Aplicación de las TICs en el sector moldista y matricero
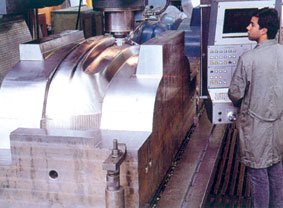
El objetivo último del proyecto era poner a disposición de las empresas del subsector de moldes y matrices herramientas para el desarrollo gráfico avanzado que, aplicadas a la gestión del diseño, consiguiera hacerlas más eficientes y competitivas, gracias a la reducción de las improductividades en la fase de diseño, la mejora de la comunicación entre los clientes y proveedores y la eliminación de las operaciones que no aporten un valor añadido al producto (derivadas de errores en el diseño y acciones repetitivas).
El sector moldista y matricero presenta unos requerimientos específicos de sistemas informáticos para sus aplicaciones, variables en función de la fase del proyecto en la que se esté trabajando, los datos de entrada y los resultados finales que se espera alcanzar.
Además del uso que se debe realizar de los sistemas CAx en el diseño y fabricación de la pieza y del utillaje, para la correcta gestión del proyecto (interna, con los proveedores y los clientes) es necesaria la utilización de herramientas de soporte y herramientas para el intercambio de información, así como el establecimiento de protocolos de comunicación (herramientas PDM, sistemas ERP, herramientas para trabajar en entornos colaborativos, etc.).
Las tecnologías de la información y comunicación en el sector fabricante de utillajes son aplicables en las diferentes fases del ciclo de desarrollo de producto, que incluye el diseño y la fabricación tanto de la pieza como del utillaje.
Fase 1: Valoración de la fabricación de los utillajes
Ya en esta fase previa a la del diseño y fabricación de los utillajes, es conveniente el uso de sistemas informáticos para agilizar las tareas de valoración, permitiendo realizar una oferta mucho más precisa, evitando el sobre/infra dimensionado de los utillajes y, en definitiva, reduciendo los riesgos y costes asociados.
En el caso de que la información se entregue en formato electrónico, es conveniente utilizar un visualizador de CAD que identifique las partes más conflictivas de la pieza (partes negativas, paredes delgadas, agujeros, pliegues…) con la finalidad de ayudar a cotizar el utillaje. Este visualizador debería permitir la importación de diferentes formatos de información o, en su defecto, sería necesario el uso de traductores entre diferentes formatos.
Una de las últimas tendencias que se está llevando a cabo, cuando se desea realizar una cotización para la fabricación de un utillaje de transformación, son las técnicas de fabricación rápida de prototipos estéticos, sin la necesidad de que sean funcionales (técnicas de “rapid prototyping” mucho más económicas), que permitan tener la pieza física en las manos para así poderla visualizar y manipular.
Como resultado de esta primera fase, además de la propia valoración económica y temporal del trabajo a realizar, pueden surgir posibles mejoras del producto para su transformación y reducir los costes asociados.
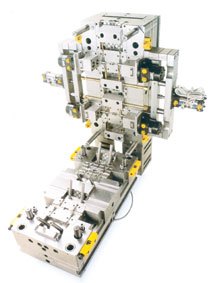
Fase 2: Diseño del utillaje
Con estos datos iniciales, y con la ayuda de los sistemas CAD, se procede al diseño del utillaje. Si los sistemas de CAD no incorporan traductores de diferentes formatos de información, será necesario el uso de traductores externos. Una vez la geometría de la pieza es importada correctamente al sistema CAD, con ayuda del propio programa sería conveniente detectar aquellos elementos que estén normalizados o que estén caracterizados en las bases de datos del sistema, con el objetivo de reducir esfuerzos y tiempo en el diseño de estas partes. Algunos programas avanzados de CAD incorporan librerías específicas para el diseño de moldes y matrices o sistemas basados en el conocimiento (sistemas KBE) que asisten y asesoran en la ejecución de las tareas de diseño.
Como herramienta externa, y de gran soporte en el diseño de los utillajes, encontramos las herramientas de simulación mediante elementos finitos (sistemas CAE). Estos sistemas simulan a partir del diseño de la pieza, de las características del material y de las condiciones de proceso cómo se comportará el material durante el proceso de transformación.
a) En el caso de los análisis reológicos para prever la correcta inyección de una pieza de plástico, estos programas usualmente dividen en diferentes fases el proceso de inyección de termoplásticos y termoestables, llegando a simular desde la entrada de material en la cavidad del molde hasta la extracción de la pieza de éste con sus contracciones y deformaciones correspondientes.
