Anclaje del revestimiento de hormigón proyectado en la rehabilitación de un túnel
Msc.-Ing. Frank von Havranek † | Friedr. Ischebeck GmbH
Ischebeck Iberica, S.L.
Pol. Industrial 'El Oliveral
Calle S, No.25
46394 Ribarroja del Turia / Valencia
18/09/2023El túnel ferroviario de Effolderbach se construyó en 1870. Sin embargo, poco después de su puesta en funcionamiento, parte de la bóveda tuvo que ser reforzada. En rehabilitaciones posteriores se han instalado arcos de celosía con nervios de hormigón proyectado en algunas secciones y el revestimiento de arenisca se remplazó localmente por mampostería.
En la década de los 50 se observó un descenso del nivel de la clave de hasta 0,35 m como consecuencia del desprendimiento de zonas rocosas. En algunas zonas, la entrada de agua y las heladas erosionaron severamente el espesor de la bóveda de arenisca, que originalmente era de 0,25 a 0,50 m de espesor, lo que redujo significativamente su capacidad de carga. Por este motivo, en 2009 se realizó una estabilización con hormigón proyectado anclado.
Tras evaluar varias soluciones y realizar análisis económicos, DB Netz AG optó por renovar la estructura existente inmediatamente e instalar un revestimiento anclado permanente. La elección de un sistema de anclaje apropiado es una tarea compleja. En el proceso de selección del método constructivo óptimo, es necesario tener en cuenta el gran número de normas constructivas, desde la introducción de los estándares europeos, las regulaciones específicas de ferrocarriles (algunas de las cuales tienen versiones actualizadas para cumplir con los estándares europeos) y en el caso de Alemania, el estado de las aprobaciones de productos.
Este artículo utiliza un caso específico para exponer los puntos que pueden ser determinantes en la elección de un sistema de anclaje permanente.
1.- Alcance de los trabajos
El túnel ferroviario Effolderbach es un túnel de doble vía y de 673 m de longitud ubicado en la vía ferroviaria 3701 Gießen – Gelnhausen a 40 km hacia el noreste de Fráncfort del Meno. La mampostería de la bóveda, de más de 140 años de antigüedad, se reforzó con un revestimiento de hormigón proyectado.
Para cumplir con el contorno de referencia prescrito para el tráfico ferroviario según la directriz 853 de DB Netz AG [1], la nueva cáscara de hormigón proyectado tuvo que fabricarse con un espesor limitado (Fig. 1). No obstante, para garantizar una capacidad de carga suficiente, fue necesario su anclaje permanente en la roca con elementos portantes de acero. El término permanente, se define en la norma DIN EN 1990, tabla 2.1 en la clase de vida útil 5 para estructuras de ingeniería civil, con una vida útil de diseño de 100 años [2].
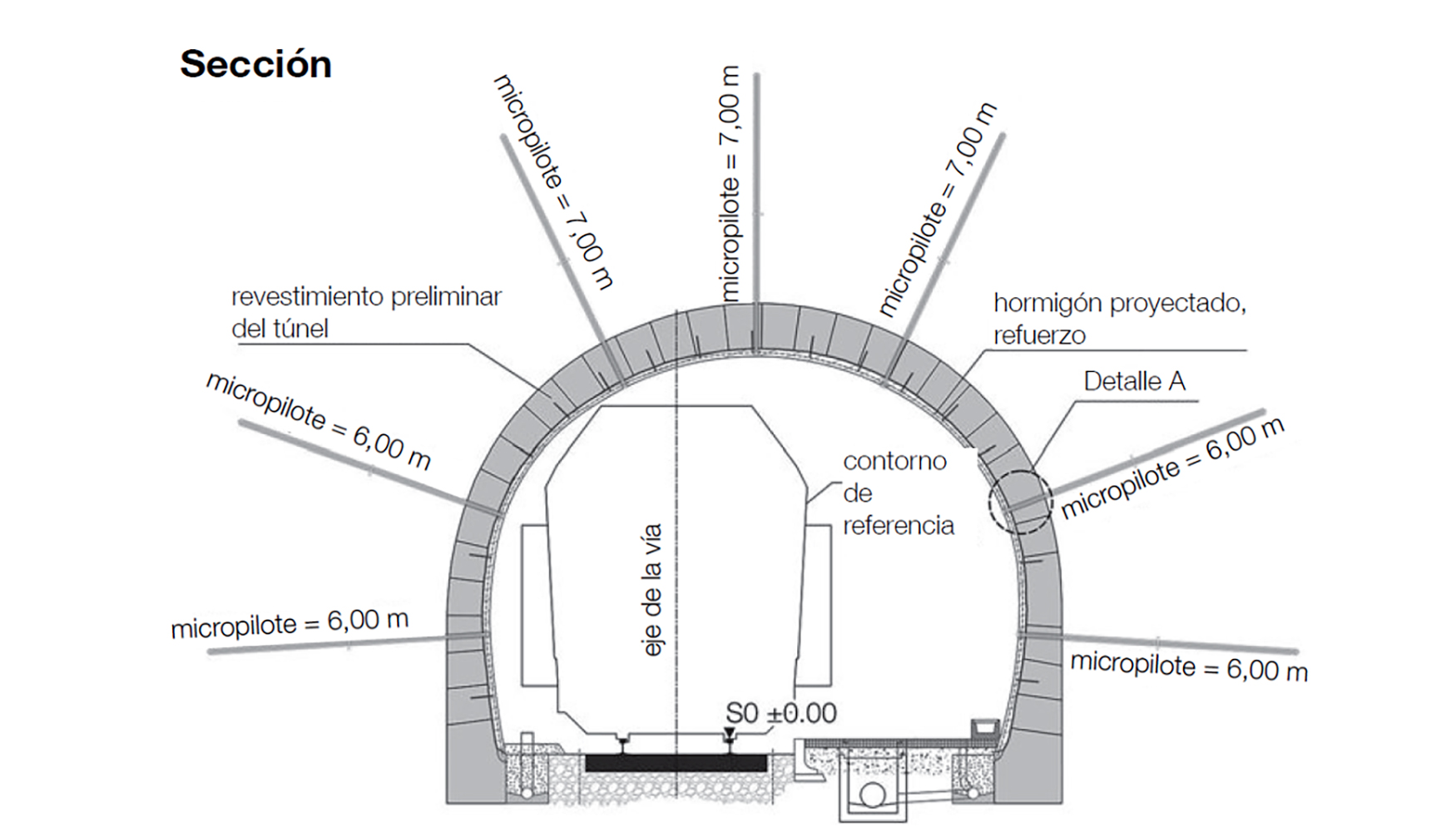
La vida útil restante del túnel tras su acondicionamiento será menor a 100 años, sin embargo, los sistemas de anclajes solo pueden clasificarse según las normativas como permanentes o temporales, siendo este último como máximo de dos años [3], [4]. Esto hizo que sólo se pudieran utilizar sistemas con la aprobación del Instituto Alemán de Tecnología de la construcción ‘Deutsche Institut für Bautechnik’ (DIBt) para uso permanente. Otro punto importante para el cliente, era que el sistema una vez instalado no requiera mantenimiento. Partiendo de estos requisitos se estudiaron posibles alternativas.
2. Selección del sistema de anclaje
Los anclajes permanentes tradicionales según la norma DIN EN 1537, como los anclajes de cable o anclajes de barra se descartaron, ya que se caracterizan por la longitud de anclaje libre y el pretensado [5]. El uso de este tipo de anclajes habría supuesto esfuerzos adicionales de pretensado en la bóveda del túnel (que ya no era estable) del orden del 80 a 100% de la fuerza de los anclajes. El pretensado de los anclajes trabaja con toda su carga independientemente de la carga real en la estructura. Estos esfuerzos adicionales podrían provocar nuevos daños en la estructura existente. Por otro lado, el pretensado debe inspeccionarse regularmente por el operador del túnel, para lo cual es necesario tener acceso al cabezal de anclaje y una adecuada protección contra la corrosión del mismo. Al mismo tiempo, el control periódico del pretensado durante toda la vida útil del túnel y los eventuales retesados necesarios, y cierres de línea asociados, supondría unos costes de mantenimiento significativos. Debido a esto, la directriz 836 establece que la utilización de anclajes de la norma DIN EN 1537 [6] debe ser aprobada por el organismo responsable de DB Netz AG.
