Dinámica de las máquinas de medición de coordenadas
Medición y Control
Estos temas siguen siendo de vital importancia. Sin embargo, el copiado ha cambiado las reglas del juego introduciendo otro factor: las fuerzas de inercia.
Al medir los puntos diferenciados, estas fuerzas de inercia son normalmente insignificantes. Durante el copiado, la aceleración y, por tanto, las cargas de inercia están siempre presentes. A medida que aumenta la velocidad, se incrementa la aceleración. De hecho, la aceleración aumenta mucho más rápidamente, y varía con el cuadrado de la velocidad de copiado sobre una trayectoria de curva normal.
Las fuerzas de inercia a baja velocidad son insignificantes, por tanto, es en esta zona en la que deben funcionar los sistemas de copiado convencionales, que no tienen ningún tipo de compensación dinámica. A medida que aumenta la velocidad, las fuerzas dinámicas dominan rápidamente el rendimiento de medición de este sistema. No obstante, la mayoría de las MMC se emplean en un entorno de producción en el que son importantes los tiempos de los ciclos. Esto supone una gran ventaja a tener en cuenta si se desean unas mediciones más rápidas.
Un ejemplo: El trazado muestra los datos obtenidos midiendo una misma superficie a dos velocidades distintas. Ilustra cómo se acumulan las fuerzas dinámicas según aumenta la velocidad, lo que genera un aumento de errores en la forma.
El trazo rojo muestra las lecturas a baja velocidad (10 mm/s / 0,4 pulg/s), que proporciona un cálculo preciso de la superficie. El trazo azul muestra las lecturas a alta velocidad sin corregir (150 mm/s / 6 pulg/s), y muestra cómo disminuye el tamaño medido del orificio a medida que se acumulan las fuerzas centrípetas en el manguito según la máquina se desplaza alrededor de la superficie. A estas velocidades, las fuerzas de inercia son hasta 225 veces más altas que las alcanzadas durante un copiado a baja velocidad.
Los errores dinámicos aumentan con la velocidad
Las MMC modernas pueden desplazarse a altas velocidades - varios cientos de mm/s. Sin embargo, los copiados normales tienen que hacerse a velocidades mucho más bajas si se necesita cierta precisión. Para obtener una precisión aceptable en piezas de poca tolerancia, los sistemas de copiado convencionales realizan las mediciones a baja velocidad - generalmente, menos de 20 mm/s (0,8 pulg/s).
Evidentemente, existe la posibilidad de copiar a una velocidad muy superior, siempre que se puedan superar los errores dinámicos inducidos por la deflexión de la estructura de la máquina.
El gráfico de errores frente a velocidad muestra el incremento de errores en una tasa de aumento de velocidad, ya que las fuerzas de inercia están relacionadas con la aceleración, a su vez relacionada con el cuadrado de la velocidad.
Emax es el error máximo permitido en la medición de una superficie concreta. Como regla general, debe ser aproximadamente un 10% de la tolerancia de la superficie. Al trazar este error en el gráfico podemos ver la velocidad máxima, S1, a la que se debe copiar la superficie.
Necesitamos buscar la forma de cambiar la relación entre velocidad y precisión, de forma que sea posible alcanzar velocidades más altas manteniendo la precisión. Renishaw lo consigue mediante Renscan DC, una técnica patentada de medición de compensación dinámica.
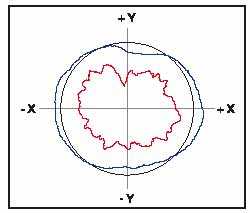
Componentes del error dinámico
Los factores que determinan el perfil de aceleración de la máquina durante el ciclo de copiado incluyen:
Configuración de la superficie: tamaño, forma y orientación, que definen el recorrido del desplazamiento de la máquina.
Velocidad de copiado: define la velocidad de destino que debe alcanzarse durante el copiado (considerando que la mayoría de los copiados empiezan a velocidad cero, por lo que la velocidad no se mantiene durante todo el copiado).
Rendimiento del motor y el servo de la máquina: ¿cuánto puede acelerar para alcanzar la velocidad de copiado de destino?
Por cada perfil de aceleración concreto, existen factores que aumentan la repetición de errores dinámicos (deflexión de inercia), y pueden ser compensados por Renscan DC:
Ubicación de la 'Macro': la rigidez de la estructura de la máquina y, en consecuencia, el rendimiento dinámico, varía durante todo el rango operativo. La posición de la superficie que se va a medir es por tanto un factor significativo.
Condición de la máquina: el estado de los rodamientos y el sistema motor, que puede ser el origen de una "inclinación" durante el copiado.
Aunque no se pueden predecir, estos errores dinámicos son repetitivos. Esto significa que es posible compensarlos, siempre que se cumplan determinadas condiciones.
Existen también otros factores que crean errores dinámicos no repetitivos menores (‘ruido’ del sistema) en un perfil de aceleración determinado, y no son compensados por Renscan DC:
Condición de la superficie: las superficies desiguales provocan vibraciones y determinados errores en la medición.
Ruido del servo / estabilidad: la capacidad de la máquina para mantener una velocidad programada depende de los parámetros de control y del rendimiento electromecánico del sistema motor.
Estos errores dinámicos son de naturaleza más aleatoria y, por tanto, no es posible compensarlos. No obstante, sólo suponen una pequeña parte del total de errores dinámicos.
Por último, existen factores que no afectan al error dinámico:
'Micro' posición: pequeñas variaciones sobre la posición nominal, la forma y el tamaño de la superficie en una fabricación y tolerancias integrantes normales.
Temperatura: los errores dinámicos son inmunes a la temperatura. Sin embargo, las variaciones de temperatura pueden tener un impacto en la precisión estática y, en consecuencia, en el rendimiento de la medición.
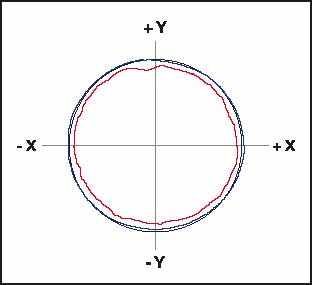
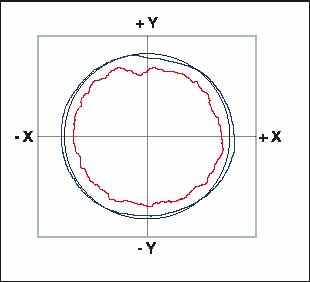