The mechanised in dry avoids ecological problems and reduces the costs of the process, with greater speeds of cutting and greater length of the tools
Sustainable manufacture. Lubricación By minimum quantities (MQL)
If we split of a generic definition of engineering of manufacture —“Science whose object is the knowledge, application and development of optimum processes for forming of goods of team and consumption, according to specifications of design, basing in the use of productive factors and taking into account the ends of the individual, company and society”—, the origin of the commitment to the sustainability finds perfectly situated, this yes, it is necessary to have clear the ends of the individual, the company and the society.
Is important that the industry answer to the previously posed challenge, as his contribution to the development of the society is key. The industries that decide to form part of a sustainable development have a first point of support in the Industrial Ecology (EI): “economic and physical Structure accompanied of an attitude of the agents involved in the industrial society, that look for a balance sustained with the biosphere by means of the reduction of the consumption of raw materials, power of the industrial processes and waste, so that the biosphere can replace them and assimilate them”.
If we centre us in the processes of manufacture based in start of material and try to apply strategies that comport a commitment with the sustainability, have a first opportunity to optimise the strategy of production in the employment of a technology of alternative production and the reduction of waste related with the utilisation of the liquids refrigerantes. This strategy will allow us diminish the economic and ecological costs of the refrigerantes employed in the machines-tool as well as diminish the dangerous waste for the environingingment, the illnesses of the leather and the respiratory problems.
What would occur if the legislators and the associations of insurance of labour accidents approved laws and regulations more strict in reply to the risks that suppose the liquids refrigerantes? As that the companies would have a greater responsibility and new obligations regarding the personnel, in addition to some greater financial costs.
Exists some strategy of production that avoid the economic and ecological problems that comports the mechanised with refrigerantes? Yes, the mechanised in dry avoids ecological problems in addition to reducing the costs of the process, without forgetting, that can obtain greater speeds of cutting and greater length of the tools, causing an increase of the productivity.
Sustainable manufacture
If we engage us with the environingingmental improvement of a product, the optimisation of the technicians of production can achieve the sustainable balance that look for. The sustainable manufacture has to pose like “an optimum process that minimises the scraps and the pollution caused during the forming of the product and under specifications of ecodiseño”.
This optimisation of the process is not regulated by a norm and is especially a philosophical approach to be followed. If it analyses the strategy that at present follows any company of any industrial state, observes how in some cases, follow realising investments, for example, in machines-tools that follow generating waste contaminantes, still existing in the mercando alternative technologies that reduce to the minimum said waste. These companies have not valued his possible performance under criteria of sustainable development: Where it finishes the responsibility of the company that manufactures a product without diminishing the impact of waste?, which is the acceptable level of toxic broadcast?, which coefficient of participation have assumed these companies in front of the new challenge?
In the current industrial panorama find us with companies that use systems of manufacture whose main aim to be competitive is the one to obtain products in a minimum time, to a suitable cost and with an optimum quality.
The technicians and engineers of manufacture involved in these systems of manufacture have to establish a strategy based in references and proposals related with the production and of direct implantation in the politics of gestión of a factory:
- Decrease of the consumption of power and consumption of clean power: apply renewable energies, use conventional energies of low environingingmental impact, install equipment of high energetic performance, recover the residual heat.
- Reduction of resources: install equipment of control of consumption of resources, recircular flows, recover the effluents like by-products, recycle the excess materials for other processes, increase processes of inspection in the purchase of materials, purchase quantities (minimum) adapted of materials, control of inventories, automatic dosage of ideal quantities.
- Reduction of stages of manufacture: improves of methods and time, reduce stages of the superficial treatments, simplify the type of materials used, simplify the number of components, secuenciar the operations of production to minimise his broadcasts.
- Reduction of broadcasts: segregar the types of broadcasts according to degree of impact and ease of recycled, improve the gestión of the flows contaminantes, install equipment to reduce broadcasts, reutilizar by-products of the internal process or externamente, improve the systems of storage to reduce the impact, use cleaning products less toxic and dangerous, recycle intern and externamente.
- Improve of maintenance: rediseñar the plant to facilitate the maintenance, schedule sequences of load to reduce the material of cleaning, inspect and realise operations of periodic cleaning, improve the gestión of the warehouse for caducity of products, good gestión of the operations of the system of production, increase the control of broadcasts, install equipment of process for an alone product to improve his gestión and saving of materials of cleaning.
