Sensores de temperatura con autocalibración
El proceso de fermentación
La fermentación es un proceso de cultivo de células. Los cultivos consumen una solución de nutrientes, multiplicando y creando el producto necesario. La fermentación normalmente se realiza en biorreactores seriados, los cuales están fabricados en acero inoxidable 316L y encamisados para calentarlos o enfriarlos según se requiera por el proceso.
La célula a cultivar se introduce en el biorreactor, el cual se llena con una solución nutriente. Esta solución, varía en función del cultivo celular específico y del producto deseado, pero típicamente consiste en glucosa, glutamina, hormonas y otros factores de crecimiento. El agitador asegura que la solución y el cultivo celular se mezclan completamente para promover un crecimiento eficiente dentro del depósito. Los biorreactores están conectados en serie, con cada recipiente sucesivo más grande que el anterior para contener la masa celular creciente.
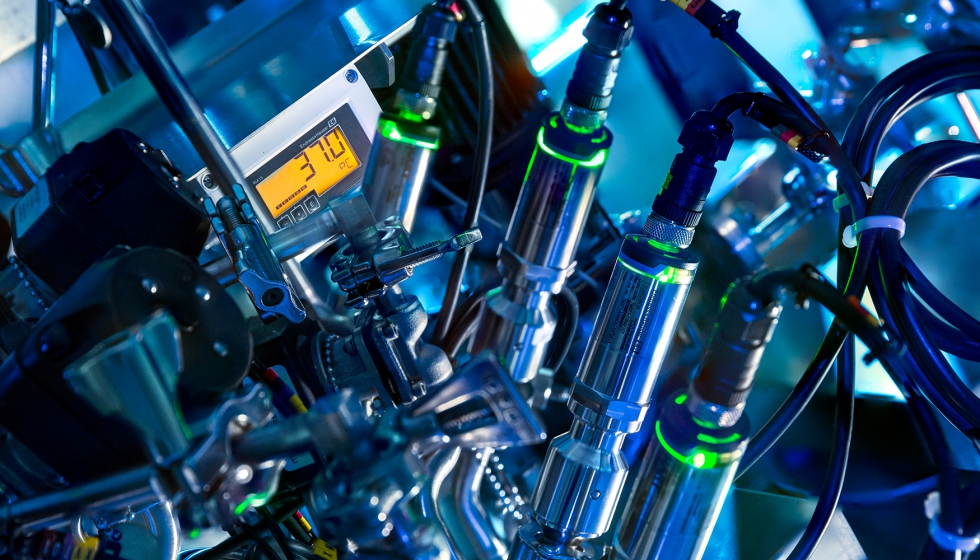
El producto resultante de las reacciones puede ser desde antibiótico hasta vacunas y otros productos basados en células. La reacción se completa una vez se ha consumido la solución nutritiva, alcanzándose el rendimiento deseado. La solución pasa al proceso de recolección donde el producto se separa de las células muertas y otros productos de desecho (CO2, amonio y lactato).
El proceso de fermentación se divide en varias fases: preparación del medio estéril, fermentación, recolección, proceso de limpieza (CIP), aclarado final y esterilización (SIP). Los tres tipos más comunes de fermentación por lotes son, lote único, recolección intermitente / lote alimentado y lote continuo.
• Un lote único de fermentación, funciona hasta que no hay más nutrientes por consumir por las células cultivadas. Normalmente entre 7 y 14 días.
• El lote por recolección intermitente, funciona de manera similar al lote único. Excepto que a medida que se agotan los nutrientes y se recoge el producto, se agrega una solución de nutrientes fresca para permitir ciclos de lotes más largos. El tiempo típico es de 2 a 3 semanas.
De manera similar, un proceso por lotes alimentados, agrega nutrientes y soluciones de alimentación adicionales, pero pospone la recolección hasta el final del lote.
La producción de vacunas suele ser una cosecha intermitente, mientras que la producción de proteínas, generalmente, se alimenta por lotes.
