Solución de problemas de plaquitas intercambiables
Un poco de historia: el desarrollo de la plaquita intercambiable
A mediados de los años 50 las herramientas de corte con plaquita intercambiable revolucionaron el mecanizado. El hecho de que una punta de filo de corte estuviera soldada al soporte implicaba que era inamovible y que se limitaban en gran medida las opciones de material de la herramienta. Asimismo era necesario reafilar el filo repetidas veces. La eliminación de este problema mediante las plaquitas intercambiables condujo al desarrollo de nuevas calidades de carburo cementado y, en consecuencia, al desarrollo de recubrimientos de plaquitas. La reducción de la ubicación y tamaño del material de corte al filo de corte de la herramienta permitió la implantación de nuevas tecnologías que mejorarían considerablemente el rendimiento del mecanizado.
Entre ellas estaban el desarrollo por un lado de geometrías de corte que facilitaran el proceso de mecanizado y por otro lado de un sistema de sujeción de herramientas que hiciera más eficaces tanto la instalación como el mantenimiento. Otro logro lo constituyó la estandarización e intercambiabilidad de las herramientas de corte.
De modo que en la actualidad, medio siglo más tarde, ¿en qué punto se encuentra la tecnología de plaquitas intercambiables?
Es de destacar que a lo largo de la pasada década las plaquitas de corte intercambiables para fresado dieron paso a nuevos conceptos de cuchilla de diseño libre, aunque siempre dentro de los límites impuestos por las normas ISO. El resultado fue un mayor rendimiento, pronunciados ahorros para la industria metalúrgica y herramientas perfectas para la nueva maquinaria CNC.
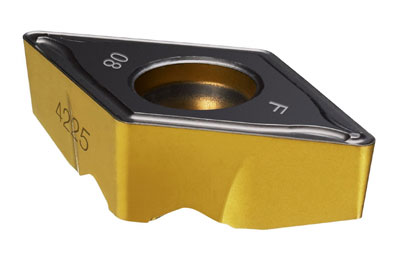
El movimiento es sinónimo de problemas
En especial representa un problema el movimiento de la plaquita en el caso de las plaquitas de torneado más grandes, entre ellas las de forma en V y D con ángulos del punto de 35 y 55 grados, que se utilizan con frecuencia para procesos de perfilado y ahuecado. Estas plaquitas se utilizan normalmente para acabado y sus filos de corte generan una superficie estrechamente controlada mediante el acabado superficial y las tolerancias de las dimensiones. La larga palanca existente entre el tornillo central y el filo de corte de estas plaquitas produce una elevada presión, lo cual puede producir una deformación plástica en las localizaciones de los apoyos de las plaquitas y permitir el movimiento del filo de corte.
Además, la sujeción convencional del tornillo de estas plaquitas en el apoyo del portaherramientas ocasiona que se ejerza una acción combinada hacia abajo y hacia los laterales al apretar estos tornillos, lo que aumenta la inestabilidad de la plaquita en el portaherramientas.
Cualquier tendencia de las plaquitas a moverse en el apoyo, por ligera que sea, puede afectar también a la formación de virutas. Cuando la profundidad de corte se reduce desde un nivel que es relativamente pequeño al principio, dicha profundidad se hace mucho más pequeña en relación con el radio delantero de la plaquita, de modo que el proceso de rotura y formación de dichas virutas se degrada.
El objetivo es conseguir que la plaquita no se mueva, lo que eliminaría la necesidad de reducir los datos de corte.
¿Constituyen las normas ISO un obstáculo para la innovación?
El torneado con plaquitas intercambiables se ha visto frenado por dos problemas concretos:
Acabado y torneado semiacabado
Este problema es producto de diminutos desplazamientos de las plaquitas dentro del juego de sujeción del sistema portaherramientas. Por supuesto que este mismo efecto influye asimismo en el rendimiento y en los resultados de los procesos de torneado medio, que presentan una creciente necesidad de conseguir tolerancias de trabajo precisas.
