Influencia de los materiales aeronáuticos en la selección de las herramientas de corte para su mecanizado
A finales del siglo XIX el aluminio comenzó a utilizarse para la fabricación de dirigibles. Los hermanos Wright, a los que se les atribuye, en 1903, la invención del primer avión autopropulsado, ya utilizaron aluminio para su fabricación. Desde entonces hasta nuestros días el aluminio ha seguido perfeccionándose mediante nuevas aleaciones cada vez más resistentes (como la 7075 T6) y que siguen siendo ampliamente utilizadas en la industria de la aviación, suponiendo entre un 20% a un 60% (dependiendo del modelo de avión) de los materiales utilizados en la fabricación de las aeronaves. Su principal aplicación es en estructuras primarias (fuselajes).
A principios de los años 40, se comenzaron a fabricar los primeros aviones impulsados por turborreactores (motores de reacción) concebidos para reemplazar a los de pistones. Este hito marcó también un importante desarrollo de nuevas aleaciones que fuesen resistentes a altas temperaturas y a su vez que tuviesen una alta resistencia a la oxidación, se puede decir que fue el principio de las que hoy conocemos como superaleaciones o aleaciones resistentes al calor. Los componentes principales de estas aleaciones son el níquel, cobalto, cromo, molibdeno y hierro (ejemplos de aleaciones resistentes al calor utilizadas hoy en día son; Inconel (718, 625, etc.), Hastelloy, Invar, Monel, etc. Su principal aplicación en la aeronáutica, son los motores de los aviones. Unos 10 años más tarde comienza el uso comercial del titanio y sus aleaciones (la aleación más común hoy en día es el Ti6Al4V), incorporándose también a piezas críticas de las estructuras y de los motores aeronáuticos.
A principios de los años 60 se comenzó a introducir la fibra de boro para el uso de materiales compuestos, una fibra costosa de producir y de aplicaciones bastante reducidas. Pero a finales de los 60 se inició la producción de fibra de carbono y de aramidas, lo que supuso un gran salto en la variedad de aplicaciones y una reducción muy importante de los costes de producción. La demanda por parte de los fabricantes de aeronaves de materiales más ligeros, unidos al incremento del precio del combustible por la crisis del petróleo de 1973, hicieron que cada vez se tuvieran más en cuenta estos materiales ligeros y resistentes, utilizándose al principio en estructuras que no tuvieran que soportar grandes cargas.
Hoy en día, gracias a los grandes desarrollos que han experimentado estos materiales y la necesidad de ahorro en consumo de combustible (menos peso, menos gasto), mayor protección ambiental y ahorro de operaciones, los composites representan hasta el 50% de los materiales en el total de algunos modelos de aviones, utilizándose para las estructuras primarias y secundarias. Algunos ejemplos de composites son plásticos reforzados con fibras de carbono (CFRP), de vidrio (GFRP), Aramida (Kevlar), PEEK, etc.
Materiales más comunes a mecanizar en la industria aeronáutica
- Aleaciones de aluminio; 2011 (al Cu), 6061 (al Mg), 7075 T6 (al Zn), etc.
- Aceros inoxidables:
o PH's 13/8 PH, 15/5 PH, 17/4 PH, etc.)
o Dúplex y superdúplex (2205, 2304, 2507, etc.)
o Austeníticos (304, 316, 316L, 310, etc.)
o Martensíticos (420, etc.)
- Titanios y aleaciones de titanio (Ti6Al4V, Ti5553, Ti 6246, etc.)
- Super aleaciones o aleaciones resistentes al calor (Inconel 718, Hastelloy, etc.)
- Composites (CFRP, GFRP, etc.)
Maquinabilidad de los materiales aeronáuticos
El término maquinabilidad lo podríamos definir como el efecto que tienen las propiedades de los materiales, sobre la facilidad o dificultad de ser mecanizados por arranque de viruta.
