The reduction of emissions for machinery engines
October 19, 2009
Engine manufacturers are working with clients in more detail and more quickly than before. To accept this view of cooperated work of great scope, Perkins has been a real opportunity to deliver machines with higher quality, durability, economy of fuel and productivity.
Perkins and his team from carrying out emissions regulations are working to understand the current and future legislation to ensure that the business can develop good strategies in terms of development of the engine and customer support. This is an issue that is reaping great dividends for them while they are willing to create and implement the future product strategy.
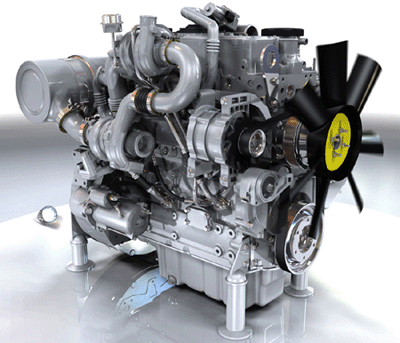
"When talking about the 'Tier4' are talking about currently about two stages of emission legislation", explains Julia Boorman, Director at the global level of emissions regulation and compliance of Perkins. "First, to know that 'Tier4 Interim' in North America and 'Stage IIIB' in Europe demand a moderate reduction of NOx (nitrogen oxide) levels of between 15 and 50% depending on the range of power." "The reduction in the levels of particulate (PM) up to 95% is a significant movement." This is aimed at the use of systems of post-treatment in leaks to achieve this objective and will come into use in January 2011 for engines over 130 kW and a year later for 56 to 130 kW engines. Three years later, in 2014 and 2015 the Tier IV Final/Stage 4 will require a subsequent reduction of 80 to 90% of Nox, which will also incorporate new additional technology.
However there are a lot of the other requirements of legislation separate to achieve the required emissions levels. They are directed to ensure that compliance is not only applied to the production stage but also to compliance in field under actual operating conditions. These areas include the requirements do not exceed, extended environmental conditions, systems testing, testing, use and control of ventilation of the engine exhaust.
Current emission legislation specifies a test State at different points in the curve of operation of the engine using a hot engine. This is a simple test to implement and predicts how a motor will respond and what emissions occur. But there is the introduction of the cycle of systems 'non road' in the Tier 4 Interim/Stage IIIB. This is a test standard for all manufacturers of engines, designed to represent the cycle of operation of a typical machine 'off higway' which includes a period of work when the engine is cold and also uses many rapid changes in the engine speed and load. This test requires a more sophisticated engine test chamber and the performance of the engine is considerably more difficult to predict.
Measurement of lower levels of particles offer an additional technical challenge. The traditional method of heavy of the role of the filter to determine emissions of PM during a test becomes more difficult when the PM who is measuring can be relatively smaller condensation.
Emissions should be achieved not only a standard temperature but on a wide range of operating conditions such as high and low temperature and altitude above almost the full range of operation of the engine.
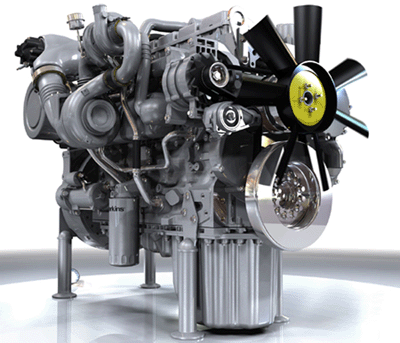
"There will be in the future a requirement for testing in field of machines to ensure that they actually comply with emissions after being sold." This is like wrapping in a program requested measurements by legislators that is the responsibility of the manufacturer of the engine. It will take an example of a model of a particular machine on which it is installed a portable measurement equipment that will measure the output of emissions for a short period of time. "This team is in many cases adapted to find a location safe and suitable to be installed in many types of compact machinery", believes Boorman.