• Un proceso por lotes continuo, agrega nutrientes de manera continua y recolecta producto y desechos con un dispositivo de retención celular, lo que resulta en una mayor concentración de producción. Este tipo de lote se usa especialmente para procesos lábiles, como la producción de células madre. Los nutrientes y el nuevo cultivo celular se añaden continuamente y la recolección se realiza sin detener el proceso. El proceso sólo se para por motivos de mantenimiento, limpieza/esterilización o por calibración.
Con lotes que duran varias semanas, o incluso meses, un sensor de temperatura fuera de especificaciones sin detectar, puede arruinar la producción entera del lote, a un coste de varios cientos de miles de euros de valoración de producto.
Esto es debido, básicamente, a que la temperatura es el parámetro más importante en los procesos de fermentación. Se utiliza para optimizar el crecimiento y la productividad y monitorizar las condiciones del reactor. La temperatura es importante en el mantenimiento de la solubilidad del medio, así como en proporcionar condiciones estables en la producción de proteína. Los fermentadores, normalmente, tienen múltiples sensores (ver imagen 1) monitorizando la temperatura en varios niveles de la solución para mantener una temperatura uniforme. Los sensores de temperatura están también en las camisas calefactoras para mantener la temperatura adecuada (ya sea frío o calor) de los reactores.
Limpieza
Es importante que los elementos biológicos no deseados (p.ej. bacterias ajenas) no crezcan en los reactores. La contaminación de los tanques puede dar como resultado una pérdida de producto o incluso obligar al desmantelamiento del reactor para su limpieza. Por este fin, los tanques de fermentación son limpiados y esterilizados después de cada Batch mediante CIP y SIP.
El proceso CIP es utilizado habitualmente para la limpieza de los biorreactores, fermentadores, depósitos de mezcla, entre otros en las industrias de Ciencias de la Vida, Alimentación y Bebidas. El proceso CIP es utilizado para remover los componentes de los cultivos celulares de lotes anteriores, eliminando los residuos del proceso y controlar la bio-carga, reduciendo los niveles de endotoxina en los equipos y sistemas de procesamiento. Esto se logra durante el CIP con la combinación de calor, acción química y caudal turbulento a lo largo del tiempo para remover los precipitados minerales y los residuos proteicos. La solución cáustica (base) es la solución principal, aplicándose una sola vez y recirculada a través del biorreactor, seguido de un enjuague de agua para inyección (WFI) o agua pura (PW). El lavado con la solución ácida se utiliza para eliminar los precipitados minerales y los residuos proteicos.
El proceso SIP, es un proceso de esterilización que consiste en la inyección de vapor en el depósito a 121 ºC, mantenido durante una hora.
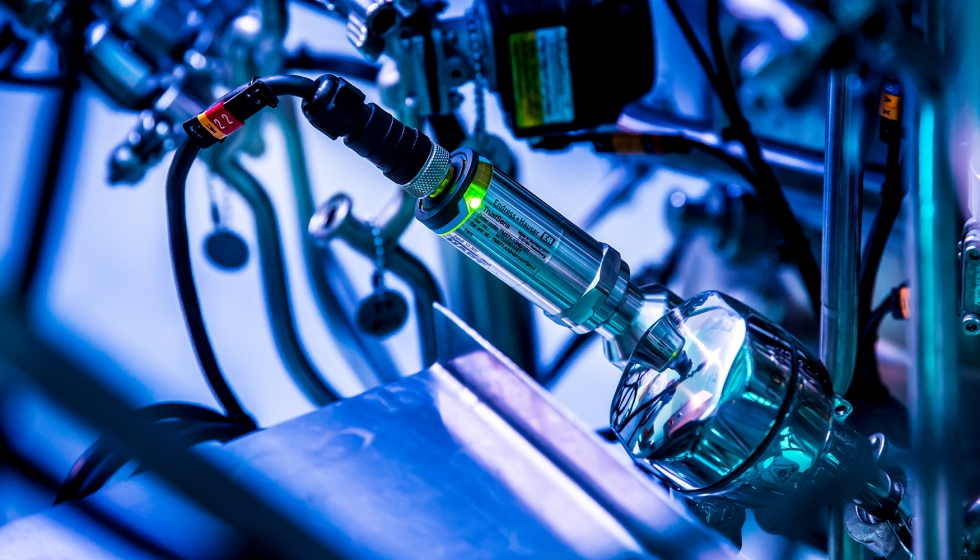
Recientemente, la Gestión de Riesgos de la Calidad (QRM por sus siglas en inglés), se ha convertido en un requisito regulatorio de obligado cumplimiento para los fabricantes de fármacos. La Agencia Europea de Medicamentos (EMA) y la Federal Drug Administration (FDA) de Estados Unidos, publican guías y requisitos que se espera sean cumplidas por los clientes y vendedores. Guías tales como ‘Process Validation: General Principles and Practices’ de la FDA y el anexo 15 publicado por la EMA, ofrecen información a los fabricantes de medicamentos de como diseñar correctamente los procesos.