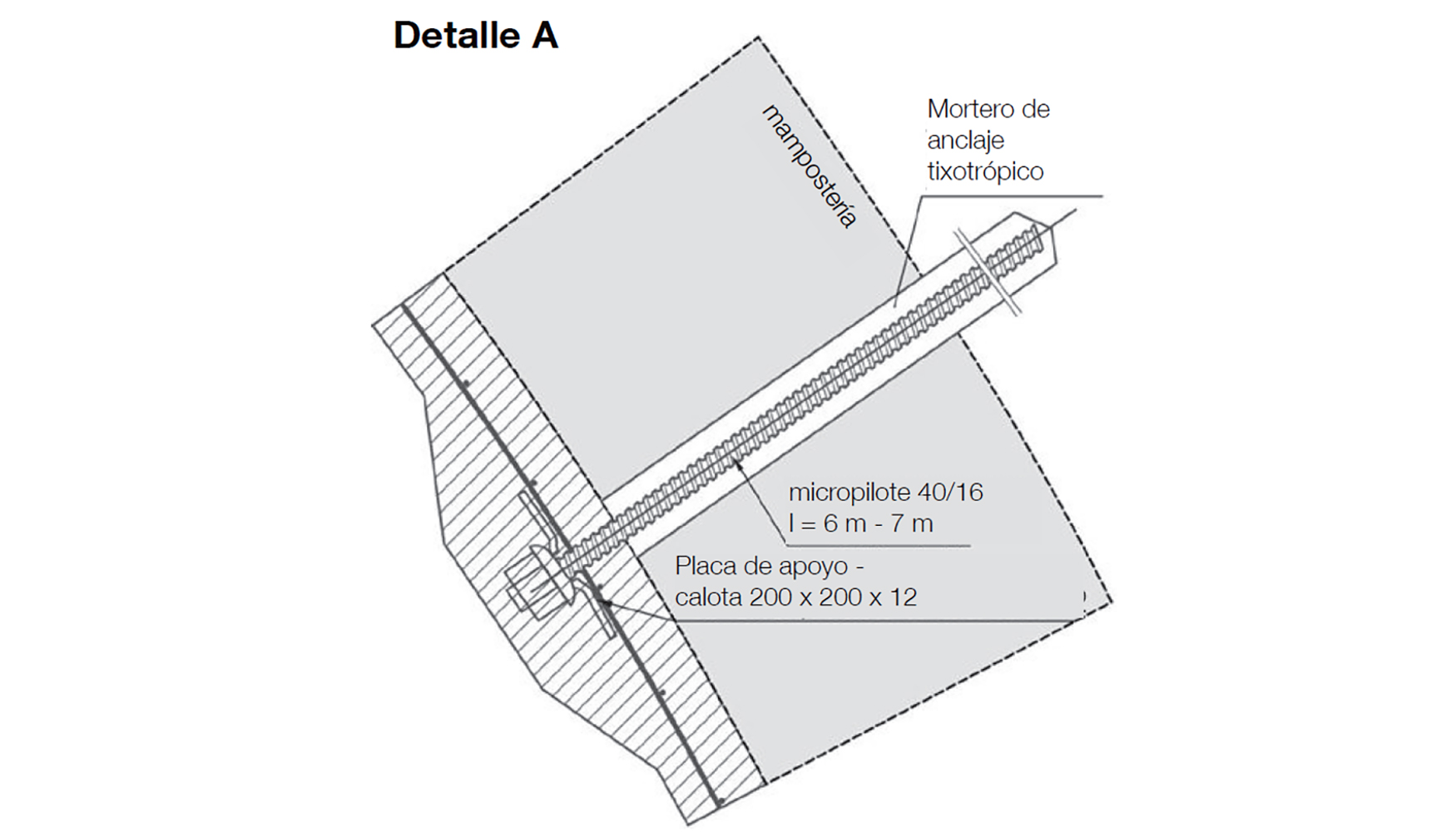
Por lo tanto, desde un primer momento, la atención se centró en sistemas pasivos, dentro de estos fundamentalmente los micropilotes sometidos a tracción según la norma DIN EN 14199 [7]. Las ventajas de estos sistemas son que las cabezas de los micropilotes quedan completamente embebidas en el hormigón proyectado brindando una protección 100% frente a la corrosión y, por tanto, no requieren mantenimiento, y que los elementos portantes están recubiertos de mortero de cemento en toda su longitud (Figs. 2 y 3).
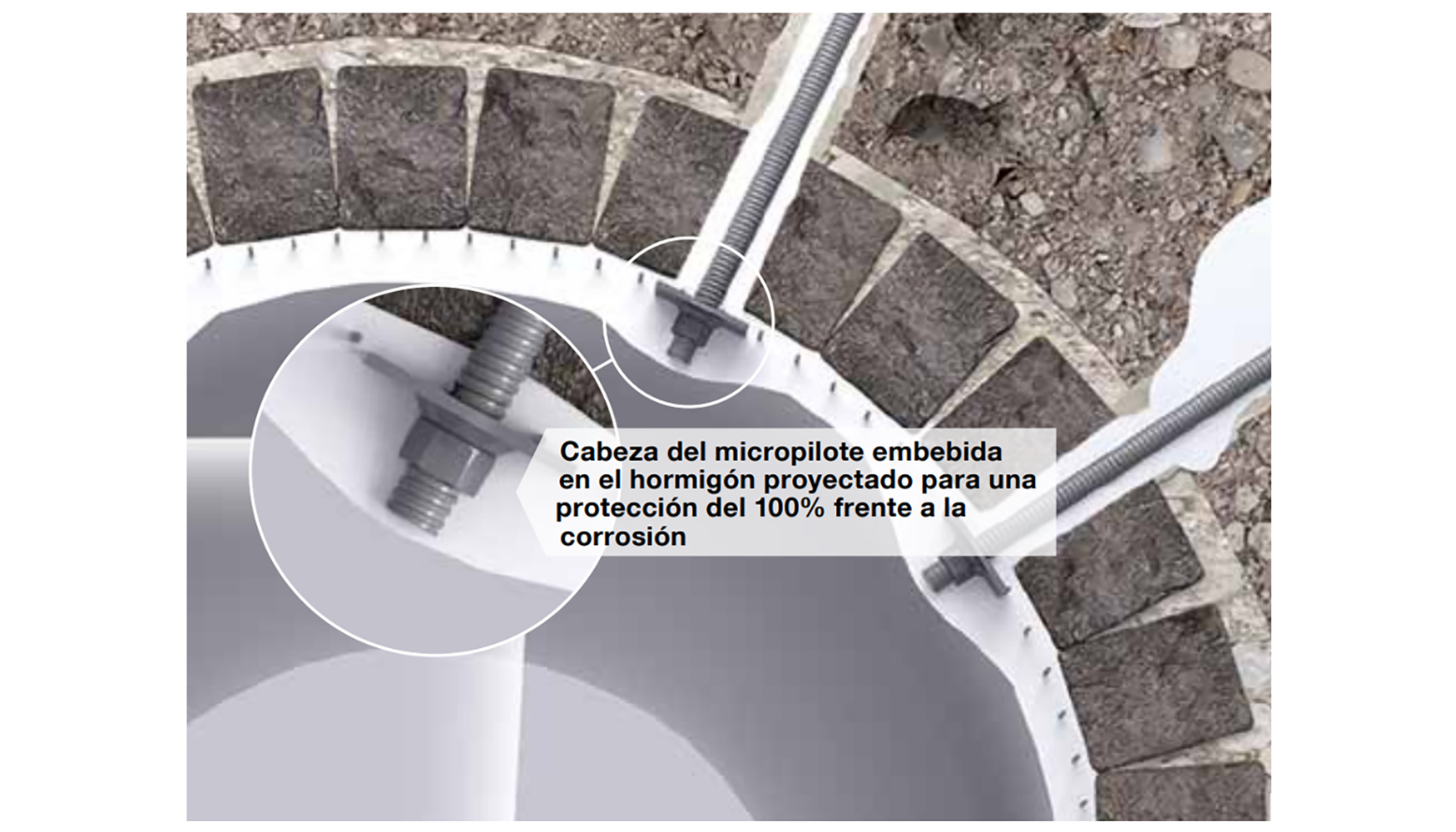
Al igual que en los anclajes activos, la carga sobre los elementos portantes es de tracción axial, con la diferencia de que la carga se adapta gradual y continuamente en función de los asentamientos milimétricos reales que se producen. Esta capacidad de los sistemas pasivos de poder adaptarse a la carga, es una ventaja que en la práctica muchas veces se pasa por alto.
Se estudiaron dos sistemas de micropilotes. En primer lugar, el micropilote armado con barra maciza nervada [8], homologado por las autoridades de la construcción alemana, y en segundo lugar, el micropilote TITAN de Friedr. Ischebeck GmbH, homologado por las autoridades de la construcción por primera vez en 2003 [9], único sistema autoperforante para aplicaciones permanentes.
A partir de las perforaciones exploratorias, detrás de la mampostería de apoyo se observó roca fuertemente meteorizada, en parte inestable y con grandes fisuras. Al igual que en los anclajes de cables y de barras macizas, los micropilotes de barras macizas convencionales ejecutados en roca no consolidada o en perforaciones inestables deben emplearse tuberías de revestimiento de la perforación (camisa) [4]. Sin embargo, su instalación es compleja; los mayores diámetros de perforación hacen necesarios equipos de perforación más pesados [10] y puede ser difícil de controlar cuando se perfora en la zona de la bóveda.
Para poder utilizar barra maciza nervada en obras permanentes, las barras deben tener un revestimiento de plástico corrugado para su protección para la corrosión y en los puntos de unión entre barras se debe colocar una protección adecuada con tubos termo retráctiles, cuya instalación requiere tiempo adicional. Tras la inyección, se extraen las camisas y se rellena con lechada el espacio anular resultante [11].
El empleo de este tipo de micropilotes es poco frecuente en túneles. Además, la obra disponía de unas ventanas de trabajo muy ajustadas condicionadas por las paradas nocturnas. Por las razones anteriores, no fue viable utilizar micropilotes a tracción de barra maciza.
3. Anclaje con micropilotes autoperforantes TITAN
La experiencia previa positiva en el empleo del sistema de micropilotes con barra autoperforante llevó a optar por este sistema desde la fase inicial de planificación. Dentro de las ventajas de este sistema, en rocas inestables destaca que el elemento portante de acero es también varillaje de perforación. Esto evita los posibles bloqueos debidos al colapso de las perforaciones o las desviaciones axiales al insertar elementos portantes de acero convencionales a través de fracturas [11], [12].
