Illig presenta la 3ª generación de máquinas de termoconformado para una mayor capacidad de producción y calidad
Fabricación de envases
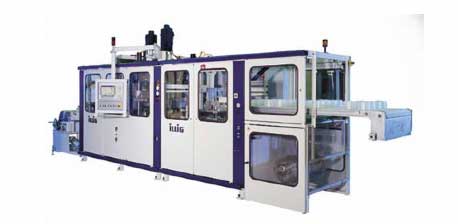
La 3ª generación, con una velocidad de producción de 55 ciclos/min, se presenta en la feria Fakuma de Friedrichshafen.
Con el fin de que el industrial procesador tenga asegurado a largo plazo el éxito económico, la máquina debe cumplir la larga lista de requisitos de los clientes. Las principales condiciones para ello son: fácil manejo de la máquina, un concepto flexible de la misma y una gran reproducibilidad de todos los elementos funcionales que intervienen en el proceso.
Para cumplir las exigencias impuestas al proceso de moldeo/troquelado es imprescindible que la estación de moldeo/troquelado sea muy rígida y que los planos de las mesas de moldeo sean perfectamente paralelos.
Con el fin de obtener unos resultados de corte óptimos, las palancas acodadas, las mesas y las columnas guía están optimizadas para que las fuerzas de cierre y troquelado sean máximas. Éstas son transferidas a las mesas por medio de palancas acodadas dobles y son generadas por servomotores con piñón movido por rosca. Para que no se formen fuerzas transversales en las guías de las columnas de las mesas de moldeo, la fuerza se introduce por el centro de la articulación de la palanca acodada doble. El perfil de velocidades, diseñado con precisión, de las palancas acodadas dobles permite la máxima introducción de la fuerza durante el proceso de troquelado.
Gracias a las diversas opciones de ajuste de los recorridos de las mesas y a las velocidades de los marcos tensores superior e inferior, accionados por separado, hay 10 programas de moldeo diferentes con los que poder realizar sin ningún problema todas las variantes de piezas moldeadas.
Gracias a la servotecnología utilizada por Illig, con la cual es posible sincronizar con gran precisión los movimientos de la mesa de moldeo con los del pistón de estirado previo, puede conseguirse una óptima distribución del grosor de las paredes laterales del producto. La mejor distribución de material permite obtener, además, la misma estabilidad del producto partiendo de un plástico de menor grosor, lo cual da lugar a una mejor calidad de los productos, como por ejemplo, una mayor rigidez de la pieza moldeada y unos bordes de sellado completamente exactos y planos a lo largo de toda la superficie de sellado, que se consiguen mediante pisones refrigerados en el molde.
Las máquinas automáticas de moldeo por aire comprimido son el resultado de una optimización consecuente del proceso de moldeo. Modernos programas de moldeo y la disposición optimizada de las unidades implicadas en el proceso de moldeo permiten fabricar complicadas geometrías de piezas moldeadas mediante moldeo por aire comprimido o por vacío. Intervalos de trabajo cortos, un alto grado de automatización gracias a la interrelación de las unidades de punzonado, de troquelado con fleje de acero y de apilamiento, y una madurada tecnología de cambio rápido del molde son las condiciones para una gran productividad y la reproducibilidad de todos los parámetros del proceso.
Aumento del número de ciclos y mejora de la calidad de los productos con las termoconformadoras de 3ª generación
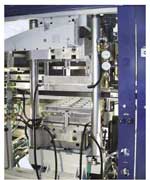
Convertir los potenciales libres de las secuencias de movimientos en un mayor número de ciclos
Una novedad la constituye el recién desarrollado interfaz de usuario, que permite un guiado puntual del operador a través de cada una de las fases de optimización. Esto quiere decir que para la optimización y según el programa de moldeo, la máquina prefija automáticamente para el operador los parámetros importantes para el rendimiento, cuyos efectos se representan en dicho interfaz de usuario recién desarrollado. Una ventaja importante de esta visualización es la representación puntual de las informaciones necesarias y de las funciones auxiliares según los principios del diseño industrial profesional. El interfaz de usuario es fácil de entender. Evita errores de manejo gracias a una clara y sencilla estructura del menú. La navegación por cada una de las páginas del menú es muy cómoda y puede seleccionarse en el panel de control. Para el sistema de diálogo también hay una ayuda electrónica, que se encuentra en el sistema de manejo.
Las nuevas tecnologías permiten la optimización por separado de todas las situaciones de funcionamiento, así como una asignación exacta de todos los parámetros del proceso a cada una de las fases del proceso de moldeo. Los puntos iniciales y finales y los valores absolutos de presión, vacío, etc. se pueden determinar y documentar de modo preciso. Todas las medidas se pueden guardar en memoria, de modo que estarán disponibles en caso de repetir producto.
Las condiciones para una alta productividad y para la reproducibilidad de todos los parámetros del proceso son: intervalos de trabajo cortos, alto grado de automatización por el hecho de unir las unidades de punzonado, troquelado con fleje de acero y apilamiento, y una elaborada tecnología de cambio rápido del molde.