Regarding the environingingmental gestión in the surroundings of manufacture, if we wish that our factory contribute to the balance sustained, is necessary that the gestión have very clear some aims and environingingmental commitments, of coordination and control of the industrial activities.
The Systems of Environingingmental Gestión (SGMA) are a point of key support to fix the structure of the model of sustainable gestión of our factory, since we will have to pipe, check, verify and ensure us that the processes fulfil with the applicable norms and the corporate strategy.
The administration, the law and the citizens demand a strict fulfillment of environingingmental requests and therefore, a SGMA is a necessary tool to structure and document this commitment. The norm JOINS-IN-ISO 14001 remembers us what is a SGMA: “Part of the system of gestión that includes the organisational structure, the planning of activities, the responsibilities, the practices, the procedures, the processes and the resources to develop, implant, carry to effect, review and keep up to date the environingingmental politics”.
Exist two normative models for the implantation of a SGMA:
- Norms ISO 14000.
- Regulation CE number 761/2001 (EMAS).
Both models allow to the companies the development of a system of environingingmental gestión and his integration with the rest of bus systemsiness gestión, and like this can fulfil with the environingingmental commitment demanded.
For a company that produce goods of team and consumption, speak directly of the concept of ‘clean production' can simplify him the approach that engloba the sustainable manufacture and the environingingmental gestión since it centres in the effective execution of the productive processes so that it generate the minimum value of by-products or waste no aprovechables internally with the minimum consumption of raw materials and for this supports in three fields of performance:
- Select processes that minimise the production of waste and the environingingmental impact in the surroundings.
- Minimise and reduce the processes that generate waste and excessive consumption of raw materials.
- Valorizar Internally the generation of waste like alternative prime matter and like this mitigate the environingingmental impact and the cost of the waste generated.
Ecological and economic application of the fluids of cutting
In the processes of conformed by elimination of material is necessary to control the following factors: elastic deformation of the material in his process of break, strengths of compressesion and of friction between surfaces, high temperatures and chemical wear by the contact with the oxygen. The control of these factors allows to keep between limits the life of the tool and achieve the tolerances with stability.
The fluid of cut counters these factors by means of the refrigeration and lubricación of the surroundings piece-tool and the evacuation of the excess material (figure 1). His utilisation causes a high cost of maintenance and elimination, in addition to a problem in base to the current criteria of Sustainable Manufacture. Likewise, to the economic factor adds the strong environingingmental impact that cause this waste, as well as the possible development of illnesses of the workers that are in permanent contact with the fluids during a prolonged time.
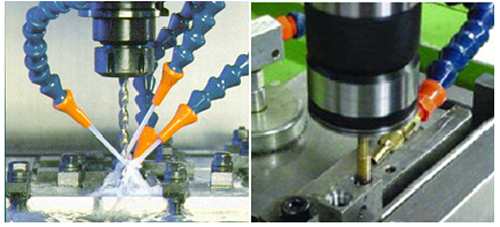
In front of these exigencias, and in base to the experience accumulated in the mechanised of different materials and operations of cut, the first that pose us is to give the jump to the mechanised in dry or with minimum quantities of refigerante.
The mechanised in dry of components of steel and smelting with operations of turning and milling, at present has an efficient answer with the tools of cut of hard metal recubierto given his high resistance to the thermal sensors wear.
Instead, in operations of taladrado, mandrinado and threaded of steels and alloys of aluminium, without forgetting the by cut with saw, the lubricación by minimum quantities (MQL- Minimum Quantity of Lubricant) keeps on being key to obtain a commitment between the efficiency of the operation and the economic application of the fluid of cutting.
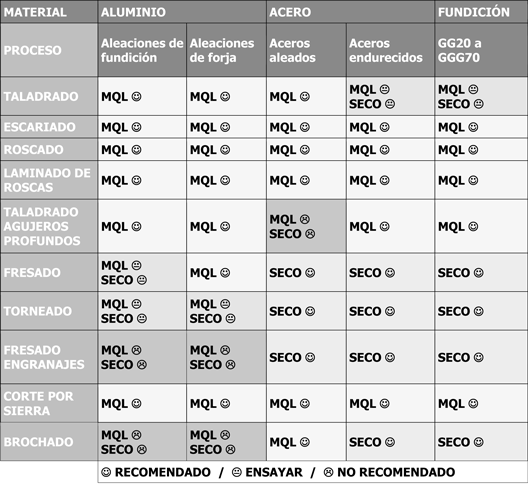
Table 1. Areas of application.
