La Fundación IMH a través de su departamento Asmaola ha llevado a cabo una serie de ensayos de mecanizado con refrigerante a alta presión
Mecanizado con alta presión de refrigerante: ganancias en duración de vida de herramienta de corte y tiempo de proceso
Muchas pymes han detectado la necesidad de resolver una problemática relacionada con la rotura de viruta en sus procesos automatizados de mecanizado de piezas, que en un elevado porcentaje trabajan con el acero inoxidable 316L. A fin de ayudar a resolver a estas empresas su problemática y de demostrarles las ventajas o mejoras que aporta el mecanizado con refrigerante a alta presión (HPC), se han llevado a cabo una serie de pruebas experimentales sobre un cuerpo de acero inoxidable AISI316L en un centro de torneado Ibarmia utilizando niveles de presión de refrigerante hasta 80 bar. En este artículo se resumen los resultados de aumento de duración de vida de las herramientas de corte obtenidos en dichas pruebas experimentales.
Uno de los principales factores económicos en el proceso de mecanizado es la duración de la herramienta de corte; el desgaste de la herramienta es una variable que afecta directamente en el coste del proceso y en el acabado de las superficies de la pieza mecanizada.
Diferentes fabricantes de herramientas de corte han publicado informes de estudios que reflejan las ventajas que aporta la aplicación del refrigerante de forma eficaz mediante chorros de alta presión, dirigidos directamente a la zona de corte. Además reflejan que esta influencia es especialmente importante en el mecanizado de materiales considerados de baja maquinabilidad, como las superaleaciones, el titanio y los aceros inoxidables. La necesidad de controlar el calor disipado en el proceso y la formación de la viruta, entre otros, obliga a adoptar medidas especiales.
1. Introducción
Debido al incremento de demanda por parte de las pequeñas empresas de mecanizado del entorno acerca de la problemática existente en la rotura de herramientas de corte, dificultades de evacuación de viruta y el elevado nivel de desgaste de herramientas durante el mecanizado del acero inoxidable (en un 90% de los casos), con el impacto económico que todo ello supone, la Fundación IMH a través de su departamento Asmaola ha llevado a cabo una serie de ensayos de mecanizado con refrigerante a alta presión en sus instalaciones a fin de demostrar y transferir dicha tecnología a las empresas.
Esta tecnología consiste básicamente en dirigir el líquido refrigerante a alta presión de forma efectiva sobre la zona de corte y su mayor aplicabilidad se encuentra en el mecanizado del acero inoxidable y el acero con bajo nivel de carbono y, en especial, los materiales más exigentes, como aleaciones de titanio, níquel y otras superaleaciones resistentes al calor empleados principalmente en la industria aeronáutica y aeroespacial [1].
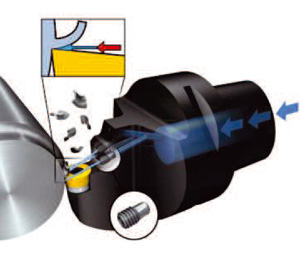
Figura 1. Aplicación del refrigerante a alta presión en torneado (Sandvik).
Se han realizado grandes avances en el desarrollo de nuevas aleaciones que mantengan sus propiedades a altas temperaturas y sean resistentes a la corrosión, pero sin embargo estas aleaciones de hierro, níquel, titanio y aluminio presentan una gran dificultad a la hora de ser mecanizadas. La compleja maquinabilidad de las aleaciones de titanio y de níquel se debe, entre otros, a la mala capacidad de disipación del calor generado en el mecanizado, lo que conlleva que se alcancen temperaturas superiores a 1.000º en el extremo de la herramienta provocando un elevado gradiente de temperatura.
La aplicación del refrigerante a alta presión en este tipo de mecanizados ofrece en comparación al mecanizado convencional ciertos avances en:
- la formación de virutas.
- distribución del calor generado.
- la adherencia del material de la pieza en el filo de corte.
- la integridad de la superficie.
- el desgaste de la herramienta.
Y todo ello afecta al proceso de fabricación consiguiendo una mayor competitividad y logrando:
- mayor productividad.
- aumento de la duración de vida útil de la herramienta de corte.
- mayor calidad de los componentes.
- un control más preciso de la forma de la viruta producida así como de su evacuación.
La rotura de la viruta durante el mecanizado depende de la profundidad de corte, de la velocidad de avance, la velocidad de corte y la presión del refrigerante [2]. La elevada presión del fluido de corte facilita la rotura de la viruta y además su efecto refrigerante es mayor en la zona de corte lo que permite reducir considerablemente la temperatura. Todo ello permite aumentar por una parte las condiciones del proceso y, por consiguiente, reducir los tiempos de ciclo de mecanizado y por otras parte la vida útil de las herramientas de corte.
El objetivo principal de este trabajo ha consistido en contrastar estas conclusiones mediante pruebas experimentales con un material y bajo unas condiciones de trabajo que se presentan con mucha frecuencia en pequeñas empresas de mecanizado del entorno.