Existe un primer análisis de llenado de la pieza que simula el comportamiento del plástico durante la fase de primera presión o llenado de la cavidad, según unas condiciones de inyección determinadas, considerando un molde ideal a temperatura constante. A partir de los resultados de estos análisis, se puede definir un sistema de inyección optimizado para evitar posibles problemas de inyección como: líneas de unión, retenciones de aire, zonas con sobrecalentamiento de material, piezas cortas, etc.; también se pueden detectar de manera aproximada las zonas críticas de refrigeración en el molde y establecer las condiciones óptimas de inyección, tal y como el tiempo de inyección, temperatura del plástico, temperatura del molde, presión de inyección necesaria, así como la fuerza de cierre necesaria y, por tanto, la máquina a utilizar.
Otro análisis, consecutivo al anterior, es el análisis de compactación. Este análisis consiste en simular la fase de segunda presión del proceso de inyección. Éste permite definir el perfil de compactación donde es especialmente útil, en aquellas piezas que necesiten una compactación muy específica para compensar contracciones y conseguir elevadas precisiones dimensionales.
Una aproximación más rigurosa de los análisis de llenado y compactación anteriores se puede realizar con el análisis de la refrigeración, que considera los circuitos de refrigeración del molde y, por tanto, no utiliza la hipótesis de molde a temperatura constante. Este análisis permite comprobar la eficacia de la refrigeración del molde, y de esta manera, el técnico puede sugerir modificaciones para mejorar las condiciones de enfriamiento y llegar a optimizar el molde y el tiempo de ciclo. De manera aproximada se puede evaluar el ciclo de inyección, incluyendo el tiempo de inyección, compactación y refrigeración.
Los análisis de contracciones y deformaciones a partir de los anteriores son muy útiles para predecir, por un lado, las contracciones que sufrirán las piezas una vez inyectadas y enfriadas y poder hacer las correcciones necesarias en el molde; y por otro, para predecir las deformaciones de las piezas debidas a las tensiones acumuladas durante todo el proceso de inyección. Esto permite variar la geometría de la pieza, el material o las condiciones de inyección, compactación o refrigeración, para minimizar las deformaciones.
Para predecir las tensiones y deformaciones que se producen en una pieza de plástico durante su uso, existe el análisis de tensiones, que permite predecir las tensiones que se crean en la pieza debidas a cargas externas estáticas y lineales, teniendo en cuenta las tensiones internas derivadas del proceso de inyección. Esta simulación es útil, sobre todo cuando se conocen con exactitud las cargas externas a las que será sometida la pieza a la que se ha hecho previamente los análisis hasta deformaciones.
Existe otro tipo de análisis, muy útil para moldes multicavidad que permite hacer el equilibrado de coladas de una manera prácticamente automática. Proporciona las dimensiones de los canales de distribución para que todas las cavidades se llenen de forma idéntica. Las principales ventajas que esto comporta son un idéntico llenado y compactación para cada cavidad del molde, así como unas dimensiones idénticas en todas las piezas.
b) Los programas de simulación del proceso de estampación de chapa metálica permiten simular la deformación de la chapa durante su proceso de transformación. La simulación permite actuar en dos fases bien diferenciadas del proyecto de desarrollo de un utillaje. Por un lado, de forma rápida, a partir del modelo CAD de la pieza, se puede hacer un primer análisis sobre la fabricabilidad y la calidad de la pieza estampada y las características del proceso de transformación asociado. Así mismo, esta primera simulación partiendo de la pieza, también ofrece la posibilidad de obtener un asesoramiento para la definición posterior del diseño de las herramientas de transformación. En una segunda fase, de manera más exacta y partiendo de las geometrías CAD de las herramientas y de unas primeras condiciones de proceso, se puede simular el comportamiento de la chapa durante el proceso de estampación, las interacciones con las herramientas de transformaciones y analizar, de manera más precisa, la calidad final de la pieza estampada y las condiciones de transformación óptimas sin necesidad de fabricar los utillajes.
Una vez el primer diseño del utillaje haya sido valorado con herramientas de simulación, si los resultados han sido óptimos, se puede proceder con el diseño definitivo de los componentes de los utillajes para su posterior fabricación.