Los materiales que tienen mejor maquinabilidad, por lo general, podemos considerar que se mecanizan con parámetros de corte más altos (Velocidad de corte Vc, Avance F, profundidad de pasada Ap, carga lateral Ae, ) y que se precisa menos potencia y menos fuerza de corte para realizarlo y todo ello con una vida de herramienta mayor y obteniendo mejores acabados.
El material que normalmente se toma como referencia es el acero AISI 1112, al que se le atribuye una maquinabilidad de 100. La composición química de este acero es:
- C => 0,13% máx.
- Mn => 0,7% mín. a 1% máx.
- P => 0,07% mín. a 0,12% máx.
- S => 0,16% mín. a 0,23% máx.
Los materiales con un valor de maquinabilidad por encima de 100, significa que son más fáciles de mecanizar y cuanto más bajo sea el valor, significa que más difícil de mecanizar son.
Aunque los factores que influyen en la maquinabilidad de un material son muchos y complejos de determinar, podríamos enumerar como algunos de los más influyentes;
- la composición química
- la conductividad térmica
- la micro estructura
- la resistencia a la tracción
- la dureza y ductilidad
Aun teniendo en cuenta que son muchas las variables y factores que influyen en la maquinabilidad, y que hacen muy difícil obtener una tabla precisa que relacione materiales y maquinabilidad, he querido mostrar una en la que aparecen algunos de los materiales aeronáuticos más comunes a mecanizar y su correspondiente valor de maquinabilidad.
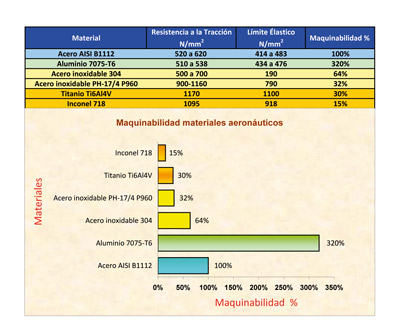
Según el gráfico de la figura 1, el mecanizado del Inconel 718 sería el que más dificultad presentaría a la hora de ser mecanizado, ya que presenta el índice de maquinabilidad más bajo y por el contrario el Aluminio 7075-T6, es el que resulta más fácil de mecanizar, ya que es el que presenta un índice de maquinabilidad mayor.
Influencia del material en la selección de la herramienta de corte (*):
Las propiedades físicas como conductividad térmica y otras y las mecánicas como resistencia a la tracción, límite elástico, etc. de los materiales, son las que determinan su comportamiento ante el mecanizado y por lo tanto nos van a condicionar en la selección de las herramientas adecuadas y en sus condiciones de trabajo.
Aluminio y aleaciones de aluminio
El aluminio es un metal de baja densidad, blando comparado con el acero, aunque aleado puede llegar a alcanzar resistencias a la tracción superiores a 600 N/mm2, presenta buena conductividad térmica, todo ello hace que sea de fácil mecanización.
Fresado y torneado de aluminio
Las características más comunes de las fresas HM integral o placas para el fresado y torneado de aluminio son: Filos de corte muy afilados, ángulos de desprendimiento positivos, canales de evacuación de viruta, amplios (fresado), superficie de desprendimiento pulida (esto no es necesario pero favorece el mecanizado), canales de evacuación pulidos, en las fresas de metal duro (no necesario pero favorece el mecanizado).
El recubrimiento superficial de la herramienta, no es necesario para aluminios con bajo contenido de silicio (Si < 0,5%), aunque éste, le dará mayor duración a la herramienta, sobre todo en operaciones de desbaste. Para aluminios con alto contenido en silicio (Si > 10%) y sobre todo para fresas de metal duro integral, el recubrimiento se hace casi obligado si queremos tener una vida de herramienta mayor, ya que el silicio es muy abrasivo. Para las placas de fresado y torneado, el substrato del material de corte (HM) que se suele utilizar, es de gran dureza (dentro de los carburos de tungsteno), lo que permite que den buen rendimiento, aun sin recubrimientos adicionales.