El micropilote TITAN se ejecuta como un pilote de tracción con boca de perforación perdida, con longitudes de barras suministradas habituales de 3 m, utilizando un equipo de perforación provisto de un martillo de cabeza, disponible normalmente en la construcción de túneles (Fig. 4).
El único elemento adicional necesario es un cabezal de lavado o inyección (Fig. 5), pudiéndose realizar la inyección dinámica durante la perforación (Figs. 6 y 7). No son necesarias tuberías de revestimiento de la perforación, ya que la perforación se puede estabilizar con lechada de cemento simultánea a la perforación (Fig. 7) [12], lo cual facilita significativamente el trabajo de los operarios en obra.
La instalación se pudo realizar de forma ágil mediante un equipo convencional de perforación con dos brazos, cada uno con un martillo en cabeza y cesta, y un sistema de inyección tradicional.
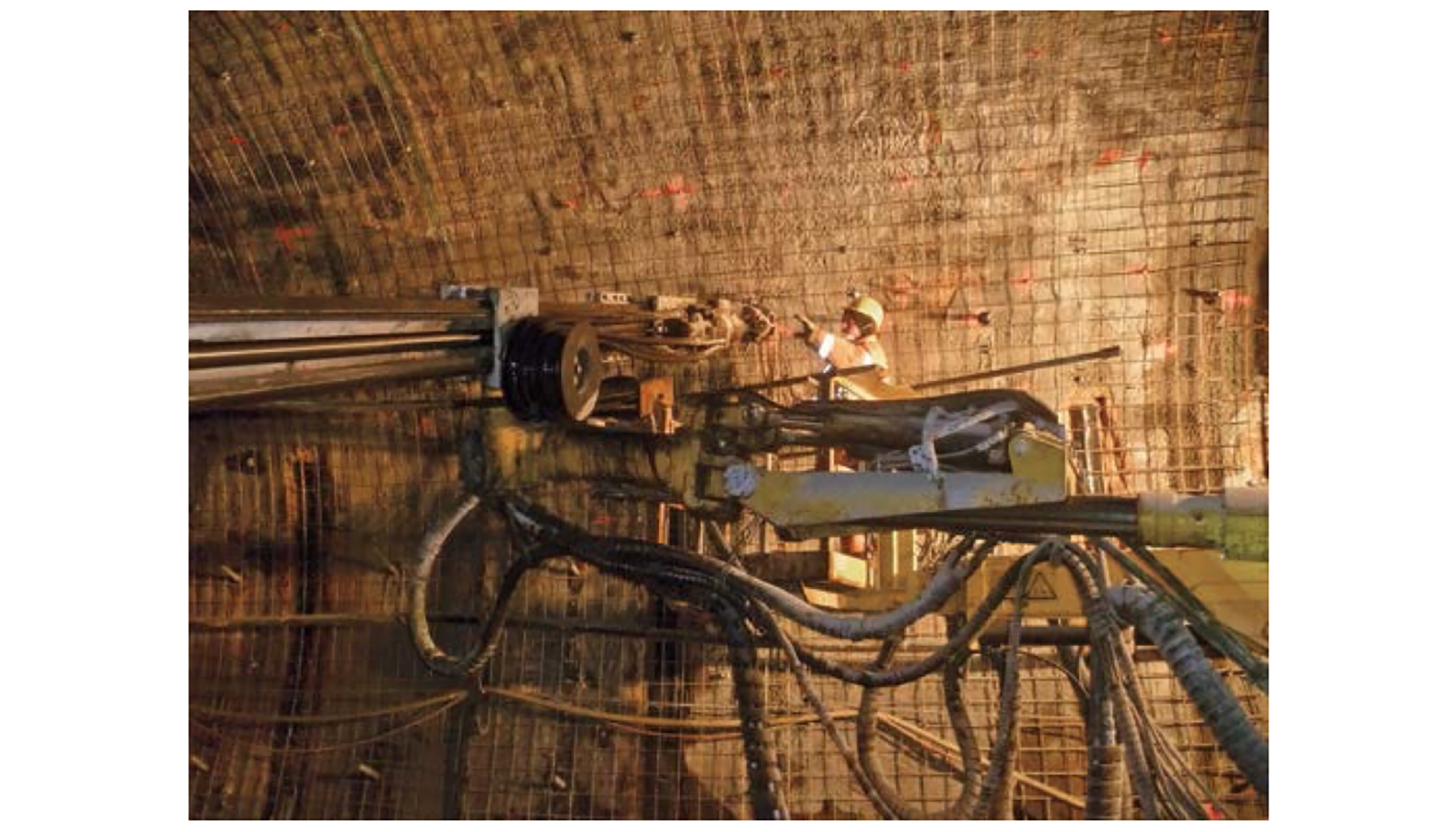
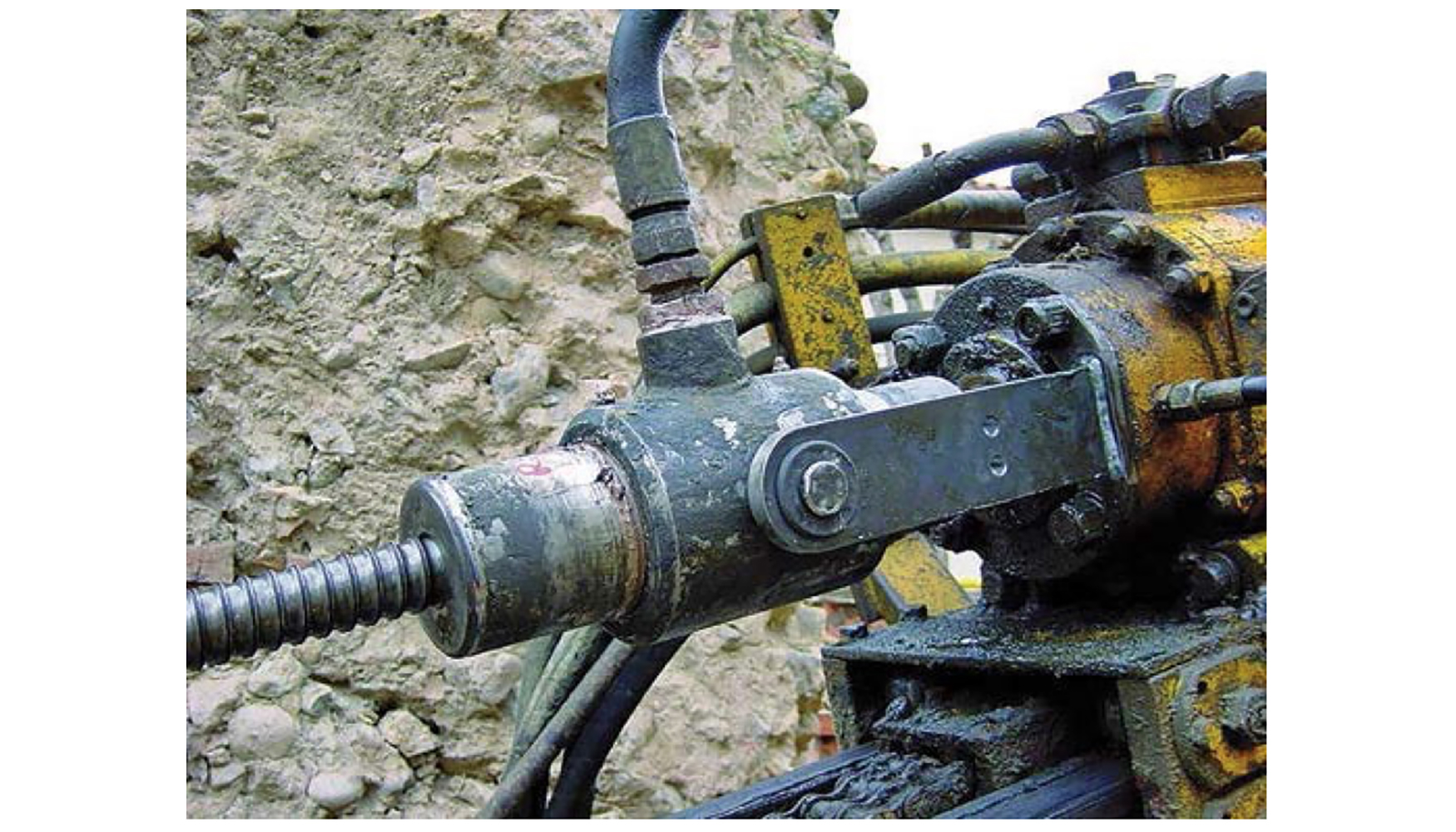