CoroTurn TR de Sandvik Coromant evita el movimiento de las plaquitas. Unas ranuras perpendiculares en la parte inferior de las plaquitas que encajan en rieles coincidentes (riel en T) del portaherramientas impiden cualquier movimiento de la plaquita en su apoyo cuando la fuerza de corte actúa sobre el filo. CoroTurn TR soluciona el problema del deterioro de la precisión, el desgaste innecesario de la herramienta y la pérdida de productividad debidos a la flexión del filo de corte durante el mecanizado. Otro efecto favorable añadido es la localización precisa de la plaquita en el portaherramientas, que influye positivamente en el ángulo de montaje y en la necesidad de compensación de la máquina.
Este usuario tenía que mantener una vida concreta de la herramienta para que el torneado de precisión se ajustase al cambio de configuración de los palets de componentes. El problema se agudizó cuando la herramienta de torneado, con plaquita intercambiable de forma en D según norma ISO, sólo resultó capaz de procesar dos tercios del número de componentes necesarios para cada palet entre cada indexación. La causa detectada fue el movimiento microscópico de la plaquita. El eje de acero que se iba a mecanizar tenía una tolerancia en las dimensiones de 0,02 mm en algunos lugares, un límite de acabado superficial de 1,3 micrones de radio y huecos y hombros, lo que hacía aumentar el movimiento de la plaquita. Al reducir a la mitad la profundidad de corte, de 0,25 a 0,12 mm, se redujo a su vez la fuerza de corte, lo cual ocasionó problemas de rotura de las virutas e interferencia de dichas virutas con la medición automatizada tras el mecanizado.
En otro proceso que implicaba copiado y perfilado de una cavidad radial, se necesitaron varios ajustes del filo de corte mediante compensación de la máquina para mantener la tolerancia de forma. En este caso la vida de la herramienta se duplicó al eliminar el movimiento de la plaquita. Se limitaron las paradas de la máquina a sólo una compensación de filo de corte a mitad del lote.
La solución al problema en ambas aplicaciones fue la precisa colocación de la plaquita en el portaherramientas gracias al riel en T.
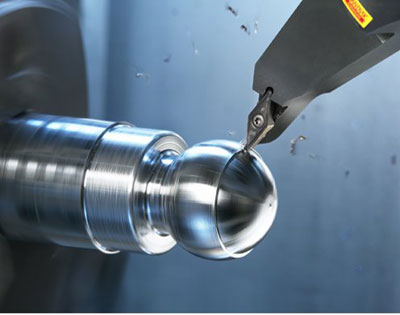
Procesos internos y de acabado
En un caso con mecanizado de acabado interno, el taller de maquinaria usaba una herramienta de mandrinado multifilo que requería una determinación exacta de la posición del filo de corte. Cada cambio de herramienta suponía paradas de 15 minutos. La eliminación del movimiento de la plaquita conseguía mantener la precisión y evitar las paradas. La eliminación de 1.500 cambios de herramienta por año representó un aumento de 375 horas del tiempo de mecanizado.
