El nuevo sistema Flex Finishing de ABB revoluciona el sector de la robótica
Durante mucho tiempo ha sido difícil para los ingenieros de aplicaciones robóticas lograr un movimiento rápido y mantener al mismo tiempo la estabilidad del contacto con
la pieza. Desde hace varios años, ABB ha destacado en este campo desarrollando robots que pudieran llevar a cabo tareas de montaje delicadas en la industria de automoción. Este progreso ha sido posible gracias a la utilización de sensores que miden la fuerza
de contacto y de bucles de realimentación que controlan la fuerza y la adaptan al movimiento del brazo del robot. Con estos robots de fuerza controlada trabajando con el controlador de robots S4Cplus, el tiempo de montaje de grupos propulsores se pudo
reducir hasta en un 75 por ciento. Recientemente, se ha logrado dar un paso más en el uso de robots de fuerza controlada en una clase más compleja de aplicaciones: rectificado, desbarbado y pulimentado de unidades fabricadas, por ejemplo, en un taller de fundición. A diferencia del montaje de piezas, el control de las fuerzas del proceso en estas aplicaciones es mucho más exigente, y hasta ahora no era posible conseguirlo. Existen varias razones para esa mayor complejidad: el desgaste de las herramientas, las dimensiones variables de las piezas y la falta de una precisión total y repetible de los soportes, con el riesgo de grandes desviaciones de la posición y resultados irregulares. Tradicionalmente, el proceso de acabado ha precisado mucha mano de obra, y la calidad del producto terminado no ha concordado con el rectificado, desbarbado y pulimentado manual. Hasta ahora, la posición de los robots utilizados para esta tarea se controlaba con herramientas y soportes adaptables, de acuerdo con trayectorias y velocidades definidas, ayudados a veces por un servomotor extra a fin de ajustar las variaciones en las dimensiones. En este modo de operación, si el robot no puede alcanzar la trayectoria fijada porque la pieza no está colocada correctamente, seguirá tratando de cortar a través de ella. En consecuencia, el robot se para, la herramienta se rompe o la pieza se estropea. Para limitar esos daños, los robots clásicos de limpieza de piezas de fundición funcionan a un ritmo más lento con una productividad limitada. Debido a la necesidad del control de posición, estos robots deben estar programados para ajustarse a una alta precisión en la trayectoria, un esfuerzo que exige mucho tiempo al ingeniero. Todos estos inconvenientes estaban frenando la expansión de las aplicaciones de los robots en esta industria.
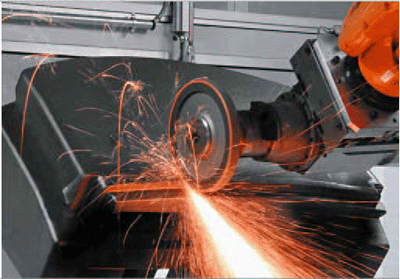
Pasos hacia una innovación sustancial
La nueva y exclusiva aplicación robótica lanzada por ABB en 2007 combina cinco elementos innovadores: empleo del último controlador de robots de ABB, el IRC5, con su interfaz de sensores de alta velocidad, un entorno de programación que
permite que el robot encuentre por sí solo la trayectoria óptima, un bucle de realimentación que controla la presión de la herramienta, un bucle de realimentación que ajusta la velocidad de la herramienta y una oferta de producto fácil de usar y preadaptado.
El IRC5 se construye sobre el sistema operativo más avanzado de la industria para control de robots y equipos periféricos. Con el lenguaje Rapid y el sistema operativo para robótica Motion Technology and Communication (tecnología de movimientos y comunicaciones) de ABB, constituye el sistema operativo de controlador más potente existente en la actualidad. IRC5 tiene dos canales Ethernet, uno para la LAN y otro para conexión local, así como dos canales serie para comunicaciones punto a punto con los sensores. El ancho de banda proporcionado por el controlador IRC5 es crítico para las prestaciones globales y el tiempo de reacción del robot con vistas a corregir y ajustar su posición. Para alcanzar la tasa de muestreo adecuada para ajustar el posicionamiento dinámico del robot, el sensor debe estar estrechamente integrado con la electrónica del controlador si se quiere que esta innovadora aplicación arroje buenos resultados. El IRC5, equipado con Motion Technology MultiMove de ABB, es una referencia mundial que permite el control simultáneo de hasta cuatro robots (36 ejes). Los robots pueden compartir objetos de trabajo comunes, lo que permite configuraciones complejas coordinadas. MultiMove facilita asimismo el cambio dinámico entre movimientos independientes y coordinados. Esta característica única hace posible abordar las tareas complejas de rectificar, desbarbar y pulimentar. El entorno de programación que apoya al usuario de esta aplicación innovadora es el primero en ofrecer esta nueva dimensión de programación. Permite una programación sencilla y eficaz al utilizar el propio sensor de fuerza para definir la trayectoria del movimiento del robot. La programación se gestiona desde el FlexPendant y desde un módulo exclusivo de la aplicación para crear el programa para Force Control Machining (mecanización con control de fuerza). El concepto proporciona al operario la posibilidad de mover a mano el robot y enseñarle la trayectoria aproximada. Posteriormente, el robot utilizará automáticamente la información aproximada para seguir la pieza; al tiempo, registrará automáticamente la trayectoria exacta y creará un programa de robot. El bucle de realimentación FC Pressure permite que el robot rectifique, pulimente o pula objetos fundidos manteniendo una presión constante entre la herramienta y la superficie de trabajo. El software FC Pressure está destinado a procesos que requieran una superficie terminada de gran calidad. Permite que el robot ‘sienta’ efectivamente su entorno y siga la superficie de la pieza fundida, cambiando su posición para aplicar una presión constante en la superficie, incluso si no se conoce su posición exacta. Mientras haya un contacto continuo, las rebabas y otros sobrantes se eliminan hasta la misma profundidad.
