Digitalización, automatización, fabricación aditiva y electromovilidad, el futuro de la producción
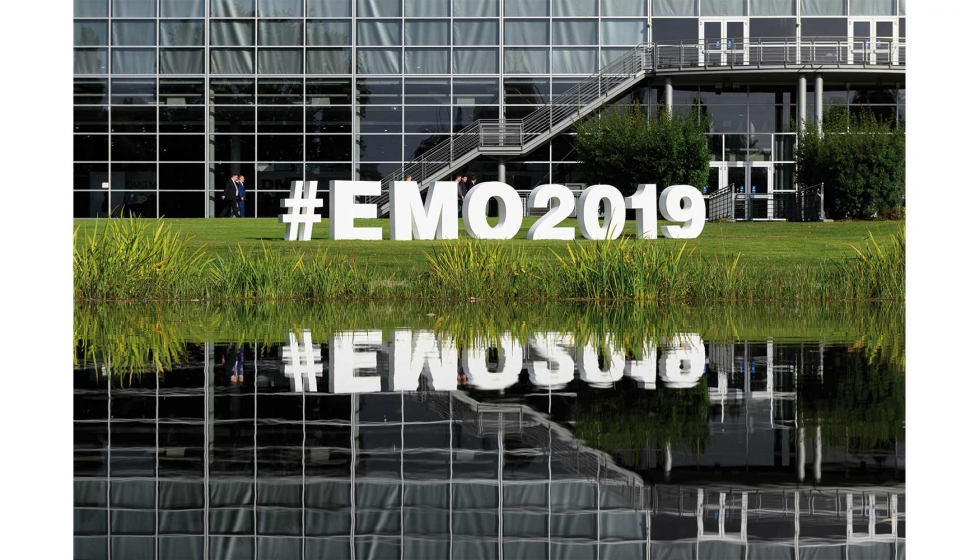
En la pasada edición de la EMO Hannover, celebrada en septiembre de 2019, bajo el lema ‘Las tecnologías inteligentes impulsan la producción del mañana’ pudieron verse temas de futuro como la conexión en red digital de las máquinas-herramienta, Internet industrial de las cosas (IIoT) y la interfaz de máquina universal Umati. La creciente importancia de la transformación digital en el sector de la máquina-herramienta quedó demostrada por numerosos expositores que vincularon sus máquinas-herramienta mediante soluciones de software innovadoras. A continuación, presentamos algunos de los puntos más destacados de la feria para dar una impresión de la gama de innovaciones expuestas en la EMO Hannover. Entre ellas se incluye una selección de nuevos desarrollos de máquinas-herramienta, pero también soluciones de digitalización y automatización que ahora forman parte integral de los entornos de producción modernos. A continuación, las innovaciones en la técnica de sujeción y las herramientas de precisión, que son campos indispensables para el mecanizado de metales. También se presentan nuevas funciones del sistema CAD/CAM para el diseño de componentes, la simulación del proceso de producción y la programación del sistema de control. Por último, el informe destaca las formas en que los temas futuros como la electromovilidad y la fabricación aditiva pueden estar estrechamente relacionados para aumentar la eficiencia y los niveles de precisión de los procesos de fabricación.
Herramientas mecánicas
Liebherr-Verzahntechnik GmbH sigue la tendencia de integrar diversos procesos de trabajo en las máquinas de tallado de engranajes. Un ejemplo presentado por el especialista en engranajes en la EMO Hannover fue la máquina de engranajes de corriente continua LK 280. Ésta combina el proceso de pelado de rodillos con el desbarbado automatizado durante el tiempo de mecanizado, permitiendo así el mecanizado completo de engranajes producidos en serie, por ejemplo en la industria del automóvil y en la fabricación de engranajes. La máquina se maneja con el sistema de programación LHGearTec, que está integrado en el sistema de control. Esto también ofrece acceso a la plataforma online de Liebherr, que a su vez proporciona acceso a otras funciones útiles, los llamados servicios LH. Entre ellas se encuentra la supervisión remota en directo del estado de la máquina. Otro punto culminante de la ingeniería en la feria fue el gemelo digital de la máquina. Esto ofrece grandes ventajas, especialmente durante la fase de desarrollo de la máquina. Permite la comprobación y optimización virtual de la estructura mecánica y la cinemática antes de la implementación real, además de la medición virtual de los tiempos de mecanizado.
