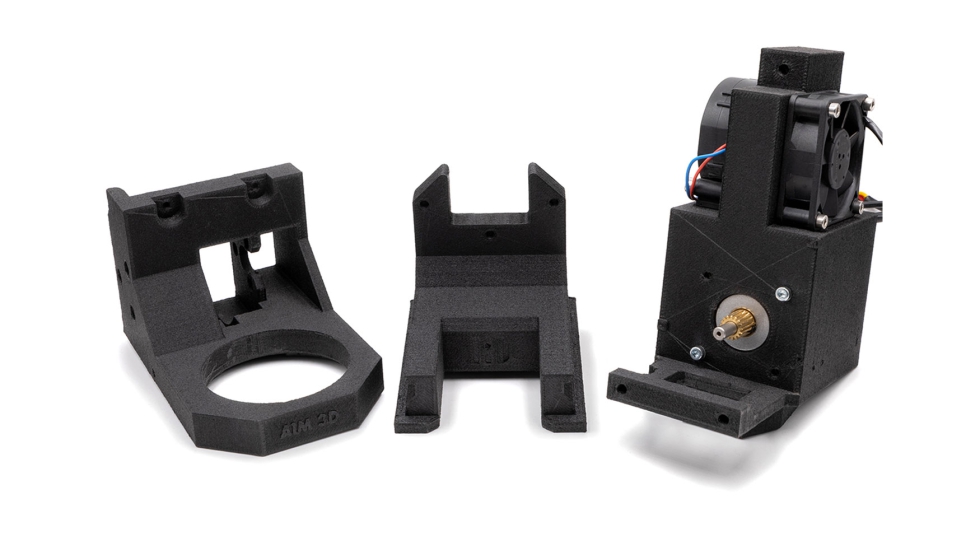