Para hacer realidad las cargas y por tanto la duración de los husillos de accionamiento de la mesa portamolde a movimientos de cierre más rápidos, se utiliza una nueva tecnología de accionamiento. El comportamiento dinámico básico de los accionamientos utilizados, con tecnología de control electrónico, permite unas rampas de aceleración de mayor pendiente y, por consiguiente, fases de aceleración y frenado más cortas. El tiempo así ahorrado se utiliza para que la transición en el cambio de sentido sea más suave.
La simetría de los medios no sólo debe estar en el lado del molde, sino también en el lado de la máquina. Unos recorridos demasiado largos de los medios (aire de moldeo, refrigeración), aunque estén dispuestos simétricamente, dan lugar a desviaciones inaceptables en la pieza moldeada y pueden influir negativamente en el tiempo de proceso, es decir, los tiempos de llenado o vaciado se vuelven innecesariamente largos.
Una disposición directa de las válvulas de vacío y de aire comprimido en la estación de moldeo permite unos tiempos de llenado los más cortos posibles para cada una de las cavidades, y por tanto, unos tiempos de ciclo lo más cortos posibles. El control del aire de moldeo, del vacío de moldeo y del aire de desmoldeo se lleva a cabo mediante una tecnología de válvulas robusta y nada propensa a las averías.
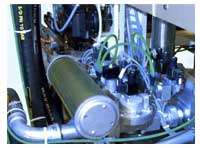
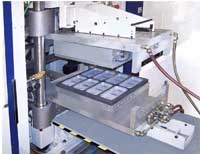
Un programa de reequipamiento integrado en el sistema de mando hace que el cambio de molde sea más fácil y rápido, siendo necesarios unos pocos pasos. El transporte del plástico se abre automáticamente durante el reequipamiento y más tarde se vuelve a ajustar a la nueva anchura del plástico. Además, los dispositivos de troquelado y de apilamiento se ponen a la posición correcta respecto a la estación de moldeo. El diseño de la máquina también tiene en cuenta que todas las piezas de formato puedan cambiarse desde el lado de manejo. En el caso de las máquinas RDKP, el molde de moldeo, por ejemplo, se cambia por completo en un solo paquete. Los cortes con fleje de acero, las contracapas de troquelado y las piezas de formato de apilamiento van equipados con unos dispositivos de tensado rápido, de manera que es posible efectuar un cambio completo de formato en el menor tiempo posible.
Unos modernos conceptos de cambio de molde permiten colocar las partes superior e inferior del molde en forma de pisos en unas estructuras de montaje especiales, que luego permiten efectuar trabajos de mantenimiento estando el molde abierto, sin tener que cambiarlo de sitio.
Al optimizar el proceso se ha ampliado la máquina básica con las siguientes características:
• Transporte del plástico con sistema tensor de cadenas neumático.
• Sistema de marco tensor superior e inferior mediante control en cascada.
• Válvulas muy dinámicas para la formación y reducción de la presión de moldeo.
• Control sin escalonamientos del aire de desmoldeo.
• Técnica de accionamiento y secuencias de movimiento optimizadas para la estación de moldeo, troquelado y apilamiento.
Gracias a la optimización integrada de la máquina y del molde, se pueden mejorar puntualmente los requisitos de las piezas moldeadas. Al mismo tiempo también se han cumplido los requisitos de construcción de la máquina, por ejemplo:
• Regulación de los parámetros importantes en el proceso de termoconformado
• Reproducibilidad del proceso de termoconformado
• Reducción del consumo energético
• Breves tiempos de cambio de molde
• Mantenimiento guiado y conservación preventiva
• Mayor disponibilidad y productividad.
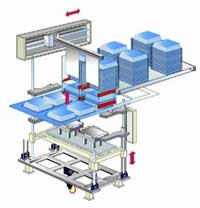
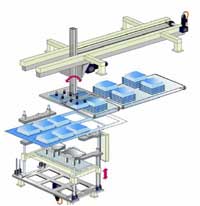
Optimización del proceso mediante diversas variantes de sistemas de apilamiento
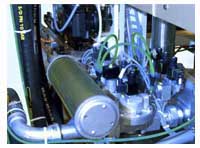
Sistema de manipulación
Como opción se tiene una cinta de descarga de dos partes, que simplifica la retirada del producto en caso de manejarse varias máquinas. El cambio de las piezas de formato mediante la tecnología de cambio rápido permite unos tiempos mínimos para prepararse para otro producto.
Gracias al sistema de manipulación se pueden mejorar puntualmente las siguientes exigencias de los clientes:
• Movimiento de rotura controlado
• Reducción de costes de las piezas de formato de apilamiento
• Es posible el apilamiento A/B/C, sin límite de altura de la pieza moldeada
• Reducción de los filetes de la rejilla de troquelado
• Sistema de mando integrado en la máquina automática de moldeo
• Rápido cambio de formato y rearranque
• No hay ninguna presión sobre la pila de productos
La suma de todas las ventajas de las termoconformadoras de 3ª generación proporciona al usuario grandes beneficios gracias al ahorro de consumo energético y a unos tiempos de ciclo aún más cortos.
Etapas ampliadas para una modularidad y flexibilidad máximas
Ahora explicamos a los clientes el concepto de la optimización de procesos mediante demostraciones en situaciones similares a las de fabricación. Los números de ciclos determinados teóricamente se muestran a los clientes en la práctica, para que superen un ensayo práctico. De este modo Illig también apuesta por el avance tecnológico de las termoconformadoras de 3ª generación.