Asimismo, la ISO9001:2008-7.6, Good Manufacturing Practice (GMP) y las normas y estándares de la Organización Mundial de la Salud, (WHO) requieren que todos los equipos e instrumentos sean calibrados o verificados en intervalos específicos, contrastados con los estándares de medición trazables a nivel nacional e internacional. El problema principal con los ciclos de calibración programados, es el rendimiento de los instrumentos entre calibraciones.
Cuando se planifica un ciclo de calibración de un instrumento, en el fondo, se está realizando una gestión del riesgo que se puede tener en la fabricación de un producto por un error del instrumento calibrado. En la siguiente figura, se muestra un ciclo de calibración de seis meses. La línea roja, denota el riesgo de que un instrumento pueda desviarse a lo largo del tiempo debido a la deriva del propio sensor, envejecimiento u otros factores una vez se ha recalibrado a las especificaciones iniciales cada seis meses.
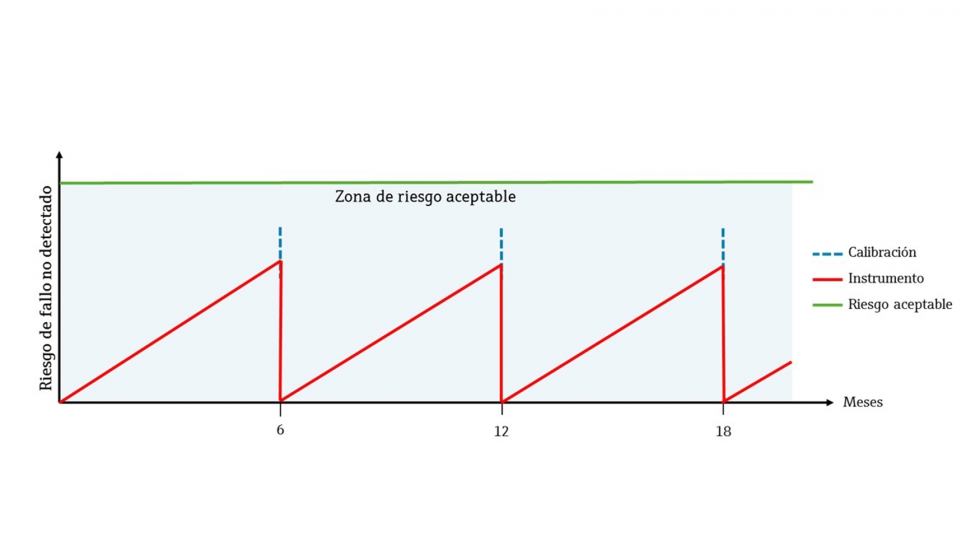
La evaluación de cada cuanto se tiene que realizar una calibración, dependerá tanto de la gestión del riesgo de fabricación como del coste asociado que representa. Este coste asociado, no sólo implica el coste propio de realizar la calibración, si no los costes de:
- Tiempo de paro de producción, valoración de cuánto se deja de producir durante ese periodo de tiempo
- Agentes de limpieza de la instalación (CIP/SIP)
- Costes energéticos para realizar la limpieza (CIP/SIP)
- Inertización de la instalación.
