Pruebas predictivas de dureza para el control de producción y diseño de materiales
Las pruebas de dureza se usan, entre otros métodos, para conseguir esta información y conocer las características de estos materiales. Normalmente, la dureza se testa a temperatura ambiente, después de que la pieza haya sido enfriada tras el templado o haya sido sometida a una temperatura moderada. Pero en ese momento, la pieza ya ha atravesado diferentes fases metalúrgicas. Así, la prueba de dureza resulta menos efectiva para estimar las propiedades mecánicas a altas temperaturas, incluso tras un enfriado rápido por apagado en el que pueden haber contribuido efectos adicionales como la dureza de tensión o la transformación de fase sin difusión.
La realización de la prueba de dureza in situ a una alta temperatura de hasta 700ª C —como recientemente ha conseguido el Centro de Materiales de Leoben, en Austria [2]— se utiliza para analizar la precipitación y el reblandecimiento con el tiempo. Para este propósito, se utiliza un durómetro de rebote automático acorde al principio EQUOTIP. Se puede reducir la disipación de la energía ya que no hay recalentamientos, lo que hace posible determinar las características del material en línea y durante el proceso de producción. De esta manera, se puede llevar a cabo la prueba y variar los componentes del material durante el tratamiento térmico. A continuación, detallamos los recientes resultados obtenidos con este método en aceros para útiles con una alta aleación.
La prueba de dureza por rebote
Muy en sus comienzos, el nuevo valor de medida de dureza Leeb (HL) no era conocido, y se tenía que facilitar la conversión a valores de dureza tradicionales como Brinell (HB), Rockwell (HR) o Vickers (HV) según las necesidades de los usuarios para asegurar su calidad de producción. Con el tiempo, el valor original de valor de dureza Leeb, acorde al principio EQUOTIP, ha ido imponiéndose cada vez más como un método decisivo para controlar la calidad de los procesos de producción. De ahí que numerosas industrias hayan aceptado ya con especificaciones escritas su significancia y credibilidad en sus tests normalizados.
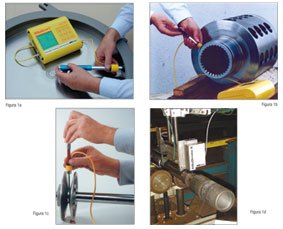
En 1999, el Instituto Force de Dinamarca [5-7] llevó a cabo una investigación detallada sobre durómetros portátiles en aceros de vaso a presión. Concluyeron que los resultados obtenidos con la prueba de dureza por rebote acorde al principio EQUOTIP deberían ser aceptadas en general sin conversión por las razones explicadas más arriba. La aceptación generalizada de las industrias al principio EQUOTIP ha llevado a su normalización en 1996 (ASTM 956-96). Hoy, EQUOTIP se puede utilizar de acuerdo al NIST (National Institute for Standards and Technology), organismo oficial de normalización norteamericano.
La base de medida HL
HL= VR .1000
VA
Esto significa que con un valor totalmente elástico en que VR = VA, HL sería igual a 1.000 o, lo que es lo mismo, que HL desciende a medida que disminuye la dureza del material. Este procedimiento explica el nombre de EQUOTIP (Energy QUOtient y TIP; traducido: cociente de energías y tip: golpe, toquecito, el necesario para desencadenar la medida). El procedimiento de medida se muestra con más detalle en la figura 2.
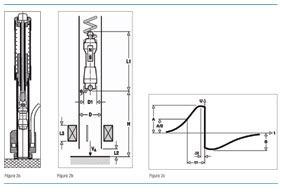
Otro parámetro importante para determinar el valor HL de un material de dureza conocida es la energía de impacto, que se calcula a partir de la velocidad de impacto, la masa del cuerpo de impacto y su rigidez —que determina cuánta energía absorbe el cuerpo de impacto—. Para reproducir la dependencia de la dirección estándar es necesario especificar la velocidad y la masa por separado con el fin de obtener una longitud de movimiento específico. De esta manera, el método de prueba LEEB permite medir en cualquier dirección. Sin embargo, los resultados no son completamente independientes del ángulo de impacto. Cada una de las pruebas estándar tiene su propia dependencia de dirección característica, determinada por 1) la combinación de la velocidad de impacto y el movimiento libre del cuerpo de impacto y 2) la forma de la señal de inducción de voltaje, determinada por la curva velocidad/tiempo por una parte y, por otra, por las características de la bobina sensora y el imán permanente. Esto significa que la energía de impacto, en general, es el parámetro más importante en la significancia de los valores HL para todos los durómetros que trabajan con unidades de los siete cuerpos de impacto estandarizados: D, DC, E, D+15, DL, C y G. La bobina y el imán permanente no se especifican explícitamente, pero tienen que ser escogidos de tal manera que sus parámetros cumplan con la señal de inducción de voltaje.
Es bien sabido que las lecturas HL en una muestra dada varían significativamente dependiendo del cuerpo de impacto utilizado. Las principales razones son 1) las diferentes energías de impacto, 2) los diferentes materiales y tamaños del la punta del cuerpo de impacto y 3) la diferente rigidez de los cuerpos de impacto. Es por ello que el valor HL depende de la geometría y las propiedades del material de la punta, y predominantemente de su curvatura, dureza y elasticidad. Además, el efecto de la deceleración en las corrientes en remolino puede afectar el resultado. Por ello, se debe especificar también el material del tubo y hay que adoptar precauciones especiales para reducir estas corrientes en remolino.
Si no se adoptan las precauciones mencionadas, pueden ocurrir grandes desviaciones impredecibles en los valores HL. Mostramos una comparación de una serie de medidas tomadas con un durómetro clásico y un durómetro EQUOTIP en la figura 3. Se cubrió un amplio rango de dureza usando varios bloques de referencia estándar de diferentes durezas. Bastante a menudo las medidas son buenas para el rango de dureza de bloques de referencia estándar entre 700 y los 750 HLD (índices del instrumento de impacto D). Pero por debajo y por encima las desviaciones son considerablemente grandes y los resultados de tales medidas han de ser consideradas insignificantes y erróneas.
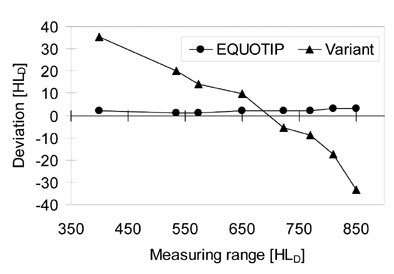
Referencias
[2] Ebner,R; Leitner,H.; Caliskanoglu,D.; Marsoner, S.; Jeglistch, F.; Z.Metallkd.92 (2001) 7, 820
[3] ASTN A956-00: Método estándar de prueba para el testado de dureza Leeb en productos de acero
[4] Durómetro EQUOTIP. Instrucciones de uso. 7ª edición (98 06 291 E) PROCEQ SA, Zurich 1978.
[5] Borggreen, K.; Hansen, D.H.; Hansen, J.B., Auerkari, P. Nordtest Technical Report 424. Primera Parte. Instituto Force, Copenhague, 1999.
[6] Borggreen, K.; Tønder, P; Lorentzen, M.S Hansen, J.B.; Auerkari, P. Nordtest Technical Report 424. Segunda Parte. Instituto Force, Copenhague, 1999.
[7] Borggreen, K.; Tønder, P; Lorentzen, M.S Hansen, J.B.; Auerkari, P. Nordtest Technical Report 424. Tercera Parte. Instituto Force, Copenhague, 1999.