El aumento de la demanda de soluciones de automatización también está impulsando la demanda de robots industriales en particular. Éstos requieren engranajes cicloidales de alta precisión para conseguir altos ratios de reducción. Durante su producción es crucial que se mantengan altos niveles de precisión hasta el rango micrométrico de un dígito cuando se mecanizan los agujeros y el perfil de los dientes. La máquina-herramienta Viper 500 MFM del fabricante Klingelnberg, de Hückeswagen, se encarga de ello. Se trata de una tarea que no se puede realizar con ciclos de mecanizado estándar, especialmente no de forma que se ahorre tiempo. Hasta cuatro engranajes cicloidales se rectifican simultáneamente en una sola sujeción. Una de las ventajas de la máquina es el dispositivo de medición integrado. Esto permite el control y la documentación individual de los engranajes cicloidales fabricados. Si el resultado del mecanizado no cumple las especificaciones requeridas, el software de medición calcula los valores de corrección adecuados. Éstos se transfieren automáticamente al control de la máquina para su tratamiento posterior directo, con el fin de garantizar el cumplimiento de las especificaciones de tolerancia. El operario de la máquina sólo tiene que habilitarlo. No hay necesidad de un manejo laborioso, adaptación del proceso o transferencia manual de los valores de corrección.
Como reacción a la creciente importancia de la e-movilidad, EMAG presentó soluciones de fabricación innovadoras para componentes de motores electrónicos. La superficie exterior de los rotores de los motores eléctricos, que se sueldan entre sí a partir de paquetes de chapa, debe ser repasada. Los requisitos de calidad de la superficie son tan elevados que sólo se permite un proceso de torneado longitudinal externo convencional con una baja velocidad de avance. Las superficies se pueden producir sin la torsión habitual que se produce durante el torneado mediante un proceso de torneado de pelado que produce un movimiento de rodadura de la herramienta sobre la pieza, lo que significa que el punto de contacto del filo de la navaja se desplaza continuamente. Esta calidad de la superficie sólo puede alcanzarse mediante el rectificado. Además, la elevada velocidad de avance permite reducir considerablemente el tiempo de proceso en comparación con los procesos de mecanizado alternativos, aumentando así la rentabilidad.
Además de los dispositivos de procesamiento mecánico y electroquímico, EMAG también presentó máquinas para la soldadura láser, la limpieza láser y la estructuración láser. La limpieza láser combinada en una máquina, es decir, la eliminación de la suciedad o los residuos de aceite de los componentes y la posterior estructuración de la superficie, puede preparar las superficies de los elementos de los componentes para su unión mediante encolado o lacado. Este proceso tiene una ventaja decisiva sobre el chorro de arena, ya que elimina la necesidad de una costosa limpieza de los componentes después de la estructuración por láser.
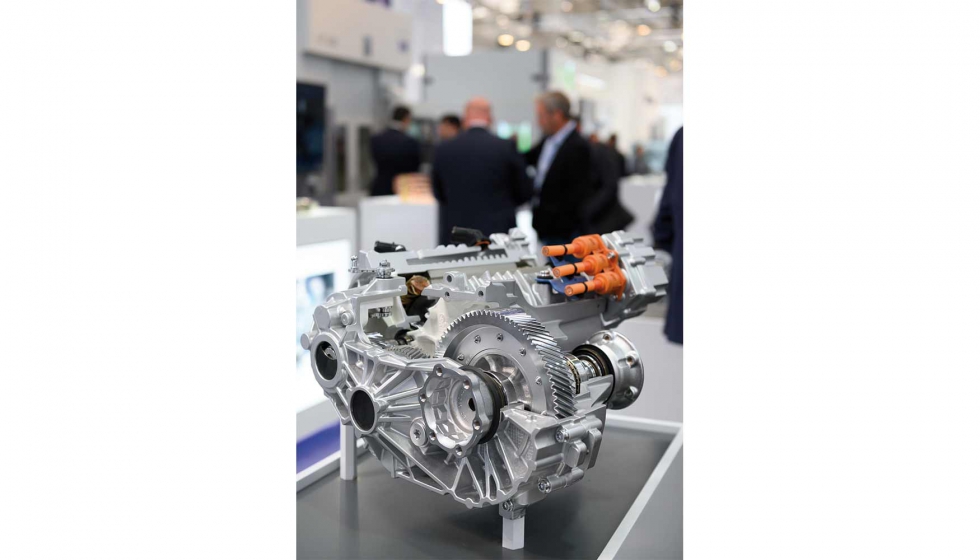
Krause + Mauser, de Oberndorf am Neckar, es un renombrado especialista en soluciones de fabricación para la industria automovilística. En la EMO la empresa presentó desarrollos innovadores, por ejemplo, para el taladrado fino CNC de bielas. Anteriormente, el taladrado de forma 2D permitía crear un contorno de trompeta o una forma ovalada con una tolerancia de unos pocos micrómetros en el pequeño ojo de biela para mejorar la lubricación en este rodamiento y, por tanto, minimizar la fricción. Un nuevo cabezal de taladrado piezoeléctrico 3D con un filo de corte controlable permite ahora también un taladrado no circular definido en el rango de los micrómetros, lo que mejora aún más las propiedades de fricción del rodamiento. Permite producir formas ovaladas o libres 3D y compensar los errores de forma sistemáticos que surgen de las fuerzas de corte o de las influencias de sujeción.