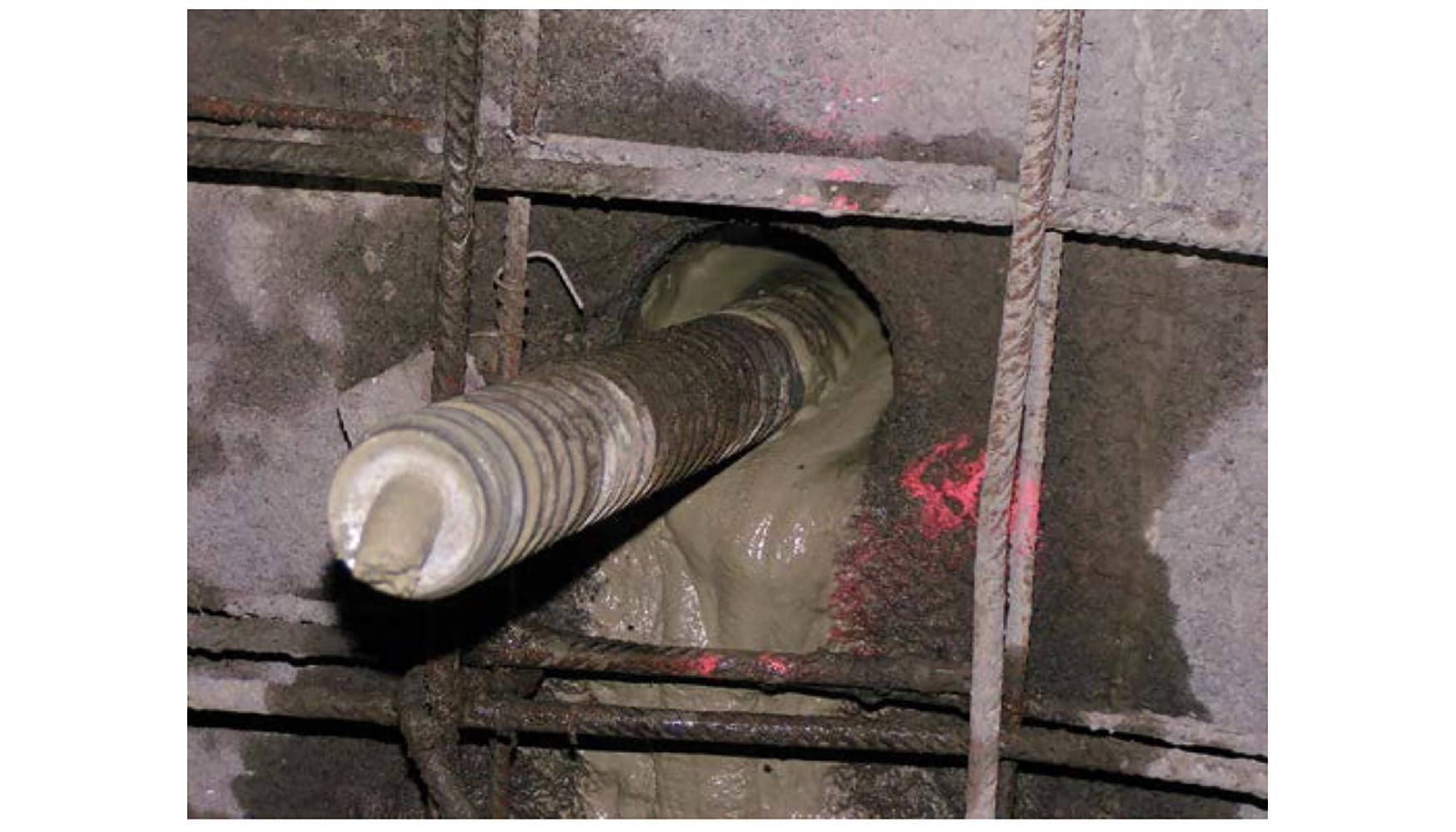
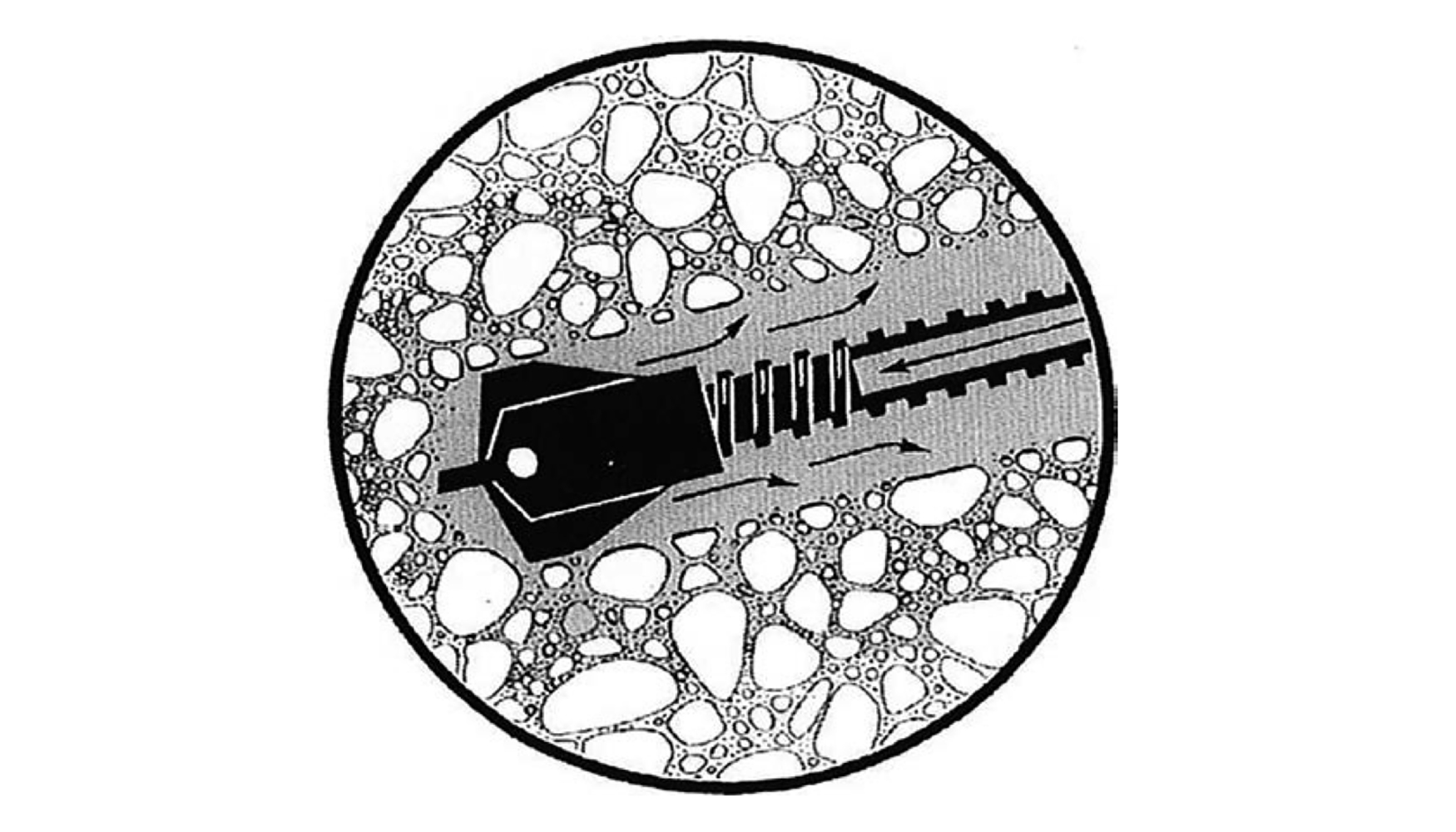
Se definió una fuerza de anclaje característica de 200 kN. Con el objetivo de tener suficiente reserva de carga para situaciones impredecibles que puedan surgir, mayor par de giro y mejor transmisión de la energía de impacto (ventajosa para el avance de perforación al perforar en roca maciza) se optó por el micropilote TITAN 40/16 (ampliamente sobredimensionado).
El sobredimensionamiento de la sección transversal permite garantizar suficiente sección durante toda la vida útil, incluso en el caso de falta de lechada en el cuerpo de inyección debido a fisuras locales [6].
El elemento portante es una barra hueca de acero con diámetro exterior de 40 mm, un diámetro interior de 16 mm y una rosca continua (Fig. 8). La sección efectiva de la barra de acero es de 900 mm2, la resistencia característica de 530 kN y la carga de rotura de 673 kN [13].