To realise a gradual adaptation to the mechanised based in a system MQL, is recommended to initiate, although it was of experimental form, the conversion in parallel and in the same machine of some operations where employ refrigerantes to solutions of mechanised in dry. Besides, the installation of a system of lubricación by minimum quantities based in the feeding of aerosol in an alone pipe, is very easy and does not require hardly maintenance. In the table 1, show the areas of application of the mechanised in dry and of the MQL.
1. Mechanised in dry
The mechanised in dry supposes the complete elimination of the fluid of cutting. So that when it realises a process of this type, have to adopt measures so that the functions that usually exerts the fluid are assumed by other means.
To implant it requires realise a deep analysis of condition them limits of the operation jointly with the knowledge detailed of the complex interactions associated to the process, between the tool of cut, the piece to mechanise and the machine tool. On this base, can identify and adopt measures and solutions to attain implement the mechanised in dry.
The factors to which awards them greater influence in the wear of the tool are the adhesion and the abrasion for speeds of low cutting and the diffusion and the oxidation to high speeds and high temperatures of cutting. In consequence, the material of the tool has to present low tendency to the adhesion with the material of the piece as well as high hardness and resistance to the wear to high temperature.
The materials of tools at present available, answer of uneven form to the mentioned characteristic. The tools recubiertas are example of materials that allow that the mechanised in dry extend to areas in which the lubricantes consider at present like essential. The advances in the field of the materials of cutting and the coatings will contribute firmly to the reduction of the fluids of cutting.
2. Lubricación By minimum quantities, MQL
The lubricación by minimum quantities (MQL- Minimum Quantity of Lubricant), substitutes the use of the refrigeration-lubricación conventional by means of fluids of cut, by the supply in the points of friction of a very small quantity of lubricante (0.5-50 ml/h) in shape of aerosol with micropartículas of oil suspended in him. His application during the process of cutting does not generate any residue on the piece and the tool.
The equipment MQL base in a tank of lubricante, one or several units of regulation of mix and pipes of lubricante with filters of rociado.
The air compressesed goes in the tank presurizado of the lubricante where has generated an aerosol with a size homogéneo of the particles of oil of < 0,5 µm, what allows the transport of the aerosol to long distances (20 metres) if separation of the mix and without that forms any mist. This transport can realise so much in machining centres of high speed as in machines with change of tools by turret milling machines (figure 2).
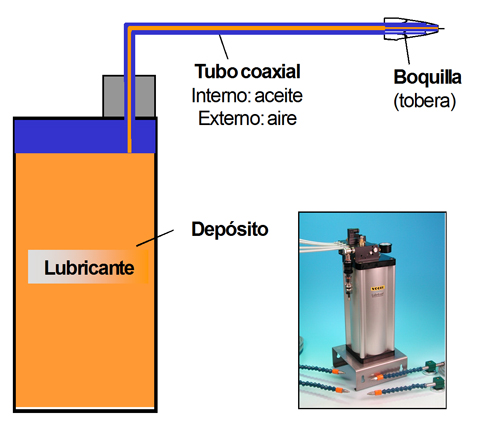
The regulation of the quantities required of lubricante and air of atomisation, as well as the adjust of the internal pressesure of the tank of lubricante realise manually by means of valves of control mounted in the tank of the lubricante.
The manufacturers of systems MQL, have of a range of digital equipment that allow individualizar the quantity and composition of the aerosol required for each tool through the team of CN by means of orders M or H.
Regarding the supply can realise of external form or intern (figure 3):
- Lubricación external by minimum quantities. The necessary aerosol in the point of the process generates to the exit of the filter. It observe in the figure 2, that the lubricante and the air of atomisation feed through coaxial lines until the filter of rociado that operates like effect venturi. An inner tube supplies a minimum quantity of lubricante, whereas another external tube surrounds to this chorro with air and expels it to the tool. The concentric flow of oil and air that results of this design avoids that the chorro of rociado expand and contaminate the surroundings with the excess aerosol. The lubricación external uses mainly in operations of cut of material by saw, milling of slots and operations of turning. In the case of the operations of mechanised, like taladrado and escariado, the external supply is adapted only in when it fulfils the relation length/diameter, L/D < 3. When the relation L/D is greater, the tool has to retreat several times so that the hole can be dampened again, causing an increase of the time of mechanised. The external supply can present problems when it mechanises with multiple tools where the lengths and diameters vary considerably. The orientation of the nozzle of supply has to adjust manually depending on the length and the diameter of the tool.When the tools involved in the operation do not have channels of internal refrigeration the external supply is the only solution.