Por su parte, Index-Werke GmbH presentó un nuevo desarrollo de tornos automáticos de producción de doble husillo que complementa los tornos automáticos de un solo husillo de la serie C. El concepto de máquina en tándem con dos husillos principales y contrahusillos idénticos duplica el rendimiento sin aumentar la superficie de trabajo o la necesidad de personal. De esta forma, la máquina cierra el hueco entre los tornos automáticos monohusillo y multihusillo. Otra innovación de Index-Werke es el software de astillado ChipMaster que forma parte integral del ciclo. Este puede ser usado en los tornos Index con los últimos controles de Siemens, o reequipado si es necesario. El software varía la alimentación para interrumpir la formación de la viruta y así evita la creación de largas virutas continuas. El ciclo se puede implementar independientemente del material de la pieza de trabajo y ofrece una solución sencilla y económica, por ejemplo, para evitar intervenciones no planificadas por parte del operario de la máquina para retirar las virutas continuas y enredadas.
Y Heller Maschinenfabrik GmbH, con sede en Nürtingen, se centró en tres temas principales: la digitalización, la globalización con proximidad al cliente y los nuevos modelos de negocio. El fabricante de máquinas presentó tres nuevas unidades, entre ellas la H 2000 y la HF 3500. El centro de mecanizado de 4 ejes H 2000 ofrece una mayor productividad que sus predecesores gracias a las medidas diseñadas tanto para reducir el peso como para aumentar la rigidez. Esto se ha conseguido gracias a la utilización de estructuras de bancada y columnas de fundición optimizadas desde el punto de vista topológico. El centro de mecanizado de 5 ejes HF 3500 con el paquete speed-dynamics permite un mayor rango dinámico y, por tanto, un aumento de la productividad en el mecanizado simultáneo en 5 ejes. Además, se ha añadido una solución de automatización al centro de mecanizado en forma de un robot de colaboración de Fanuc en combinación con un sistema de pinzas de Schunk. Estos son cada vez más importantes en el entorno de producción moderno como resultado, por ejemplo, de la continua escasez de trabajadores cualificados. Heller tiene previsto utilizar soluciones de automatización adaptadas localmente como base para el mercado mundial y ampliarlas con aplicaciones propias.
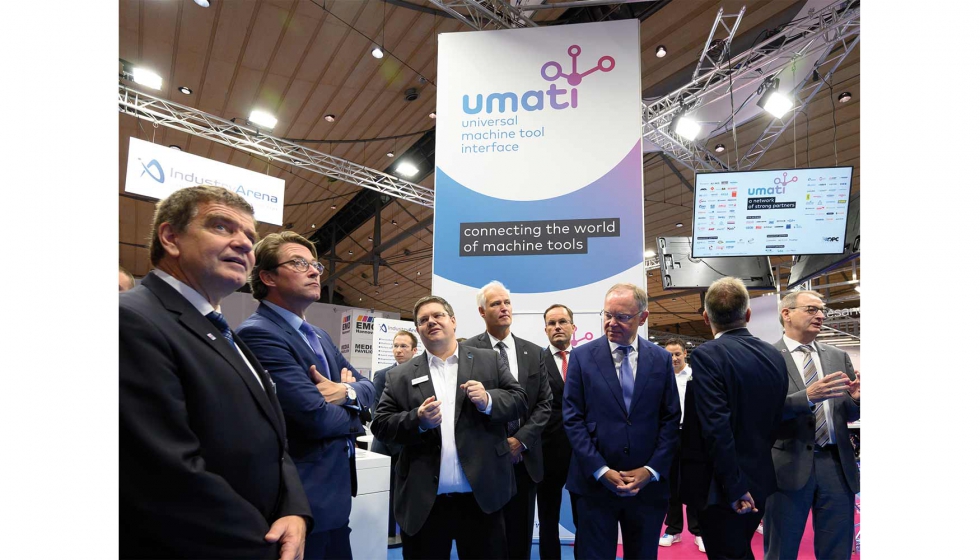
El sistema de lenguaje común Umati estuvo muy presente durante la feria desde la misma visita de apertura con el Ministro Federal de Transporte e Infraestructura Digital Andreas Scheuer.
