Mayor eficiencia de costes en el torneado de piezas duras
Recientemente, dos fabricantes han logrado optimizar sus procesos de mecanizado de componentes endurecidos un 116 y un 322%, respectivamente, de la noche a la mañana. Estos beneficios no implicaron la sustitución de la maquinaria o la aplicación de nuevos métodos, sino simplemente la sustitución del tipo de plaquita intercambiable utilizada en las operaciones de torneado de sus tornos de CNC. Este cambio permitió triplicar la velocidad de avance anterior. Y, el avance, como todos sabemos, determina el tiempo necesario para realizar un corte en una operación de torneado. Como resultado, se consiguió ahorrar un número considerable de horas de producción (al igual que costes) al año.
“La velocidad de avance es el elemento que realmente nos permitirá optimizar las operaciones, tal y como ilustran estos dos ejemplos de optimización de la productividad” explica Martin Saunders, especialista en aplicaciones de torneado. “Y, lo que es mejor aún, este incremento en la velocidad de avance seguirá proporcionando excelentes acabados superficiales. Por ejemplo, un avance de 0,3 mm/rev genera un acabado superficial inferior a Rz 1 micra y un avance de 0,5 genera uno inferior a Rz 5. Como referencia, con el fin obtener un acabado superficial convencional de una pieza torneada de Rz 6.3, con una plaquita redonda estándar, se requerirían avances un 60 ó 65% inferiores”.
La responsable de estas optimizaciones de la productividad es la plaquita Xcel, una innovación en la tecnología del filo de corte que ha tenido un fuerte efecto en el sector del torneado de piezas duras.
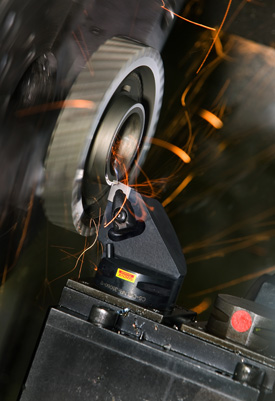
El mecanizado de componentes en su estado endurecido, ya sea templado o cementado, ofrece grandes ventajas a la hora de conseguir una mayor precisión de una forma más eficiente. En esta creciente área de mecanizado, el torneado de piezas duras ha sido objeto de múltiples desarrollos de herramienta. Un obstáculo superado hace ya unos años fue disponer de las máquinas-herramientas adecuadas y, a pesar de que algunos tornos son más indicados que otros para garantizar los estables reglajes necesarios para esta área, la mayoría de los tornos de CNC cumplen los requisitos necesarios.
Torneado de piezas duras
El HPT presenta su propio conjunto de exigencias, ya que las fuerzas de corte y la presión en la herramienta son más extremas. Asimismo, el material endurecido de la pieza es abrasivo, lo que conlleva un mayor desgaste y una mayor generación de calor. Existen, no obstante, materiales de herramienta muy adecuados para esta área, principalmente el nitruro de boro cúbico (CBN), ya que se trata del segundo en dureza después del diamante. En la actualidad, está disponible una gama de excelentes calidades de plaquita con partículas de CBN, como principal componente, para el torneado de piezas duras.
El concepto de la plaquita Xcel ha supuesto un salto generacional de rendimiento en el torneado de piezas duras. Sacha Kotarac, especialista en aplicaciones con experiencia en la asistencia a empresas de ingeniería, deja que el acabado superficial determine su aplicación de la plaquita. “Introduzco la plaquita Xcel lo máximo posible para el torneado en acabado, siempre que las exigencias de acabado superficial sean alcanzables”, dice Sacha, “y también aprovecho la capacidad de la velocidad de avance lo máximo posible para las operaciones de desbaste. Siempre que disponga de la incidencia suficiente al hacer frente a cualquier escuadra, puedo aplicar Xcel con avances hasta 0,5 mm/rev, si dispongo de una estabilidad normal. Estamos hablando de velocidades dos veces superiores a las de las plaquitas Wiper. Además, las plaquitas Xcel y Wiper deben considerarse como complementarias, ya que, a menudo, ofrecen una operación estable con resultados predecibles”.
