Conceptos básicos de seguridad
La prensa mecánica es una máquina diseñada o prevista para transmitir energía desde un motor primario hasta un punzón por medios mecánicos, con objeto de trabajar (conformar, plegar o cortar) en el troquel un metal en frío. Esta energía puede ser transmitida por un volante de inercia y un embrague o por medio de un mecanismo de accionamiento directo.
Los principales peligros existentes en las prensas mecánicas son los mecánicos: aplastamientos, atrapamientos, cortes, seccionamientos, impactos, perforación, proyección, etc. Son peligros que se pueden dar en la zona del troquel, entre las partes móviles, en la corredera, en los cojines, en los expulsores de piezas, en los mecanismos de accionamiento, etc.
La principal zona de peligro en las prensas mecánicas es la zona del troquel, y es en esta zona donde se deben tomar las medidas preventivas más evidentes. Esta zona puede ser protegida con diversos sistemas que pueden ser complementarios entre sí, entre los que se pueden citar los resguardos fijos perimetrales, los resguardos con dispositivos de enclavamiento y bloqueo, los resguardos asociados al mando con dispositivo de bloqueo, los resguardos con dispositivos de enclavamiento de apertura prematura, equipos de protección electrosensibles que utilizan dispositivos de protección optoelectrónicos activos (barreras inmateriales) y los dispositivos de mando a dos manos.
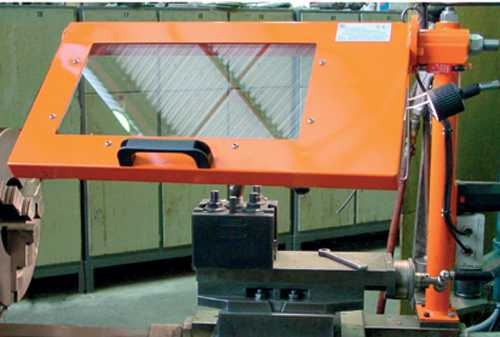
En lo que se refiere a los resguardos, todos ellos y los dispositivos de protección instalados deben ser interconectados, al menos, con el sistema de mando de la prensa con la misma categoría que la que se requiere para esos resguardos y dispositivos.
Un sistema paralelo a la instalación de los resguardos y que minimiza los peligros mecánicos en la zona del troquel, son los dispositivos de mando a dos manos, sistemas de seguridad que ocupan las dos manos del operario evitando que éstas puedan acceder a la zona del troquel durante la realización de la operación de prensado. El movimiento peligroso se desencadena accionando los dos elementos de mando en un intervalo de tiempo de 0,5 s (accionamiento síncrono). Si se suelta uno de los dos pulsadores durante el movimiento peligroso, la orden de mando queda anulada. El movimiento peligroso sólo podrá continuar si ambos pulsadores vuelven a su posición inicial y se pulsan de nuevo en el intervalo de tiempo especificado. La distancia de seguridad entre los elementos de mando y la zona peligrosa debe ser lo bastante amplia para garantizar que al soltar sólo uno de los elementos de mando, la zona peligrosa no se alcance antes de que concluya o se detenga el movimiento peligroso.
El mando bimanual va asociado a un módulo de seguridad que controla la simultaneidad del accionamiento de los pulsadores en un intervalo menor a 0,5 s para poder realizar nuevo ciclo de troquelado. El módulo aporta al sistema, junto con el mando bimanual, categoría de mando 4, es decir, redundancia y autocontrol (el autocontrol implica una función de seguridad indirecta que desencadena una acción de seguridad si disminuye la aptitud de un componente o de un elemento para desempeñar su función o si se modifican las condiciones de funcionamiento de manera que se generan peligros. La redundancia supone la aplicación de más de un dispositivo o sistema, o parte de un dispositivo o sistema, con el objetivo de asegurar que, en el caso de fallo de una parte en la realización de su función, haya otra disponible para realizar esa función).
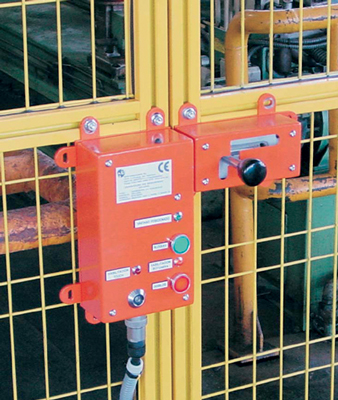
Dispositivos optoelectrónicos
Otro sistema habitual de seguridad que protege de los peligros mecánicos son las barreras inmateriales que consisten en equipos de protección electrosensibles que utilizan dispositivos de protección optoelectrónicos activos. Consisten en un emisor y un receptor situados frente a frente. El emisor emite de forma secuencial sobre cada haz tramas codificadas en emisión infrarroja. Cuando se emiten, reconocen y establecen todos los haces, la barrera puede armarse automáticamente o mediante un mando externo. El corte de uno o varios haces cualesquiera que sean provoca la apertura de los elementos de salida.