Las velocidades de corte en fresado y torneado de aluminio (p.e. 7075) con plaquitas de HM pulidas, pueden llegar a 3.000 m/min. Lo que supone unas 15.165 rpm para un plato de Ø 63 mm ó 9.554 rpm para el torneado de una pieza de Ø 100 mm. Los avances también pueden ser altos, p.e. en fresado con plaquitas, de fz = 0,6 mm (avance por diente) o de F= 0,75 mm/rev en el caso del torneado, todo dependiendo de la geometría de las placas, la estabilidad, la pasada, etc.
Para el mecanizado de aluminios con herramientas de metal duro es necesario utilizar aceites de corte, como primera opción, o MQL.
Las piezas aeronáuticas, en muchas ocasiones precisan de unos radios de acuerdo ‘particulares’ lo que hace que las fresas y las plaquitas de fresado deban tener estos radios. Algunos de los radios más comunes son: 0,5 - 1 - 1,6 - 2 - 3 - 3,2 - 4 - 5 mm.
Debido a las geometrías particulares de las piezas para aviones, en muchas ocasiones se requiere que las fresas ofrezcan gran variedad de largos y destalonados de cuello, a la vez de un corte 'extra suave' para poder realizar piezas de paredes muy delgadas sin que éstas sufran deformaciones por las fuerzas de corte.
Aceros inoxidables
Los aceros inoxidables son aleaciones de acero que contienen más de un 11% de cromo, que es el elemento que le confiere la protección contra la oxidación y la corrosión. Atendiendo al tipo de aleación del acero inoxidable, los podemos clasificar en:
- Ferríticos (430) (apenas utilizado en aeronáutica, por no ser tan resistente a la oxidación y corrosión, como el resto)
- Austeníticos (304)
- Martensíticos (420)
- Dúplex (2205)
- Endurecidos por precipitación (PH-17/4)
Los inoxidables como vimos en la figura 1 tienen mayor o menor maquinabilidad dependiendo del tipo que sean, pero por lo general, se mecanizan peor que los aceros corrientes. El cromo junto con otros aleantes como el níquel, molibdeno, etc. aumentan la resistencia a la tracción, le confieren menor conductividad térmica, mayor ductilidad y un endurecimiento por deformación, lo que se traduce en más dificultad a la hora de mecanizarlos.
Fresado y torneado en a/inoxidables
Las características más comunes de las fresas de HM integral y placas para fresado y torneado de aceros inoxidables son: filos de corte ‘vivos’, sin llegar a los valores para aluminio, ángulos de desprendimiento positivos, pero no tanto como para aluminio. p.e. para fresas de HM integral; Aluminio => 15º A/inox. => 10º, canales de evacuación similar a los de aceros comunes. Los recubrimientos del tipo TIN, TICN, TIALN, CrN, etc. en el caso de las herramientas para A/inox son muy importantes. En estos materiales, no tener recubrimiento es sinónimo de reducción drástica de la vida de la herramienta debido a las altas temperaturas que se generan en el corte de estos materiales. Para las placas de fresado y torneado, el substrato del material de corte (HM) que se suele utilizar es más tenaz que en las de aluminio.
Las velocidades de corte en fresado y torneado de acero inoxidable con plaquitas de HM pueden estar entre los 60 a 350 m/min dependiendo principalmente del tipo de inoxidable. Los avances, aunque son menores a los usados en los aceros corrientes, no deben de ser reducidos de forma importante pues de hacerlo se genera mayor fricción y más calor. Por ejemplo: avance por diente para una fresa HPC de metal duro integral Ø 12 mm con recubrimiento; - en acero F-114 => fz = 0,075 mm - en a/ inox 304 => fz = 0,053 mm.
Para el mecanizado de aceros inoxidables con herramientas de metal duro es necesario utilizar aceites de corte como primera opción, o MQL, aunque en el caso de fresado con plaquitas cabe la opción de hacerlo en seco, sólo con aire, aumentando la velocidad de corte, poe ejemplo fresado de un AISI 304; - Con taladrina Vc = 130 m/min. – En seco Vc = 220 m/min.