En definitiva, hay que realizar una evaluación entre el riesgo de que un proceso salga erróneo y el coste global de realizar las calibraciones. A mayor frecuencia de calibración, mayor coste, pero mejor control del riesgo de proceso.
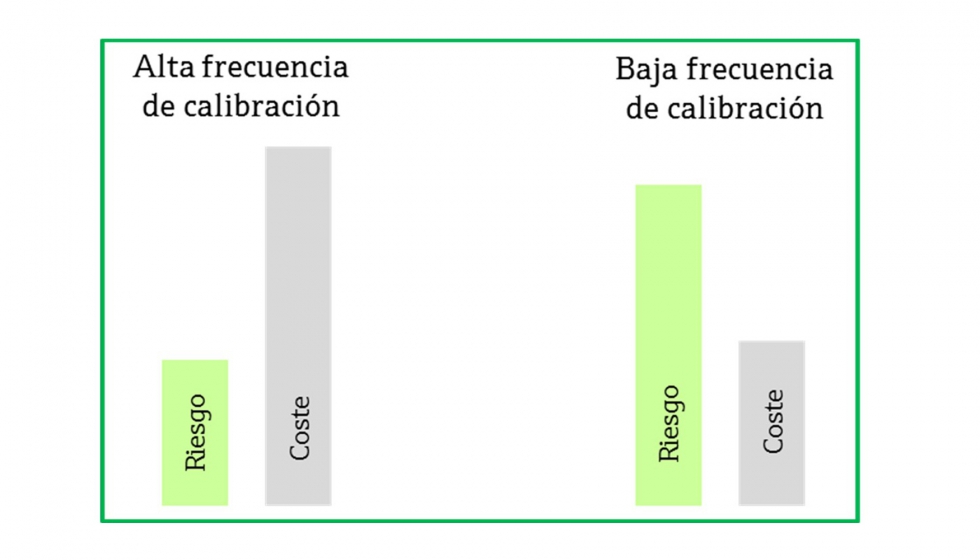
La desviación entre las calibraciones siempre tiene que permanecer por debajo de un nivel aceptable. Sin embargo, la posibilidad de una situación de fallo no detectado (fuera de especificaciones) aumenta gradualmente a lo largo del tiempo, teniendo como resultado un aumento del riesgo en el aseguramiento de la calidad del producto fabricado.
Si un sensor de temperatura se sale de especificaciones antes del periodo de calibración fijado, aparecen una serie de preguntas de no fácil respuesta.
- ¿Cuándo el sensor se fue de especificaciones?
- ¿Cuántos lotes (Batches) se han visto afectados?
- ¿Cuál es la calidad de esos lotes?
- ¿Tiene el producto que ser sacado del mercado?
- ¿Qué coste de imagen y económico tendrá para la empresa?
Lo ideal sería que los sensores de temperatura se calibrasen después de cada lote, pero los costes de realizar calibraciones innecesarias, incluyendo los costes laborales y de producción, así como una cierta cantidad de riesgo al tener que manipular los sensores y el posible daño de estos, descarta esta opción.
En la mayoría de los casos, la fijación de la frecuencia de calibración dependerá básicamente, del riesgo de que un instrumento pueda desviarse a lo largo del tiempo debido a derivas del propio sensor respecto al coste global de realizar las calibraciones.