In addition, the haze caused by the gas and oil of the ventilation of the block should be considered as part of the output of the engine emissions and they must be controlled. In some cases the gases of the block must be filtered and in other cases they can be taken back to the (closed-circuit ventilation) admission.
In many cases the engine will be not distributed to the OEM post-treatment connected in their final configuration system. The engine and the post-treatment can be distributed as two separate parts and they may even from different points of the manufacture. The client may need to install both components on two different points in its manufacturing process.
Emissions of the engine are certified by the manufacturer, but the system will not reach these levels until that has been assembled by the customer. Obviously this will require a level of close collaboration between the engine manufacturer and OEM to ensure that the after-care has been installed to the appropriate engine correctly.
The 'image' of emissions is developing rapidly. As new countries announce their plans to improve the quality of the air, the map changes continually. The general trend will be that emissions in Europe, North America and Japan regulation shall be adopted by other large economies. By 2016, there will be up to five different levels of emissions in the world and they will be certified by many more national and regional authorities.
Tier 4
Design for maintenance was the main consideration in the development of new engines of the Perkins 1200 Series strategy. The main intention was to allow mechanics to make routine tasks of operation and at the same time reduce the maintenance costs for the operators.
The typical features that support this option include the adoption of a new auxiliary of the lid of the distribution that uses pulleys type poly v, which have an interval of six times higher maintenance than the current system. Another example of time-saving is the new hydraulic adjustment of the tanks. This eliminates the need for adjustment every 1,000 hours. Although this is not a complex operation for the operator can prove difficult if the machine is in field. The arrival of the deposit of the post-treatment will reduce time and money for the end user and prevent the potential damage of the post-treatment.
Undoubtedly the engines of the future will have high levels of technological complexity and there will be an increase in the number of components not relatives, more sensors and actuators.
The skills required for technicians in diesel engines have changed since some time and this trend will accelerate. Sound skills will not be sufficient, the technicians of tomorrow will need superior skills for the diagnosis and there will be a strong electronics and the use of computers understanding.
The desire for a capacity of advanced product support has led to make a substantial investment in the development of their network. The development of skills is not restricted to technicians, this also extends to all aspects of the Organization of the dealer. Perkins believes that a relationship of strong work with resellers provides a strong foundation to improve and ensure success in the future.
Setting new standards for product support
In 2005, Perkins began a programme of adjustments of new standards for its distributors.
Each Distributor is regularly audited against these standards and are expected to show a continuous growth and capacity. The covered global product support and flexibility in the network is seen by the client as a differentiator from the rest of off-higway engine manufacturers. This position will grow strong as emissions legislation includes other technologies in the market.
Not all countries require to comply with the standard Tier 4 / Stage 3b
Many countries will require products to achieve a different less restrictive emissions range. It will not be commercially viable or technically possible to have a single model of machine for around the world, the cost of more sophisticated engines and the risk of high sulphur content of fuels will require models to less regulated countries.
Perkins is developing a range of engines to fulfill these needs, to be built near these regions of consumption on several continents.
These are in some cases, simple and highly effective engines on its cost. But it also likely make them engines electronically controlled and sophisticated for these industries and regions who prefer to pay a little more to obtain high productivity and a higher fuel economy.
There are a number of technologies available in the control of NOx. Previous releases were successfully controlled technologies in the interior of the cylinder, changing the dynamics of the combustion process to achieve a clean combustion. But this by itself alone is insufficient to achieve NOx levels required in the Tier 4 Interim.
After many considerations, Perkins has come to the conclusion that there are two viable technologies. One is to use the exhaust gases for cooling the combustion process and the second is to use a system called selective catalytic reduction (SCR).
NOx is formed at high temperatures inside the engine cylinders. A small proportion of exhaust gases can be cooled, introduced in the cylinder. As the exhaust gases have a high content of steam (the combustion product) they cool the combustion and reduces the formation of NOx.