“Un empresa de fabricación con la que trabajamos estaba planeando sustituir sus afiladoras por tornos para sus operaciones de torneado de piezas duras. En este caso, vimos que la mejor solución era utilizar Xcel para el desbaste, seguida de la plaquita Wiper WG para la operación de acabado. Hicimos unas pruebas en sus máquinas y les presentamos los resultados junto con los tiempos de mecanizado. Como consecuencia, el cliente consideró que compensaba cambiar todos los planos de sus componentes para introducir la incidencia necesaria para beneficiarse de la capacidad de la plaquita Xcel, y nos solicitaron que equipáramos totalmente su máquina. Les recomendamos una velocidad de avance de 0,4 mm/rev para el desbaste con Xcel, generando un acabado superficial de Ra 0.5 micras. Y, para la plaquita WG, la velocidad de avance recomendada fue de 0,33 mm/rev, generando un acabado de Ra 0.42 micras”.
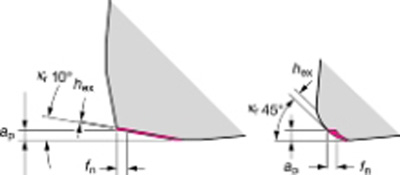
Estabilidad
La estabilidad, por supuesto, es un requisito para garantizar el éxito de todas las aplicaciones con plaquitas de CBN, pero con la plaquita Xcel es incluso más importante. Al utilizar una plaquita Xcel, con el fin de garantizar que se dispone de las condiciones necesarias para el éxito de la operación, la relación longitud-diámetro debe mantenerse inferior a 4-1. Esto no quiere decir que si es superior la operación no será exitosa, pero, si es inferior, se cuenta con las mejores condiciones posibles.
La plaquita redonda estándar genera menores fuerzas de corte, pero la velocidad de avance se ve muy limitada por la relación entre el radio de punta y el acabado superficial. La plaquita Wiper con geometría WH ofrece un buen acabado superficial con un mayor avance, además de unos requisitos de estabilidad relativamente bajos. La plaquita Wiper con la geometría WG ofrece un acabado superficial incluso mayor a una velocidad de avance también superior, pero requiere una mayor estabilidad. Cuando existe la posibilidad de utilizar la plaquita Xcel, su rendimiento es inigualable, ya que ofrece un gran acabado superficial a altas velocidades de avance, pero requiere estabilidad. Incluso a bajas velocidades de avance, Xcel generará un muy buen acabado superficial. La relación entre la velocidad de avance y el acabado superficial siempre es un parámetro clave cuando buscamos minimizar los tiempos de corte.
Al disponer de un ángulo de posición reducido, de 10°, la profundidad de corte es limitada, pero, en el HTP, es limitada de todos modos. Con las plaquitas redondas convencionales, el grosor de la viruta varía a lo largo del filo, pero, con Xcel, se crea una viruta uniforme y delgada que ofrece la capacidad de aplicar mayores velocidades de avance. Un elemento fundamental de la innovación en el concepto Xcel es la manera en que la parte recta del filo se funde con la geometría Wiper especialmente desarrollada, la cual forma la transición hacia la incidencia posterior del filo.
La profundidad de corte se ve determinada por el filo recto pero, por lo general, es lo suficientemente amplia para la operación de torneado; la cual a menudo requiere una tolerancia de trabajo ligeramente superior a la del rectificado. La capacidad de la plaquita se aprovecha al máximo cuando se pueden aplicar operaciones de una pasada, utilizando todo el filo con la capacidad de profundidad de corte y el avance máximo que el límite de acabado superficial permita. Para las operaciones de semi-acabado, la estabilidad es a veces el factor restrictivo.
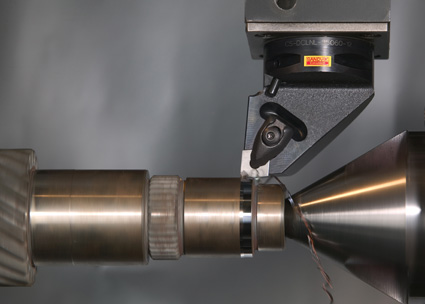
Vida útil de la herramienta
La vida útil también se ve optimizada con el concepto de plaquita Xcel. Con una plaquita redonda estándar, el desgaste es mayor en la profundidad de corte del filo; lo cual limita considerablemente su duración. En la plaquita Xcel, el desgaste se distribuye uniformemente a lo largo del filo. La optimización con Xcel se debe, en parte, a que el tiempo de contacto reducido durante el corte genera menores temperaturas y éstas se distribuyen a lo largo de un filo recto más extenso. Como consecuencia, con Xcel, se pueden mecanizar más piezas, incluso con avances muy elevados.
