Caso de éxito Excelencia-Tech
Entrevista IQS School of Engineering (Universitat Ramon Llull) y la implementación de la fabricación aditiva en el currículo docente de la universidad.
Dr. Guillermo Reyes, Dr. Giovanni Gómez, Dr. Marco Antonio Pérez, Ariadna Chueca y Albert Forés, investigadores del Departamento de Ingeniería Industrial
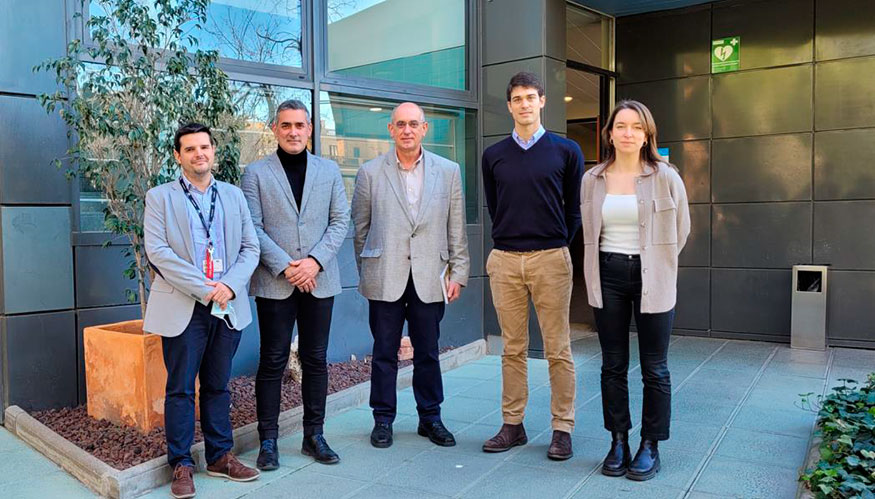
Háblanos sobre el IQS. ¿Qué tipo de investigación desarrolláis? ¿Cuál es vuestro objetivo?
IQS es un centro universitario con más de 115 años de experiencia docente e investigadora. A través de sus dos facultades universitarias imparte estudios de grado, master y doctorado. A través deI School of Engineering en las áreas de Química e Ingeniería Química, Ingeniería Industrial, Biotecnología, Bioingeniería, Farmacia y desde IQS School of Management en las áreas de Administración y Dirección de Empresas, International Business, Marketing, Finanzas y Turismo.
El centro cuenta también con la división IQS Executive Education que ofrece formación especializada a los profesionales y a las empresas y con IQS Tech Transfer através de la cual se realiza investigación, innovación y transferencia de tecnología. Por otra parte, desde IQS TechFactory se impulsa la cultura emprendedora y se da soporte a la creación de nuevas empresas.
Por su tradición científica, IQS es una institución especialmente relevante para empresas del ámbito de la química, la ingeniería química e industrias farmacéuticas. En el año 2000, inició los estudios de Ingeniería Industrial, en 2013 los estudios de Biotecnología y en 2014 los estudios de Farmacia, grado que imparte conjuntamente con Blanquerna otro centro de la Universidad Ramon Llull. El próximo septiembre comenzará a impartir el grado en Ciencias Biomédicas.
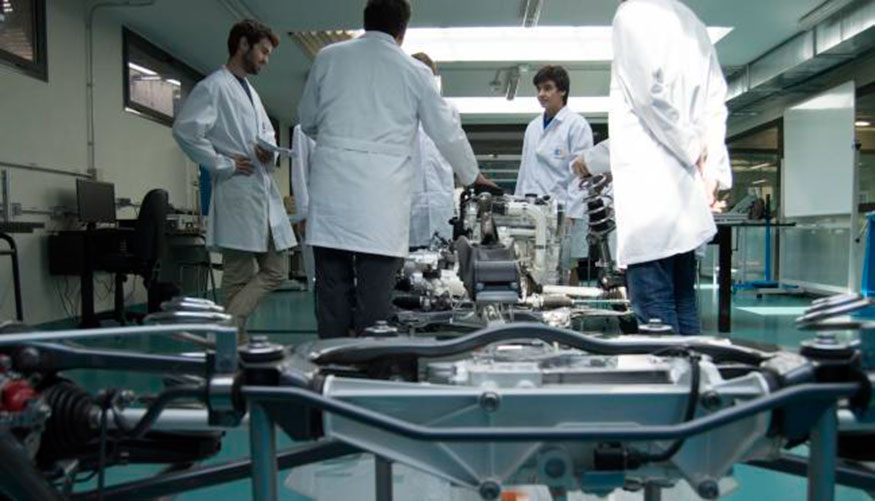
¿Cómo ha evolucionado el departamento de Ingeniería Industrial?