En las piezas para aviones, en los A/inox, igual que en los aluminios, es muy común el uso de radios de acuerdo ‘particulares’ y en ocasiones también se precisan de fresas con largos y destalonados de cuello específicos.
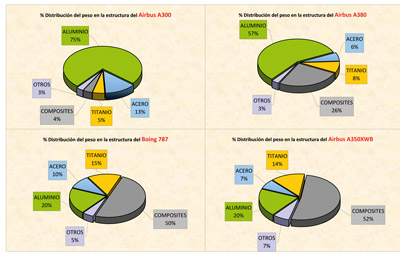
Titanios y aleaciones de titanio
Las aleaciones de titanio como el Ti6Al4V, poseen un ratio resistencia-peso, sin igual, a la vez que una resistencia a la corrosión mayor que los aceros inoxidables, es también dúctil y tienen muy baja conductividad térmica. Otra propiedad que tienen es una rápida recuperación elástica. Todo ello hace que las aleaciones de titanio sean más difíciles de mecanizar.
Fresado y torneado de titanio y aleaciones de titanio
A las herramientas para titanios se les puede conferir características muy similares a las de aceros inoxidables, principalmente en lo que a geometría se refiere (filos de corte y ángulos de desprendimiento). Los recubrimientos resultan imprescindibles de cara a la vida de herramienta. El calor generado en el corte de las aleaciones de titanio es muy alto, debido a su baja transmisión del calor, a su alta resistencia y al efecto de muelle que produce la viruta y que hace que quede rozando sobre la superficie de desprendimiento de la herramienta. El sustrato del material de corte en las fresas de metal duro integral suele ser igual que para los inoxidables, las plaquitas de fresado ligeramente más tenaces y sin embargo, para las placas de torneado suelen tener mayor dureza.
Las velocidades de corte en titanio son bastante más bajas que en los aceros inoxidables, siendo valores muy comunes por ejemplo para fresas de metal duro integral recubiertas Vc = 60-80 m/min. En cuanto a los avances, son muy similares a los de los a/inox austeníticos pero con una sustacial reducción de la profundidad de pasada.
El uso de aceite de corte es imprescindible, en el caso del titanio.
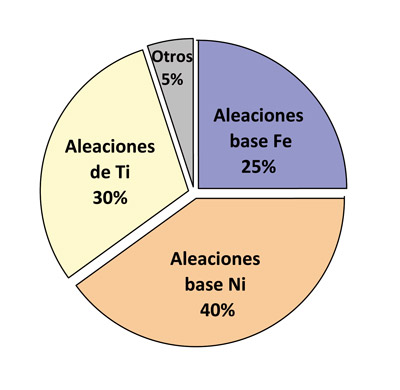
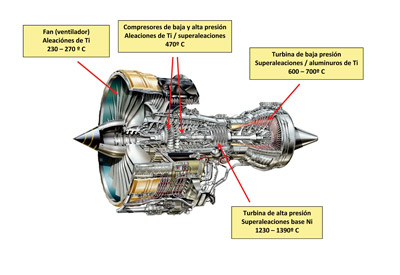
Aleaciones resistentes al calor o superaleaciones
Las superaleaciones más utilizadas en la industria aeronáutica son las de base níquel o con alto contenido de Ni, son aleaciones que mantienen sus propiedades a altas temperaturas y que tienen una alta resistencia a la tracción, a la corrosión, baja conductividad térmica, son abrasivas y presentan endurecimiento por deformación. De ahí que algunas de ellas sean realmente difíciles de mecanizar.