2. Definición de las variables del proceso en las pruebas experimentales
A continuación se describen las diferentes variables de proceso definidas para la ejecución de las pruebas experimentales.
2.1. Material a mecanizar
A pesar de que el Inconel y el Titanio sean los materiales que mayor interés están suscitando en la industria aeronáutica y aeroespacial (actualmente sectores de mayor peso en el mercado), las pruebas experimentales de mecanizado con refrigeración a alta presión se han centrado en el material AISI 316L/EN14404 debido a que éste es el material más empleado por las empresas de entorno que trabajan en el sector de automoción, alimentación, mecanizado de bombas y válvulas y operaciones de decoletaje y taladrado profundo.

Se trata de un acero austenítico que presenta una baja maquinabilidad.
Para la ejecución de las pruebas experimentales se ha utilizado una barra perforada de este mismo material de 236 mm de diámetro exterior y 150 de diámetro interior.
2.2. Centro de torneado
Las pruebas experimentales de torneado se han realizado sobre un centro de torneado multiprocesos Ibarmia ZVH38/L1600.
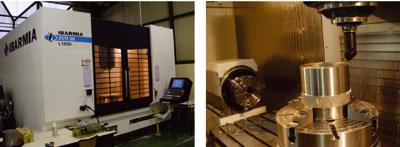
A pesar de que el proceso de mecanizado con refrigerante a alta presión contempla una presión del fluido de corte hasta 350 bar, las pruebas se han realizado a 80 bar por el simple motivo de que esta máquina no permite presiones superiores. No obstante éste es un valor de presión suficiente para obtener los beneficios de esta tecnología según indican los técnicos de Sandvik, así como los resultados obtenidos.
A fin de poder suministrar el fluido de corte a esta presión se ha instalado una bomba Arancia H5032A/80 junto con otros componentes periféricos de seguridad.
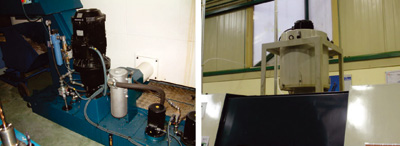
También se ha instalado un equipo de aspiración a fin de realizar una evacuación controlada de las neblinas que se producen durante el mecanizado con refrigerante a alta presión; se trata de otro problema que conlleva la aplicación de esta tecnología.
En cuanto al líquido refrigerante se ha optado por el empleo del Ecoccol MG55 CR de Fuchs emulsionado al 7%. Debido a la tipología y características de esta máquina optaron por utilizar condiciones de corte propias de operaciones de acabado más que de desbaste.
2.3. Herramientas de corte
Como herramientas de corte para las pruebas de mecanizado se ha seleccionado una de operaciones de acabado (CNMG12-04-08-MF2015) para material inoxidable. Las condiciones de la profundidad de pasada ap y avance por vuelta fn las fija el propio fabricante (ap=0,4 mm y fn= 0,2 mm/rev). La velocidad de corte óptima recomendada es de 290 m/min con el cuál la duración de vida estimada es de 15 minutos con un desgaste de 0,3 mm.
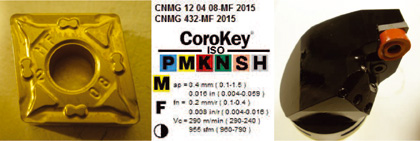
Figura 5. Plaquitas de corte (Sandvik).
3. Pruebas de mecanizado. Resultados obtenidos.
El objetivo principal de las pruebas experimentales consistió en confirmar la teoría de que el refrigerante a alta presión permite aumentar la duración de vida de la herramienta de corte además de aumentar la velocidad de corte y, por consiguiente, la productividad. Las variables de proceso que se controlaron y midieron fueron el desgaste de flanco de la herramienta, la duración de herramienta y el tamaño de viruta.
En las pruebas experimentales el criterio bajo el que se definió el fin de la vida útil de la herramienta fue el desgaste de flanco VB; según la norma ANSI/ASME B94.55M – 1985 cuando un inserto llega a tener este desgaste cumple su vida útil. Las mediciones de desgaste se llevaron a cabo con la máquina de medición de herramientas de arranque de viruta Zoller Genius 3S typeGEN-00152.
Se realizaron pruebas de torneado con presiones de trabajo de 8, 24 y 80 bar (con un caudal de fluido aproximado de 15 l/min en este último caso) y a velocidades de corte de 250, 290, 330 y 360 m/min manteniendo constantes la profundidad de pasada y avance de vuelta.
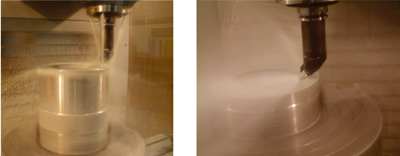
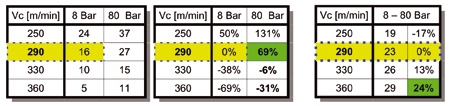
Tabla 2. Resultados de la duración de vida de la herramienta de corte. Tabla 3. Caudal de viruta en cm3/min.