Las plaquitas Xcel están disponibles en dos calidades basadas en CBN. Éste es un material de herramienta de elevada dureza en caliente y por consiguiente con una gran resistencia a la deformación plástica; lo cual permite que la plaquita sea sometida a altas combinaciones de avance y velocidad de corte en materiales endurecidos. Las calidades de hoy en día también son muy tenaces, robustas y resistentes a los choques térmicos. Las calidades actuales disponen de entre un 40% y un 65% de CBN, con un aglomerante cerámico que añade la resistencia al desgaste químico necesaria para las altas temperaturas. Asimismo, ofrecen una resistencia mecánica que garantiza una buena resistencia al desgaste por abrasión. Además, existen calidades de mayor contenido de CBN con aglomerantes metálicos para una mayor tenacidad.
Cortes continuos o interrumpidos
Los cortes continuos o interrumpidos suponen diferentes exigencias para las herramientas de corte. Para optimizar las operaciones de torneado de piezas duras, es importante aplicar las calidades más apropiadas. Para el torneado en acabado con cortes continuos, especialmente en piezas templadas, que requiere una buena resistencia al desgaste, la calidad CB7015 ofrece una muy buena combinación de altas velocidades de arranque de metal y duración. Ésta se basa en un tamaño de grano fino en un aglomerante cerámico especialmente desarrollado que permite que el desgaste se desarrolle lentamente, de manera controlada, a lo largo del filo de la plaquita Xcel. Los cortes continuos, con o sin intermitencia ligera, son ideales para esta calidad.
Cuando los cortes intermitentes predominan y son más pesados, la mejor elección es una calidad más tenaz como la CB7025. Esta calidad genera buenos acabados superficiales cuando la superficie no es lisa (como en las ruedas de engranajes o en las ranuras de ejes) y cuando el reglaje no es totalmente estable. Ésta también es una calidad moderna de grano fino de CBN en un aglomerante cerámico desarrollado para ofrecer la resistencia necesaria para soportar este tipo de exigencias.
Datos sobre Xcel
Las velocidades de avance de Xcel idealmente se encuentran entre la gama de 0,3 a 0,5 mm/rev. La profundidad de corte máxima recomendada con una plaquita Xcel es de 0,25 mm. Se deben tomar precauciones al mecanizar escuadras con plaquitas CNGX debido a la forma de la misma: manteniendo un mínimo de 2,7 mm, a menos que exista un rebaje. Si bien es cierto que se pueden alcanzar velocidades de corte hasta 300 m/min, se recomiendan, generalmente, velocidades entre 150 y 200 m/min, si la velocidad de avance tiene como objetivo principal conseguir una gran velocidad de mecanizado y la velocidad de corte tiene como fin optimizar la productividad.
Los componentes ideales son engranajes, manguitos y ejes de gran diámetro que requieren operaciones de torneado longitudinal y refrentado y que disponen de una buena estabilidad. Los materiales son típicamente aceros cementados o templados que pueden incluir 16MnCr5, por encima de 60 HRc, o 17CrNiMo6. En concreto, en las ruedas de engranaje se aplica un mecanizado de duro a blando, donde el material puede ser de 62 HRc en el diámetro exterior y descender a 30 HRc en el centro. El CBN no está recomendada para durezas inferiores a 45 HRc pero, con una calidad y aplicación adecuada, se puede trabajar con una combinación de CBN y de metal duro.
Los cortes pueden ser continuos o intermitentes, como en los dientes de un engranaje o las características de un eje, y la mejor manera de optimizar esto cortes es a través de la elección de la calidad de la plaquita. La calidad superficial es generalmente de Rz 1 o Ra 0.25 micras con tolerancias dimensionales dentro de 0,01 mm. Además, se puede conseguir un buen acabado superficial con grandes avances: 0,3 mm/rev ofrece un acabado de Ra 0.3 micras; 0,4 mm/rev ofrece un acabado de Ra 0.5; y un avance de 0.5 mm/rev ofrece uno de Ra 0.8. Asimismo, en lo referente a la capacidad de semi-desbaste, Xcel alcanzará velocidades de mecanizado inigualables.
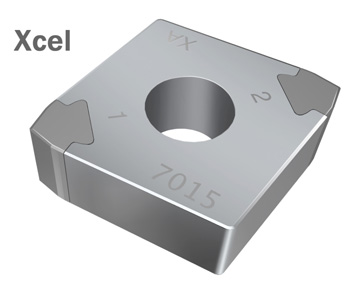