ContiTech Vibration Control y Basf utilizan Ultramid CR e Integrative Simulation para Opel
Hasta la fecha, los componentes sometidos a elevada solicitación mecánica, como soportes de motor y de transmisión y barras de torsión, se hacían exclusivamente de aluminio o acero. Para este desarrollo Basf se ha servido de su nuevo poliamida especial Ultramid A3WG10 CR además de un software denominado Integrative Simulation, a tal fin complementado con nuevas extensiones. La pieza pesa un 35% menos que su predecesora fabricada en aluminio, y ahora se fabrica en serie para el Opel Vectra y el Saab 9-3. El sistema de bancada del motor constituye un elemento esencial de unión entre el motor/transmisión y el cuerpo del vehículo. Además de poseer altas prestaciones mecánicas, estos componentes deben soportar temperaturas en un rango de 30°C a 120°C y ser resistentes a la agresión química del aceite y otros productos.
Novedad: sistema de bancada de motor fabricado con plásticos especiales
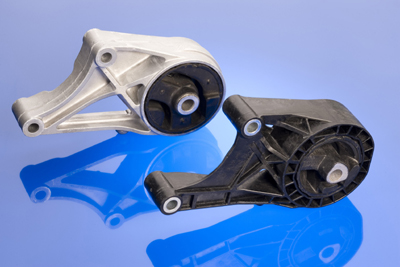
Los fabricantes del automóvil tienden a construir cada vez estructuras más livianas, pero todavía se ven obligados a utilizar el acero y aluminio para piezas estructurales y mecánicamente solicitadas de sus vehículos: tal es el caso de la bancada del motor. Hasta la fecha resultaba imposible utilizar termoplásticos para elaborar piezas sometidas a cargas mecánicas intensas. Los requisitos para un dimensionado preciso de componentes sometidos a altas cargas incluyen modelos con material de alta calidad y poderosas herramientas de diseño como Integrative Simulation, sin olvidar, por supuesto, una materia prima especialmente desarrollada para ello como Ultramid A3WG10 CR. En la familia de materiales Ultramid CR, la relación entre propiedades del material por un lado y orientación de las fibras y límite de fluencia por otro, ha sido determinada de forma extremadamente precisa. Además las prestaciones de estos plásticos son muy superiores, con una desviación estándar de propiedades mecánicas mucho menor que en los poliamidas habitualmente disponibles en el mercado. La materia prima antes de refinar se selecciona minuciosamente y pasa por un proceso de fabricación bajo condiciones sometidas a un control muy estricto, de modo que las piezas fabricadas con estos plásticos proporcionan calidades uniformes, con unas características que siguen fielmente los valores numéricos obtenidos en los ensayos.
Novedad: predicción de resistencia mediante Integrative Simulation
La parte más importante de este desarrollo (cálculos generales y simulación) depende de una herramienta software de Basf denominada Integrative Simulation. En su afán por predecir de manera confiable las fuerzas que soporta una pieza para la bancada del motor, Basf ha dado una vuelta de tuerca más en el perfeccionamiento de este software. El método ampliamente utilizado en la industria actual para dimensionar piezas consiste en llevar a cabo los cálculos de fuerzas independientemente de cualquier proceso de simulación, utilizando tan solo valores promediados de propiedades de materiales. Para un aprovechamiento óptimo de las características de los poliamidas con refuerzo de fibra es necesaria una orientación correcta de la fibra en determinadas posiciones de la pieza, ya que las características mecánicas dependen en gran parte de cómo esté alineada la micro estructura. Aquí es donde Integrative Simulation interviene: combinando los resultados de una simulación de llenado de la cámara con un análisis de elementos finitos que tiene en cuenta la orientación de las fibras en toda la pieza. A partir de los datos obtenidos, así como la influencia de la temperatura y la tasa de carga, se calculan las dimensiones de la pieza y el molde para fabricarla. Los ensayos complejos de ciclo de vida y las pruebas reales en vehículos de Dama Opel AG ponen de manifiesto la capacidad de Integrative Simulation como herramienta fiable de ingeniería y diseño.