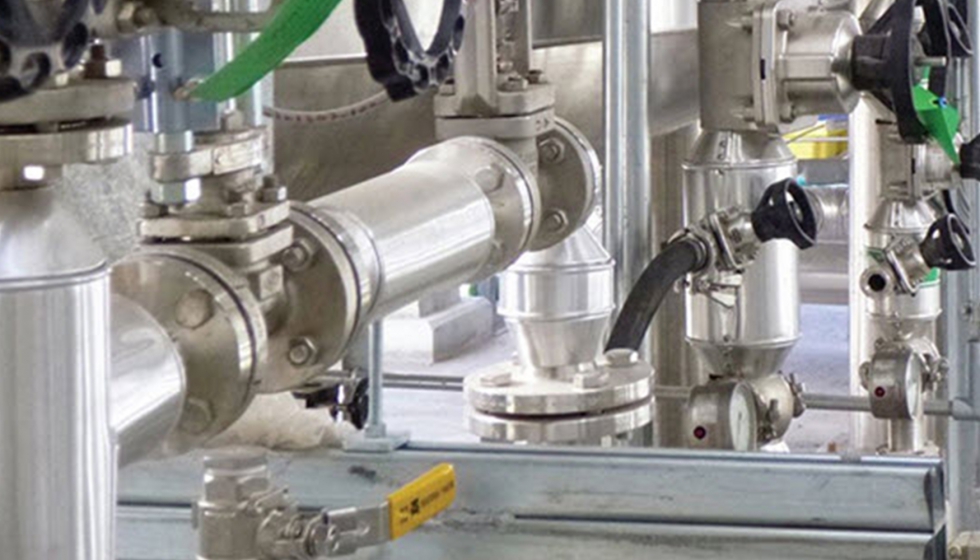
Calibración
Los elementos de medición de temperatura deben tener tanto una rápida respuesta como una alta exactitud en la medición de la temperatura. Además, son frecuentemente calibrados para mantener la exactitud en la medición. Incluso, se comparan entre ellos los sensores de temperatura de los depósitos, para detectar cualquier deriva de temperatura.
A diferencia de los procesos CIP/SIP, la calibración de los sensores no se realiza entre lotes. Una razón de peso para esto es que la calibración es un gran consumidor de tiempo y requiere que todo el proceso no esté operativo teniendo como resultado una menor producción. Esto da lugar a una falta de fiabilidad e inexactitud de la medida que podría llegar a causar niveles inaceptables de incertidumbre, arrastrándose este error entre las calibraciones. El departamento de metrología, debe tener en cuenta estas incidencias para realizar un cronograma correcto de calibración.
Los ingenieros de metrología (fiabilidad) deben pensar y analizar cuidadosamente las frecuencias de calibración. Calibrar con demasiada frecuencia resultará en una reducción de producción inaceptable, mientras que calibrar de vez en cuando puede dar como resultado un producto fuera de especificaciones. Se deben seleccionar los productos y sensores que tengan una mejor estabilidad a largo plazo, menor deriva y (si es posible) auto-monitorización para indicar si un sensor está fuera de tolerancia entre los ciclos de calibración.
Sensores con autocalibración
La más reciente innovación en temperatura son los sensores de temperatura con autocalibración, que reducen al mínimo los riesgos del aseguramiento de la calidad del producto, mejorando la productividad. Además, reducen los costes operativos (Opex) y de compra (Capex) de los patrones y del banco de calibración, costes por calibración y gestión de documentación (ver figura 2).
Esto se logra gracias a la referencia de alta precisión incluida en el mismo sensor de temperatura y que se basa en un fenómeno físico conocido como Punto de Curie o Temperatura de Curie. El punto de Curie es la temperatura a la cual las propiedades ferromagnéticas de un material cambian abruptamente a paramagnéticas. La Temperatura de Curie de un material es una constante invariable en el tiempo, que la fija la composición química del material y que es única para cada material. Esto proporciona un punto físico fijo permanente que se utiliza como referencia para la comparación del sensor de temperatura.