El departamento de Ingeniería Industrial se creó en el año 2000. En el año 2010 el Dr.Guillermo Reyes, en aquel momento director del departamento, y el Dr.Salvador Borrós, director del Grupo de Ingeniería de Materiales, vieron el auge que estaba teniendo la fabricación aditiva y decidieron integrar la impresión 3D en la docencia y la investigación. De esta manera, adquirimos la Fortus 400 de Stratasys, convirtiéndonos en la primera universidad en tener un equipo de estas características.
En 2012 ya no sólo la utilizábamos para la docencia, sino que empezamos a trabajar en líneas de investigación relacionadas con la fabricación aditiva, que han conducido a la realización de tesis doctorales y múltiples publicaciones científicas.
A partir de este momento empezamos a ampliar la familia de tecnologías y de equipos, sobre todo centrado en polímeros, llegando a tener en la actualidad 7 equipos y hasta 4 tecnologías de fabricación aditiva diferentes.
En estos momentos comenzamos dos nuevas líneas de investigación sobre impresión 3D, una con polímero cargado de partículas metálicas, y otra con polímero cargado de fibras de carbono. Ambas investigaciones se desarrollarán en el contexto de dos nuevas tesis doctorales.
En otros departamentos de IQS se trabaja en impresión 3D con otro tipo de aplicaciones. Por ejemplo, en Bioingeniería trabajan en el desarrollo de polímeros y resinas biocompatibles, utilizando un bioplotter (deposición de células). Fruto de la investigación se han llegado a fabricar implantes para tráqueas personalizadas biocompatibles, stents personalizados y otras aplicaciones biomédicas. Otros compañeros están trabajando en la reparación de aneurismas fabricando todos los modelos con impresoras 3D DLP de resina, otro grupo que está trabajando en el drugdelivery (suministro de medicamentos) diseñando microagujas para dispensar la cantidad exacta de medicamento, fabricándolas con la Stratasys Objet 30 Prime gracias a su alta resolución (permite trabajar con tolerancias nanométricas), y también un grupo dedicado a la química analítica trabaja en la impresión de material cerámico.
A través de estas líneas de trabajo tan diversas, cubrimos un amplio espectro de aplicación de las tecnologías de impresión 3D, desde las aplicaciones en el sector químico, pasando por la resistencia de materiales, hasta aplicaciones biomédicas. Dentro de IQS tenemos perfiles investigadores muy distintos, pero nos complementamos muy bien y establecemos muchas sinergias tanto en el ámbito docente como en el de la investigación.