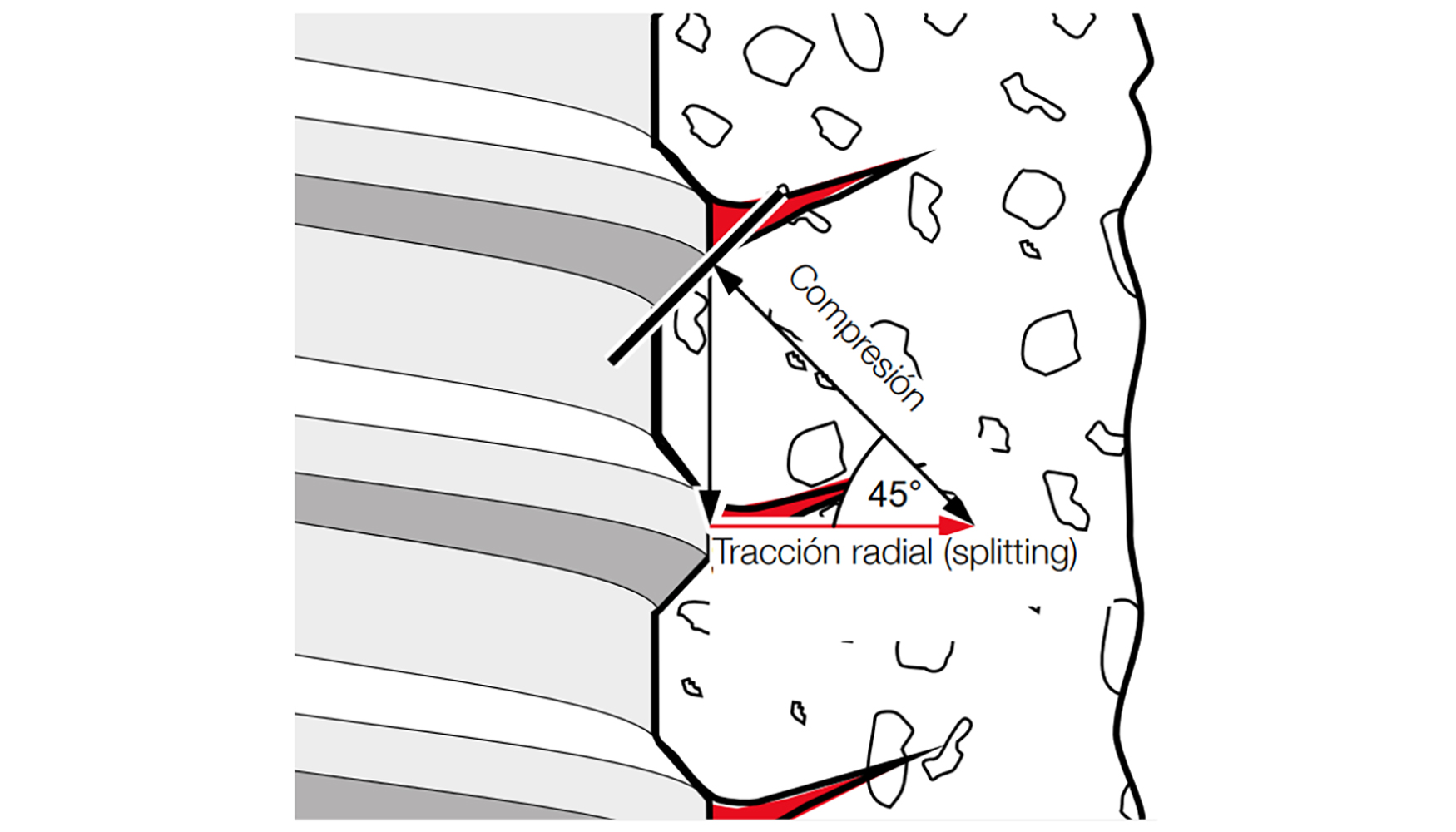
La capacidad de los micropilotes a tracción fue ensayada in situ con una carga de 360kN. Para garantizar resultados genuinos en los ensayos, se desconectó el elemento portante de acero de la mampostería de revestimiento existente en el túnel y del relleno del túnel, mediante la colocación de tubos de revestimiento plástico en los pilotes a ensayar.
Para la conexión en cabeza en el hormigón proyectado se utiliza una placa de calota de 200x200x12 mm con una tuerca semiesférica (Fig 2). Esto fue posible gracias a la capacidad obtenida en el ensayo a punzonamiento del hormigón proyectado.
4. Normativa aplicable
Antes del inicio de la actuación, el contratista planteó alternativas con elementos portantes de acero R38-500 y H0500-38, ambos con perfiles huecos R38 de acero templado y revenido 28Mn6 y con rosca según ISO 10208 (Fig. 9). Estas soluciones no se aceptaron por aspectos formales, legislativos y técnicos que se detallan a continuación.
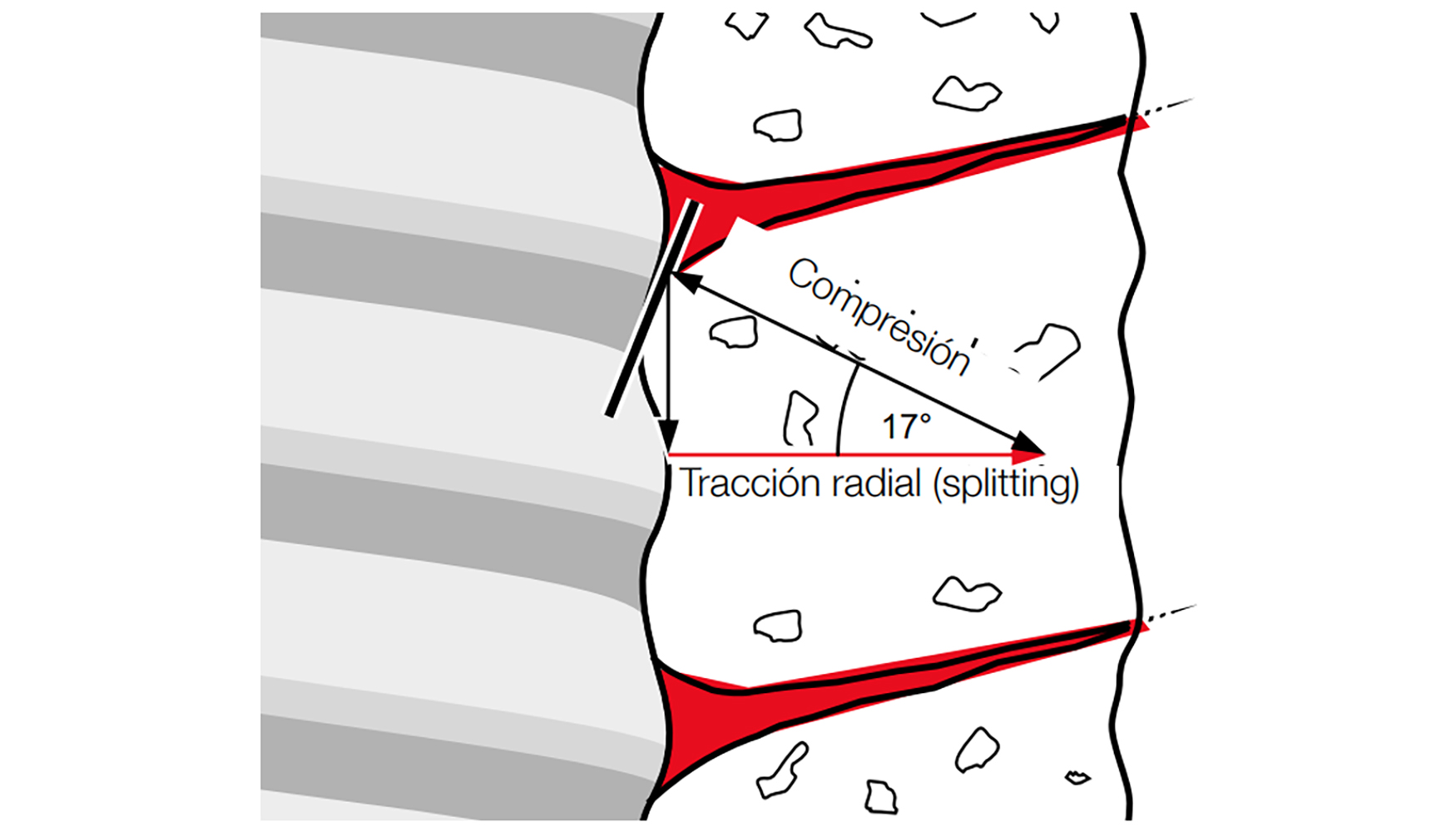
Desde el punto de vista legislativo, en Alemania se debe cumplir la norma DIN EN 14199 junto a la normativa suplementaria DIN SPEC 18539, las cuales se aplican también en el ámbito de los ferrocarriles [14].
De acuerdo a esta normativa, los pilotes armados están sujetos a la utilización de sistemas debidamente aprobados por el Instituto alemán de tecnología de la construcción (DIBt) [4]. Los elementos portantes de los pilotes deben cumplir por tanto los requisitos de la normativa europea y las normas técnicas de la construcción alemanas. Estas últimas, desarrolladas en base a décadas de investigación y corroboradas infinidad de veces por su uso en la construcción, son las más restrictivas.
Además, en el ámbito ferroviario solo se pueden utilizar sistemas que cumplen con las normativas listadas en la ‘Lista de normas técnicas específicas para la construcción de ferrocarriles’ (ELTB). En consecuencia, en Alemania los elementos portantes sin una aprobación técnica general de la DIBT solo se pueden utilizar de forma temporal (menos de dos años) [14].
5. Adherencia y ductilidad del acero para armadura
Desde un punto de vista técnico, los elementos portantes de acero tienen la función de armadura del micropilote [4] y por lo tanto pertenecen al ámbito de los elementos compuestos. El efecto portante en los micropilotes se desarrolla como combinación del elemento portante y cuerpo de inyección (bulbo).
Por este motivo, los aceros utilizados deben cumplir con los requisitos de aceros para armadura, tener suficiente ductilidad y en el comportamiento compuesto limitar el ancho de fisuración [15].
5.1. Geometría de la rosca y calidad del acero
La geometría de la rosca determina en gran medida la eficacia en la transmisión de cargas entre la barra de acero y la lechada de cemento. En primer lugar, el ángulo del flanco de los nervios de la rosca desempeña un papel muy importante. Por ejemplo, las roscas de las barras de perforación, con su inclinación de flanco muy plana de sólo 17°, generan fuerzas de expansión considerablemente mayores y, por tanto, fuerzas de tracción de radial, que las roscas de acero de armadura con una inclinación de flanco de 45°. Este efecto se muestra en las figuras 8 y 9, donde esfuerzos axiales de la misma magnitud, generan fuerzas de tracción radial muy diferentes debido a los distintos ángulos de inclinación de la biela de compresión situada perpendicularmente al flanco de la rosca.
En segundo lugar, solo algunas calidades de acero cumplen con los requisitos de ductilidad para ser utilizados como materiales compuestos. La ductilidad es la propiedad del material de deformarse plásticamente más allá de su límite elástico bajo carga y, por tanto, de no fallar sin previo aviso. Esto es un aspecto de seguridad fundamental en el ámbito de la construcción.