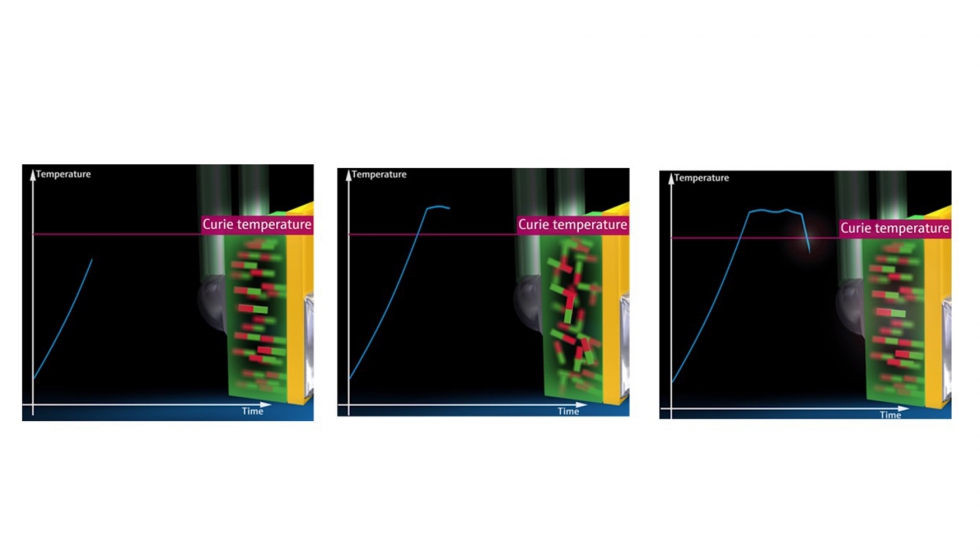
Cada vez que se inicia una fase de enfriamiento desde una temperatura superior al Punto de Curie, por ejemplo, tras la finalización de un proceso SIP, el sensor se calibra automáticamente al alcanzar la Temperatura de Curie.
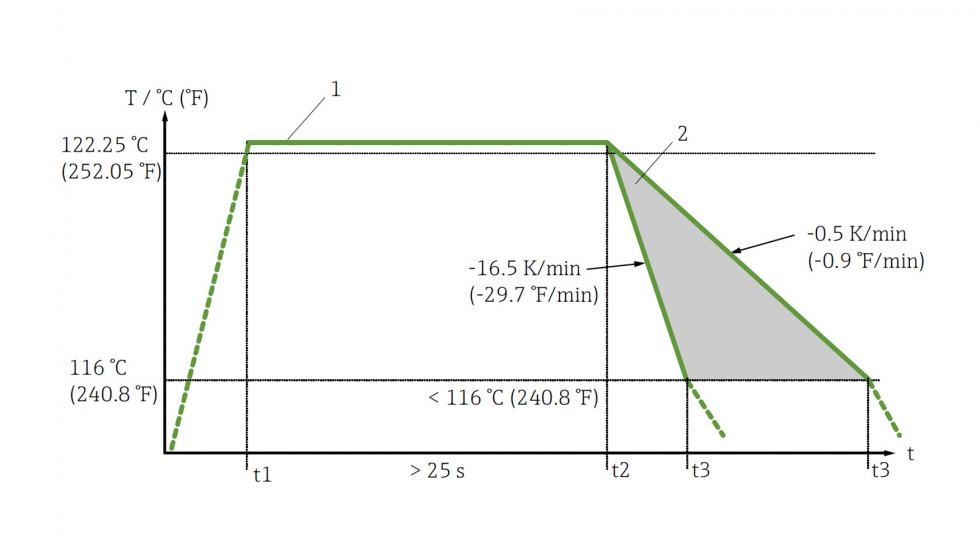
En ese momento, el cuerpo de referencia transmite una señal eléctrica, por el cambio de paramagnético a ferromagnético, que es detectada por la electrónica que incorpora el sensor, realizándose, además, una medición en paralelo del sensor de temperatura. La comparación entre estos dos valores, el de referencia y el del sensor, es de facto, una calibración que identifica el error en el sensor de temperatura.
Si la desviación medida está fuera de los límites fijados, el equipo proporciona una alarma o mensaje de error que incluso se puede visualizar físicamente en la propia unidad mediante el dispositivo LED que incorpora.
Los datos de calibración adquiridos son almacenados electrónicamente en la propia unidad y pueden ser leídos por el sistema de control mediante el protocolo Hart y utilizando un software de gestión de activos, como por ejemplo FieldCare de Endress+Hauser, extraer el certificado de calibración auditable que se crea de forma automática.