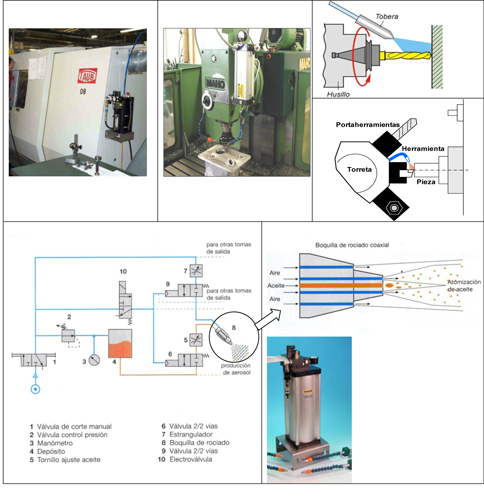
- Lubricación Internal by minimum quantities. The aerosol sends until the tool through the husillo and the tool holders (figure 4). In this case it is necessary to loan special attention to the variation of the diameters and route of the pipes. The manufacturers of machines-tool and tools of cut, have to follow a series of recommendations to avoid losses of aerosol and pressesure. Later they comment the ideal conditions of applications. The lubricación internal is ideal in operations of taladrado, threaded and escariado, since independently of the relation L/D, ensures that the aerosol always arrives to the zone of cut in any position of the tool. In the operations of taladrado of deep holes, the relation L/D causes that the MQL was indispensable.
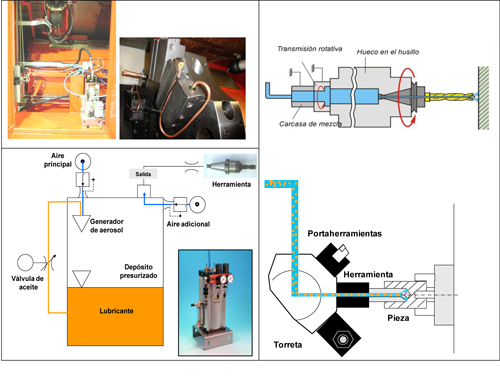
3. Ideal conditions of application
The quantity of lubricante in shape of aerosol is conditioned by the quantity of air and lubricante and by the diameters of the pipes by which transports the aerosol from the team until the filter. To reduce the losses of aerosol and pressesure recommends :
- The pipe of feeding of the aerosol does not have to have strong changes of diameter neither estrangulaciones in shape of diafragma because the lubricante can deposit partially in these points and reduce the availability of the aerosol.
- The length of the pipe of the aerosol has to be the shortest possible, as when increasing the length increase also the losses of pressesure and aerosol. The pipe of the aerosol has to be of the most straight form possible, avoiding especially the ‘acute elbows' that generate the condensation of the aerosol. The deviations have to have a minimum radius of 200 millimetres.
- All the interfaces or points of intersection between the components of the MQL have to be smooth, without holguras or excellent singings, especially, in the zone of transition between the tool and the tool holders (figure 5).
- The diameter of the pipe would have to be from among 2 and 7 millimetres, to be able to transport a quantity of oil in the lower possible time.
- The feeding of the aerosol with husillos or tools giratorias has to realise, in the possible, in axial steering. With the radial feeding, the lubricante, especially with high revolutions, can ‘centrifugarse', that is to say, can produce a partial separation of the components of the mix of aerosol. This occurs especially with tools very small turning to high speeds (figure 6).
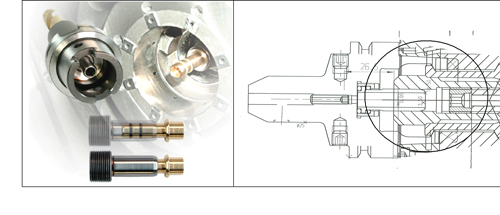

4. Oils employed in MQL
At present employ synthetic oils like alcohols grasos and oils ester (vegetal oils modified chemically). The election depends of the type of supply, the material of the piece, the operation of mechanised and the back operations of finishing (thermal sensors treatment, coating or painting).