Fresado y torneado de aleaciones resistentes al calor
Aunque algunos de estos materiales tiene una resistencia a la tracción alta, hasta 1.400 N/mm2, se precisa de filos positivos para que al penetrar en el material, no tienda a deformarlo (y por lo tanto a endurecerlo) si no a cortarlo. Todo lo dicho sobre las aleaciones de titanio, sería valido para estos materiales, excepto la velocidad de corte que en el caso de aleaciones como el Inconel 718, tiene que ser mucho menor, por ejemplo fresa de HM integral recubierta; Vc = 30 m/min. Los avances en general son ligeramente inferiores a los utilizados en las aleaciones de titanio (aprox. -20%) y al igual que en los titanios la profundidad de pasada, debe ser reducida respecto a los inoxidables. En cuanto al aceite de corte, también es imprescindible y debe de ser optimizado en su porcentaje para obtener buenos resultados.
Composites
Los composites son materiales sintéticos compuestos por dos o más componentes y que se caracterizan porque el material resultante es de propiedades (físicas y mecánicas) superiores a los que los formaban por separado, tienen muy buenas propiedades mecánicas comparadas con las aleaciones metálicas tradicionales, como pueden ser las derivadas del aluminio, y además los materiales compuestos son menos sensibles a la corrosión o a la fatiga. Suelen ser abrasivos y su mecanizado con una herramienta inadecuada puede producir que las fibras se separen de la matriz, produciendo lo que se conoce como delaminación. La generación de altas temperaturas en su mecanizado, puede provocar quemaduras que dañen o deformen la estructura.
Mecanizado de composites aeronáuticos
Normalmente consisten en fresados y taladrados, siendo mucho menos común el torneado.
Para el fresado de estos materiales con fresas de HM integral, se emplean fresas con geometrías y ángulos específicos para no producir los daños citados en el material, por ejemplo existen fresas para composites del tipo Honeycomb (paneles sándwich) con filos de corte en hélice que por la parte de arriba empujan el material hacia abajo y por la parte de abajo, empujan hacia arriba, al mismo tiempo, para evitar dañar la capa superior y la inferior. Por lo general los filos de corte son más positivos que los empleados para aluminio y dependiendo del tipo de composite, conviene que estén protegidos por recubrimientos que apenas redondean el filo, siendo muy usuales los recubrimiento de diamante o directamente las fresas con insertos de diamante (PCD), aunque debido a su extrema fragilidad, suelen ser utilizados para operaciones de acabado o cuando se requiere un buen acabado superficial.
El fresado de materiales compuestos con plaquitas, se emplea en operaciones de desbaste o piezas de grandes dimensiones y para no dañar el material conviene que sean con filos adecuados para estos materiales (a veces las que se utilizan para fresado de aluminio son válidas) y pulidas para que el corte sea lo más suave posible y reduzca el rozamiento.
El uso de aceites de corte para estos materiales puede dañarlos, por lo que conviene informase en los proveedores de estos materiales, si es posible su uso y qué cuidados hay que tener de cara a la protección de la máquina, en el caso de poder utilizarlos o de cara a la protección personal (aspiradores de polvo y humos producidos) en el caso de tener que hacerlo en seco con aire a presión.
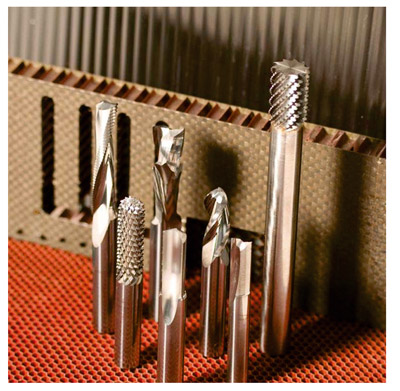

El sector aeronáutico demanda del mecanizado cada día piezas más complejas, de mayor precisión, con mejores acabados y en plazos de entrega cada vez menores, esto unido al alto coste de algunos de los materiales empleados (como titanios y superaleaciones) y al mucho tiempo de mecanizado que lleva realizar algunas de ellas, hace que la elección de la herramienta adecuada, sea clave. Buscándose por estos motivos, en el mecanizado de piezas aeronáuticas, herramientas que sean muy fiables, precisas, productivas y universales, esta última característica, muy importante de cara a conseguirlas en plazos muy cortos y precios más ajustados.