Con esta tecnología, la calibración se realiza automáticamente cada vez que la temperatura de proceso pasa a través del Punto de Curie en un proceso SIP, CIP o por perfil de temperatura en el propio proceso. Esto reduce drásticamente el riesgo de deriva relacionado con el error del proceso y, por lo tanto, costosas pérdidas de producción.
Más información acerca del funcionamiento de esta innovación tecnología, en este vídeo
Calibración de lazo
En la mayoría de los casos, también se requiere una calibración del lazo de medición, no simplemente del sensor de temperatura. La innovación tecnológica aquí descrita, incorpora la posibilidad de poder realizar una calibración de lazo de forma automática, sin necesidad de extraer el sensor del proceso. El sistema de control configurado para tal caso, unido al sensor de temperatura, realizan un protocolo de comunicación verificando la validez del lazo a diversos valores de comunicación analógica. De esta forma, se puede analizar la situación de todo el lazo de control y no solamente del sensor de temperatura.
Monitorización Heartbeat
Independientemente de la auto calibración, la cual permite disponer de certificados de calibración de forma automática cada vez que se inicia un proceso de enfriamiento rebasando la temperatura de Curie, también es importante la monitorización en continuo por el sistema de control de la señal de incertidumbre.
Gracias a la tecnología Hart, es posible extraer información de cuatro variables de proceso y poder llevarlas al sistema de control. Entre estas variables, está la diferencia de temperatura entre la referencia de Curie y la temperatura del sensor de medición, es decir, la desviación en el punto de calibración de Curie. De esta forma, el sistema de control tiene, en todo momento, la desviación que se está produciendo, pudiendo monitorizar la tendencia del sensor a largo plazo y el estudio de las desviaciones que se pudieran producir.
Calibraciones más rápidas
Todos los sensores de temperatura tienen que ser calibrados periódicamente, esto implica extraerlos del proceso lo cual puede provocar errores y consumo de tiempo. El mayor problema es que los sensores tienen que ser desconectados eléctricamente antes de ser extraídos del proceso y volverlos a reconectar una vez finalizada la calibración. Aunque el proceso es realmente sencillo, se pueden provocar errores de conexionado eléctrico ya que las terminaciones eléctricas son problemáticas en un entorno de fabricación. Este proceso típico de calibración, dura alrededor de 30 minutos por sensor de temperatura.
Si el transmisor es cableado incorrectamente o los cables se ven dañados, se puede incrementar este tiempo en hasta 20 minutos por equipo. En algunos casos, si el daño en los hilos del sensor es extremo, puede incluso tener que cambiarse completamente el sensor de temperatura.
Otro reciente desarrollo que involucra a los sensores de temperatura y que no requiere desconectar los cables cuando se extrae un sensor es el cuello QuickNeck (ver imagen 4). El técnico simplemente tiene que girar la parte superior del sensor un cuarto de vuelta y el sensor es extraído fácilmente. De esta forma, eliminando la desconexión y conexión tanto eléctrica como mecánica de los elementos de medición de temperatura, se pueden reducir los tiempos de calibración a la mitad, llevando a cabo una calibración en tan solo 15 minutos.