En el ámbito de las máquinas-herramientas para la fabricación de precisión, la empresa Kern Microtechnik GmbH de Eschenlohe presentó su última incorporación a la serie Kern Micro. El modelo Kern Mikro HD utiliza una gestión de temperatura optimizada con control activo de la temperatura de los componentes de la máquina para evitar las desviaciones de precisión causadas por las influencias de la temperatura. Un sistema de accionamiento único basado en la combinación de accionamientos de motor lineal y la hidrostática micro-gap logra altos niveles dinámicos y de productividad, la máxima calidad de los componentes y ayuda a prevenir el desgaste de los ejes de accionamiento. La máquina tiene un diseño compacto con una superficie de menos de 5 m² y, sin embargo, contiene cambiadores integrados en un almacén para hasta 210 herramientas y 60 piezas de trabajo, lo que permite un funcionamiento autónomo de la máquina en varios turnos.
Digitalización y automatización
La interfaz estándar Umati (interfaz universal de máquina-herramienta) estuvo más o menos omnipresente en EMO Hannover. Numerosas máquinas de todo el recinto ferial se marcaron con el logotipo Umati. En ellas se mostraban datos en tiempo real, como el número de revoluciones actual del cabezal o el estado de mecanizado. Todos los visitantes de la feria pudieron visualizarlo de forma sencilla llamando a la página web de Umati en su propio teléfono inteligente. 70 empresas de diez países participaron en la feria: estas empresas conectaron en red 110 máquinas y 28 servicios de valor añadido. El éxito de la implementación, así como el sólido funcionamiento durante toda la semana de la EMO y las miles de consultas simultáneas de los datos en directo confirmaron la eficacia de Umati. El siguiente hito es el lanzamiento de la versión 1.0 del estándar OPC UA, que está previsto para mediados de 2020.
El fabricante de máquinas-herramienta DMG MORI demostró cómo sus productos pueden digitalizar toda la cadena de producción, desde la planificación y la preparación hasta la producción, la supervisión y el servicio. Se presentaron más de 30 innovaciones digitales. La conectividad es un requisito fundamental para la fábrica digital: entre sus ventajas se encuentra una mayor transparencia gracias al registro y documentación continuos de los datos de la planta de producción. Por esta razón, todas las nuevas máquinas DMG Mori deben ser equipadas gratuitamente con una interfaz IIoT (Industrial Internet of Things) en el marco del programa de conexión de DMG MORI a partir de la EMO Hannover 2019. Esto permite la conexión a diferentes plataformas de IoT (Internet of Things), como Adamos, MindSphere y Fanuc Field. Además, más de la mitad de las 45 exposiciones de la EMO que el fabricante de máquinas-herramienta presentó contenían soluciones de automatización. Uno de los aspectos más destacados fue el sistema de transporte sin conductor PH-AGV 50, que puede utilizarse incluso en áreas de producción existentes para la manipulación autónoma de palés. Según DMG MORI, el desarrollo de nuevas soluciones de automatización es ahora tan importante como el de nuevos modelos de máquinas.
THK, un proveedor de guías lineales con sede en Minato, Japón, presentó un desarrollo orientado a la aplicación en forma de módulos de sensores para sus guías lineales y husillos de bolas. El módulo de sensores puede instalarse posteriormente en las guías lineales existentes para medir las vibraciones durante el funcionamiento. THK utiliza estas mediciones de vibraciones y el servicio asociado de IoT Omni edge para determinar el estado del sistema y utiliza esta información para supervisar y realizar el mantenimiento remoto de sus componentes.