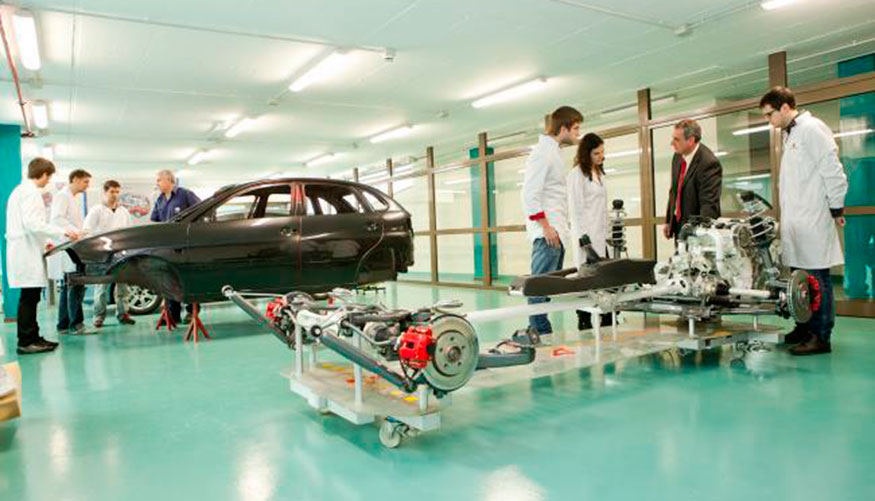
“Sin lugar a dudas, seguiremos invirtiendo en nuevas tecnologías de fabricación aditiva ya que creemos firmemente que es el futuro en la educación de nuestros estudiantes”
-Dr.Giovanni Gómez
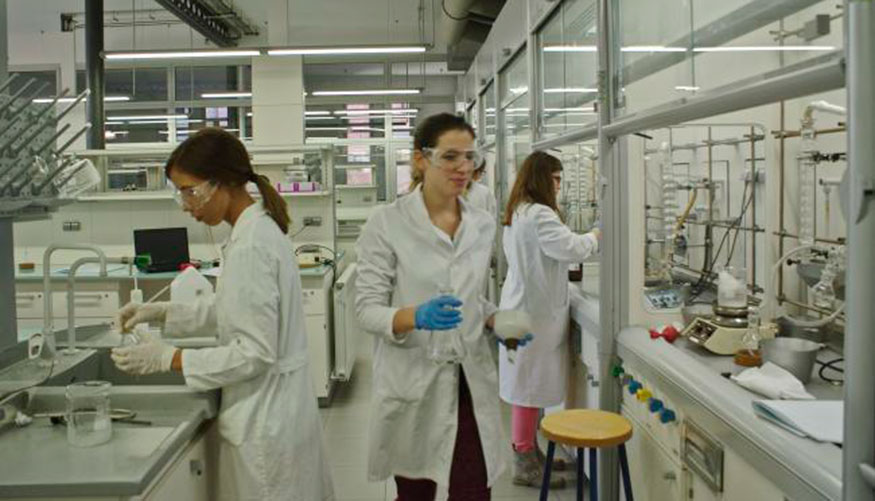
¿Cómo usáis la fabricación aditiva y qué aporta al desarrollo de los alumnos?
A nivel docente es muy atractivo y a que es uno de los pilares de la industria 4.0. Los alumnos tienen siempre mucho interés por todo lo nuevo y se nota una elevada implicación por su parte.
También la fabricación aditiva nos ayuda a construir material docente. En mi caso, por ejemplo, que imparto la asignatura de estructuras y resistencia de materiales, me ayuda a crear geometrías que representen un caso de estudio como una viga de formada y lo llevo a clase. El alumno recibe muy positivamente tener el modelo físicamente. A nivel de investigación y transferencia de tecnología, llevamos a cabo proyectos finales de grado y máster, así como doctorados, con el objetivo de que lo que investiguemos en nuestras instalaciones sea útil a las empresas. Por otro lado, en IQS estamos fomentando el uso del FabLab, donde se encuentran la mayoría de las impresoras que hemos mencionado.
Esto posibilita que los estudiantes puedan utilizar estos recursos en sus propias investigaciones, como podrían ser sus trabajos de final de grado o de máster. Además, otro de nuestros pilares de IQS es el emprendimiento e incubación de empresas, por lo que le damos acceso a los interesados para que puedan imprimir sus prototipos, y desarrollar sus diseños hasta la fase previa de lanzamiento al mercado.
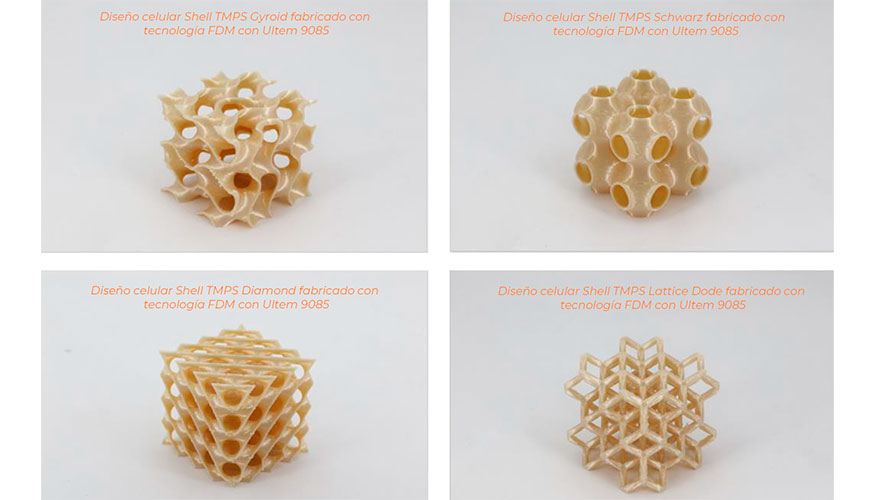
Como alumn@s, ¿qué os aporta que la universidad tenga en sus instalaciones maquinaria de fabricación aditiva?
