Nanopartículas para reforzar los brackets transparentes de las ortodoncias
Los brackets de polímeros plásticos transparentes utilizados en las ortodoncias dentales correctoras han dado muy buen resultado en los últimos años, sobre todo por la mejora estética que suponen respecto a los metálicos, pero presentan ciertos problemas de desgaste en la boca. “Estimamos la fuerza que hacen los dientes en el bracket y se nos ocurrió que la nanotecnología podría resultar útil para solucionar esta cuestión”, comenta Juan Baselga, responsable del grupo de Polímeros y Composites de la UC3M. La solución que han ideado es utilizar unas nanopartículas muy duras de alúmina y dispersarlas de forma homogénea en la polisulfona, la matriz de polímero que emplea Ceosa-Euroortodoncia para la fabricación industrial de los brackets.
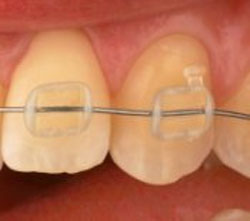
Ya no sólo sirve tener una boca sana, sino que además debe ser bonita. Cada vez más vemos cómo diferentes sectores de la población, más allá del habitual sector adolescente, luce una sonrisa con brackets. Y cada vez menos éstos son de acero inoxidable. Y es que la estética comienza a primar a la funcionalidad. Lo cierto es que se trata de un fenómeno que observamos desde hace pocos años ya que el bracket de plástico parecía no estar a la altura de su homólogo metálico en cuanto a prestaciones: resistencia mecánica, envejecimiento, resistencia a la hidrólisis, etc. Por esta razón tenían una escasa implantación en el mercado actual.
Ahora y gracias a la colaboración de la empresa madrileña Euroortodoncia con la Universidad Carlos III, en ingeniería de materiales, y con Tekniker en técnicas de microinyección, los brackets muestran las ventajas estéticas del plástico junto con unas propiedades de resistencia similares a las de los brackets metálicos.
Las prestaciones alcanzadas por el nuevo producto se basan principalmente en los dos siguientes factores: la utilización como material base de un polímero de altas prestaciones mecánicas, pero por el contrario de muy difícil inyectabilidad, y el empleo de las microtecnologías como medio de fabricación, tanto del propio molde, como posteriormente del bracket plástico mediante microinyección.
Para hacer frente a la dificultad de inyectar el material, la empresa colabora con Tekniker.
Este nuevo proceso, patentado por la compañía junto a los investigadores de la UC3M, consigue obtener un material con mayor resistencia mecánica y al desgaste, manteniendo la transparencia. “Con esta tecnología hemos conseguido desarrollar un material que es más rígido y que tiene una notable mejor resistencia a la abrasión, por lo que resiste mejor el desgaste producido por los dientes o por los alimentos en el proceso de masticación”, explica el profesor Baselga. Además, resulta biocompatible, algo fundamental cuando va a estar colocado en la boca y cumple con la normativa europea para productos que van a estar en contacto con alimentos.
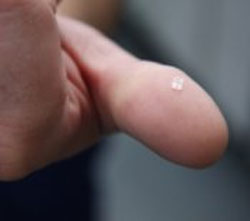
Este nuevo tipo de materiales —los plásticos nanoreforzados— encuentran aplicaciones en diversos campos de la industria, según los investigadores. En concreto, la polisulfona resulta interesante en el área biosanitaria por su biocompatibilidad en desarrollos de equipos medico quirúrgicos, donde es preciso mejorar la rigidez y la resistencia a la abrasión. Además, también encuentra potenciales aplicaciones en la industria del automóvil o en el campo de la seguridad; por ejemplo, en el desarrollo de nuevos visores en los cascos de los bomberos.
Esta innovación permite la incorporación y dispersión homogénea de nanopartículas a una matriz polimérica en muy baja proporción. Tras este proceso basado en técnicas químicas verdes que realizan los investigadores de la UC3M, en la empresa Ceosa-Euroortodoncia mezclan las partículas ya dispersas con el polímero mediante técnicas de micro-extrusión y micro-inyección para fabricar la pieza final. “Nosotros dosificamos el plástico, pues las máquinas normales lo mínimo que pueden inyectar son unos 15 gramos, cuando nuestras piezas pueden pesar 0,06 gramos… sería algo así como intentar inyectar insulina con una jeringa de caballo”, ilustra el director de la compañía, Alberto Cervera. “Y con la tecnología que estamos utilizando, la micro-extrusión y la micro-inyección, somos capaces de controlar con extrema precisión estas cantidades minúsculas de material”, añade.
La relación entre UC3M y Ceosa/Euroortodoncia aprovecha las sinergias entre el sector público y privado. “Somos una pyme y nos apoyamos en la universidad para tener un producto de primera línea, lo que luego revierte en acuerdos que hacemos desde hace más de una década en forma de proyectos de fin de carrera, tesis doctorales o programas de investigación conjuntos en el ámbito de la Unión Europea o la Comunidad de Madrid, por ejemplo”, describe Alberto Cervera. “Aprendemos un montón de esta colaboración —agrega Juan Baselga— porque desde la empresa nos plantean los problemas reales a los que se enfrentan en su área industrial y nos abren sus laboratorios a nuestra necesidades”.
Las patentes y la aplicación innovadora resultante son un claro ejemplo de la transferencia del conocimiento y de la tecnología que la UC3M promueve a través de su parque científico. Ciento veinticinco grupos de investigación y varios laboratorios trabajan para que la innovación sea posible. Todo ello, junto a una cartera tecnológica propia, muestran todas las capacidades de colaboración de la Universidad con la empresa, industria e instituciones.