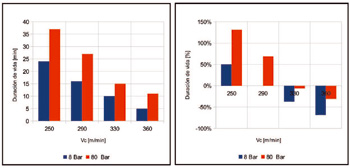
Como se aprecia en las tablas superiores, el hecho de aumentar la presión del líquido refrigerante prolonga la vida útil de la herramienta. Si se toma como referencia la duración de vida para 290 m/min a 8 bar, con el aumento de la presión se incrementa la duración en un 69%. Cuanto mayor es la velocidad de corte, menor es la duración de vida de la herramienta. Por otra parte, el aumento de la duración de vida permite reducir los costes de herramientas y número de paradas de máquina para cambio de plaquita. Asimismo, el aumento de la velocidad de corte permite aumentar proporcionalmente el caudal de material mecanizado.
Por lo tanto, en función del tipo de pieza y proceso de mecanizado que se vaya a desarrollar se puede optar por la mejor estrategia de corte a fin de aumentar la productividad, aumentar la duración de vida de la herramienta y/o reducir el número de cambio de herramientas. Como ejemplo, si lo que interesa es no tener interrupciones de mecanizado por restricciones de la pieza, interesa reducir la velocidad de corte a 250 m/min a alta presión.
También se observa que para las condiciones de corte de 290 m/min (velocidad de corte recomendada por el Sandvik) con una presión de 8 bar se obtiene una duración de vida de herramienta de 16 minutos; el fabricante de herramientas prevé un desgaste de 0,3 mm durante un tiempo de mecanizado de 15 minutos.
A continuación se muestran unas figuras de las plaquitas en su estado de fin de vida después de alcanzar los 0,3 mm de desgaste con la velocidad de corte de 290 m/min y 80 bar de presión del refrigerante.
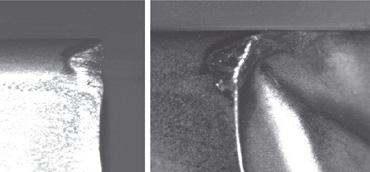
También hay que destacar los beneficios que aporta en cualquier proceso de mecanizado, especialmente en el torneado y taladrado, el hecho de producir una viruta más corta. Por una parte el proceso está más controlado porque la viruta corta resulta mucho más fácil de gestionarla y las interrupciones de máquina generadas por la manipulación y evacuación manual de la viruta son superiores. Por otra parte las propias madejas de virutas que se enmarañan entre la herramienta de corte y la pieza pueden generar defectos superficiales afectando directamente en la calidad de la pieza final.
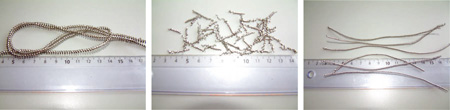
4. Conclusiones
Como conclusión se puede decir que el simple hecho de utilizar líquido refrigerante a una presión de 80 bar, para lo cual la mayoría de los centros de mecanizado están preparados, puede aumentar la duración de vida de las plaquitas de corte más en casi el 70%. Por otra parte el aumento de la velocidad de corte permite incrementar la productividad pero la duración de vida de la herramienta se reduce.
No obstante, la conclusión más importante se centra en el efecto del refrigerante a alta presión en la geometría de la viruta; la alta presión consigue reducir de manera muy importante la longitud de la viruta y por consiguiente facilita enormemente la evacuación de la viruta de la zona de corte al exterior, con todos los beneficios que ello conlleva. Además, los fabricantes de herramientas siguen trabajando en el desarrollo de nuevos productos y soluciones a fin de mejorar aún más las prestaciones del mecanizado a alta presión como pueden ser las nuevas plaquitas específicas para trabajar con alta presión.
El creciente número de máquinas multiproceso ha puesto también de manifiesto las ventajas del torneado con refrigerante a alta presión, especialmente en lo que atañe al control de las virutas, en especial cuando el cambio es automático y las virutas largas amenazan la fiabilidad de una fabricación sin supervisión.
A pesar de tratarse de una tecnología bastante desarrollada por los fabricantes de herramientas de corte y empleada por las empresas más punteras dedicadas especialmente a la fabricación de componentes aeronáuticos, ésta debería de ser transferida a las pymes a fin de mejorar su productividad y por consiguiente su competitividad.
Agradecimientos
Este proyecto ha sido desarrollado en el seno del proyecto Mekapress financiado en el marco del programa Saiotek 2010 con referencia de proyecto SA-2010/00271. También se reconoce la ayuda y aportación de herramientas de corte por parte de Sandvik para la ejecución de estas pruebas experimentales.
Referencias
[1] L. N. López de Lacalle 1, J. Pérez-Bilbatua 1, J. A. Sánchez 1, J. I. Llorente 1, A. Gutiérrez y J. Albóniga Using High Pressure Coolant in the Drilling and Turning of Low Machinability Alloys, Int J Adv Manuf Technol (2000) 16:85–91
[2] E.O. Ezugwu, J. Bonney, Effect of high-pressure coolant supply when machining nickel-base, Inconel 718, alloy with coated carbide tools, Journal of Materials Processing Technology 153–154 (2004) 1045–105