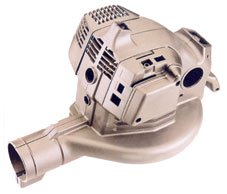
Fase 3: Fabricación de los utillajes
En primer lugar, será necesaria la importación de la geometría en los sistemas de CAM. Para la correcta importación sería conveniente que el propio sistema ya integrase traductores de diferentes formatos de información o, en su defecto, será necesario hacer uso de un traductor externo.
Con el sistema CAM se analizarán las diferentes órdenes y pedidos para establecer las estrategias a utilizar en la fabricación de los componentes del utillaje. Como ayuda en la definición de las estrategias se puede hacer uso de las bases de datos internos de los programas o del asesoramiento de los sistemas de fabricación basados en el conocimiento (sistemas KBM) (incorporan conocimientos de experiencias anteriores).
Una vez definidas las estrategias de fabricación en función de la geometría del utillaje, el material sobre el que se ha de trabajar y las características de las herramientas de trabajo, se puede realizar una simulación en el propio software de CAM que permita prever y evitar posibles errores posteriores e interferencias en las estrategias y operaciones de mecanizado, fresado, torneado, etc. Una vez se ha comprobado que las estrategias son correctas, se procede con la generación del programa de control numérico que permita comandar las trayectorias de las herramientas de la máquina para fabricar los componentes del utillaje.
Fase 4: Validación del molde
Los datos de entrada necesarios para la ejecución de esta tarea son el utillaje físico, o sus componentes, y su geometría en formato digital, en CAD 3D.
Para comprobar que las especificaciones geométricas son las correctas, resulta muy útil el uso de sistemas de inspección CAI, comparadores digitales de información, escáneres, palpadores, digitalizadores… con la finalidad de conseguir información digital del utillaje físico y así poderla comparar con la geometría de los ficheros de CAD y la geometría real del utillaje.
Para poder validar el funcionamiento del utillaje es necesaria la realización de pruebas en prensas. Se ha de realizar una preserie de piezas y comprobar que cada una de las funciones del utillaje funciona correctamente. Como herramienta de validación del correcto funcionamiento del utillaje, es muy aconsejable realizar una homologación de éste en centros especializados antes de entregarlo al cliente.
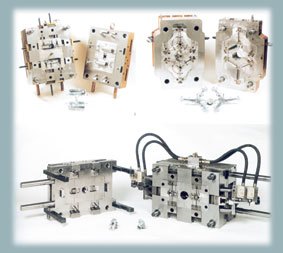
Fase 5: Validación de pieza
Para la validación/homologación de la pieza se comprueba que la pieza obtenida cumpla geométricamente las especificaciones establecidas y la calidad de ésta sea la correcta.
Para la realización de estas tareas, igual que en la validación de la geometría del utillaje, se necesita comparar la geometría de la pieza física con su geometría en formato digital de partida. Para la obtención de la geometría de la pieza se suelen utilizar como herramientas de soporte digitalizadores (con el posterior tratamiento de la nube de puntos obtenida), escáneres, comparadores digitales y herramientas de inspección CAI.
En el siguiente cuadro resumen se puede ver de manera esquemática la participación de las diferentes herramientas TIC en las fases de diseño, fabricación y validación de los utillajes.
En los últimos años los sistemas CAx han evolucionado de forma considerable, incorporando nuevas funciones que los hacen más potentes, flexibles y más fáciles de manejar. El entorno gráfico ha mejorado, tanto en la manera de trabajar mediante menús desplegables en ventanas, como en la visualización en 3D y renderizados de los objetos que se están trabajando.
En el futuro, la tendencia es que los nuevos desarrollos en sistemas informáticos estén orientados a la mejora de estos conceptos. Por otro lado, los nuevos avances están dirigidos a añadir nuevos controles que permitan realizar un uso optimizado de las nuevas tecnologías de fabricación en los siguientes aspectos:
- Permitirán reducir los tiempos de cálculo.
- Posibilitar la concurrencia en todas las operaciones con métodos unificados y protocolos estándares de comunicación para el intercambio de información que incorporarán la pericia y el conocimiento para el asesoramiento óptimo en cada momento del proceso de desarrollo del producto.
- Tendencia a incorporar en un mismo sistema informático diferentes aplicaciones CAx, de gestión y planificación del proyecto, que integren diferentes aspectos de la empresa como la gestión comercial, financiera, gestión de entradas, gestión de productos y el control del almacén.