Mechanised on line of boxes for turbines of steam
The première was a rotundo success. To finals of November of 2013 gave the starting signal for the new line of production, that immediately began to produce boxes for new turbines of steam used pair generate electrical power. No longer it does lacking to mechanise these elements in areas of separate production, but all the process takes place in a same chain of production. The machines of milling, lathe giratorio and lathe in carousel with disposal in Or situated in the new plant situated in the port of Mülheim. Through the crane of the ship no only interconnected the flow of materials between the machines, but also the process of creation of value through the control of the production.
“Now, the different machines-tool work in an alone line in the new ship of production that, from principles of year, has gone instrumenting progressively with the necessary machinery, so that with each stage of mechanisation increases the creation of value and go finishing the boxes step by step without need to have to transport them of an area of production to another“, describes the new process Rüdiger Semmler, boss of Production of turbines of steam of Siemens AG, of the Power Sector of Mülheim.
This organisation of the production constitutes a totally new field inside the mechanisation of big components with weights of more than 100 tonnes. In words of Semmler: “When three years ago we begin with the planning, there was a lot of scepticism”, remembers. But, in this time, even the more sceptics have convinced of the tarpaulin of the new idea. This new form of organisation of the production will provide to Siemens savings in the times of transport and storage. “Besides, the different steps of the production also will be able to coordinate better between himself. Like this, it is possible to reduce considerably the times of manufacture and the costs“, explains Semmler, resumiendo the advantages of the new production on line.
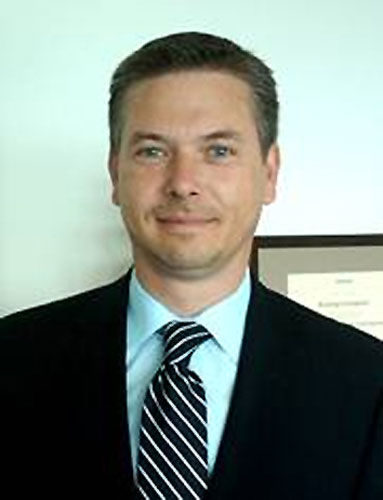
Rüdiger Semmler, boss of Production of turbines of steam of Siemens AG, Power Sector of Mülheim, comments on the new production in chain: “When we begin three years ago, it existed a lot scepticism. But, now, even the more sceptics have convinced of the tarpaulin of the new idea”. Photo: Siemens.
The mechanisation of boxes for turbines is a process of individual manufacture, in which each component is different. “By this reason, have realizar a production based in models”, explains Semmler. All the machines have of a control of Siemens with which the machines-tool integrate in the processes of communication, engineering and production. That is to say, splitting of a model of data 3D, generates information for the manufacturing of the work and automate the programs for the different steps of production; by means of Siemens NX (CAD/CAM), establishes an enclosed chain from the model 3D until the machine.
“Now, the different mechanisations, as those that are necessary for each one of the components, program of form automated, so that our personnel qualified only has to take part in the program in concrete cases “, explains the boss of Production in reference to the advantages of the connection in network. “Likewise, we work with a subjection standardised with positions of exact zero, what serves to facilitate and speed up considerably the start of the mechanisation”.
Thanks to this new poceso of production in chain, the developers of Siemens have optimised the process and, at the same time, also the different steps of the mechanisation. “Now, we save in the processes of work from the moment in that it initiates the process of mechanisation of the boxes on the big fresadora of portico”, comments Semmler. This is possible thanks to a complete mechanisation more perfect, that already was usual in the small and average components, but that had not entered still in the construction of heavy machinery.
The peculiarity of this portico is that the head fresadora is had so that the components can mechanise in the same position in which afterwards they have to work in the plant of generation of the customer. Of this form achieves a greater degree of accuracy in the mechanisation, in the order of hundredth of millimetre, even with big components. These so reduced tolerances are necessary, since inside the turbines of steam produce high pressesures and temperatures. “The surfaces of estanqueidad have to mechanise with this accuracy to avoid exhaust pipes of steam, since it does not exist any material of estanqueidad suitable for upper temperatures to 500 °C”, explains Semmler.