This has a cost effective and relative, can be assembled compact form the engine and is expected to give a slight improvement in fuel consumption on current engines Tier 3 of about 3 per cent.
The main difference is that it requires a second fluid in addition to the diesel fuel. A second deposit is placed on the machine which needs to be filled by the operator regularly, perhaps every three of four times that the fuel tank is filled. This fluid known as Adblue and Diesel Emissions Fluid in America contains a product called Urea.
This urea is injected in small amounts (from 4% to 5% of the diesel fuel) in the exhaust system where it is mixed with the exhaust gases. The hydrolysis produced in the catalyst converts urea into ammonia, which reacts with NOx in the SCR catalyst to produce nitrogen, water and carbon dioxide. A final stage of oxidation catalyst is required to clean up any traces of ammonia in the output of the gases.
The SCR allows savings in fuel consumption of 5% on other technologies. Although the total consumption of the liquid is extremely closed. Where the operation saves money really in the SCR depends on the relative cost of urea and the fuel in the country in question.
The diesel particulate filter
For the reduction of particles Perkins has chosen a filter of particle diesel (DPF) of cordierite. This porous ceramic material is highly efficient in removing particles of 90% as minimum and often higher.
The exhaust gas flow through a wall porous depositing particles and leaving clean exhaust.
Diesel oxidation catalyst
The diesel particulate filter could not if just eliminate all legislated gases, hydrocarbons, carbon monoxide and organic soluble fraction also must be controlled. So the DPF is used in combination with another device called a diesel oxidation catalyst (DOC). The DOC has similar cordierite material but uses the principle of direct flow. The gases pass directly through the device through the wall. The DPF and DOC are combined in the same container in the machine.
The DPF regeneration
As the particle filter cleans exhaust gas particles, soot will begin to accumulate in the filter. This needs to be cleaned through a process called 'regeneration'.
The range to which the filter is filled depends on how clean is the engine and makes the output of the engine particles it lowest possible. In addition, the cycle of operation of the machine has some effect in the range of soot accumulation.
There are two basic forms of regeneration that can clean the soot filters, a so-called continuous process of low temperature of regeneration or a casual process of high temperature of regeneration.
Low regeneration temperature catalyst metal helps create NO2 in the exhaust, which oxidized coal at temperatures of around 250 ° C or higher.
A limitation of this technology is that it requires some NOx to make the process work, usually a minimum of 25: 1 NOx/particle ratio and a ratio of 40/1. Still, the particles of the engine output is very low, only viable in engines to 130 kW where a little more of NOx is permitted by law.
This process occurs continuously so that the operator will normally not notice anything different during the work cycle and will not need to take exceptional action.
High temperature of regeneration
The high temperature of regeneration is a casual process used to burn the soot accumulated after several hours of operation. There are different methods but preferred by Perkins for the more than 130 kW engines is to use a burner in the exhaust which warms the exhaust gases above 600 ° C directly rusting soot accumulated in a controlled way.
Ashes
Although almost all particles in the filter is oxidaran completely during regeneration there are small amounts of minerals that not combust.
The ash is not regenerated and needs to be cleaned using a special machine. In North America the environmental protection agency (EPA) specifies that the first maintenance of ashes should not be before the 3,000 hours for engines below 130 kW and 4500 hours for more than 130 kW engines.
In Europe, although not specified by legislation, Perkins feels that the maintenance is a drawback to the owners of machinery and should be avoided everything that is possible.
Thanks to a small increase in the size of the filter in the lower powers Perkins has controlled avoid the maintenance of ash for some of its range of engines.
Sulphur
Sulphur in the fuel is not only a problem for Perkins, of the entire industry. Sulfur reacts with precious metals in catalysts and avoid that they work correctly. Legislators recognize this and a new ' diesel ultra low-sulfur ' will be introduced to the sector off-higway. These will have levels of sulphur less than 15 ppm, similar to those used in the sector on-higway.