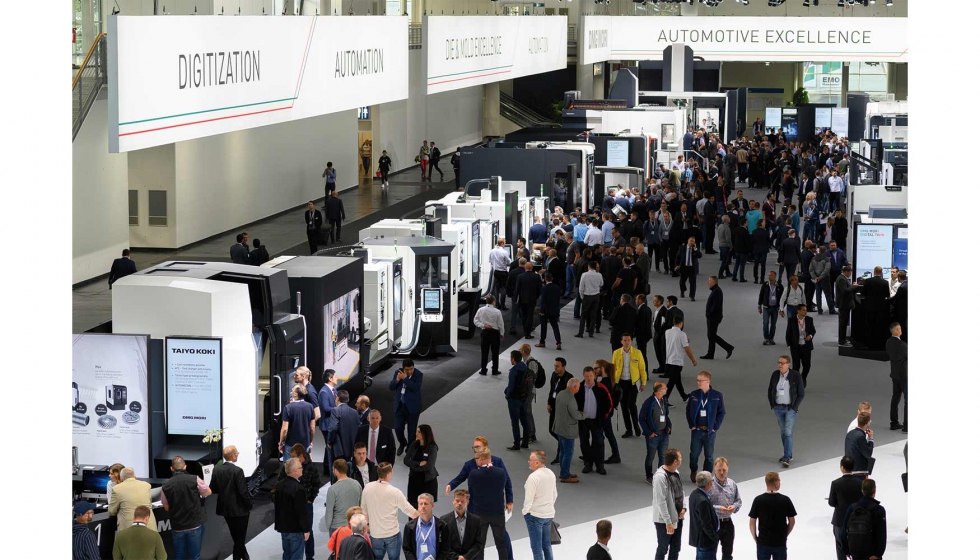
Fijación de la pieza de trabajo
Todos los procesos de la máquina-herramienta requieren el uso de equipos de sujeción para mantener la pieza de trabajo en posición segura durante el mecanizado. De los nuevos productos presentados en la EMO Hannover surgieron dos tendencias en particular: un manejo más sencillo para reducir los tiempos improductivos y la integración de la electrónica en los elementos de sujeción para apoyar los sistemas de automatización de mayor nivel.
Schunk GmbH & Co. KG, el experto en sistemas de sujeción y técnicas de fijación de Lauffen am Neckar, presentó una serie de novedades en su stand. Entre ellos se encontraba la pinza eléctrica KSE 100, que garantiza una sujeción correcta mediante un sistema de medición del recorrido de sujeción integrado. En su sistema de sujeción de punto cero NSE S3, Schunk presentó un elemento de sujeción que permite consultar el estado de la sujeción. Esto es útil para reconocer una transferencia de pieza exitosa, especialmente en procesos de carga automatizados. Además de proporcionar un reconocimiento binario, el elemento de sujeción en el punto cero NSE S3 también mide la fuerza de sujeción mediante sensores integrados. De este modo se pueden controlar las fuerzas necesarias para la sujeción de los componentes y obtener información sobre las tendencias para las medidas de mantenimiento preventivo.
El fabricante de dispositivos de sujeción Römheld GmbH de Laubach sigue ampliando sus soluciones de digitalización. Los actuadores lineales hidráulicos y las mordazas giratorias, equipados por primera vez con un sensor de posición integrado, facilitan el control de la altura de la pieza. Esto es útil, por ejemplo, en piezas de fundición en las que la geometría puede fluctuar considerablemente hasta un milímetro o más debido al proceso de fundición. Los elementos de sujeción comprueban la geometría de la pieza en los puntos de sujeción con una precisión de una décima de milímetro durante la sujeción propiamente dicha. Normalmente es demasiado costoso y en muchos casos imposible obtener información comparable de los sistemas de medición de desplazamiento convencionales en el reducido espacio de trabajo de la máquina-herramienta.
Andreas Maier GmbH & Co. KG de Fellbach presentó una nueva pinza que permite que la propia máquina-herramienta se ocupe de las tareas de manipulación de la pieza. Normalmente se utilizan robots para esta aplicación de automatización. Lo especial de la pinza es que puede ser insertada en el husillo de trabajo de la máquina-herramienta (como una herramienta de corte) y almacenada en el almacén de herramientas. La pinza recibe la energía de accionamiento a través de aire comprimido o, alternativamente, a través del suministro de lubricante refrigerante. La mayoría de las máquinas-herramienta disponen de al menos una de estas fuentes de energía. En ambos casos, la fuerza de sujeción se puede ajustar de forma continua. También dispone de una opción de consulta eléctrica, alimentada por batería. Esta controla el proceso de sujeción y da una confirmación por radio de su finalización con éxito.
Y Hainbuch GmbH de Marbach presentó una innovación libre de electrónica en forma del CentroteX S. Se trata básicamente de un sistema de cambio rápido para platos de torneado. Incluso los cambios rápidos de los platos convencionales pueden tardar varios minutos, mientras que el nuevo sistema permite cambiarlos en menos de un minuto. Tiene un nivel de precisión de repetición muy alto de sólo dos micrómetros.