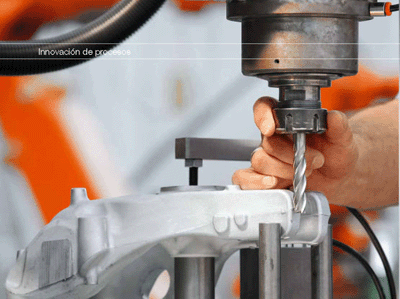
El resultado es un mejor acabado de la superficie, la capacidad de admitir variaciones en la fundición, un riesgo mínimo de daños en la superficie de la fundición y un desgaste previsible de la herramienta. Puesto que la presión se consigue desplazando la trayectoria del robot, esta función se presta especialmente a las operaciones de pulido, rectificado y limpieza cuando la superficie debe ser regular y suave. La segunda característica del software FC SpeedChange permite al robot mecanizar superficies de fundición a velocidad constante e ir más despacio cuando encuentra demasiadas rebabas. En los procesos donde la precisión de la trayectoria es importante y donde el resultado del acabado debe satisfacer unas dimensiones concretas, FC SpeedChange es la elección adecuada. Con FC SpeedChange, se controla la posición del robot y éste sigue una trayectoria programada que conserva una tasa constante de eliminación de material. Trabaja a la máxima velocidad de proceso y ralentiza el robot automáticamente cuando las fuerzas de mecanizado son excesivas, para así minimizar las variaciones dimensionales debidas a las deformaciones del brazo del robot, y para evitar los daños consiguientes en la pieza o en la herramienta a causa del esfuerzo y del calor. Como en el caso de FC Pressure, esto se traduce en una duración menor de los ciclos, en la capacidad para admitir variaciones en las piezas fundidas, en un riesgo mínimo de daño en las piezas y en un desgaste previsible de la herramienta.
El producto final incluye un procesamiento avanzado de la señal del sensor, funciones matemáticas, solución lógica y una interfaz gráfica de usuario orientados a una programación rápida, fácil y precisa en la que se utiliza el sensor para que el operario guíe con la mano al robot con vistas a una programación directa e intuitiva. El producto de ‘enchufar y utilizar’ contiene todos los componentes necesarios, con el sensor, la electrónica y el cableado montados y probados en el robot, y sólo deja al integrador o al cliente el proceso de adaptación.
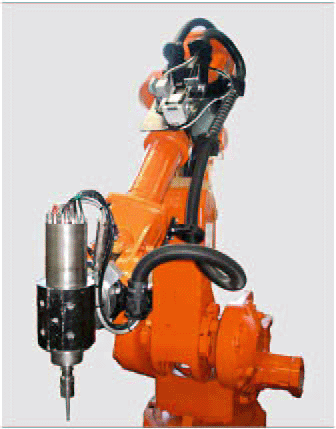
Completar esta tarea compleja y multidisciplinaria ha obligado a combinar el trabajo de investigadores de muchas universidades y de ABB, de ingenieros de ABB y de clientes. ABB y la Universidad Técnica de Lund iniciaron juntos los primeros pasos para definir y aplicar el sensor básico y las funciones de control [2,3]. Desde esta perspectiva, se hizo preciso mejorar el conocimiento de la aplicación y encontrar la interfaz de usuario óptima [4]. La forma de culminar el trabajo con éxito estaba clara, y consistía en reunir los recursos globales de ABB con los casos reales para ponerlo a prueba aportados por los socios industriales. John Kuhn, de Rimrock Corporation, que llevó a cabo las pruebas en tiempo real, dijo: “Force Control puede influir en nuestra actividad más que ningún otro producto lanzado por ABB hasta la fecha”. Rimrock Corporation es un proveedor destacado de productos de automatización y servicios de integración en Norteamérica y un socio apreciado de ABB durante mucho tiempo.
Un fuerte tirón en el mercado
Cuando se presentó al público por primera vez RobotWare Machining FC en la Gifa, la mayor feria de fundición del mundo, que se celebra en Düsseldorf, la conmoción entre los clientes fue incontenible. Los clientes comprobaron claramente la mejor calidad del producto y el considerable ahorro en tiempo de ingeniería, que puede llegar ahora al 80 por ciento. Además, la duración del ciclo del robot se reduce en alrededor de un 20 por ciento con el control mejorado, y la vida de las herramientas de mecanización se puede alargar también en un 20 por ciento. Tras el lanzamiento con éxito de la tecnología Force Control para aplicaciones de montaje y mecanización, ABB está interviniendo en nuevas áreas. Una de ellas es la industria aeroespacial, en donde se requieren trabajos de taladrado con robots precisos, fiables y eficaces para conseguir una producción flexible.
Ahora, con RobotWare Machining FC, las operaciones de acabado de productos en las fundiciones son mucho más sencillas y permiten obtener piezas coladas acabadas mejor, más rápidamente y a mejor precio.