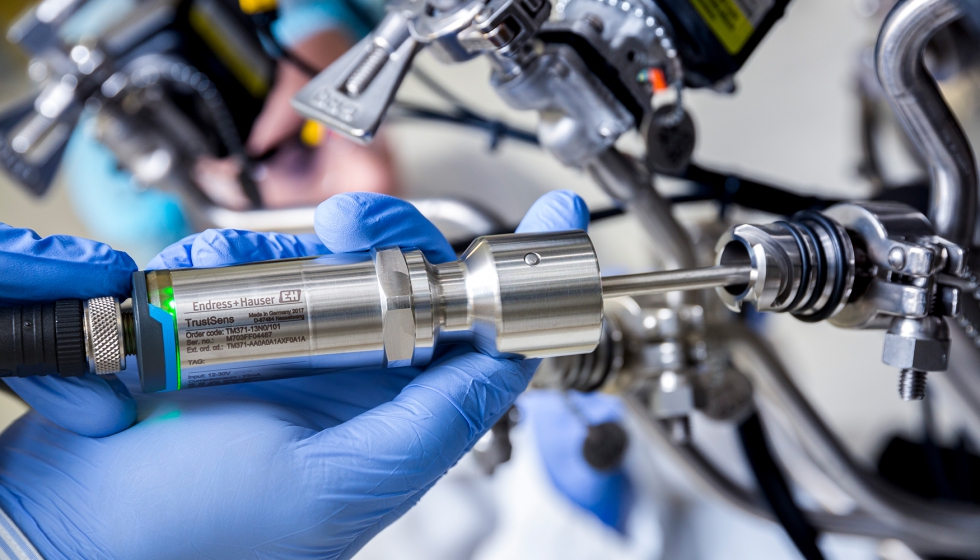
Sumario
La temperatura es una medición crítica en los procesos de bio-ingeniería por ello, la FDA y otras agencias requieren que se realicen calibraciones de forma regular de los sensores de temperatura. La mayoría de las plantas calibran los sensores de temperatura cada seis meses, pero estos pueden desviarse en este periodo, pudiendo arruinar lotes de gran valor económico. La tecnología patentada de cuello rápido (imagen 4) elimina la necesidad de desconectar los cables, disminuyendo el tiempo de calibración a la mitad, pero la gran innovación es la utilización de sensores de temperatura auto calibrables que se calibren automáticamente al final de cada lote o proceso de esterilización. El valor añadido de estos sensores es:
- Reducción de los riesgos de producción, ya que se conoce en cada lote que el sensor está midiendo correctamente.
- Aumento de productividad al no tener paradas de planta para realizar la calibración.
- Ahorro de costes de limpieza y sanitización gracias a no tener que desmontar el sensor de proceso.
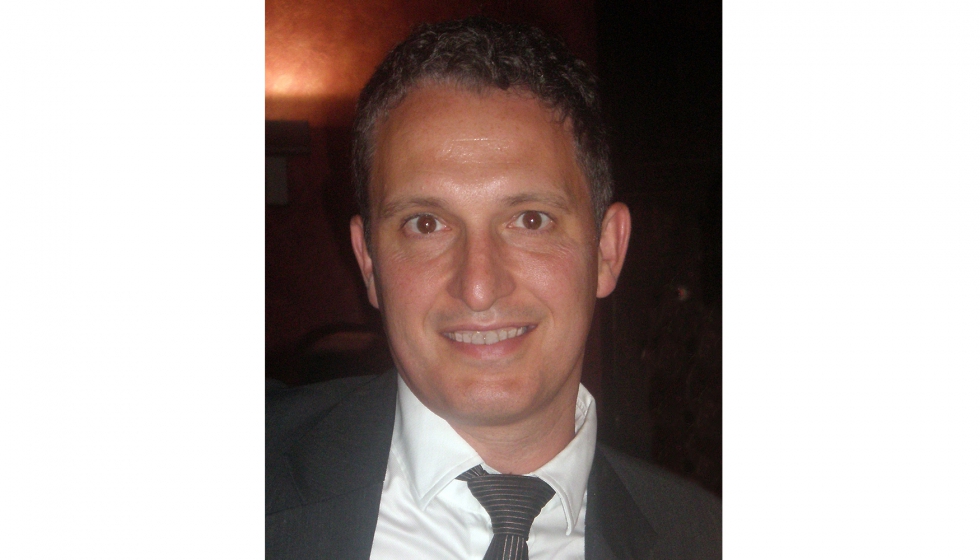
Enlaces de interés
• Explicación del principio de funcionamiento del sensor TrustSens: https://goo.gl/kUJ5c9
• Evaluación del sensor TrustSens por la plataforma Visaya: https://goo.gl/94f53h
• Webinar: TrustSens el primer sensor con auto calibración: https://goo.gl/yGdRJA
• El sensor más rápido del mercado: https://goo.gl/kZuoCM