Herramientas de precisión
Sandvik Coromant presentó un sistema de perforación indexable recientemente desarrollado que puede perforar a profundidades de hasta siete veces el diámetro de la perforación (7xD). El cuerpo base y los insertos indexables de la broca indexable CoroDrill DS20 han sido rediseñados. Las fuerzas reducidas y la facilidad de corte mejoran la fiabilidad del proceso, especialmente durante la penetración del material. El aumento de la profundidad de perforación puede eliminar la necesidad de perforar desde ambos lados de un componente, ahorrando tiempo y dinero y mejorando la calidad del agujero. Un importante objetivo de desarrollo fue la reducción de las emisiones de ruido. Esto se logró a través del diseño de la herramienta y la atenuación de las vibraciones torsionales. Sandvik Coromant también ha lanzado un nuevo MDI (Modular Drilling Interface). El diseño modular de la broca y el adaptador de acoplamiento significa que una sola interfaz puede utilizarse para múltiples diámetros de broca. El doble centrado con alta precisión dimensional asegura una concentricidad óptima y una precisión de repetición.
La planta Emuge de Richard Glimpel GmbH & Co. KG ha desarrollado una nueva tecnología de corte de rosca en cooperación con Audi, Ingolstadt. Esto reduce considerablemente el tiempo necesario para el corte de los agujeros roscados. El corte de roscas convencional consta de dos pasos: el taladrado sólido y el posterior corte de roscas propiamente dicho. El sistema Taptor, de nuevo desarrollo, permite realizar el taladrado macizo y el corte de roscas en un solo paso. La eliminación de las etapas de pre-perforación y cambio de herramienta que antes eran necesarias proporciona al nuevo proceso una ventaja de tiempo significativa, aumentando así la capacidad de la máquina. La tecnología se integrará, junto con Audi, en la producción en serie de componentes de aluminio fundido.
El especialista en herramientas de taladrado profundo, Botek Präzisionsbohrtechnik GmbH presentó un paso innovador para el procesamiento de herramientas desgastadas con pocos recursos. En el futuro, Botek permitirá equipar las brocas monolabiales de metal duro desgastado (tipo 113 y 113-HP) con una nueva cabeza de metal duro. Hasta ahora, sólo era posible sustituir las brocas monolabiales en herramientas con vástagos de acero. Gracias al nuevo procedimiento desarrollado, el mango de metal duro de las herramientas puede ahora reutilizarse varias veces. Esto no afecta a las propiedades de productividad, seguridad de proceso y calidad de mecanizado de la herramienta. También es posible rectificar las herramientas. Las brocas monolabiales de metal duro se pueden recargar en una gama de diámetros de 5,0 a 12,0 mm, lo que ayuda a los clientes a ahorrar energía y material y, por tanto, costes.
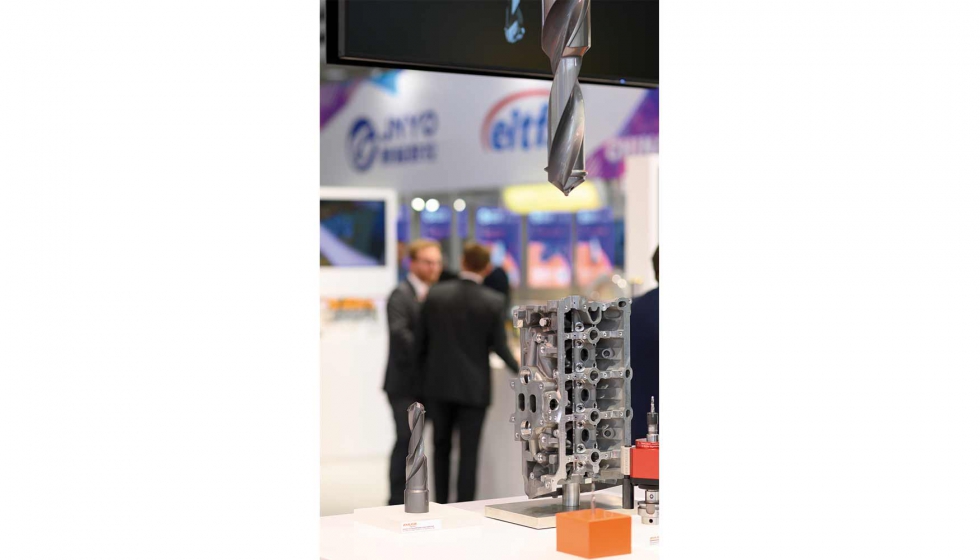
CAD / CAM y software de control
Un punto culminante de la tecnología de control fue el Sinumerik One de Siemens AG, Munich. Los gemelos digitales ayudan a la transformación digital permitiendo que los procesos de trabajo sean simulados y probados de forma completamente virtual. La empresa Fill GmbH, con sede en Gurten, es el único socio austriaco de desarrollo (y uno de los pocos constructores de máquinas) que participa en Sinumerik One. Fill presentó el centro de mecanizado syncromill h21-63/500 equipado con el sistema de control Sinumerik One en la EMO Hannover 2019. Ha sido especialmente desarrollado para el mecanizado de componentes de marcos estructurales, como los que se utilizan, por ejemplo, en aplicaciones de e-movilidad.