The oils ester have a greater effect of lubricación, minor viscosidad, greater rank of ebullición and temperature of inflamabilidad. They evaporate more slowly (see figure 7) that an alcohol graso and generate a fine film of oil on the piece. They use to reduce the friction and the adherencia between the tool of cutting and the shaving. They are adapted for operations of taladrado, mandrinado and threaded in steels and alloys of aluminium. When treating of a fluid based in esters from vegetal origin, is a biodegradable fluid, no toxic, no irritante or harmful.
The alcohols grasos are adapted for operations of cut in which the effect refrigerante is more important that the effect lubricante. His greater evaporation generates surfaces practically dry. They are adapted in the mechanised of grey smelting.
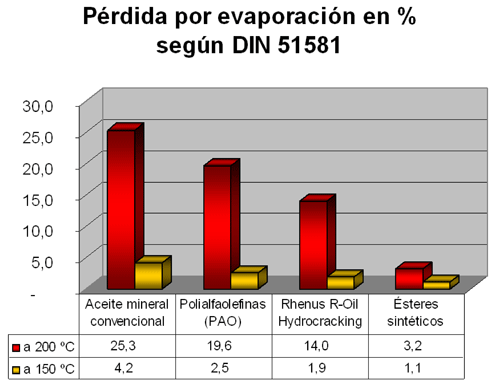
5. Measurement of toxic substances in the air in zone of work
An appearance that concerns to the users of systems MQL, is the possible pollution that can suffer the air of the surroundings, affecting to the conditions of the place of work because of the particles in suspension that can remain after the application of the aerosol.
The essays realised in different laboratories, based in measures along several turns of work, show that the risk of pollution for the operario and his surroundings is minimum, since any measure reaches 25% of the value limit established. Nevertheless, it is necessary to go back to remember that the oils employed in MQL are toxicológica and dermatológicamente safe, and are classified like risk hídrico of class 1 (lubricante of conventional refrigeration: risk hídrico class 2 or 3).
Strategy of introduction and profitability
The ideal conditions to implant properly a system MQL concentrate in the commitment of the company to include in his plan of innovations the technology MQL and formulate put clear with regard to the reduction of costs and environingingmental improvement.
To determine with rapidity and precision the characteristics demanded in the application of MQL, is convenient to take into account the following factors:
- The technician of mechanised, for example tornear, mill, taladrar, etc.
- The application of MQL (external/intern).
- The material to mechanise.
- Type of mechanised: interior, external, continuous or interrupted.
At present, the manufacturers of tools supply tools of ready cutting for the supply MQL in almost all the processes and usual operations of cutting.
Nevertheless, a company that pose the process of implantation of a system MQL, can pose the following basic phases for his execution:
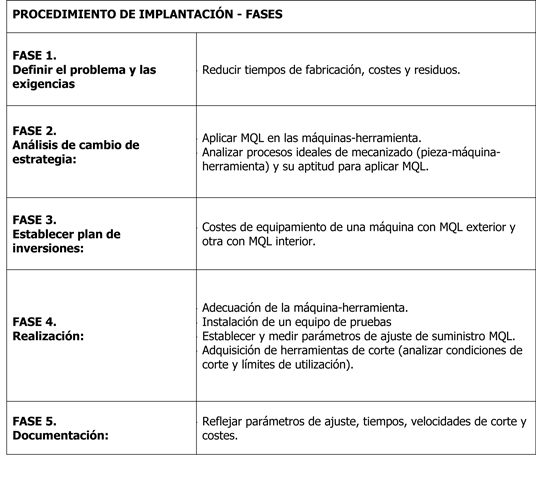
1. Examples of application
Like example of application, show the last experimental proofs realised in the laboratory of essays, where have obtained the following results:
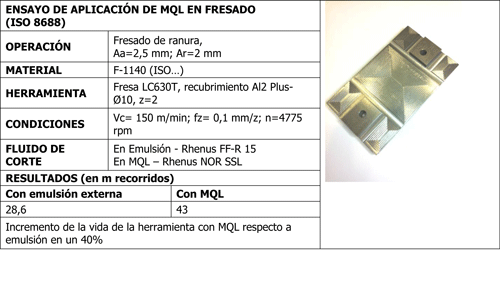
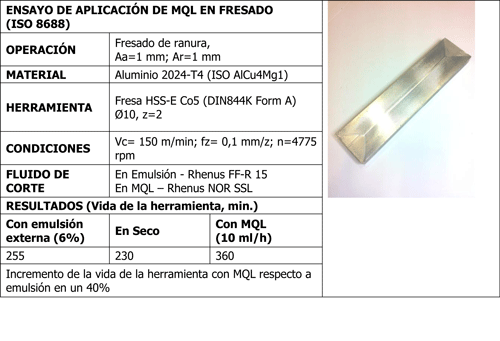
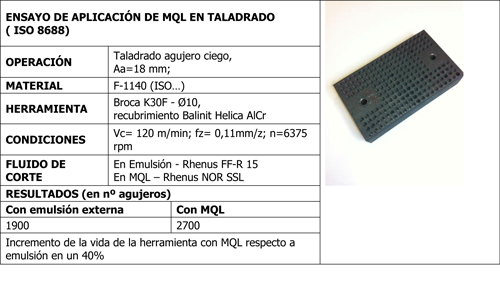
2. Main advantages
The implantation of a system MQL causes the following advantages:
Lower costs
- Supresión of liquid refrigerantes
- Supresión of components for the machines-tool like filters of taladrinas and systems of prefiltración.
