Evaluación in-process de la rugosidad superficial en operaciones de fresado
En los últimos años, los avances en sensorística y computación han permitido un acercamiento a la monitorización y control adaptativo de procesos productivos en base a algoritmos de inteligencia artificial. En este artículo se presenta una plataforma desarrollada por Ascamm Centro Tecnológico que permite hacer evaluación in-process de la rugosidad superficial en operaciones de fresado.
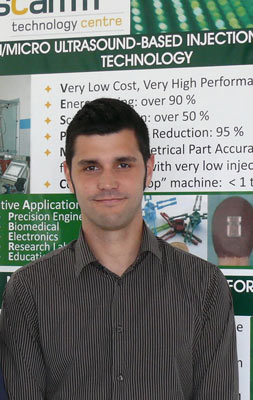
La rugosidad superficial juega un papel importante en el rendimiento y prestaciones de una pieza final, influyendo sobre la precisión dimensional, coeficientes de fricción y desgaste, resistencia térmica y eléctrica, límite a fatiga, resistencia a corrosión, requerimientos de post-procesado, apariencia y coste de fabricación, entre otros [1]. Actualmente, la rugosidad superficial se mide mayoritariamente con rugosímetro una vez el proceso productivo ha terminado y no hay posibilidad de influir sobre la calidad superficial a través del propio mecanizado. Dentro de todos los parámetros que se pueden calcular una vez medido el perfil, la rugosidad superficial media, 'roughness average' (Ra) es el parámetro de evaluación del acabado superficial que más se ha difundido y, en general, aparece en muchos planos de piezas mecánicas.
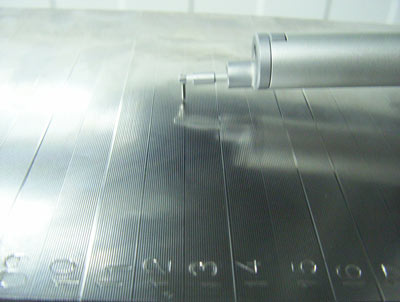
Una vez realizada la medición, para conseguir el acabado deseado en la industria metalmecánica y especialmente en el sector moldista y matricero, la operación de acabado manual de piezas es todavía muy importante. Aunque permite conseguir el acabado superficial deseado, es un proceso que requiere de una cierta habilidad del operario, consume un tiempo no menospreciable y acaba influyendo en la precisión geométrica de la superficie. Se considera que el acabado manual tiene un coste alrededor del 15% del coste total operacional en un proceso general de fabricación de molde [2].
Por este motivo resultaría interesante poder medir o evaluar de forma indirecta la rugosidad superficial durante la misma operación de acabado. Es decir, en el mismo momento que se está produciendo y, de este modo, poder actuar sobre el proceso de mecanizado para garantizar que una vez terminado, el control y verificación de rugosidad se habrá realizado correctamente y la pieza cumplirá con los requisitos de plano.
Sin embargo, no es tarea fácil. Existen muchos parámetros que influyen sobre la generación de superficie y, por extensión, sobre la rugosidad superficial. Algunos investigadores han clasificado estos parámetros en 4 grupos principales considerando [3]:
- Parámetros de mecanizado: avance lineal, profundidad axial y radial de pasada, velocidad de rotación de cabezal, dinámica y cinemática de la máquina, uso de líquidos lubricantes y de refrigeración, etc.
- Características de la herramienta de corte: material, run-out, geometría, radio, etc.
- Características de pieza: propiedades del material, geometría, paredes delgadas, dureza, etc.
- Fenómenos del proceso: variación de las fuerzas de corte, fricción en la zona de corte, formación de viruta, vibraciones, etc.
Todos ellos son parámetros que interactúan a través de relaciones causa-efecto complejas, difíciles de identificar y cuantificar, y que por consiguiente hacen que resulte difícil poder ajustar los parámetros de corte que permitan asegurar la rugosidad superficial de una pieza antes de empezar el proceso. La selección de parámetros de corte depende hoy en día mayoritariamente, en muchos talleres, de la experiencia del operario.
En los últimos años, los avances en sistemas de computación y sensorística han permitido avanzar considerablemente en la comprensión científica y monitorización del proceso de corte y generación de superficie.
En este artículo presentamos un sistema desarrollado por Ascamm [4] para la evaluación indirecta de la rugosidad superficial in-process basado en la monitorización de vibraciones en direcciones X e Y de mecanizado con acelerómetros piezoeléctricos, y el uso de Redes Neuronales Artificiales (RNA) para el cálculo del parámetro de rugosidad Ra. El sistema se aplicó al proceso de fresado con herramientas punta de bola, ya que la influencia de la geometría de herramienta sobre el acabado superficial es más relevante que en el caso de fresas planas, tal y como se puede observar en la figura.