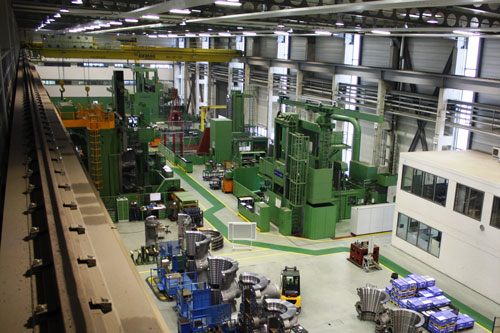
The following step that will carry out Siemens in Mülheim will be the complete mechanisation by means of virutaje, milling and perforación in a same position of fixation, with back control of quality by means of application of procedures of measurement automated and documentation. “When three years ago we ask offers for a destined machine to a new unit of production, did not exist all over the world any manufacturer in conditions to offer a machine tool for the complete mechanisation of components so big and weighed like which manufacture here”, comments Semmler.
“The ideal for us would be an able machine to mechanise components until 100 tonnes of weight. But also we would content us with a capacity of 60 tonnes, because then the spectrum of components would be the sufficiently wide to be able to take out the maximum split of a machine of this type”, says the boss of Production of Siemens. The energetic group already has found companies that work beside Siemens in the development of a machine of this type. Semmler Shows trusted when ascertaining the interest of the manufacturers of machine tool. “Along the spring of the next year will have of the first offers and then will be able to proceed to the construction”, says the boss of Production.
But the big challenge is not only the complete mechanisation, but also the integration of the technology of measurement applied during the process. To accommodate the tolerances and execute controls of quality, in the manufacture of machinery of big size a lot of measurements execute still manually. “Also we want to automate this process, by what are in conversations with a big number of manufacturers of equipment of measurement”, explains Semmler.
To date, the workers still have to access to the interior of the boxes to measure the tolerances. “In the future it will have to be the same machine the one who execute this process, and will have to be able to optimise by himself same”, augura Semmler. As already sucede in the car industry, in the future a safe process of mechanisation will have to guarantee the quality of the components, according to the lemma that “the quality produces during the manufacture and no during the measurement”. This aim only can reach by means of a control of the process, when it verifies the aptitude of the pieces for the manufacture. To be able to abandon the technicians of manual measurement, the manufacturers of Mülheim finish to develop beside his mates of Siemens CT of Munich the first own technicians of measurement. “In this field already have done big advances and the first technicians already have put in practice in some areas”, affirms the boss of Production.
The production of turbines of steam in Mülheim
The turbines of steam convert the heat in mechanical power. The heat can produce by means of sources fossils like coal, oil and gas, that burn in special boilers (thermoelectric head offices and electrical head offices of steam and gas), or by means of solar power (thermoelectric solar plants). The heat heats the water. The steam of water produced of this form produces an impulse giratorio in the álabes of the turbuna. Of this way sets up a rotor. Because of the strong fall of the pressesure and the need of a performance enormously high, said process executes of staggered form.
Inside the global network of production of Siemens Power, Mülheim occupies a very important place like centre of development and production of big turbines of steam. Mülheim Directs all the services of engineering, shopping and production, and establishes the specifications of quality and supply. The production takes place so much in Mülheim as in the plants twin of Budapest (Hungary), Cilegon (Indonesia) and Newcastle (England), for quoting only some.
One of the characteristics stood out of the turbines of steam of Siemens is his high quality. During all the productive process, the strict control of quality guarantees a high constant quality and the fulfillment of the specifications demanded, so much in the same plant as by part of the internal and external providers. The controls of operation, materials of manufacture and of geometry accompany to the turbine through all the steps of production.
The manufacture realizar in different parallel steps, but connected successively. It begins with the production of the trees. The trees of turbine manufacture in steel ultrarresistente and supply like pieces soldered prefabricated. It gives them the optimum form in lathes of high precision. In this process demands maximum accuracy of the tolerances, in the order of hundredth of millimetre.
Also in the manufacture of the boxes demands a maximum accuracy. In spite of his size, the milling machines, the lathes and the punches work with a maximum precision and tolerances of hundredth of millimetre.