Un parámetro determinante de la ductilidad es el alargamiento alcanzado bajo carga máxima. Por ello, la norma DIN EN 14199 regula que los elementos portantes de los micropilotes deben cumplir la norma de acero para el armado de hormigón DIN EN 10080 (en Alemania DIN 488).
Adicionalmente, se deben verificar los requisitos del Eurocódigo 2: DIN EN 1992-1-1. Además, las barras huecas utilizadas como elementos portantes para micropilotes autoperforantes deben cumplir las normas DIN EN 10210 o DIN EN 10219.
5.2. Requisitos para el acero de armadura según la norma
Los requisitos fundamentales para el hormigón y el acero de armadura, que se especifican detalladamente en las normas mencionadas anteriormente DIN EN 10080, DIN 488 y Eurocódigo 2 (EN 1992-1-1), son (Fig. 10 y 11):
- Límite elástico fy, k. Re = 400 - 600 {500}N/mm2,
- Relación de resistencias ft/fy o Rm/Re ≥ 1,08,
- Deformación unitaria característica εuk ≥ 5,0 % (Agt ≠ deformación en rotura),
- Tensión nominal en fatiga βfyk ≥ 150 {145} N/mm2 para N ≥ 2 {1} × 106 ciclos de carga,
- Ensayo de aptitud al doblado - desdoblado,
- Geometría de la rosca: ángulo del flanco de los nervios de la rosca α ≥ 45° {40º},
- Soldable (la soldadura no suele ser necesaria para los elementos portantes, pero el C < 0,22% determina también otras propiedades importantes del acero).
Los valores indicados entre llaves {…} corresponden a las especificaciones de la DIN 488 y [15] a [18].
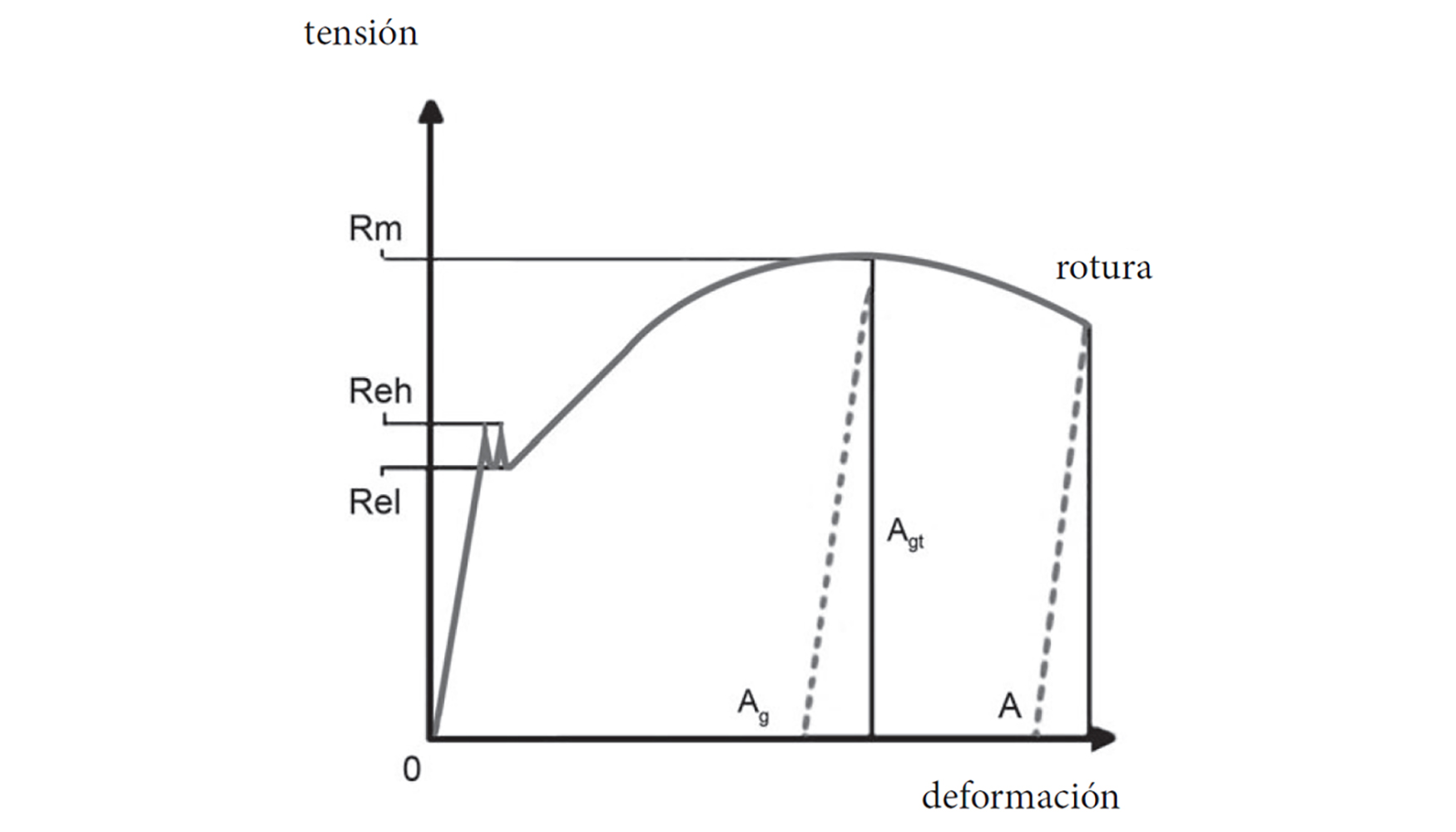

Los perfiles huecos de acero acabados en caliente para construcción y los conformados en frío de acero no aleado y de grano fino están regulados por las normas DIN EN 10210 y DIN EN 10219 respectivamente, donde se especifica la energía mínima de rotura en flexión por choque KV:
- Aceros no aleados KV ≥ 27 J a -20 °C [19], [20],
- Aceros de grano fino KV ≥ 40 J a -20 °C [19], [20].
La resistencia de los aceros de armadura de refuerzo a los esfuerzos dinámicos o de impacto está relacionada con la ductilidad. Por lo tanto, para estos aceros se definen valores mínimos para la energía de rotura en flexión por choque KV.
El resultado del ensayo de péndulo de Charpy (véase la Fig. 12) es la energía de impacto. Este es un criterio esencial para la tenacidad del material de acero y su resistencia a la propagación de grietas o rotura.
En los sistemas autoperforantes, en los que el elemento portante es también el varillaje de perforación, estas propiedades son por tanto de especial interés. La aparición de daños irreversibles en la barra (como deformaciones plásticas o fisuras) durante la instalación puede tener consecuencias fatales.
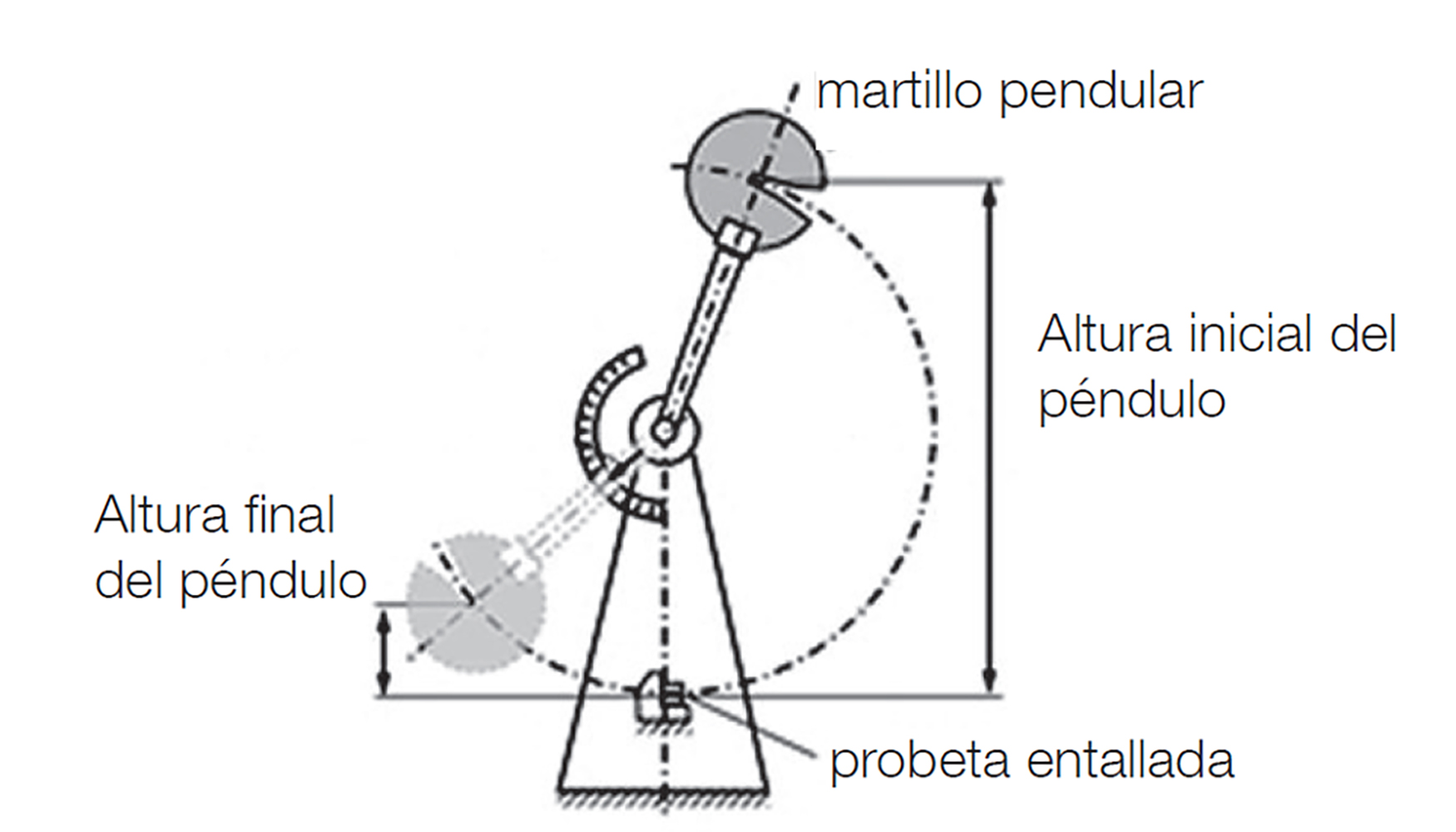
5.3. Elementos portantes de acero para armadura de grano frío
El acero utilizado para las barras portantes TITAN es el acero estructural de grano fino S460NH. Las normas DIN EN 10210 y DIN EN 10219 hacen referencia explícita a este material. Dentro de sus características destacan su gran ductilidad y tenacidad. La materia prima de las barras TITAN es acero laminado en caliente. Las barras TITAN superan el ensayo de aptitud al doblado – desdoblado, al igual que las barras de acero para armaduras convencionales B500 (véase la Fig. 11).