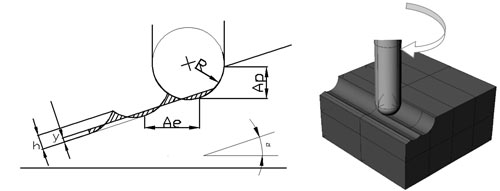
En el siguiente vídeo (http://www.youtube.com/watch?v=v5nJZodMemY) se muestra el funcionamiento de la integración llamada CutOpt. Esta aplicación fue implementada a través de una plataforma que combina Labview y Matlab. Tal y cómo se observa en el vídeo, el operario introduce información del proceso: máquina-herramienta, parámetros de corte, características de herramienta, material a mecanizar y uso de líquidos de lubricación, y el programa, una vez iniciada la mecanización, captura las vibraciones en los ejes X e Y, las filtra para seleccionar únicamente vibraciones producidas durante el arranque efectivo de viruta y generación de superficie; es decir, eliminando desplazamientos rápidos de herramienta sin mecanizado, y la Red Neuronal Artificial, calcula, con estos inputs, de forma indirecta, la rugosidad superficial que se está produciendo y la ofrece en nomenclatura de niveles ISO.
La Red Neuronal Artificial
La Red Neuronal Artificial es un sistema de inteligencia artificial sencillo basado en aprendizaje y cálculo automático a través de un sistema de interconexión de neuronas o unidades simples de computación. Es necesario entrenar la red con experiencias previas para que sea capaz de resolver situaciones desconocidas. De este modo se realizaron un total de 250 experimentos de mecanizado que se utilizaron para entrenar, validar y testear la red. Se diseñaron varias arquitecturas de RNA y finalmente se optó por una configuración típica de dos capas, entrenada con un algoritmo Levenberg-Marquardt de backpropagation, que para el entrenamiento cuando el error de validación de la RNA deja de disminuir asegurando un comportamiento óptimo de la red. Los inputs de la red son los parámetros de proceso, las características de la herramienta, el material, uso de lubricantes y las vibraciones capturadas con acelerómetros piezoeléctricos tal y cómo se puede observar en el vídeo. El único output, el parámetro Ra de rugosidad superficial media.
El coeficiente de correlación de los resultados obtenidos fue muy alto (R=98%) en comparación con otras investigaciones publicadas hasta el momento. Por lo tanto, la calidad de los resultados obtenidos es considerable.
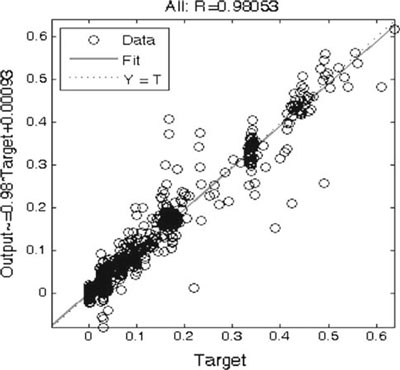
Sin embargo, todavía queda un camino importante a recorrer para conseguir trasladar del laboratorio, a la industria, un sistema de evaluación indirecta de la rugosidad superficial, ya que es difícil desarrollar un sistema universal, integrable sin experimentación previa a todas las configuraciones posibles de proceso: máquina, porta-herramientas, herramienta de corte, material, parámetros de proceso y estrategias, etc. No obstante, es importante mencionar, que los avances constantes en sensorística y computación acercan cada día más este tipo de solución al taller.
El futuro del mecanizado avanza hacia una nueva generación maquinaria inteligente capaz de monitorizar el propio proceso, hacer auto-diagnosis y adaptar automáticamente los parámetros de corte para optimizar el proceso asegurando calidad y maximizando productividad.
Bibliografía
[1] Schulz H. High-speed milling of dies and moulds - cutting conditions and technology. CIRP Annals - Manufacturing Technology 1995;44(1):35-38.
[2] Groover MP, Society of Manufacturing Engineers. Fundamentals of modern manufacturing: materials, processes, and systems. 2nd ed. New York: John Wiley & Sons; 2004.
[3] Benardos PG, Vosniakos G-. Predicting surface roughness in machining: a review. International Journal of Machine Tools and Manufacture, 2003 6;43(8):833-844.
[4] Quintana G, Garcia-Romeu ML, Ciurana J. Surface roughness monitoring application based on artificial neural networks for ball-end milling opera- tions. Journal of Intelligent Manufacturing 2009:1–11.