La sujeción puede implicar obstrucciones
Solución de problemas de movimiento de la plaquita
Los operarios experimentados de un taller de maquinaria encuentran formas de solucionar los movimientos microscópicos del filo de corte y las pérdidas de precisión, el doble problema de las plaquitas intercambiables. En ocasiones algún operario llega a una solución temporal o fabrica una herramienta especial para solucionar el problema. De forma alternativa, el taller aprende a vivir con el problema, sin darse cuenta de que procede del empleo de plaquitas intercambiables que cumplen las normas ISO. El usuario compensa los efectos con la programación, normalmente modificando los datos de corte, de pasadas adicionales o distinto recorrido de la herramienta. Las consecuencias indeseadas más comunes de esas soluciones son una mayor duración de los ciclos, un deficiente control de las virutas y el uso de plaquitas innecesariamente grandes.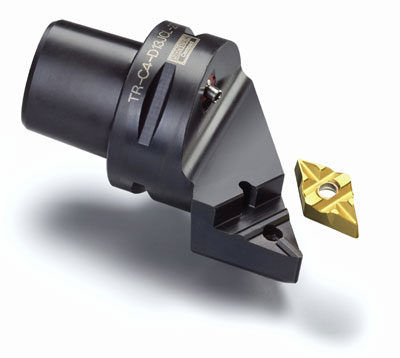
Evolución de la tecnología de plaquitas intercambiables
Una razón fundamental es la adhesión a las normas ISO de las plaquitas de torneado y las limitaciones al diseño que induce dicha estandarización. Además, hasta ahora las antiguas técnicas de sujeción de las plaquitas han resultado aceptables para la mayor parte de las aplicaciones, al contrario que en la actualidad, en que las demandas de rendimiento y los resultados exigidos al torneado son mucho mayores.
Otra razón reside en las limitaciones de la tecnología de fabricación de las plaquitas.
Las plaquitas especiales rectificadas solucionaron este tipo de problema cuando las plaquitas estándar dejaron de ser adecuadas. Ahora, la tecnología de prensado de plaquitas permite soluciones de precisión para la localización y el apoyo de plaquitas intercambiables con seguridad, pero únicamente fuera de las normas ISO.
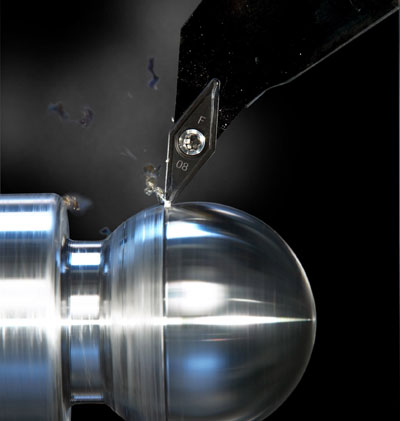
CoroTurn TR
Los claros beneficiarios de este avance son los fabricantes de componentes de precisión. Los componentes se pueden mecanizar con tolerancias muy estrechas y un mejor acabado superficial, con una mayor vida de la herramienta y menos cambios de herramienta. La productividad no tiene por qué verse comprometida por el uso de datos de corte menores y las paradas de compensación se reducen gracias una vida de la herramienta más prolongada y homogénea, además de una mayor precisión.
Muchas aplicaciones de torneado medio se benefician de la ausencia de movimiento y de la precisión de la indexación hasta ± 0,05 mm que proporciona CoroTurn TR.
Problemas esenciales resueltos
El perfilado con plaquitas en punto (D y V) es otro problema solucionado por CoroTurn TR ya que las plaquitas grandes usadas con frecuencia para operaciones de perfilado sufren más movimientos por efecto de la fuerza de corte. Normalmente, los problemas aparecen durante los procesos de copiado interno y externo, y cuando se mecanizan piezas de forjado o de fundición con distintas tolerancias, dureza de la corteza y recorrido de la herramienta. En este sistema no se necesitan cuñas de carburo cementado, al contrario que en la sujeción convencional, porque sin movimiento de la plaquita no aparecen desgaste ni deformación significativos en el apoyo.Las plaquitas CoroTurn TR solucionan el problema en un creciente número de procesos de torneado en aplicaciones de acero y acero inoxidable. La nueva tecnología de plaquitas proporciona, además, nuevas posibilidades para modernizar procesos de torneado medio o en acabado, así como de perfilado que están sujetos a límites cada día más restrictivos y a presión de la competencia. El desarrollo de CoroTurn TR está en línea con los avances en máquinas multitarea, en las que unas herramientas flexibles, con mayor precisión, permiten un mejor uso, contribuyendo a un mecanizado completo de los componentes “de una vez” en una sola configuración.