SolidCAM GmbH de Schramberg presentó las nuevas funciones de su software de solución CAM SolidCAM 2019. Esto permite una programación rápida y sencilla de las máquinas-herramientas, incluyendo centros de torneado y fresado multicanal y tornos de cabezal móvil CNC. Incluso máquinas complejas con varios ejes pueden ser virtualmente mapeadas para la simulación y verificación de las operaciones de mecanizado con la ayuda de la simulación de máquina integrada. La base de datos de máquinas se amplía constantemente. Se han añadido más funciones al software. Éstas permiten, por ejemplo, ajustar la velocidad de la herramienta para cualquier profundidad de taladrado. El rango de tipos de herramientas soportadas para el mecanizado simultáneo en 5 ejes ha sido ampliado de manera que ahora se pueden utilizar todos los tipos de cortadores de segmentos circulares, incluyendo cortadores de barril, lentes, gotas y conos.
DP Technology, Camarillo USA, presentó sus últimas innovaciones de software Esprit CAM. El Esprit Additive soporta la programación de máquinas de fabricación aditiva, así como de máquinas híbridas aditivas y sustractivas. El software puede utilizarse para generar trayectorias de herramienta especializadas para procesos de fabricación aditiva como la soldadura por deposición láser, así como para el posprocesamiento sustractivo de los componentes resultantes. Otra característica clave del sistema CAM Esprit es la integración de algoritmos basados en inteligencia artificial (AI) que optimizan automáticamente el programa. Esto simplifica los procesos de programación y aumenta la productividad de la máquina.
Tecnología de producción para la electromovilidad
La electrificación de la cadena de transmisión también presenta interesantes desafíos para el desarrollo de nuevas soluciones de fabricación y conceptos de herramientas. La forma en que se producen los motores eléctricos para coches híbridos o totalmente eléctricos es crucial aquí. Las cantidades crecientes que se necesitan requerirán que los procesos de fabricación de componentes para motores eléctricos se organicen de forma eficiente.
Ceratizit Luxembourg presentó varios conceptos de herramientas innovadoras que permiten el mecanizado preciso y eficiente de carcasas de aluminio para motores eléctricos. El reto consiste en lograr un mecanizado preciso de los orificios del estator con diámetros de aprox. 200 a 300 mm y una profundidad de más de 300 mm. Las herramientas deben ser de construcción ligera para no sobrepasar la carga admisible de los husillos de la máquina. Una de estas soluciones de herramientas que cumple estos requisitos es una herramienta de perforación fina totalmente aditiva que se expuso en la EMO Hannover. Se utilizó la fabricación generativa para diseñar estructuras filigranas y con puntales para el cuerpo base, permitiendo así la fabricación de una herramienta relativamente ligera pero rígida. Los taladros del estator pueden mecanizarse en un solo paso, respetando las tolerancias IT6 y las tolerancias de redondez de hasta 2/100 mm.
Ceratizit presentó otro desarrollo de herramientas de mandrinado fino en forma de una barra de mandrinado escalonada de plástico que es más fácil de fabricar y más rentable gracias a su diseño modular. Esta herramienta consiste en un cuerpo base tubular ligero que se fabrica convencionalmente mediante procesos de mecanizado. A este cuerpo base se le aplican capas producidas adicionalmente que contienen PCD (diamante policristalino) o casetes equipados con insertos indexables. Esto permite obtener el diámetro de mecanizado correcto del diámetro del estator. Estas capas, compuestas por un plástico reforzado con fibras especialmente desarrollado, son capaces de canalizar las fuerzas de mecanizado en el cuerpo base. Gracias a la construcción modular del cuerpo base y de las capas, la herramienta se puede adaptar de forma rápida y económica a las necesidades del cliente.