Las barreras inmateriales son equipos de seguridad positiva autocontrolada. Si surge alguna avería en el dispositivo de seguridad, el movimiento de la prensa, peligroso para el operario, se detendrá automáticamente. Cualquier fallo provoca la parada de los movimientos de la prensa. Una vez que se haya despejado la zona protegida, el movimiento que se había interrumpido con la intrusión no deberá reanudarse con su ritmo normal, ni siquiera cuando se efectúa el rearme mediante un pulsador.
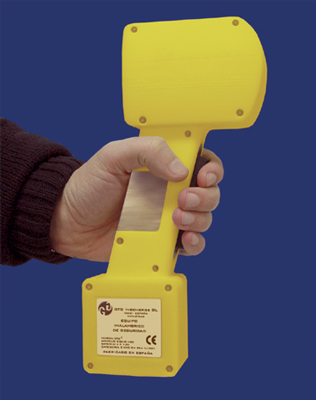
Este tipo de rearme debe retomar el movimiento al principio del ciclo.
Las barreras inmateriales deben satisfacer los siguientes puntos:
- Sólo será posible el acceso a la zona peligrosa a través de la zona de detección de la barrera.
- Cuando sea posible permanecer entre los haces fotoeléctricos y la zona de peligro de la prensa, se deben instalar medios adicionales, como otros haces, para detectar a una persona que permanezca allí.
- No se iniciará ningún movimiento peligroso mientras cualquier parte del cuerpo humano esté interrumpiendo la barrera inmaterial.
- Serán equipos de seguridad positiva autocontrolada. Si surge alguna avería en el dispositivo de seguridad, el movimiento de la prensa, peligroso para el operario, se detendrá automáticamente.
- Cualquier fallo provoca la parada de los movimientos de la prensa. Una vez que se haya despejado la zona protegida, el movimiento que se había interrumpido con la intrusión no deberá reanudarse con su ritmo normal, ni siquiera cuando se efectúa el rearme mediante un pulsador. Este tipo de rearme debe retomar el movimiento al principio del ciclo para reanudarse el ritmo normal.
- La barrera inmaterial de seguridad sólo podrá autorizar que se reinicie un movimiento peligroso después de comprobar que la prensa funciona correctamente y de que se haya activado un pulsador de rearme (bloqueo del arranque).
Por otro lado, la imposibilidad de parar la prensa en las mejores condiciones posibles es otro de los peligros más habituales que presentan éstas máquinas. Esto supone que, ante un suceso imprevisto, la prensa puede no estar preparada para realizar la parada de emergencia correcta, ni tener un correcto control sobre el sobrerrecorrido de frenado ni sobre el embrague freno.
La instalación de pulsadores de parada de emergencia resulta de utilidad en la mayoría del parque de maquinaria. En una prensa mecánica, es de utilidad la instalación de varios pulsadores de seta con enclavamiento mecánico, sobre todo en la parte posterior, donde el operario dispone de una peor visibilidad. Si se acciona la seta de emergencia se corta la alimentación eléctrica al motor principal que aporta movimiento a la máquina y también se deshabilita la maniobra de marcha de la máquina, por lo que para rearmar de nuevo la prensa es necesario desenclavar la seta de emergencia y realizar la maniobra de rearme de la máquina.
Es de importancia vital para mantener la seguridad de las prensas el control efectivo del sistema embrague – freno. El embrague y su sistema de mando debe estar diseñado de forma que, en caso de fallo de la energía neumática o eléctrica, el embrague se desembrague y el freno sea inmediatamente aplicado
Velocidad nula y peligros eléctricos
Es de gran utilidad el control de la velocidad de giro en los motores de las prensas. Los módulos de control de velocidad nula sirven para la detección de velocidad nula en motores de corriente alterna o continua. Con el control de velocidad nula se evita la inversión del sentido de giro durante su funcionamiento, evitándose así el posible salto de elementos mecánicos de la prensa por giro brusco del volante de inercia. Se utilizan en los circuitos de mando de desbloqueo del sistema de enclavamiento de los protectores móviles o para activar frenos de bloqueo tras pararse el motor. A través del uso del módulo de control se puede controlar el paro del motor con la medición de la tensión remanente de los bobinados del estátor.
Los peligros eléctricos, por su parte, también tienen importancia a la hora de realizar un análisis de riesgos en las prensas mecánicas. Los principales son los peligros de contactos directos e indirectos. Para evitarlos se incide en la renovación o cambio del cuadro eléctrico, en el cableado de la nueva instalación y en la modificación de la maniobra.
Entre otros servicios, GTG Ingenieros realiza los ajustes necesarios para garantizar que no se produzca el solapamiento de embrague y freno. Se comprueba el desfase entre el accionamiento neumático de cada válvula en el tiempo para evitar el solapamiento cuando el embrague y el freno están activados por diferentes válvulas. Se realiza mediante lecturas de la presión aplicada en cada válvula y registradas en un PC. Dicha regulación se realiza cambiando el tamaño del orificio de paso de aire de cada válvula hasta que tengan el desfase adecuado. Con este sistema se evitan desgastes prematuros del embrague freno y esfuerzos mecánicos innecesarios en la máquina.