La resistencia al impacto del acero S460N, de hasta W = 100 J a -20 °C, es significativamente mayor que la de los aceros de armadura convencionales de aproximadamente 40 J a -20 °C. Esta característica permite ofrecer reservas suficientes para la deformación en frío o para la elevada carga dinámica a la que se ven sometidas las barras durante la fase de perforación con martillo en cabeza a rotopercusión.
Sobre la base de este material dúctil se fabrica la rosca TITAN con un ángulo de flanco de 45º. La pronunciada inclinación del flanco y la correspondiente área proyectada de corruga fR ≥ 0,14 son características determinantes de la calidad superior del elemento portante. El valor mínimo de área proyectada de corrugas es de fR=0.056 en barras de hormigón armado con diámetro superior a 12 mm [17]. Por tanto las barras TITAN superan en más del doble el valor mínimo de las armaduras convencionales. Esta es una de las razones por las que los anclajes inyectados TITAN alcanzan mayores tensiones de adherencia entre la barra de acero y la lechada de cemento y pueden utilizarse como permanentes sin necesidad de tubo nervado de plástico, es decir, sin doble protección anticorrosión.
La protección frente a la corrosión en los anclajes TITAN queda proporcionada por el recubrimiento de la lechada de cemento del elemento (W0 ≥ -8 según DIN 50929-3, Tabla 7). En función de la sección transversal de la barra y de la carga se definen los espesores mínimos de lechada de cemento necesarios. Gracias a la buena adherencia, las tensiones anulares entre el bulbo y la barra pueden transmitirse sin generar fisuras dañinas o desconchamientos [9]. Adicionalmente, deben cumplirse los espesores mínimos de recubrimiento en función de las clases de exposición [4] aplicándose siempre el criterio más restrictivo.
Por tanto, las barras autoperforantes TITAN cumplen con los requisitos necesarios para poder utilizarse como barras de armadura y con las exigencias de protección contra la corrosión para uso permanente. A su vez, también están homologadas como acero para armadura de micropilotes en aplicaciones permanentes por el instituto alemán de tecnología de la construcción (DIBt) con la homologación número Z-34.14-209.
Conforme a esta homologación su instalación fue prevista por el DB Nets AG para el refuerzo del túnel (Fig. 13).
5.4. Barras de acero que no cumplen con la normativa para su uso como elemento estructural
Es frecuente que los pliegos de licitaciones para anclajes, especialmente en la construcción de túneles, especifiquen aceros de alta resistencia y por tanto que sean suministrados. Cabe destacar que la propiedad ‘alta resistencia’ no está claramente definida y sus posibles valores se han ido elevando conforme al desarrollo de la industria del acero. Antiguamente hacía referencia a aceros estructurales con un límite elástico mínimo ≥ 355 N/mm2, pero actualmente se suele entender como aceros de alta resistencia los que tienen un límite elástico mayor > 600 - 800 N/mm2. La mayor resistencia del acero supone un ahorro como consecuencia de la reducción de la sección transversal requerida, sin embargo conlleva desventajas como el riesgo de corrosión por fisuración. En general, estos aceros están normalizados (laminados en caliente o templados y revenidos). En algunos casos también se combinan los procesos de fabricación.
En el mercado existen barras de aceros puros templados y revenidos, como el 28Mn6. Sin embargo, estos aceros no pertenecen a los aceros estructurales. Los aceros obtienen su temple y revenido del alto contenido de carbono con C = 0,25 - 0,32 % (aceros estructurales de grano fino de alta resistencia C < 0,20 %) y constituyentes de aleación. El carbono es necesario para el proceso de temple y revenido, pero al mismo tiempo reduce el alargamiento de rotura y hace que el acero sea más frágil y susceptible a la fisuración. Como componente de aleación, se añade un 1,5% de manganeso (Mn) al 28Mn6 para aumentar la profundidad de temple, ya que el manganeso reduce la velocidad crítica de enfriamiento, pero tiende a formar granos gruesos. El acero templado y revenido está destinado a piezas sometidas a grandes esfuerzos y resistentes al desgaste en ingeniería mecánica [22], [23].
El temple y revenido propiamente dicho es un tratamiento térmico complejo en el que se alcanzan hasta 850°C, durante el cual se produce una conversión del carbono. Tras el temple y revenido, el 28Mn6 alcanza una energía de rotura en flexión KV = 40 J a +20 °C. Incluso después de este tratamiento térmico, no cumple los requisitos de las normas DIN EN 10210 o DIN EN 10219 (por ejemplo, con respecto a C ≤ 0,22 % y KV ≥ 27 J a -20 °C). Además, estas normas no incluyen los aceros templados y revenidos.
El uso de barras de acero 40Cr templado y revenido importado de Asia resulta aún peor. El componente de aleación cromo aumenta la resistencia a la tracción, la resistencia a altas temperaturas y la resistencia al agua a presión del acero, pero también reduce la velocidad crítica de enfriamiento. Sin embargo, en combinación con el altísimo contenido de carbono (0,40% de media) para aumentar la resistencia y como base para el tratamiento térmico, el acero se vuelve más quebradizo y su deformación en rotura y energía de rotura en flexión disminuyen significativamente [23], [24].
Los aceros templados y revenidos y los aceros resistentes al calor no están destinados principalmente al sector de la construcción. Sus propiedades están optimizadas para otras aplicaciones. Por lo tanto, el uso de estos aceros en la industria de la construcción requiere la correspondiente reglamentación técnica general (por ejemplo, normas) o normas técnicas reconocidas (como homologaciones).
En cambio, para los aceros estructurales normalizados y homologados están disponibles las declaraciones de prestaciones de los productos para la construcción, una disposición central del Reglamento de la UE sobre productos de construcción.
5.5. Barras de perforación (rosca R)
Las barras de perfil redondeado (rosca R) según la norma ISO 10208 son barras de perforación puras. Es decir, están optimizadas para perforar bajo cargas elevadas y en entornos confinados. Están diseñadas para insertar herramientas de perforación en sus extremos y están normalizadas consecuentemente. La rosca R no tiene la geometría para cumplir los requisitos para su uso como armadura ni para proporcionar protección contra la corrosión. El ángulo de flanco de aproximadamente 17° no cumple la norma DIN 488 ni la norma DIN EN 10080. Este tipo de rosca se utiliza habitualmente en aplicaciones temporales en la construcción de túneles debido a la facilidad de conexión con las perforadoras de martillo existentes, aunque no cumple con los requisitos normativos para las barras de armado.
Resulta interesante observar que ni la norma DIN 488 ni la norma DIN EN 10080 distinguen entre aplicaciones temporales y permanentes. Por lo tanto, incluso para aplicaciones a corto plazo, el uso de barras con este tipo de rosca se encuentra en el límite de su idoneidad para su uso. Esto es más destacable aún en el ámbito de la construcción de túneles, donde los aspectos de seguridad son muy valorados.
Para los anclajes inyectados según DIN EN 1537/DIN SPEC 18537, se requiere la aprobación de la longitud de anclaje (longitud de adherencia) del bulbo, incluso para aplicaciones temporales [3]. En el caso de los micropilotes según la norma DIN EN 14199/DIN SPEC 18539, se requiere siempre la homologación de todo el sistema de pilotes [4]. Esto manifiesta la necesidad de utilizar un sistema completo. Se debería evaluar en qué medida la utilización de barras con rosca R en aplicaciones temporales cumple con los requisitos normativos enumerados anteriormente.
6.- Conclusiones
Los trabajos realizados durante la rehabilitación del revestimiento del túnel ferroviario han sido realizados con anclajes autoperforantes TITAN. La utilización de este sistema permitió el cumplimiento de la normativa vigente. La flexibilidad en la tecnología de perforación habitual en la construcción de túneles permitió instalar las barras TITAN en los plazos previstos. El revestimiento de hormigón proyectado fue anclado de forma permanente y segura para el resto de la vida útil del túnel. La inyección dinámica mejora notablemente la estructura del macizo. El relleno de las fisuras encontradas pudo controlarse variando los valores de agua y cemento (relación A/C), la presión de inyección y las cantidades de inyección o el uso de lechada de inyección tixotrópica.