- Without costs of waste of shavings and liquid refrigerantes.
- Is not necessary to clean the pieces of work.
- Easy amortización when increasing the length of the tools and mechanise to greater speeds.
Greater productivity
- Significant reduction of time of production (30/50%).
- Greater efficiency of mechanised.
- Useful life tools increases until 300%.
- Can use in multiple process of production.
Use of technological advantages
- Easy integration in new and simple machinery adecuación in existent conventional machines.
- Use in parallel of mechanised in dry and by liquids refrigerantes.
- Initially, does not need any change in the design of the tool holders / husillo.
- Better quality of mechanised when reducing the rozamiento.
Reduction risks for the health.
- Decrease of the cutaneous conditions and of the respiratory tract.
- Greater hygiene of the place of work.
Conclusions
The technicians and engineers of manufacture involved have to pose the commitment that supposes a strategy based in proposals related with criteria of sustainable manufacture, for example: decrease of the consumption of power and consumption of clean power, reduction of resources, reduction of stages of manufacture, reduction of broadcasts and improvements of maintenance.
The companies of manufacture of goods of team and consumption that use processes where employ liquid refrigerantes, can minimise the scraps and the pollution caused by means of the employment of the lubricación by minimum quantities – MQL.
The manufacturers of machines-tool and of tools of cut, have of sufficient essays and experimental data of application of the MQL in a wide group of materials and operations of cut, that show that the MQL is an applicable technology that guarantees lower costs, increase of productivity and technological innovation.
References
- Brundtland, G.H., (1988), Our common future. Alliance Ed., Madrid.
- Well, R., (2009) The sustainable manufacture and unit of innovation. Unit of international innovation of Manufuture. Fatronik-Tecnalia. http://www.manufuture.es
- Capuz Curl, S. Et al, (2002), Ecodiseño. Engineering of the cycle of life for the development of sustainable products. Ed. UPV.
- Corderas, J., (1999), environingingmental Engineering of the company: clean technologies, Ed. Universitat Oberta Of Catalonia, Barcelona.
- Dhar, N. Et al (2006), The influence of minimum quantity of lubrication (MQL) on cutting temperature, chip and dimensional accuracy in turning AISI-1040 steel, Journal of Materials Processing Technology, 171, 93–99.
- Jayal, To.D. Et al, (2010) Sustainable manufacturing: Modeling and optimization challenges at the product, process and system levels, Journal of Manufacturing Science and Technology 2 2010) 144–152.
- OECD, Organization for Economic co-Operation and Development, (2009), Sustainable Manufacturing and Echo-innovation: Framework, Measurement and Industry and policy practices, www.oecd.org/sti/innovation/sustainablemanufacturing.
- Rigola, M., (1988), Production cleaner, Ed. Rubes, Barcelona, 1998.
- Rupérez, J.To. Et al, (2008), Ecodiseño. Social need and Business Opportunity, Foundation Ecology and Development.
- Schacht, M et al. (2004), Lubricación by minimum quantities: MQL, Vogel-SKF. 1-5102-And.
- Shokrani To. Et al. (2012), Environingingmentally conscious machining of difficult to machine materials with regard to cutting fluids, International Journal of Machine Tools and Manufacture, doi:10.1016 / j.ijmachtools 2012.02.00.
- His And., et al, (2007), Refrigerated cooling air cutting of difficult-to-cut materials, International Journal of Machine Tools and Manufacture 47, 927–933.
- Weinert, K et al (2004), Dry Machining and Minimum Quantity Lubrication, Manufacturing Technology, Vol. 53, No. 2., 511-53.