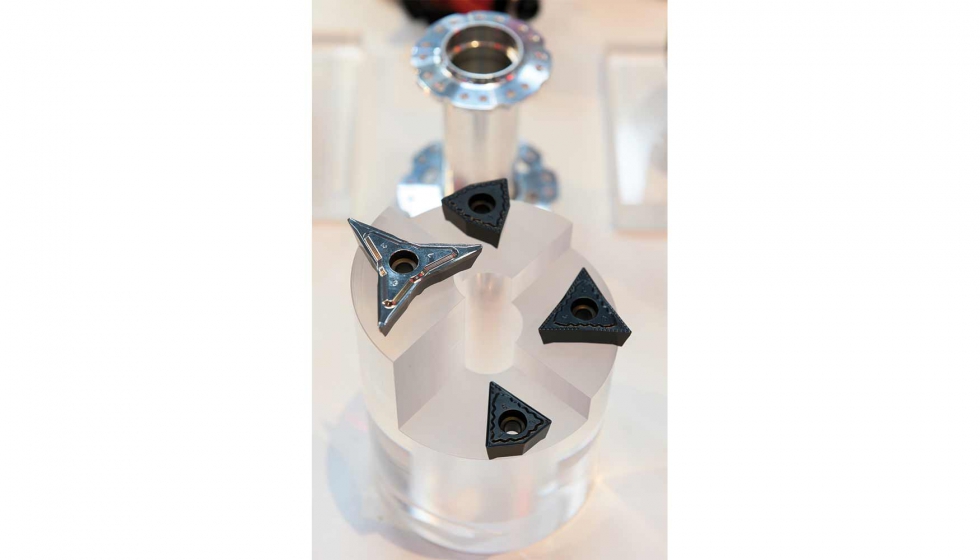
Fabricación aditiva
La creciente importancia de la fabricación de aditivos en la producción en masa ha dado lugar a un aumento de la demanda de procesos automatizados de fabricación de aditivos. El fabricante suizo de máquinas-herramienta GF Machining Solutions presentó el DMP Flex 350. Se trata de una nueva máquina para la impresión metálica en 3D que ofrece una calidad de componentes altamente reproducible y una capacidad de automatización excepcional. La alta calidad se consigue creando un vacío antes de la admisión de gas inerte durante el proceso de lecho de polvo. Esto extrae aire oxigenado incluso de los espacios entre los polvos, evitando así reacciones que interrumpan el proceso. La cámara de vacío sellada, junto con el polvo y los componentes, se puede retirar automáticamente de la máquina después del proceso de impresión en 3D. La ventaja en este caso es el corto tiempo de cambio, ya que la máquina puede iniciar inmediatamente el siguiente proceso de impresión una vez que se ha insertado una nueva cámara de vacío. No es necesario detener la máquina para la laboriosa y larga retirada de componentes, necesaria, por ejemplo, para la manipulación de partículas de polvo finas y peligrosas.
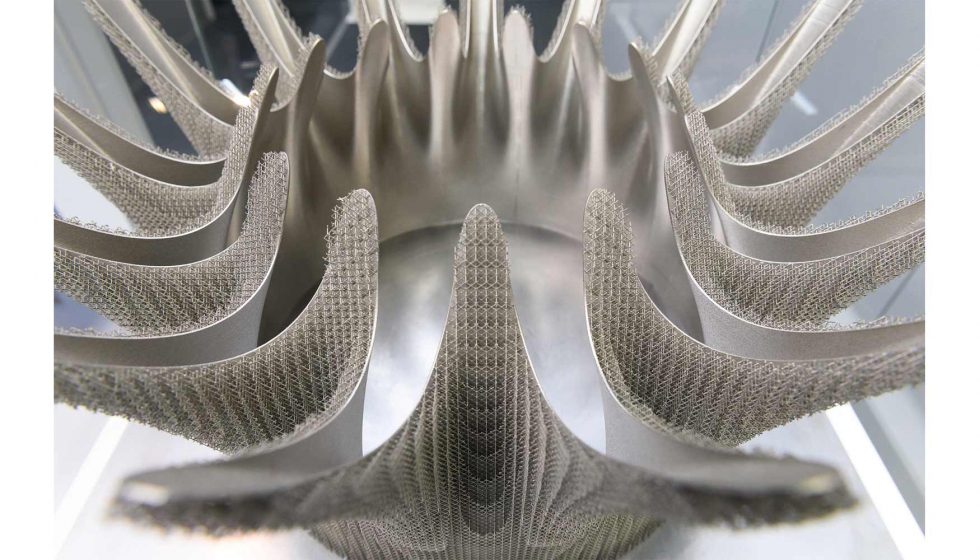