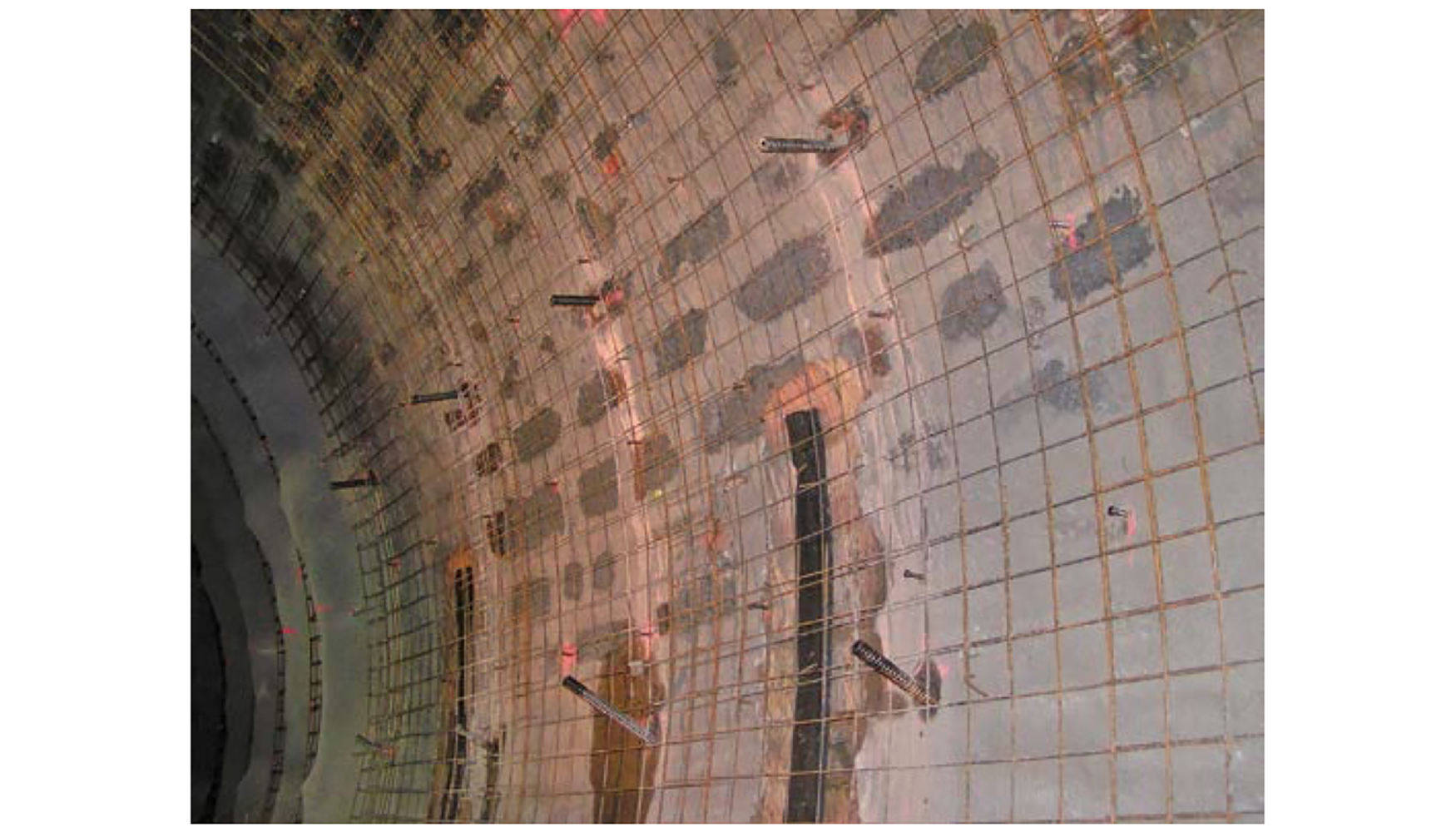
En la actualidad resulta complejo conocer exhaustivamente la normativa relativa a la construcción de todos los estados miembros de la Unión Europea, adicionalmente a las regulaciones tanto nacionales como europeas de productos de construcción.
El objetivo de las normas europeas era lograr una simplificación. Sin embargo, este objetivo se ve mermado por un lado por las disposiciones nacionales complementarias, y por el otro por la posible pérdida de conocimientos, pudiendo un acuerdo de la UE sobre el mínimo denominador común conllevar riesgos. El Instituto alemán de tecnología de la construcción (Deutsches Institut für Bautechnik, DIBt) está realizando una importante contribución en Alemania para evitar estos riegos.
Agradecimientos
El autor agradece a todos los implicados por su apoyo y valiosos consejos que han hecho posible este artículo.
Un agradecimiento especial a DB Netz AG Frankfurt a. M., representada por Carsten Jüngst, a DB International GmbH Frankfurt a. M., representada por Dipl.-Ing. (FH) Thomas Rapp (DB Netz AG), y a la sociedad de geología y metrología de la construcción, Prof. Dr.-Ing. Bernhard Fröhlich.
Bibliografía
- [1] DB Netz AG: Directriz 853 – Diseño, construcción y mantenimiento de túneles ferroviarios. Frankfurt a. M., 2002.
- [2] DIN EN 1990:2010-12 Eurocódigo: Bases de cálculos de estructuras. Versión en alemán. EN 1990:2002+A1:2005+A1: 2005/AC:2010. Berlín: Editorial Beuth, 2010.
- [3] Manual de normas: Manual de trabajos geotécnicos especiales – Volumen 4: Anclajes inyectados. Editorial Beuth, 2013.
- [4] Manual de normas: Manual de trabajos geotécnicos especiales – Volumen 1: Micropilotes. Editorial Beuth, 2013.
- [5] DIN EN 1537:2013, Ejecución de trabajos geotécnicos especiales – Anclajes inyectados. Berlín: Editorial Beuth.
- [6] DB Netz AG: Richtlinie (Ril) 836 – Diseño, construcción y mantenimiento de movimientos de tierras y otras estructuras geotécnicas. Frankfurt a. M., 2008.
- [7] DIN EN 14199:2012-01, Ejecución de trabajos geotécnicos especiales. Micropilotes. Berlín: Editorial Beuth.
- [8] Licencia general para la construcción Z-32.1-2: DYWIDAG GEWI-pilotes (micropilotes) armados con barras de acero corrugado B500B, 20 mm, 28 mm, 32 mm, 40 mm y 50 mm. DYWIDAG Systems International GmbH. Instituto alemán de ingeniería estructural (DIBt), 2013.
- [9] Licencia general para la construcción Z-34.14-209: Micropilotes TI¬TAN. Friedr. Ischebeck GmbH. Instituto alemán de ingeniería estructural (DIBt), 2014.
- [10] Maidl, B., Themes, M., Maidl, U.: Manual de ingeniería de túneles I. Berlin: Wilhelm Ernst & Sohn, 2013.
- [11] Girmscheid, G.: Procesos y métodos constructivos de túneles. Berlin: Wilhelm Ernst & Sohn, 2013.
- [12] Eichler, K.: Construcción en rocas y túneles II. Métodos y parámetros. Tecnología y medio ambiente. Excavación y seguridad. Materiales de construcción y sus propiedades. Renningen: Editorial Expert, 2007.
- [13] Friedr. Ischebeck GmbH: Pilotes inyectados TITAN – La innovación se impone. Diseño, dimensionamiento y ejecución. Friedr. Ischebeck GmbH, 2014.
- [14] Lista de normas técnicas específicas para la construcción de ferrocarriles (ELTB). Bonn: Eisenbahn-Bundesamt, Sección 21, Octubre 2013.
- [15] DIN EN 1992-1-1 Eurocódigo 2: Proyecto de estructuras de hormigón – Parte 1-1: Reglas generales y reglas para edificación; Versión en alemán EN 1992-1-1:2004. Berlín: Editorial Beuth, 2005.
- [16] DIN 488-1:2009-08, Acero para hormigón armado – parte 1 Calidades de acero, propiedades, marcado. Berlín: Editorial Beuth.
- [17] DIN 488-2:2009-08, Acero para hormigón armado – barra de armadura. Berlín: Editorial Beuth.
- [18] DIN EN 10080:2005-08, Acero para el armado del hormigón. Acero soldable para armaduras de hormigón armado. Generalidades. Berlín: Editorial Beuth.
- [19] DIN EN 10210-1:2006-07, Perfiles huecos para construcción, acabados en caliente, de acero no aleado y de grano fino. Parte 1: Condiciones técnicas de suministro. Berlín: Editorial Beuth.
- [20] DIN EN 10219-1:2006-07, Perfiles huecos para construcción soldados, conformados en frío de acero no aleado y de grano fino. Parte 1: Condiciones técnicas de suministro. Berlín: Editorial Beuth.
- [21] Schröter, F.: Aceros de alta resistencia para la construcción metálica. Selección y aplicación. Ingeniería civil 9 (2003), Pag. 426–432.
- [22] Schatt, W., Simmchen, E., Zouhar, G.:Materiales de contrucción para máquinas e instalaciones. Weinheim: John Wiley & Sons 1998, 5ta ed. 2009.
- [23] Padelt, E. et al.: Conocimientos básicos del ingeniero. Editorial Leipzig, 12ma Ed. 1985.
- [24] Rieg, F., Steinhilper, R.: Manual de construcción. München: Editorial Carl Hanser, 2012.