Albert (doctorado): En ingeniería industrial tenemos una asignatura de fabricación en la que nos enseñan diferentes métodos. La primera parte de esa asignatura es el mecanizado clásico (torno y fresadora) y la segunda la impresión 3D. Ves un cambio enorme a la hora de diseñar pensando en retirar de viruta y cómo puedes cambiar la forma para repensar las opciones de diseño aprovechando al máximo la tecnología 3D.Y esto es lo más interesante, poder trabajar y entender cómo funciona la fabricación aditiva versus el enfoque clásico de fabricación.
Dr.Reyes (profesor): Cuando hace 15 años todavía nadie hablaba de la impresión 3D, nosotros le dedicamos un capítulo para que todos los alumnos que pasaran por la Universidad salieran conociendo las posibilidades de estas tecnologías; qué ventajas tiene, cómo se utiliza, sus limitaciones, diferentes sistemas y cuándo utilizarla. La intención es que cada graduado de IQS salga sabiendo que existe la fabricación aditiva, que es una alternativa y que no es solamente para hacer divertimentos de plástico.
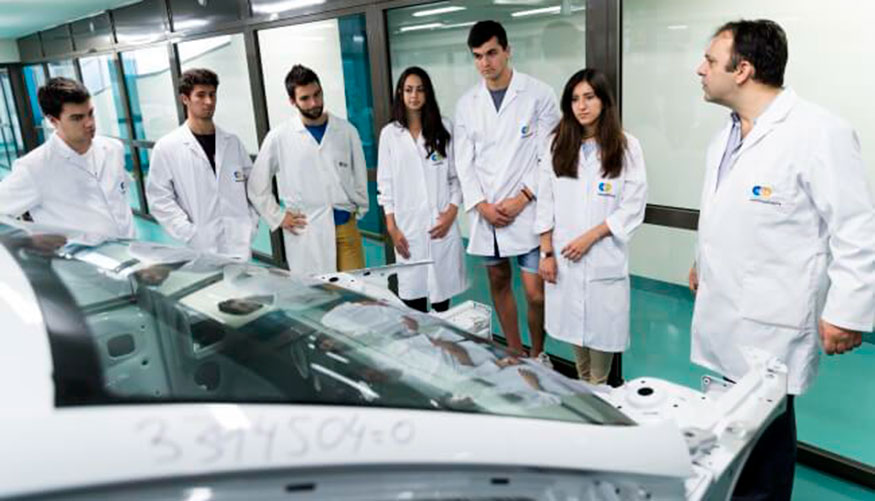
¿Y a nivel interno, utilizáis las impresoras?
Muchísimo. Aplicaciones a nivel interno tenemos decenas y el ahorro en costes se nota muchísimo. Por ejemplo, fabricamos piezas para soportar viales en un agitador o en un equipo de ultrasonidos. Estas piezas, debido a que provienen de la industria farmacéutica, son muy caras. Son piezas que habitualmente se fabrican mediante moldes de inyección de plástico, y el hecho de poder imprimir las reduce este coste unas diez veces.
Desde el punto de vista de funcionalidad, le hemos buscado infinidad de aplicaciones: Muchísimos utillajes internos, incluso recambios de máquinas que están en desuso, o son antiguas y que no encuentras recambios fácilmente. Diseñamos la pieza en CAD, ajustamos las tolerancias y la imprimimos. Y eso es un ahorro en tiempo y dinero.